Защита от пыли при добыче и переработке полезных ископаемых (2012)
Руководство по защите от пыли при добыче и переработке полезных ископаемых
Dust Control Handbook for Industrial Minerals Mining and Processing
- Министерство здравоохранения и социальных служб США (The United States Department of Health and Human Services)
- Центры по сдерживанию заболеваний (Centers for Disease Control)
- Национальный институт охраны труда (National Institute for Occupational Safety and Health)
- Отдел исследований в области безопасности (Division of Safety Research)
2012
Авторы: Эндрю Секада, Эндрю О’Брайен, Джозеф Чал, Джей Колинет, Уильям Фокс, Роберт Франта, Джерри Джой, Рандольф Рид, Патрик Ризер, Джон Раундс и Марк Шульц
(Andrew B. Cecala, Andrew D. O’Brien, Joseph Schall, Jay F. Colinet, William R. Fox, Robert J. Franta, Jerry Joy, Wm. Randolph Reed, Patrick W. Reeser, John R. Rounds, Mark J. Schultz)
Управление по исследованиям в области безопасности и санитарии при добыче полезных ископаемых (Office of Mine Safety and Health Research)
Питтсбург, Пенсильвания - Спокан, Вашингтон
Январь 2012
Это документ является общественным достоянием, и может свободно копироваться и распространяться
This document is in the public domain and may be freely copied or reprinted. Ссылка на файл PDF на русском языке
Правовая оговорка:
Упоминание любой компании или продукции не означает, что её услуги или продукция одобряются Национальным институтом охраны труда (NIOSH). Кроме того, ссылки на интернет-сайты (за исключением сайта Института NIOSH)не означают, что NIOSH одобряет финансирование организаций или их программ, или продукции. Также NIOSH не несёт ответственности за содержание этих сайтов. Все ссылки на сайты, имеющиеся в этом документе, были действительны на момент его публикации.
Доступ к информации:
- Для получения документов, относящихся к охране труда и технике безопасности, свяжитесь с NIOSH:
- Телефон 1-800-CDC-INFO (1-800-232-4636); TTY 1-888-232-6348; e-mail cdcinfo<собока>cdc.gov
- или посетите сайт Института охраны труда NIOSH: www.cdc.gov/niosh
Для ежемесячного получения новостей от Института, подпишитесь на рассылку электронных новостей (NIOSH eNews), посетив www.cdc.gov/niosh/eNews.
DHHS (NIOSH) Publication No. 2012–112
- См. также переводы документов NIOSH:
Персональный шахтёрский пылемер PDM (2006)
Обеспыливание при подземной добыче угля (2010)
Ограничение предельно допустимой концентрации угольной пыли в шахтах США (2011)
Отчёт специалистов NIOSH о разработке воздушного душа для защиты шахтёров от пыли (2012)
Сокращения и единицы измерения |
---|
Сокращения |
AASHTO American Association of State Highway and Transportation Officials – американская организация, разрабатывающая требования к дорогам, их проектированию, строительству и испытаниям.
ACGIH American Conference of Governmental Industrial Hygienists – “…” объединяющая специалистов в области промышленной гигиены, разрабатывает ПДК вредных веществ и др. AEK airflow extensible Kraft – пористая воздухопроницаемая крафт-бумага, используемая для изготовления мешков для фасовки продукции. AIRRS Air ring seal – динамическое противопылевое бесконтактное уплотнение места прохождения бура через буровую платформу с помощью обдува зазора струями сжатого воздуха. ASHRAE American Society of Heating, Refrigerating and Air-Conditioning Engineers – организация, объединяющая специалистов в области вентиляции, кондиционирования и отопления. ASTM American Society for Testing and Materials - американская международная добровольная организация, разрабатывающая и издающая стандарты для материалов, продуктов, систем и услуг. B&BCD bag and belt cleaning device – устройство, которое очищает наружную поверхность заполненных мешков и поверхность конвейерной ленты от пыли после того, как мешки наполнены материалом и отправлены по ленточному конвейеру к месту укладки на паллеты. Благодаря этой очистке снижается запылённость при последующей укладке мешков и др. BHP brake horsepower – мощность, потребляемая вентилятором с учётом его КПД. CBR California Bearing Ratio - Калифорнийская проверка несущей способности (материала, используемого для создания грунтовых дорог, в данном случае - для перевозки полезных ископаемых внедорожными самосвалами). При проверке цилиндр вдавливается в материал, фиксируется усилие. CEMA Conveyor Equipment Manufacturers Association – объединение ведущих изготовителей оборудования для перемещения материалов в Северной Америке http://www.cemanet.org/. CFR Code of Federal Regulations - сборник основных постановлений и приказов органов федеральной исполнительной власти США. DSH Dust Suppression Hopper – устройство для снижения запылённости при погрузке сыпучего материала в ёмкость. Состоит из бункера-накопителя, который накапливает не непрерывно поступающий материал, а потом высыпает его - сплошной струёй, что уменьшает вовлечение окружающего воздуха в движение падающего материала. EPA Environmental Protection Agency - Агентство по охране окружающей среды. ESP Electrostatic precipitator – промышленный электрофильтр. FIBC Flexible Intermediate Bulk Container - мягкий контейнер (биг-бэг / big-bag) - мешок большого размера и грузоподъемности, имеющий стропы-петли. FK flat Kraft - стандартная крафт-бумага для изготовления бумажных фасовочных мешков. HEPA high-efficiency particulate air (filter) – высокоэффективный противоаэрозольный фильтр, улавливает не менее 99.97% частиц размером 0.3 мкм. HVAC heating, ventilation, and air-conditioning – отопление, вентиляция и кондиционирование воздуха. IP Inch Pound – система единиц измерения, используемая в США, и основанная на единице измерения длины дюйм (25.4 мм) и фунт (0.454 кг). Так как исходные формулы были написаны в этой системе, при переводе отдельно приводится оригинальная формула, и отдельно – формула, полученная из оригинальной при использовании системы СИ (метр килограмм). LEV local exhaust ventilation – местная вытяжная вентиляция, местный отсос. MERV minimum efficiency reporting value – комплексный показатель эффективности улавливания пыли фильтровальным материалом, учитывает эффективность для 3 диапазонов размеров частиц. MLV modified low-velocity - Модифицированная низкоскоростная вентиляционная система, в которой начальный вертикальный участок служит для улавливания крупных частиц за счёт очень низкой скорости воздуха, а остальные схожи с обычными высокоскоростными системами. MSD musculoskeletal disorder – заболевания опорно-двигательного аппарата MSDS Material Safety Data Sheet – паспорт безопасности, документ с описанием свойств вредного вещества. MSHA Mine Safety and Health Administration - Управление по охране труда и промышленной безопасности в горной промышленности. NIOSH National Institute for Occupational Safety and Health – Национальный институт охраны труда. NISA National Industrial Sand Association - торговая ассоциация, представляющая крупнейших североамериканских производителей и переработчиков промышленных песка (http://www.sand.org/). NK natural Kraft – стандартная крафт-бумага для изготовления бумажных фасовочных мешков. OASIS overhead air supply island system – автономная фильтрующая вентиляционная система, подающая чистый воздух на рабочее место сверху – “воздушный душ”. OSHA Occupational Safety and Health Administration – Управление по охране труда в Минтруда США. PF protection factor – коэффициент защиты, отношение концентраций; снаружи (закрытой кабины) к концентрации в кабине оператора; или концентрации пыли при не использовании средства снижения запылённости к концентрации при его использовании. PEL - permissible exposure limit - Предельно допустимая концентрация, ПДК. PM particulate matter – аэрозоли, в настоящем Руководстве – преимущественно твёрдые частицы. PSE particle size efficiency – средняя эффективность улавливания частиц определённого диапазона размеров. PTFE polytetrafluoroethylene – политетрафторэтилен, фторопласт-4. SOP standard operating procedure – правила выполнения работ. SP static pressure – статическое давление (воздуха в вентиляционной системе) TP total pressure – полное давление воздуха в вентиляционной системе. TSP total suspended particulates – (концентрация) всех частиц пыли, находящихся в воздухе, включая средне- и крупнодисперсные, не-респирабельные частицы. TWA time-weighted average – средняя по времени концентрация (например – среднесменная для 8-часовой смены) USBM United States Bureau of Mines – Горное Бюро, предшественник MSHA (см. выше). VP velocity pressure – скоростной напор воздушного потока (ρν2/2). |
Единицы измерения |
acph air changes per hour – кратность воздухообмена за час. cfm cubic feet per minute – кубических футов в минуту – объёмный расход ~ 28.3 л/мин = 1.7 м3/час. cfm/ft2 cubic feet per minute per feet squared – кубических футов (28.3 л) в минуту на квадратный фут (9.3 дм) = 3.05 л ̸ (дм*мин) = 0.183 м3/(дм*час) = 18.3 м3/(м2*час) fpm feet per minute – футов в минуту, скорость ~ 0.305 м/мин ~ 18.3 метров в час. ft feet – фут, длина 304.8 мм. ft2 feet squared – квадратный фут = 9.3 дм = 0.093 м2. ft/min feet per minute – футов в минуту, скорость ~ 0.305 м/мин ~ 18.3 метров в час. gal/yd2 gallons per square yard – галлонов на квадратный ярд (~0.836 м2) gpm gallons per minute – галлонов (1 галлон США – сухой – 4.405 л, жидкий – 3.785 л) в минуту. gr/cf grains per cubic foot – гран (1 гран ~64.8 мг) на кубический фут (~28.3 л) ~ 2.288 мг/л. gr/dscf grains per dry standard cubic foot – гран на один кубический фут (газа) при стандартных условиях (давление 1 атм = 101.325 Па, температура 60° F = 15.6° С) при нулевой относительной влажности. kg/m3 kilograms per cubic meter – килограмм на кубометр. lb pounds – фунт, вес ~ 0.45 кг. lbs/hour pounds per hour – фунтов в час lbs/min pounds per minute – фунтов в минуту μg/m3 micrograms per cubic meter – микрограмм (10-6 грамм) на кубометр. μm micrometers – микрометр, микрон, 0.001 мм. mg/m3 milligrams per cubic meter – миллиграмм (10-3 грамм) на кубометр. mm millimeters – миллиметр. NPT national pipe taper – трубная коническая резьба. pH potential of hydrogen - водородный показатель. psi pounds per square inch – давление в фунтах на квадратный дюйм ~6.895 кПа. psig pound-force per square inch gauge – относительное давление (по отношению к атмосферному), выраженное в psi (1 psi = 6.895 Па). То есть давление (например - в ёмкости) 100 psig (698.5 кПа) означает, что абсолютное давление равно 100 psi + 14.7 psi (атмосферное давление 101.3 кПа) = 114.7 psi (799.8 кПа). RPM revolutions per minute – оборотов в минуту, об/мин. scfm standard cubic feet per minute – кубический фут (газа) в стандартных условиях (давление 1 атм = 101.325 Па, температура 60° F = 15.6° С) при нулевой влажности – в минуту. TPH tons per hour – тонн в час. wg water gauge – водяной столб, например – измерение давления в высоте водяного столба (1 мм wg = 9.8 Па) |
См. также: Коэффициенты для перевода единиц измерения (National Institute of Standards and Technology) http://physics.nist.gov/Pubs/SP811/appenB9.html |
Благодарности
В разработке этого руководства приняли участие следующие лица, перечисленные в алфавитном порядке:
- Роджер Бриз Roger Bresee, Vice President, Technical Services, Unimin Corporation, Peterborough, Ontario, Canada;
- Крис Брайан Chris Bryan (ушёл на пенсию), C.M.S.P., Occupational Health & Safety Manager, U.S. Silica Company, Berkeley Springs, WV;
- Роберт Кастелан Robert M. Castellan, M.D., M.P.H., Expert—Division of Respiratory Disease Studies, National Institute for Occupational Safety and Health;
- Синтия Фарие Cynthia Farrier, Graphics Specialist, National Institute for Occupational Safety and Health;
- Кристофер Финдлэй Christopher Findlay, C.I.H., C.M.S.P., U.S. Department of Labor, Mine Safety and Health Administration, Arlington, VA;
- Ян Фёрт Ian Firth, Principal Adviser—Occupational Health, Rio Tinto Limited, Bundoora, Victoria, Australia;
- Марион Молчен Marion Molchen, Molchen Photography, Washington, PA;
- Ян Матмански Jan Mutmansky, Ph.D., P.E., Professor Emeritus, Pennsylvania State University, University Park, PA;
- Кеннет Вопал Kenneth Vorpahl (на пенсии), C.I.H. (1973-2009), C.S.P. (1976-2009), General Manager/Safety & Health, Unimin Corporation, Winchester, VA;
- Ричард Вуд Richard Wood, International Union of Operating Engineers, National HAZMAT Program, Beaver, WV.
Об этом руководстве[править]
Это пособие появилось в результате успешных совместных усилий правительства США и промышленности в направлении защиты здоровья шахтёров и людей, работающих на перерабатывающих предприятиях. Основной вклад в создание руководства внесли Отдел исследований в области техники безопасности и охраны труда в горном деле (Office of Mine Safety and Health Research OMSHR) Национального института охраны труда (NIOSH); и промышленная ассоциация Industrial Minerals Association–North America (IMA-NA). Отдел техники безопасности и охраны труда (OMSHR) в NIOSH занимается предотвращением несчастных случаев и профзаболеваний путём проведения исследований и профилактики, а IMA-NA представляет компании, занятые добычей и переработкой минеральных полезных ископаемых.
Руководство было написано группой специалистов по технике безопасности, охране труда, профессиональным заболеваниям, и инженерами (перечислены ниже) для того, чтобы собрать и представить проверенные технологии и методы снижения воздействия пыли на людей, используемые на всех стадиях добычи и переработки минеральных полезных ископаемых. В документе описаны и сами технологические процессы, которые приводят к загрязнению воздуха пылью, и способы снижения воздействия пыли на рабочих. Применение технических средств коллективной защиты, описанных в руководстве, поможет работодателям, специалистам по охране труда и рабочим добиться конечной цели – предотвратить развитие необратимых и неизлечимых профессиональных заболеваний (пневмокониоза, силикоза) и других заболеваний, возникающих при воздействии пыли.
Руководство предназначено в первую очередь для работодателей, занимающихся добычей и переработкой минеральных полезных ископаемых, и в нем подробно описаны методы снижения запылённости на всех этапах добычи и обработки сырья, в том числе: при бурении, дроблении, просеивании, перемещении, упаковке, погрузке и перевозке. Руководство создавалось для того, чтобы помочь людям, работающим в горной промышленности, использовать современные методы снижения запылённости (с помощью эффективных средств коллективной защиты), чтобы уменьшить или (полностью) устранить воздействие пыли на рабочих при опасных концентрациях. Такое предотвращение – главный способ сбережения здоровья американских рабочих.
Со-председатели комитета целевой группы (task force)
- Эндрю Секада Andrew B. Cecala, Senior Research Engineer Dust Control, Ventilation, and Toxic Substances Branch, NIOSH
- Эндрю О’Брайен Andrew D. O'Brien, C.S.P., General Manager/Safety & Health Unimin Corporation
Члены комитета
- Джей Колинет Jay F. Colinet, Senior Scientist Dust Control, Ventilation, and Toxic Substances Branch, NIOSH
- Уильям Фокс William R. Fox, Manager/Safety & Health Unimin Corporation
- Роберт Франта Robert J. Franta, Quotation Engineer Spraying Systems Co.
- Джерри Джой Jerry Joy, C.I.H., C.S.P., Research Scientist—Industrial Hygienist Dust Control, Ventilation, and Toxic Substances Branch, NIOSH
- Рандольф Рид Wm. Randolph (Randy) Reed, Ph.D., P.E., Research Mining Engineer Dust Control, Ventilation, and Toxic Substances Branch, NIOSH
- Патрик Ризер Patrick W. Reeser, Engineering Manager U.S. Silica Company
- Джон Раундс John R. Rounds, Director Project Engineering Unimin Corporation
- Марк Шульц Mark J. Schultz, P.E., Senior Mining Engineer Pittsburgh Safety and Health Technology Center (PS&HTC), Dust Division, Mine Safety and Health Administration (MSHA)
Редактор
- Джозеф Чал Joseph Schall, Health Communications Specialist, NIOSH
Подготовка оригинал-макета
- Жанна Зиммер Jeanne A. Zimmer, Physical Science Technician, Dust Control, Ventilation, and Toxic Substances Branch, NIOSH
IMA-NA одготовка оригинал-макета
- Марк Эллис Mark G. Ellis, President IMA-NA
Предисловие к переводу[править]
ВНИМАНИЕ, перевод сделан без консультации со специалистами в области добычи и переработки полезных ископаемых, и может быть неточен. Во всех сомнительных случаях обращайтесь к первоисточнику.
Из-за несовершенства используемых технологий добыча и переработка полезных ископаемых часто сопровождается образованием пыли, попадающей в воздух. Вдыхание такой пыли моет привести и нередко приводит к развитию необратимых и неизлечимых профессиональных заболеваний – силикоза, пневмокониоза[V- 1], и др. Поэтому для сбережения здоровья рабочих используются различные методы профилактики вдыхания пыли – изменение технологии; герметизация оборудования; автоматизация процесса; эффективная вентиляция и, наконец, средства индивидуальной защиты – противоаэрозольные респираторы.
Однако огромный опыт, накопленный специалистами промышленно-развитых стран показал, что использование СИЗ органов дыхания является не только самым последним, но и самым ненадёжным средством профилактики профессиональных заболеваний – по сравнению с использованием более надёжных средств коллективной защиты[V- 2][V- 3]. К сожалению, в СССР и в РФ по ряду причин практически не проводились измерения реальной эффективности СИЗОД, и на основании чисто лабораторных проверок бытует противоположная точка зрения.
В РФ в течение последней четверти века отмечается неуклонное ухудшение условий труда. Даже по официальным данным доля людей, работающих во вредных и опасных условиях, составляет 1/3 от числа всех работающих (2014)[V- 4], и нет никаких причин для изменения этой тенденции. В этих условиях для защиты здоровья рабочих широкое применение нашли именно СИЗ, и их использование стимулируется государством (расходы на закупку СИЗ компенсируются за счёт обязательных отчислений в Фонд Социального Страхования, до 20%). Принят закон о специальной оценке условий труда 426-ФЗ, который допускает снижение класса вредности при обеспечении рабочих СИЗ – что предполагает, что использование СИЗ позволяет устранить воздействие вредных производственных факторов на рабочего.
Однако эти мероприятия проводятся в условиях, когда из-за отсутствия государственных научно-обоснованных требований к выбору СИЗОД изготовители и продавцы систематично и значительно завышают эффективность своей продукции (точнее – товара), тем самым провоцируя потребителя закупать те виды респираторов, которые заведомо не способны обеспечить надёжную защиту рабочих. Например, при подземной добыче полезных ископаемых широко используются респираторы-полумаски – а СИЗОД такой конструкции считаются специалистами наименее эффективными по сравнению со всеми другими (полнолицевыми масками, респираторами с принудительной подачей воздуха под лицевую часть)[V- 5]. Замеры в производственных условиях показали, что при их непрерывной носке возможно просачивание неотфильтрованного воздуха через зазоры между маской и лицом до 45% - и их продолжают выдавать для работы при запылённости, порой превышающей 1 грамм на м3 (ПДКрз при отсутствии кварца – 10 мг/м3).
Более того, выполнение тяжёлой физической работы в сложных условиях, нередко при повышенной температуре, и необходимость общаться для выполнения работы, не позволяют использовать СИЗОД своеввременно – вообще. Негативное влияние на рабочего (повышенное сопротивление дыханию, снижение концентрации кислорода и повышение концентрации углекислого газа во вдыхаемом воздухе, повышенные температура и влажность вдыхаемого воздуха, давление на лицо и др.) также стимулируют рабочего не использовать СИЗОД, а субъективные ощущения органов чувств не всегда позволяют определить, что запылённость превышает ПДКрз.
Использование заведомо недостаточно эффективных СИЗОД в условиях, не позволяющих применять их своевременно - не может обеспечить профилактику профзаболеваний. Но они большей частью не выявляются и не регистрируются. Например, в Ростовской области в 2012г было выявлено 66 случаев профзаболеваний[V- 6], в то время как в Новой Зеландии в том же году (при схожей численности населения) - 17÷20 тысяч. Не-выявление заболеваний приводит к отсутствию ответственности работодателя, не принимающего должных мер к улучшению условий труда, и к полному отсутствию ответственности изготовителей СИЗОД, декларирующих в рекламных целях сверхвысокую эффективность своей продукции (например, в США научно обоснованные государственные ограничения запрещают применять полумаски при концентрации вредных веществ более 10 ПДКрз, а в РФ ОАО «АРТИ» предлагает полумаску с коэффициентом защиты более 5000...).
В результате ухудшения условий труда (и вопреки широкомасштабному использованию эффективных СИЗ, объём продаж которых за последние годы возрос в 5 раз[V- 7]), смертность среди трудоспособного населения в РФ в 4.5 раз выше, чем в Европейском Союзе, и страна продолжает вымирать в мирное время и при отсутствии стихийных бедствий (природного характера).
В этом документе представлены рекомендации по защите рабочих от вдыхания пыли с помощью средств коллективной защиты, которые используются в США и других развитых странах. Они могут быть полезны при планировании и проведении работ по улучшению условий труда с учётом современного развития науки и уровня техники. Во многих случаях выполнение приведённых рекомендаций позволяет избежать применения СИЗОД (по крайней мере – как основного и единственного средства защиты). Это соответствует конвенции 1977г Международной Организации Труда (№ 148) "Конвенция о защите работников от профессионального риска, вызываемого загрязнением воздуха, шумом и вибрацией на рабочих местах" (ратифицирована РФ), статьи 9 и 10 которой однозначно рекомендует использовать в первую очередь технические средства коллективной защиты, и лишь при их недостаточной эффективности - респираторы.
Формулы для вычислений значений в системе СИ помечены «(СИ)», а исходные формулы (для единиц измерения фунты, футы и т.п.) помечены «(IP)» и выделены курсивом.
См. также:
Рекомендации NIOSH по снижению концентрации пыли в зоне дыхания при подземной добыче угля
Статьи о завышении эффективности СИЗ органов дыхания
Медицина труда и промышленная экология №4/2013
Токсикологический вестник №6/2014
.
ССЫЛКИ
- ↑ Измеров Н.Ф., Кириллов В.Ф. ред. Гигиена труда. — Гэотар-медиа. — Москва, 2010. — С. 180. — 592 с. — 2000 экз. — ISBN 978-5-9704-1593-1.
- ↑ British Standard BS 4275:1997 «Guide to implementing an effective respiratory protective device programme».
- ↑ Стандарт ФРГ DIN EN 529:2006 Atemschutzgeräte — Empfehlungen für Auswahl, Einsatz, Pflege und Instandhaltung.
- ↑ “ … Смертность трудоспособного населения в РФ превышает аналогичный показатель по Евросоюзу в 4.5 раза, и в 2.5 раза средний показатель по России.
- … на большинстве предприятий сложилась неблагополучная, а нередко критическая ситуация с условиями труда
- … практически каждый третий работник трудится в условиях, не отвечающих санитарно-гигиеническим требованиям.
- … Обеспеченность средствами индивидуальной защиты органов дыхания не превышает 60-79%.
- ... Однако регистрируемый уровень хронической профессиональной заболеваемости не отражает истинной ситуации, связанной с состоянием условий труда на производстве“
- ↑ Кириллов В.Ф., Филин А.С., Чиркин А.В. Обзор результатов производственных испытаний средств индивидуальной защиты органов дыхания (СИЗОД) // ФБУЗ "Российский регистр потенциально опасных химических и биологических веществ" Роспотребнадзора. Токсикологический вестник. — Москва, 2014. — № 6 (129). — С. 44-49 Wiki PDF. — ISSN 0869-7922.
- ↑
- Проведённые нами исследования выявили следующие тенденции: более ранее присоединение тяжёлых осложнений обусловило и раннюю инвалидизацию шахтёров с профзаболеваниями, срок развития которой от момента постановки первичного диагноза сократился более чем в 60 раз: с 20 лет в 1960-х годах предыдущего столетия до 4 месяцев в настоящее время. ...
- Наконец, за полувековой период почти в 10 раз, с 38 до 4 лет, сократился средний срок дожития шахтёров с момента постановки диагноза профзаболевания ...
- И.H. Пиктушинская. "Медицина труда и экология" (приложение к "Охрана труда. Практикум") №2 2013, №2 2014.
- ↑ Экономика и жизнь, 25.03.2013 За последние пять лет объём приобретаемых в России средств индивидуальной защиты, в рублёвом эквиваленте, вырос в пять раз
Введение[править]
При добыче и переработке минеральных полезных ископаемых для получения конечного продукта, они дробятся, размалываются, обогащаются, высушиваются, сепарируются по размерам. Эти операции механизированы, и их выполнение может привести к образованию большого количества пыли. При использовании недостаточно эффективных технических средств коллективной защиты, концентрация респирабельной пыли в воздухе может достичь опасного уровня, и создать угрозу для здоровья рабочих. Поэтому федеральное законодательство (США) установило ограничения концентрации пыли, воздействующей на шахтёров. Для уменьшения концентрации пыли и её воздействия на рабочих используют технические средства.
В этом руководстве слово “пыль” используется для обозначения маленьких твёрдых частиц, возникающих при механическом разрушении материала. В зависимости от размера, такие частицы могут стать опасными для здоровья рабочих – особенно при попадании в воздух. Наибольший размер частиц, которые могут попасть в воздух под воздействием ветра ~ 60 мкм. Это примерно соответствует толщине человеческого волоса. Если размер частиц от 60 до 2000 мкм, то они тоже могут попасть в воздух, но высота их подъёма (обычно) не превышает ~0.9 м, и затем они снова падают вниз. А частицы крупнее ~2000 мкм (2 мм) обычно перекатываются или “переползают” с места на место при воздействии ветра[В 1].
Крупные частицы могут воздействовать на носовые проходы, вызывая раздражение и заложенный нос, а при попадании в горло они могут вызвать раздражение и кашель. При вдыхании более опасны частицы пыли меньшего размера, которые могут оставаться в воздухе во взвешенном состоянии часами. В общем, чем меньше аэродинамический диаметр частицы пыли, которую вдохнул человек, тем выше вероятность того, что она сможет глубоко проникнуть в органы дыхания, прежде чем осядет на их стенки.
В развитых странах разработаны методы измерения концентрации пыли, которые позволяют определить – какая доля от уловленной пыли попадает в определённый диапазон аэродинамических диаметров частиц. Например, пробоотборные устройства, измеряющие концентрацию вдыхаемой пыли, улавливают около 97% частиц меньших 1 мкм (аэродинамический диаметр), но только половину частиц диаметром 100 мкм [В 2]. А устройства для измерения концентрации респирабельной пыли более избирательно улавливают такие частицы, которые лучше оседают в той части лёгких, где происходит газообмен. Они улавливают около половины частиц с аэродинамическим диаметром 4 мкм. А эффективности улавливания частиц других размеров – иная: для частиц 10 мкм – около 1%, а для частиц менее 1 мкм – около 97%[В 2]. Такие маленькие частицы – по отдельности – невидимы для невооружённого глаза.
За выполнением требований федерального законодательства США в области техники безопасности и охраны труда при добыче полезных ископаемых следит Управление по охране труда при добыче полезных ископаемых Mine Safety and Health Administration (MSHA). Это Управление, входящее в состав Минтруда США, было создано в соответствии с Законом об охране труда на шахтах 1977г (Federal Mine Safety and Health Act of 1977). Управление имеет полномочия разрабатывать и пересматривать стандарты по охране труда, обязательные для выполнения работодателем, для сохранения жизни и предотвращения несчастных случаев и профзаболеваний шахтёров. Эти требования приводятся в главе 1 раздела 30 свода федеральных законов (Chapter 1 of Title 30, Code of Federal Register CFR). В документе установлены ПДКрз для разных химических веществ (респирабельная пыль), и ограничение 10 мг/м3 для всей пыли по массе. Но если в пыли может быть кварц, то проводится замер концентрации респирабельной пыли, и с помощью рентгеновской дифракции (Аналитический метод NIOSH 7500[В 3]) измеряется содержание кварца в пыли. В респирабельной пыли чаще всего кристаллический кварц встречается в трёх распространённых формах - кварц, тридимит и кристобалит. Если содержание кварца превышает 1%, то ПДКрз по респирабельной пыли вычисляется по формуле:
- ПДКрз (респирабельная пыль) = 10 мг/м3 / (содержание респирабельного кварца [%] + 2)
Выполнение такого ограничения предотвращает воздействие респирабельного кварца при концентрации свыше 100 мкг/м3. Национальный институт охраны труда (NIOSH) рекомендует для респирабельного кварца ПДКрз 50 мкг/м3 для 10-часовой смены и 40-часовой рабочей недели[В 4]. А для тридимита и кристобалита ПДКрз равна половине значения, вычисленного по формуле выше для кварца.
С учётом указанных требований законодательства, при добыче и переработке полезных ископаемых важно определить, когда концентрация респирабельной пыли в зоне дыхания рабочих превышает допустимую, и (в этих случаях) разработать, установить и обеспечить эффективную работу технических средств коллективной защиты, описанных в этом руководстве (если это необходимо). С этой целью Национальная ассоциация производителей и переработчиков промышленных песка NISA недавно опубликовала второе издание "Occupational Health Program for Exposure to Crystalline Silica in the Industrial Sand Industry" [В 5]. В документе приводится информация, необходимая для правильного измерения и оценки воздействия пыли на рабочих.
Вдыхание пыли кварца и возможные последствия для здоровья[править]
Как сообщалось в документе "NIOSH Hazard Review: Health Effects of Occupational Exposure to Respirable Crystalline Silica", вдыхание респирабельной пыли, содержащей кварц, может привести к нескольким серьёзным последствиям для здоровья – развитию силикоза, туберкулёза, хронического бронхита, эмфиземы и хронической почечной болезни[В 6]. Кроме того, по мнению специалистов NIOSH кристаллический кварц является потенциальным канцерогеном[В 6][В 7] 54 Fed. Reg. 2521 (1989)].
Силикоз обычно развивается при вдыхании пыли кристаллического кварца. Это заболевание неизлечимо, необратимо и потенциально смертельно. Кварц является одним из самых распространённых минералов в земной коре, и при проведении многих видов горных работ приходится разрушать породу или руду, содержащую кварц. Поэтому большинство людей, занятых добычей полезных ископаемых, могут подвергаться воздействию кристаллического кварца во время бурения, дробления, сепарации по размерам, перемещения и погрузки.
При вдыхании мелкодисперсной респирабельной пыли, частицы могут проникать глубоко в лёгкие и достигать альвеол. Осевшие в альвеолах частицы кристаллического кварца могут стимулировать воспалительный токсический процесс, который в конечном итоге может перерасти в клинически выраженный силикоз. В зависимости от концентрации респирабельного кристаллического кварца, и длительности его вдыхания, у рабочих может развиться одна из нескольких форм силикоза[В 6]:
- Хронический силикоз – развивается при длительном чрезмерном воздействии кристаллического кварца, и впервые становится клинически заметным после 10-30 лет после первого воздействия;
- Ускоренный силикоз - развивается при воздействии кристаллического кварца при большой концентрации, и впервые становится клинически заметным через 5-10-30 лет после первого воздействия;
- Острый силикоз – развивается при воздействии кристаллического кварца при (необычно) очень большой концентрации кварца, и становится клинически заметным через короткий период времени после первого воздействия – от недель до 5 лет.
Наиболее распространённой формой заболевания является хронический силикоз, который возникает после многих лет вдыхания пыли кристаллического кварца и приводит к образованию характерных узловых рубцов в лёгких. Со временем начальные небольшие узелки могут слиться в большие фиброзные массы, и такое состояние называют прогрессивным массивным фиброзом (ПМФ). Ускоренный силикоз встречается гораздо реже хронического, но развивается гораздо быстрее. Острый силикоз встречается наиболее редко, и это самая серьёзная и самая смертельно опасная форма заболевания. В отличие от хронического и ускоренного силикоза – когда флюорография обычно показывает разбросанные небольшие (и, возможно, также большие) потемнения, при остром силикозе флюорографические снимки показывают его похожим на диффузионную пневмонию. Это проявление объясняется обширным повреждением слизистой оболочки лёгких, из-за которого альвеолы наполняются жидкостью, содержащей белок, разлагающиеся клетки и другие материалы[В 8].
При развитии силикоза не у всех рабочих будут явно выраженные симптомы заболевания. У части людей с хроническим силикозом нет заметных симптомов – несмотря на наличие характерных признаков на флюорографических снимках. Но у многих рабочих с хроническим силикозом симптомы будут развиваться с течением времени, а у тех, кто болен острым или ускоренным силикозом симптомы (могут появится) до того, как будет поставлен диагноз. Хотя силикоз неизлечим, но его разные симптомы – боль в груди, неконтролируемый кашель, одышка - ослабляют больного, и требуют терапии. Кроме того, у больных силикозом выше риск развития туберкулёза и других инфекционных заболеваний[В 6][В 8].
В этом введении показана необходимость снижения воздействия респирабельной пыли кварца на рабочих. Описанные в этом руководстве способы снижения концентрации пыли до ПДКрз применимы не только для пыли кварца, но и для других видов пыли. Хотя это руководство разрабатывалось для использования при снижении запылённости при добыче и переработке полезных ископаемых, но изложенные здесь методы могут использоваться для снижения запылённости и на предприятиях других отраслей.
.
ССЫЛКИ
- ↑ EPA (1996). Air quality criteria for particulate matter, Vol. 1. Research Triangle Park, NC: National Center for Environmental Assessment, Office of Research and Development, Environmental Protection Agency.
- ↑ 2,0 2,1 ACGIH [2007]. 2007 Threshold limit values for chemical substances and physical agents and biological exposure indices. Cincinnati, OH: American Conference of Governmental Industrial Hygienists.
- ↑ NIOSH [2003]. NIOSH manual of analytical methods, 4 ed., 3rd supplement. Cincinnati, OH: U.S. Department of Health and Human Services, Centers for Disease Control and Prevention, National Institute for Occupational Safety and Health, DHHS (NIOSH) Publication No. 2003–154.
- ↑ NIOSH [1974]. NIOSH criteria for a recommended standard: occupational exposure to crystalline silica. Cincinnati, OH: U.S. Department of Health, Education, and Welfare, Public Health Service, Center for Disease Control, National Institute for Occupational Safety and Health, DHEW (NIOSH) Publication No. 75–120.
- ↑ NISA [2010]. Occupational health program for exposure to crystalline silica in the industrial sand industry, 2nd ed. Washington, DC: National Industrial Sand Association.
- ↑ 6,0 6,1 6,2 6,3 NIOSH [2002]. NIOSH hazard review: health effects of occupational exposure to respirable crystalline silica. By: Schulte PA, Rice FL, Key-Schwartz RJ, Bartley DL, Baron P, Schlecht PC, Gressel M, Echt AS. U.S. Department of Health and :Human Services, Centers for Disease Control and Prevention, National Institute for Occupational Safety and Health, DHHS (NIOSH) Publication No. 2002–129.
- ↑ 54 Fed. Reg. 2521 [1989]. Occupational Safety and Health Administration: air contaminants; final rule; silica, crystalline-quartz. (Codified at 29 CFR 1910.)
- ↑ 8,0 8,1 Davis GS [2002]. Silicosis. In: Hendrick DJ, Burge PS, Beckett WS, Churg A, eds. Occupational disorders of the lung: recognition, management, and prevention. W.B. Saunders, pp. 105–127.
ГЛАВА 1. Принципы пылеулавливания[править]
Для снижения концентрации пыли и уменьшения попадания респирабельной пыли в органы дыхания рабочих при переработке минерального сырья в США чаще всего используют технические средства коллективной защиты – пылеулавливающее вентиляционное оборудование. Хорошая вентиляционная система имеет ряд достоинств, и она уменьшает загрязнение воздуха, что повышает производительность труда и сохранение ценного продукта.
При переработке минерального сырья чаще всего используют местные вентиляционные отсосы (local exhaust ventilation systems LEVs). Они улавливают пыль, образующуюся во время разных этапов переработки сырья (дробление, размол, сепарация по размерам, сушка, фасовка, погрузка) и переносят пыль по воздуховодам к пылеуловителям. Улавливая пыль в месте её попадания в воздух, местные отсосы предотвращают загрязнение воздуха рабочей зоны и попадание пыли в органы дыхания рабочих.
Местные отсосы используют создание разрежения в укрытии для улавливания пыли до того, как она попадёт в воздух рабочей зоны. В эффективной вентиляционной системе обычно есть улавливающее приспособление (кожух, укрытие, вытяжка и т.п.), спроектированное так, чтобы улучшить улавливание в максимальной степени.
Использование местных вентиляционных отсосов даёт ряд преимуществ:
- Захват и удаление мелкодисперсных частиц, которые трудно уловить при попадании в воздух;
- Возможность или использовать уловленный продукт в технологическом процессе, или не использовать его так, чтобы он не влиял на процесс;
- Возможность беспрепятственной и стабильной работы при температуре ниже 0°С – что не всегда возможно использовании мокрых методов пылеподавления.
Кроме того, такой способ снижения запылённости может быть единственно возможным в тех случаях, когда улавливаемая пыль гигроскопична, или когда даже при небольшой влажности могут возникнуть проблемы (например – при обработке глины или сланца) и т.п.
В большинстве случаев образование пыли происходит очевидным способом. Каждый раз, когда сухой материал перемещается, обогащается, или перерабатывается, с большой вероятностью может образовываться пыль. А при попадании пыли в воздух, последний становится опасным для здоровья рабочих. Кроме того, при большой концентрации пыли ухудшается обзор, что ухудшает безопасность рабочих.
Обычно образование пыли, требующее использования систем обеспыливания, происходит в 5 случаях:
- В местах перегрузки материала в транспортных системах – когда он падает при передаче от одной части транспортной системы к другой. Например, это происходит при перегрузке с одного ленточного транспортёра на другой, или при сбросе в бункер, или в ковшовый элеватор.
- При дроблении, размалывании, просеве, сушке, смешивании, выгрузке из мешков, погрузке в грузовики и вагоны.
- При выполнении операций, при которых происходит вытеснение воздуха – наполнение мешков, паллетирование или пневматическое заполнение ёмкостей (бункеров и т.п.).
- На открытом воздухе, когда потенциальный источник пыли не может контролироваться, например – при колонковом бурении и взрывных работах.
- На открытом воздухе – на дорогах, складах и других местах с грунтовым покрытием, где происходит перемещение материала, который может быть источником пыли (при разных работах и при сильном ветре).
Хотя в случаях 4 и 5 может образоваться много пыли, они обычно не учитываются при проектировании вентиляционной системы предприятия, так как они охватывают большую территорию и условия (в таких местах) непредсказуемы. Поэтому в таких случаях требуется использовать другие методы, отличающиеся от вентиляции. Они рассмотрены в последних главах этой книги.
Проектирование и применение обеспыливающего оборудования связано с решением нескольких разных технических задач – эффективное использование имеющегося пространства; (определение) расстояния, на которое нужно проводить воздуховоды; учёт того, насколько легко будет использовать уловленную пыль в технологическом процессе; использование электрического оборудования; и выбор подходящих пылеуловителей. Также при проектировании системы обеспыливания нужно решить – какой она будет: одной (централизованной), или в виде нескольких систем для отдельных (групп) источников пыли. При проектировании требуется правильно поставить задачу, для каждого случая выбрать наиболее подходящее оборудование, и для каждого конкретного случая и конкретной операции спроектировать наилучшую пылеулавливающую систему.
В этой главе сделано много ссылок на руководство по проектированию промышленной вентиляции “Industrial Ventilation: A Manual of Recommended Practice for Design”, созданное американской организацией, объединяющей специалистов в области промышленной гигиены ACGIH[1- 1], и в настоящем документе использовано несколько рисунков из этого руководства. Всем, кого интересует защита рабочих от пыли при добыче и переработке минеральных полезных ископаемых с помощью (вентиляционных) пылеулавливающих систем, и особенно инженерам, которые проектируют такие системы, следует считать руководство ACGIH исходным источником информации. А информация, приведённая в этой главе, будет дополнять содержание руководства ACGIH.
Основы работы пылеулавливающих систем[править]
Хорошо спроектированная обеспыливающая система должна учитывать не только (свойства) пыли как потенциального загрязнения, но и характерные черты пылеулавливающих систем. При определении свойств пыли как потенциальной угрозы для рабочих нужно ответить на ряд вопросов. Требуется определить: размеры частиц и их распределение по размерам, их форму и физические свойства, и количество пыли, попадающей в воздух. Размеры частиц показывают, насколько пылинки крупные или мелкие, и для этого обычно используют границы диапазона размеров (верхнюю и нижнюю). Размеры частиц обычно измеряют в микронах (1 µм = 1 мкм = 10-6 м = 0.001 мм). Респирабельными частицами, (наиболее) опасными для здоровья рабочих, считают частицы с размером ≤ 10 мкм. Для сравнения, ячейка сетки 325 mesh соответствует частице размером около 44 мкм, и это (примерно) наименьший размер частицы, которую можно увидеть невооружённым глазом. Крупные пылинки гораздо лучше улавливаются пылеулавливающими системами, и в этом часто помогает сила тяжести.
Форма частиц влияет на их улавливание и на то, насколько хорошо они отделяются от (тканевого) фильтровального материала. Форма частиц – это термин, который обычно используется в аэрозольной технологии, а для описания диаметров частиц аэрозоля часто используют термин “аэродинамический диаметр”. Аэродинамический диаметр частицы – это диаметр такой сферической частицы, у которой плотность равна 1000 кг/м3 (стандартная плотность капли воды), и которая оседает в неподвижном воздухе под действием силы тяжести с той же скоростью, что и рассматриваемая частица[1- 2]. Аэродинамический диаметр частиц широко используют при проектировании фильтрующих установок и воздухоочистителей. Кроме этого, при проектировании пылеулавливающей системы важными обстоятельствами, влияющими на выбор пылеуловителя, и на другие части системы, является температура и влажность воздуха.
Поток воздуха и пылеулавливание[править]
Для того, чтобы регулировать потоки воздуха в вентиляционной системе, нужно учитывать расходы воздуха, скорости потоков, температуры, и использовать параметры потоков – статическое давление (SP, Static Pressure) и скоростной напор (VP, Velocity Pressure).
Скорость воздуха измеряется в метрах в секунду (футах в минуту, 1 ф/мин ~ 18.3 м/мин ~ 0.3 м/с). Расход воздуха измеряют в кубических метрах в секунду или в час (кубических футах в минуту, 1 куб фут/мин ~ 28.3 л/мин = 1.7 м3/час) – это количество воздуха, используемого в вентиляционной системе. Температура воздуха измеряется в градусах Цельсия (С) или Фаренгейтера (F). Она используется для определения возможного применимого типа уплотнений и фильтровального материала. Во многих случаях улавливание пыли происходит при высокой температуре воздуха (печи для обжига, доменные печи, сушилки).
При проектировании вентиляционных систем давление обычно измеряют в Паскалях (дюймах водяного столба, 1 дюйм wg = 25.4 мм вод. столба ~ 249 Па). Давлением в вентиляции обычно называют статическое давление, создаваемое вентилятором. Статическое давление равно разнице между давлением в воздуховоде и атмосферным давлением. Отрицательное статическое давление (разрежение) стремится сжать стенки воздуховода, а избыточное – раздвинуть.
Статическое давление используется для преодоления сопротивления вентиляционной системы (Hl, head loss), которое складывается из двух частей – сопротивления трения в воздуховодах и соединениях (Hf, frictional losses), и местных сопротивлений отдельных частей системы - таких, как циклоны и пылеуловители (Hx, shock losses)[1- 3]. Для измерения статического давления используют трубку Пито, которую вставляют в воздуховод параллельно боковой стенке, что позволяет определить отличие между атмосферным давлением и давлением в воздуховоде (Рис. 1.1).
При движении в воздуховоде с определенной скоростью, воздух создаёт дополнительное скоростное давление – динамическое давление, или скоростной напор (Velocity Pressure VP). Динамическое давление – это давление, которое требуется для того, чтобы разогнать покоящийся воздух до заданной скорости. Оно существует только тогда, когда воздух движется, и направлено в сторону его движения. Значение скоростного напора всегда положительно. Для измерения скоростного напора в вентиляции используют пробоотборный зонд, помещаемый в поток воздуха. Сумма статического давления и динамического давления равна полному давлению (Total Pressure TP)[1- 3]:
- TP = SP + VP (Уравнение 1.1) (СИ, IP)
- где TP = полное давление;
- SP = статическое давление; и
- VP = скоростной напор, или динамическое давление. Единицы измерения – Па (или дюймы вод. столба).
В руководстве ACGIG “Industrial Ventilation: A Manual of Recommended Practice for Design”[1- 1], приводится ряд определений и уравнений, которые используются для описания движения воздуха в воздуховодах вентиляционной системы. В этом руководстве также подробно описаны параметры воздуха, движущегося в вентиляционной системе и выбрасываемого из неё. А в руководстве Martin Engineering, Foundations: The Practical Resource for Cleaner, Safer, More Productive Dust & Material Control[1- 4], тоже есть глава, посвящённая измерению движения воздуха, и раздел об эффективном измерении расхода воздуха. Наконец, можно рекомендовать статью в журнале "Dust Control System Design: Knowing your Exhaust Airflow Limitations and Keeping Dust out of the System"[1- 5].
Проектирование вытяжной вентиляционной системы[править]
Все – простые и сложные – вытяжные вентиляционные системы состоят из схожих составных частей: укрытия (кожуха, вытяжного зонта), воздуховодов, пылеуловителя и вентилятора (Рис. 1.2). В руководстве ACGIH “Industrial Ventilation: A Manual of Recommended Practice for Design”[1- 1], подробно рассмотрены все аспекты таких систем. Для того, чтобы дополнить упомянутое руководство, ниже рассмотрены некоторые из основных параметров вентиляционных систем, используемые при проектировании, и более подробно рассмотрены некоторые из упомянутых аспектов. В дополнение к руководству ACGIH, в настоящем документе рассмотрены некоторые из основных параметров, используемые при проектировании, и проблемы, связанные с использованием воздуховодов при большой и при маленькой скорости запылённого воздуха.
Укрытия, вытяжные зонты[править]
Укрытия (кожухи, вытяжные зонты) конструируются так, чтобы они соответствовали свойствам перерабатываемой руды или продукта. Хорошо сконструированное укрытие является важной частью обеспыливающей вентиляционной системы, так как если оно не сможет обеспечить улавливание пыли, то остальные части системы станут бесполезны. Если укрытие хорошо сконструировано, то оно создаёт поток воздуха с таким расходом и таким направлением движения, что тот захватывает пыль и переносит её в вентиляционную систему. Эффективность укрытия оценивается по его способности побуждать запылённый воздух двигаться в сторону всасывающего отверстия воздуховода в производственных условиях.
Отличия при выдувании струи воздуха по отношению к всасыванию воздуха[править]
Рассматривая эффективность укрытий вытяжной вентиляционной системы, нужно учесть ограничения такой системы, то есть - ограниченные возможности местных отсосов улавливать загрязнённый воздух. Это наиболее наглядно проявляется при сравнении свойств потоков воздуха, всасываемого и выдуваемого из воздуховода. Поток воздуха, выдуваемый из отверстия воздуховода (после вентилятора) продолжает двигаться в первоначальном направлении на большом расстоянии от отверстия. Например, при выдувании из круглого отверстия трубы диаметром D, на удалении 30 D от отверстия скорость в центре потока снижается до ~10% от первоначальной (Рис. 1.3). Струя выдуваемого воздуха стремится принять цилиндрическую форму, и вовлечь в движение окружающий воздух (этот процесс обычно называют индукцией). А при всасывании воздуха, его скорость становится равной 10% от скорости в поперечном сечении всасывающего отверстия на расстоянии всего лишь одного диаметра отверстия.
При всасывании воздух стремиться двигаться в сторону всасывающего отверстия воздуховода - со всех сторон, и “струя” всасываемого воздуха имеет примерно сферическую форму – в отличие от конической при выдувании. Другое важное отличие относится к снижению скорости воздуха с увеличением расстояния до отверстия. Скорость воздуха снижается до ~10% в центре струи выдуваемого воздуха на расстоянии 30 диаметров от отверстия; а при всасывании – всего лишь на расстоянии один диаметр. Это показывает, насколько важно для проектирования эффективного укрытия приблизить его к источнику пыли.
Типы укрытий, зонтов[править]
Существуют разнообразные конструкции всасывающих частей вентиляционной системы, и обычно их можно разделить на три типа: кожух (укрытие); улавливающий вытяжной зонт (capturing hood); и принимающее вентиляционное отверстие (receiving hood).
Укрытие – это кожух, который частично или полностью закрывает источник пыли, что обеспечивает такой характер движения воздуха, что пыль уносится в вентиляционную систему и предотвращается её попадание в окружающий воздух. Самый лучший способ улавливания пыли – использование такого кожуха, который полностью закрывает источник пыли. Количество отверстий в кожухе сводится к минимуму за счёт устройства дверей и люков, обеспечивающих требуемый доступ к источнику пыли. Такие укрытия обычно используются тогда, когда доступ к оборудованию, которое является источником пыли, при нормальной работе не требуется, а открывание отверстий происходит, например, при начальной загрузке сырья, и при конечной выгрузке продукции. Такие типы укрытий используют при добыче и переработке полезных ископаемых, чаще всего – при дроблении, размоле, просеивании, разделении по размерам.
Когда требуется доступ к технологическому оборудованию или месту образования пыли, то часто используют неполное укрытие - будку или туннель. В этом случае важно обеспечить отсасывание такого количества воздуха, чтобы удалить пыль, попадающую в воздух, или хотя бы свести к минимуму её утечку из укрытия. Лучше всего это получается, если (удаётся) закрыть источник пыль как можно более полно. Для этого часто используют прозрачные пластиковые полосы, которые позволяют рабочим входить и выходить, но достаточно эффективно изолируют источник пыли от окружающего пространства. При использовании неполного укрытия (туннеля) требуется больший расход воздуха, чем при использовании кожуха, полностью закрывающего источник пыли.
В тех случаях, когда невозможно использовать полное или частичное укрытие, обычно используют улавливающие вытяжные зонты, которые устанавливают как можно ближе к источнику пыли. Так как источник пыли находится вне такого устройства, то для обеспечения эффективной работы вентиляционной системы крайне важно, чтобы вытяжной зонт смог уловить, засосать запылённый воздух. Он должен справиться с любым внешним движением воздуха, стремящимся унести запылённый воздух в сторону. Если пыль образуется в каком-то определённом месте, и удаётся приблизить устройство к этому месту на небольшое расстояние, то подобные вытяжные зонты могут быть очень эффективны,. Скорость движения воздуха в сторону улавливающего местному отсосу обратно пропорциональна квадрату расстояния от зонта. Когда это расстояние становится слишком большим, он становится неэффективным, и нужно изучить возможность использования сдувающе-всасывающей (push-pull) вентиляционной системы (Рис. 1.4). В сдувающе-всасывающей вентиляционной системе выпускаемая струя воздуха увлекает за собой окружающий воздух так, чтобы создать поток, преодолевающий большое расстояние до улавливающего отверстия вентиляционной системы. Сопло, выпускающее сдувающую струю воздуха, обычно размещают прямо напротив источника пыли, и направляют в сторону улавливающего отверстия. Движение выпущенной струи воздуха в сторону улавливающего отверстия вовлекает в движение окружающий загрязнённый воздух. Это делается для того, чтобы весь движущийся воздух попал в улавливающее отверстие. Сочетание такого сопла, выпускающего струю воздуха, с улавливающим вентиляционным отверстием, позволяет получить хорошую эффективность вентиляционной системы.
Третий, самый редко используемый тип – принимающее вентиляционное отверстие (Рис. 1.5). Обычно он размещается близко к месту образования пыли, и не позволяет ей разлетаться в окружающее пространство. В большинстве случаев такие принимающие вентиляционные отверстия делают небольшими по размеру. При улавливании пыли они используют инерцию частиц для уменьшения требуемой скорости воздуха. Принимающие вентиляционные отверстия редко используют при добыче и переработке минеральных полезных ископаемых, и часто – в небольших установках и инструментах, используемых на заводах и в лабораториях.
Конструкция укрытия, зонта[править]
Самыми главным параметрами конструкции укрытия являются:
- Расход воздуха, всасываемого вентиляционной системой через него.
- Положение.
- Форма.
Из трёх этих параметров, расход воздуха через укрытие является самым важным. Как упоминалось ранее, если укрытие не обеспечивает улавливание пыли, то остальная часть вентиляционной системы становится бесполезной. А при недостаточном расходе воздуха укрытие не может предотвратить распространение пыли за его пределы – в окружающий воздух. Чтобы внутри укрытия сохранялось достаточное разрежение, для новых укрытий, у которых зазоры меньше, требуется меньший расход воздуха, чем для старых укрытий, у которых зазоры больше. Из-за этого объёмный расход воздуха (м3/час) у одинаковых источников пыли может сильно отличаться – хотя улавливание пыли может быть достаточно хорошим во всех случаях.
В таблице 1.1 приводятся приблизительные значения расхода воздуха, при котором обеспечивается предотвращение утечек пыли от перечисленного оборудования.
Оборудование | Расход воздуха, м3/час [cfm] |
---|---|
Ковшовый элеватор – хорошо герметизированный | По 680 [400] вверху и внизу элеватора |
Ковшовый элеватор – хорошо герметизированный | 1360 [800] только вверху элеватора |
Ременной конвейер | 1700-2550 [1000-1500] на каждом месте перегрузки |
Медленно двигающееся колеблющееся сито | 510-850 [300-500] вытяжка |
Быстро двигающееся вибрирующее сито | Длина периметра уплотнения × 425 (1/м) [ × 250 1/ft] |
Сито | 510-850 [300-500] на каждом месте выгрузки материала |
Загрузочное выпускное отверстие | 1360-2038 [800-1200] |
Бункер для хранения материала | 510-680 [300-400] |
Вытяжные зонты, навесы | 4570 на каждый м2 площади занавеси вокруг навеса [ 250 cfm на каждый кв фут ] |
При использовании значений расхода воздуха, указанных в таблице 1.1, нужно учитывать то, что при подаче материала в бункер он увлекает туда за собой дополнительный воздух, и этот дополнительный расход воздуха должен учитываться для получения того расхода воздуха, который требуется отсасывать из бункера во время его заполнения.
Для обеспыливания другого оборудования (например – фасовочные, упаковочные машины, дробилки, магнитные сепараторы, паллетайзеры и т.п.) можно использовать тот расход воздуха, который рекомендуется их изготовителем. В некоторых случаях могут возникнуть противоречия между необходимостью установить укрытие, хорошо закрывающее пылящее оборудование и позволяющее предотвратить распространение пыли, и необходимостью обеспечить доступ к оборудованию для его обслуживания и во время работы. В таких редких случаях может потребоваться установить в укрытие всё оборудование, например – путём размещения вытяжного зонта над оборудованием и подвески гибкой занавеси по периметру вытяжки.
При определении расхода отсасываемого воздуха нужно учесть два обстоятельства – вовлечение воздуха в движение и скорость захвата частиц.
Вовлечение воздуха в движение
Вовлечение воздуха в движение происходит тогда, когда материал, падая вниз, передаёт импульс окружающему воздуху (Рис. 1.6). Из-за этой передачи энергии поток воздуха всегда движется вместе с падающим материалом. Например, при подаче песка в элеватор по жёлобу, песок будет увлекать за собой воздух (в элеватор). Этот воздух нужно удалить из корпуса (кожуха) элеватора с помощью вытяжной вентиляции, или же он найдёт другой выход, сделав элеватор источником загрязнения воздуха предприятия.
Для приближённой оценки того, какой расход воздуха нужен для компенсации вовлечения воздуха в движение материалом, можно использовать уравнение, учитывающее расход материала, высоту свободного падения, размер кусков материала и площадь поперечного сечения приёмного отверстия:
- Q = 0.1157 × Au × (R × S2 / D)1/3 (м3/с) = 416.5 × Au × (R × S2 / D)1/3 (м3/час) (Уравнение 1.2) (СИ)
- Q = 10 × Au × (R × S2 / D)1/3 (Уравнение 1.2) (IP)
- (коэффициенты 0.1157 и 416.5 используется вместо коэффициента 10 для исходных данных в метрах и кг/сек; а коэффициент 10 – для исходных данных в футах и тоннах/час)
- где Q = расход воздуха м3/сек, м3/час [cubic feet per minute];
- Au = площадь отверстия в укрытии, через которое в него подаётся материал, м2 [square feet];
- R = расход подаваемого материала, кг/сек [тонн в час];
- S = высота падения материала, м [feet]; и
- D = средний размер кусков материала, м [feet].
Самым важным параметром в этом уравнении является Au – площадь отверстия, в которое подаётся материал, через которое входит вовлекаемый в движение воздух (площадь поперечного сечения приёмного отверстия). Чем меньше площадь отверстия, тем меньше Au, и тем меньше требуемый расход удаляемого воздуха. Также, чем меньше высота падения материала S, тем меньше нужно отсасывать воздуха. При проектировании оборудования, которое будет перемещать материал, важно уменьшить значения S и Au до минимально возможных, чтобы предотвратить чрезмерное пылеобразование и снизить расход воздуха у вентиляционной системы. Значения расхода подаваемого материала R и среднего размера кусков материала D тоже влияют на требуемый расход воздуха, но при добыче или переработке полезных ископаемых они обычно постоянны.
Расход воздуха (Q) для вытяжки тоже можно оценить с помощью определения вовлечения воздуха в движение. Это важно учитывать, так как стандартные таблицы или графики могут не учитывать некоторые факторы, влияющие на необходимое количество отсасываемого воздуха. Нужно проводить вычисления с учётом вовлечения воздуха в движение, и сравнивать результат с опубликованным стандартным (внося поправки, если это кажется необходимым).
Скорость захвата частиц
Скорость захвата частиц (capture velocity) – это показатель того, какой расход воздуха требуется для захвата частиц, выходящих из источника, и их перемещения во входное отверстие вентиляционной системы. Скорость захвата должна быть достаточно большой для того, чтобы преодолеть все препятствующие (захвату) факторы, и внешнее движение окружающего воздуха. Опубликованы различные таблицы со значениями такой скорости для разных условий. При добыче и переработке полезных ископаемых диапазон таких скоростей обычно составляет 0.5-1.0 м/с [100-200 футов/мин], но в некоторых случаях может возрасти до 2.5 м/с [500 футов/мин]. В большинстве случаев значения скорости захвата были получены на основании многолетнего опыта эксплуатации различного оборудования в разных условиях.
После определения скорости захвата вычисляется соответствующий расход отсасываемого воздуха. Ниже приводится уравнение "DallaValle", применяемое для определения расхода воздуха для свободно стоящих укрытия и источника пыли (Рис. 1.07)[1- 6][1- 7]:
- Q = 1 × Vx × (10 × X2 + Ah) (м3/с) = 3600 × Vx × (10 × X2 + Ah) (м3/час) (Уравнение 1.3) (СИ)
- Q = 1.0 × Vx (10 × X2 + Ah) (Уравнение 1.3) (IP)
- (коэффициенты 1 и 3600 используется вместо коэффициента 1 при использовании метров и метров в секунду, а 1.0 – при использовании футов и футов/мин)
- где Q = расход отсасываемого воздуха, м3/с, м3/час [куб футов/мин];
- Vx = скорость воздуха, требуемая для захвата частиц в наиболее удалённом от укрытия, м/с [фут/мин];
- X = расстояние от укрытия до наиболее удалённого места захвата пыли, м [фут]; и
- Ah = площадь поперечного сечения отверстия укрытия, м2 [кв. футов].
Уравнение показывает, что скорость воздуха, размер отверстия укрытия и расстояние от укрытия до источника пыли влияют на требуемое количество отсасываемого воздуха. Очень важно расстояние до источника пыли (Х), так как оно влияет на расход во второй степени.
Также нужно отметить, что при использовании свободно стоящего укрытия воздух всасывается в него не только со стороны источника пыли, но и с противоположной стороны, и с боковых сторон. Это уменьшает способность укрытия захватывать и удалять пыль из места её образования. Для уменьшения влияния всасывания ненужного воздуха есть несколько способов. Во-первых, если укрытие находится на (какой-то) поверхности, то необходимый расход воздуха снижается:
- Q = 1 × Vx (5 × X2 + Ah) (м3/с) = 3600 × Vx (5 × X2 + Ah) (м3/час) (Уравнение 1.4) (СИ)
- Q = 1.0 × Vx × (5 × X2 + Ah) (Уравнение 1.4) (IP)
(коэффициенты 1 и 3600 используется вместо коэффициента 1 при использовании метров и метров в секунду, а 1.0 – при использовании футов и футов/мин)
Другой способ – сделать фланцы по периметру отверстия укрытия, тогда расход вычисляется так:
- Q = 0.75 × Vx (10 × X2 + Ah) (м3/с) = 2700 × Vx (10 × X2 + Ah) (м3/час) (Уравнение 1.5) (СИ)
- Q = 0.75 × V (10 × Х2 + Ah) (Уравнение 1.5) (IP)
((коэффициенты 0.75 и 2700 используется вместо коэффициента 0.75 при использовании метров и м/сек, а 0.75 – при использовании футов и футов/мин))
Фланцы препятствуют всасыванию ненужного воздуха в укрытие сзади и с боков, и это крайне простая модификация конструкции укрытия для повышения его эффективности и снижения эксплуатационных расходов. В руководстве ACGIH Industrial Ventilation: A Manual of Recommended Practice for Design[1- 1] можно найти информацию о других факторах, влияющих на скорость захвата.
Другие параметры укрытия[править]
Когда пыль захватывается и всасывается в вентиляционную систему, при входе воздуха в неё происходит преобразование статического давления в динамическое и в потери из-за местного сопротивления укрытия. Уменьшение давления из-за местного сопротивления при входе в вентиляционную систему вычисляется с помощью уравнения:
- He = (K)(VP) = SPh = VP (Уравнение 1.6) (СИ, IP)
- где He = уменьшение давления из-за местного сопротивления входа в воздуховод, Па, [дюймы водяного столба];
- K = коэффициент сопротивления;
- VP = скоростной напор (динамическое давление) в воздуховоде, Па [дюймы водяного столба]; и
- SPh = абсолютное статическое давление в воздуховоде на расстоянии около 5 диаметров от входного отверстия, Па [дюймы водяного столба].
При входе воздуха в воздуховод происходит изменение давления, которое нужно вычислить для учёта влияния каждого их укрытий в той системе, где их несколько. На Рис. 1.8 показаны коэффициенты сопротивления для трёх разных конструкций укрытий, широко используемых при добыче и переработке полезных ископаемых. В первом ряду показаны три вида всасывающих отверстий по форме – круглое, квадратное и прямоугольное, и их коэффициент сопротивления. Во втором ряду показаны те же всасывающих отверстия с фланцами, и их коэффициент сопротивления. В третьем ряду показана конструкция круглого входного отверстия с плавным, закруглённым, колоколообразным (bell mouth) входом, и коэффициент сопротивления. Видно последовательное улучшение конструкции и соответствующее уменьшение сопротивления и потерь давления.
Контрольный список вопросов для оценки эффективности местного вентиляционного отсоса[править]
Ниже приводится список контрольных вопросов для определения того, насколько выбранная конструкция местного отсоса соответствует наилучшим рекомендуемым специалистами.
- Наиболее эффективный местный отсос должен улавливать всю поступающую пыль. Это практически полностью устраняет загрязнение окружающего воздуха и вдыхание пыли рабочими.
- Нужно свести к минимуму количество и размеры отверстий в кожухе (двери, люки и т.п.). Если же доступ необходим, нужно изменить конструкцию укрытия так, чтобы оборудование находилось в камере/туннеле. Если отверстия для доступа нельзя закрывать, их можно изолировать с помощью полос прозрачного пластика.
- Если нельзя сделать кожух, закрывающий оборудование полностью или частично, нужно использовать улавливающий вытяжной зонт, и он должен размещаться как можно ближе к источнику пыли. Учтите, что расстояние до источника пыли влияет на расход воздуха во второй степени.
- Скорость захвата, создаваемая местным вентиляционным отсосом, должна быть способна преодолевать любое движение окружающего воздуха между источником пыли и всасывающим отверстием.
- Если расстояние между источником пыли и всасывающим отверстием слишком велико, или если окружающий воздух движется слишком быстро, нужно рассмотреть возможность использования сдувающее-всасывающей схемы вентиляции.
- Важно, чтобы свежий воздух, поступающий в укрытие после того, как туда войдёт рабочий, был не загрязнён пылью. Если будет всасываться воздух из загрязнённой области, то рабочий может дышать респирабельной пылью. При всасывании запылённого воздуха он никогда не должен проходить через зону дыхания рабочего.
- Используйте фланцы на всасывающем отверстии, так как они значительно увеличивают количество воздуха, всасываемого спереди – со стороны источника пыли. Оптимально использование всасывающих отверстий со скруглёнными краями.
- Нужно проверить, чтобы все конструкции местных вентиляционных отсосов соответствовали критериям, установленным в руководстве ACGIH Industrial Ventilation: A Manual of Recommended Practice for Design[1- 1].
Воздуховоды и скорость воздуха[править]
Для перемещения запылённого воздуха от источника пыли к пылеуловителю могут использоваться три вида вентиляционных систем: с большой скоростью воздуха, с маленькой скоростью воздуха, и модифицированная с маленькой скоростью воздуха. В промышленности хорошо знакомы с высокоскоростной системой, где скорость воздуха составляет 15-23 м/с [3,000–4,500 fpm]. В сущности, это пыле-собирающая система, в то время как низкоскоростная вентиляционная система является пыле-улавливающей (скорость воздуха не более 9 м/с [1,800 fpm]. Если вентиляционная система низкоскоростная, то она не может переносить крупные, не-респирабельные частицы (обычно больше 10 мкм). Учтите, что маленькая скорость воздуха не означает маленький расход воздуха. Скорость захвата у местного вентиляционного отсоса и расход воздуха одинаковы для всех видов вентиляционных систем (присоединённых к местному отсосу) – высокоскоростной, низкоскоростной, и модифицированной низкоскоростной. На Рис. 1.9 показаны основные отличия между высокоскоростной и низкоскоростной системами.
Рисунок показывает, что в высокоскоростной системе пыль будет перемещаться в любом случае – при любом наклоне воздуховода. А при использовании низкоскоростной системы воздуховоды должны быть наклонены или в сторону всасывающего отверстия, или в сторону места выгрузки пыли, так как некоторые крупные частицы, непреднамеренно втянутые в поток удаляемого воздуха, будут оседать в воздуховодах, и их нужно удалять из них.
Высокоскоростная вентиляционная система[править]
Основным свойством высокоскоростной системы является её способность переносить запылённый воздух, содержащий частицы крупнее 10 мкм, от всасывающего отверстия до пылеуловителя, не допуская при этом осаждения пыли в воздуховодах. Для предотвращения осаждения частиц требуется большая скорость воздуха.
Так как воздуховоды такой системы могут размещаться и вертикально, и горизонтально, то их несложно разместить. Это позволяет спроектировать эффективные вентиляционные системы, в которых обычно используется центральный горизонтальный воздуховод и воздуховоды меньшего диаметра, соединяющие центральный воздуховод с местными вентиляционными отсосами и источниками пыли.
Главный недостаток высокоскоростной системы – то, что частицы пыли, двигаясь с большой скоростью, истирают стенки воздуховода, особенно в местах изменения направления движения воздуха. Больше всего изнашиваются повороты и места присоединения ответвлений. Если при проектировании или техобслуживании не принять специальных мер, то произойдёт разрушение воздуховодов, в них образуются отверстия. Поэтому большую часть труб и поворотов нужно делать из более прочных материалов, и повороты делать с большим радиусом. Такой износ увеличивает трудозатраты и расход материалов на техобслуживание. У любой вентиляционной системы с отверстиями в воздуховодах снижается эффективность в месте всасывания загрязнённого воздуха, и даже одно-единственное отверстие может сильно повлиять на работу системы. Так как работа высокоскоростной вентиляционной системы зависит от её техобслуживания, то она не всегда может работать с приемлемой эффективностью.
Если воздуховоды расположены горизонтально, а воздух влажный, и расход воздуха не адекватный, то при эксплуатации возникают дополнительные проблемы. При выключении вентилятора пыль оседает на горизонтальных участках воздуховодов. Если температура воздуха опускается ниже точки росы, на поверхности воздуховодов может образовываться конденсат, что приводит к закреплению пыли на стенках, и трубы постепенно “заростают”. Со временем это приводит к уменьшению расхода воздуха через систему из-за увеличения сопротивления движению воздуха, и увеличения скорости воздуха в более узких местах. Уменьшение расхода воздуха уменьшает эффективность улавливания пыли, а увеличение скорости воздуха увеличивает скорость истирания стенок и может привести к изнашиванию системы скорее, чем можно ожидать.
Наконец, для получения большой скорости воздуха нужно, чтобы в системе был большой перепад давления. Это требует большего расхода энергии, что увеличивает эксплуатационные расходы. Также, хотя начальные расходы на изготовление и установку воздуховодов высокоскоростной системы невелики, повышенные расходы на техобслуживание и эксплуатацию приводят к большим затратам за период эксплуатации системы.
Низкоскоростная вентиляционная система[править]
Низкоскоростная вентиляционная система создаёт такое же разрежение в месте всасывания запылённого воздуха, и обеспечивает такой же расход удаляемого воздуха от источника пыли к пылеуловителю, что и высокоскоростная вентиляционная система. Отличие между ними в том, что после всасывания запылённого воздуха в низкоскоростной системе скорость перемещаемого воздуха значительно меньше. Поэтому трубы такой системы всегда делают наклонными для того, чтобы слишком большие частицы (осевшие в них) могли соскользнуть в места выгрузки для облегчения их удаления. При проектировании скорость воздуха выбирается такой, чтобы обеспечивать перенос только респирабельной пыли (обычно меньше 10 мкм). Такая мелкодисперсная пыль переносится медленно движущимся потоком воздуха, а более тяжёлые частицы оседают в воздуховодах и соскальзывают в места выгрузки.
Поэтому у низкоскоростной системы нельзя делать воздуховоды с горизонтальными участками. Воздуховоды (могут проектироваться так, чтобы) осевшая пыль использовалась повторно. Вместо длинных горизонтальных воздуховодов могут использоваться пилообразные (sawtooth design), Рис. 1.10. Для регулирования расхода воздуха используют диафрагмы – пластины с отверстиями, сужающими поток и создающими дополнительное сопротивление. Их лучше устанавливать на нисходящем участке так, чтобы не улавливался материал (пыль) за высокоскоростным потоком воздуха в отверстии.
Способность низкоскоростной системы переносить пыль ограничивается частицами, меньшими 10 мкм. Из-за отсутствия более крупных частиц, и из-за меньшей скорости воздуха, абразивный износ воздуховодов в такой системе меньше даже в тех местах, где воздух изменяет направление движения. Это позволяет использовать повороты небольшого радиуса или угловые соединения – без интенсивного износа.
При проектировании вентиляционной системы размер воздуховодов подбирается с учётом ожидаемой потери давления в системе. Потери возникают из-за трения и потерь давления в пылеуловителях. При уменьшении скорости воздуха потери давления из-за трения в воздуховодах и соединениях уменьшаются, что снижает эксплуатационные расходы энергии.
Из-за того, что воздух движется с небольшой скоростью, можно (умеренно) изменять размеры регулирующего расход отверстия, и при этом не нарушать работу системы полностью. Даже если в какой-то ветке системы сделать отверстие, открыв её, это не приведёт к сильному изменению расходов воздуха в других ветвях, так как изменение давления будет минимальным. Если одна из ветвей системы выйдет из строя, или в ней резко изменится воздушный поток, низкоскоростная вентиляционная система стремится сбалансировать режим работы других ветвей, и они стремятся сохранить эффективность. Поэтому при сохранении эффективного улавливания пыли расход воздуха, удаляемого от двух одинаковых источников пыли, может значительно отличаться. Это уменьшает общие потери вентиляционной системы.
Недостатками низкоскоростных вентиляционных систем являются большие капитальные расходы, и более сложная конструкция. В таких системах способность пропускать требуемое количество воздуха (м3/час) через воздуховоды с заданной скоростью определяет диаметр труб, который значительно больше, чем у воздуховодов высокоскоростной системы. Кроме того, из-за невозможности размещать воздуховоды горизонтально, используют “пилообразную” конструкцию, которая стоит дороже и монтаж которой сложнее.
При проектировании низкоскоростной вентиляционной системы распространённым заблуждением является то, что думают, что из-за маленькой скорости воздуха в воздуховодах не требуется использовать укрытие. Но на самом деле хорошо спроектированное укрытие/вытяжной зонт нужны и для низкоскоростной системы – это помогает снизить потери давления в системе за счёт снижения сопротивления на входе в систему. В сущности, укрытия у низко- и высокоскоростных систем одинаковы. Но все всасывающие отверстия вентиляционных систем должны размещаться на удалении от места падения материала для снижения вероятности его всасывания. Принцип низкоскоростного осаждения пыли (в укрытии) состоит в отсасывании воздуха из хорошо закрытого источника пыли. Это приводит к возникновению разрежения, удерживающего разлетающуюся пыль в укрытии. Форма всасывающего отверстия тоже имеет значение по двум причинам:
- У хорошо спроектированного входного отверстия меньше сопротивление движению воздуха.
- Хорошо спроектированное входное отверстие предотвращает всасывание материала в вентиляционную систему. Даже при использовании низкоскоростной вентиляционной системы в воздуховоды могут попасть крупные частицы. Поэтому важно, чтобы в поперечном сечении входного отверстия скорость воздуха была не выше 1-1.5 м/с [200÷300 fpm] для предотвращения всасывания крупных частиц пригодного к продаже материала.
Наконец, проектирование и размещение низкоскоростной системы требуют больше трудозатрат. Из-за ограничения, не позволяющего размещать участки воздуховодов горизонтально, иногда трудно найти физическое пространство для требуемой пилообразной конструкции воздуховодов. Но хорошо спроектированная низкоскоростная вентиляционная система требует незначительного техобслуживания и не засоряется. Ниже описаны подробности проектирования таких низкоскоростных систем.
Перемещение воздуха со скоростью до 9 м/с
Из-за особенностей низкоскоростной вентиляционной системы при её использовании нет необходимости обеспечивать определённую (конкретную) скорость воздуха в воздуховодах. Но если скорость будет равна желаемой (9.1 м/с [1800 fpm]), то воздух будет переносить большую часть респирабельной пыли (размер частиц до 10 мкм) к пылеуловителю, когда пыль попадает в воздуховоды из оборудования и находится в кожухах, закрывающих источники пыли. Основной целью использования низкоскоростной обеспыливающей вентиляционной системы является сведение к минимуму количества воздушных загрязнений (респирабельной пыли), которое выходит из системы, создавая опасность для здоровья и раздражение. При скорости воздуха 9 м/с в обеспыливаемом оборудовании (или под кожухом) создаётся небольшое разрежение, и обеспечивается отсасывание достаточного количества воздуха для того, чтобы помешать частицам пыли выходить наружу. Такая скорость воздуха и полученное разрежение создают потоки (чистого) воздуха в зазорах, входящие внутрь, а не выходящие наружу (потоки загрязнённого воздуха) в большинстве случаев.
Использование воздуховодов без горизонтальных участков
При использовании маленькой скорости движения воздуха в воздуховодах важно обеспечить отсутствие горизонтальных участков воздуховодов. Причина в том, что крупные частицы, движущиеся в потоке воздуха, могут оседать и прикрепляться к стенкам воздуховода. Это приводит к сужению воздуховодов, увеличению скорости воздуха и ускорению абразивного истирания стенок. Поэтому воздуховоды должны проектироваться так, чтобы наклон участков, где воздух движется вверх, был не менее 45°, а наклон участков, где воздух спускается – не менее 30° (Рис. 1.11). Это позволяет любой частице, попавшей в поток воздуха, соскользнуть к источнику пыли. Это также требует, чтобы во всех нижних точках воздуховодов были приспособления для выпуска накапливающейся пыли – как показано на Рис. 1.10.
Использование коллекторов
При проектировании низкоскоростной системы нужно рассмотреть возможность использования одного или более коллекторов, соединяющих пылеуловитель и выбранные места, находящиеся “в центре” источников пыли. Использование таких коллекторов позволит соединить их с источниками пыли с помощью маленьких ответвлений, и позволит легко присоединить вытяжку у отдельных частей оборудования к обеспыливающей вентиляционной системе. Коллекторы могут быть круглого или прямоугольного поперечного сечения. При недостатке места, использование прямоугольных воздуховодов с большим отличием длины и ширины облегчает размещение коллектора. Эти воздуховоды могут включать много вертикальных участков, находящихся около имеющихся вертикальных стоек, элеваторов и т.п. – вдоль них. Как упоминалось ранее, во всех нижних точках коллектора должны быть приспособления для выпуска пыли, возможно – в ковшовый элеватор.
Уменьшение работы по подгонке на месте установки и сварки
При изготовлении новых вентиляционных систем нужно использовать трубы и другие детали, изготовленные на соответствующих специализированных предприятиях – максимально полно – и при сборке системы на месте использовать готовые части. Сварка или обрезка труб в производственных условиях, на месте сборки, стоят дорого, и при хорошем проектировании системы потребность в сварочных работах можно свести к минимуму. Дополнительные затраты времени на этапе проектирования на проработку конструкции укрытий, вытяжек, воздуховодов и других элементов приносят отдачу при последующей сборке и монтаже системы.
Часто во время монтажа требуется подгонка по месту и т.п., и это нужно учесть до начала сборки. Обрезку и сварку для подгонки воздуховодов по месту при сборке) лучше (планировать так, чтобы они проводились) на концах (стандартных) воздуховодов. Тогда можно использовать воздуховоды заводского изготовления с преднамеренно завышенной длиной. Желательно также использовать воздуховоды с фланцами, установленными на концах труб уже на заводе-изготовителе, а не изготавливать и не устанавливать их на месте. Это предохранит воздуховоды от повреждений при обработке и перемещении, и затем на месте можно будет укоротить трубу до необходимого размера, переместить стык с другой трубой до нового конца воздуховода, при необходимости повернуть его, и прикрепить.
Эффективность и простота монтажа воздуховодов может быть достигнута с помощью использования фланцевых соединений. Фланцевые (и другие) соединения очень доступны, недороги и их удобно устанавливать. Такие соединения должны использоваться во всех укрытиях, частях воздуховодов и др. при заводском изготовлении частей вентиляционной системы. Их использование также позволяет избежать применения дорогостоящих сварочных работ и позволяет легко заменять участки воздуховодов при необходимости.
Избегайте изменения направления больше чем на 90°
Если воздух резко изменяет направление движения больше чем на 90°, то сопротивление резко возрастает и в высокоскоростной вентиляционной системе, и в низкоскоростной системе, Так как потери давления пропорциональны квадрату скорости воздуха, то (суммарная) потеря давления у низкоскоростной системы останется меньше. Но если требуется уменьшить потерю давления и у низкоскоростной системы, то нужно использовать несколько поворотов на небольшие углы.
Определение размеров и мест установки пластин с отверстиями, регулирующих расход воздуха.
Во многих сложных вентиляционных системах для регулирования расхода воздуха используются устанавливаемые в воздуховод пластины с отверстиями, изменяющими перепад давления, необходимый для нормальной работы нижележащего участка воздуховода. Рекомендуется в каждую из ветвей вентиляционной системы установить по одной пластине с отверстием так, чтобы это привело к увеличению перепада давления не менее чем на 500 Па (2 дюйма водяного столба). Это позволит легко увеличить систему в будущем. При добавлении дополнительных ответвлений к системе к коллектору, пластины с отверстиями можно будет заменить на другие – с более крупными отверстиями, создающими меньшее сопротивление и перепад давления.
На Рис. 1.12 показаны неудачные места размещения пластин с отверстиями. Пластины должны размещаться на расстоянии не менее 4-5 диаметров воздуховода до и или 4 диаметра после места изменения направления движения воздуха. Это позволить потоку воздуха стать более ламинарным, и восстановить нормальную скорость. Если пластина находится до поворота и близко к нему, то из-за увеличения скорости в отверстии и поворота усилится абразивный износ наружной стенки воздуховода в месте поворота. Всегда, когда это возможно, пластина должна устанавливаться на секции воздуховода, где воздух движется вниз. Это поможет избежать накопления тяжёлых частиц пыли выше пластины – что может произойти при установке пластины на участке, где воздух движется вверх (так как большая скорость воздуха в отверстии не позволит частицам спуститься вниз).
Также нельзя устанавливать пластины около входных отверстий воздуховодов. Из-за увеличения скорости воздуха в отверстии в воздуховод может попасть нежелательно много материала. Скорость захвата вытяжного зонта должна быть (если это возможно) меньше 2.5 м/с [500 fpm]. При удалении мелкодисперсной шлифовальной пыли желательно ограничить скорость 1 м/с.
Сведите к минимуму использование гибких воздуховодов
В низкоскоростных вентиляционных системах нежелательно использование (по крайней мере – систематичное) гибких воздуховодов. (Их) поломка может нарушить работу ответвлений вентиляционной системы в её остальной части. Гибкие воздуховоды увеличивают сопротивление вентиляционной системы. Если они используются, то их нужно устанавливать между всасывающим отверстием вентиляционной системы и пластиной с отверстием – это сведёт к минимуму последствия при их поломке.
Модифицированная низкоскоростная вентиляционная система[править]
Такие вентиляционные системы должны сочетать достоинства низко- и высокоскоростных систем, и не иметь их недостатков. Главным средством для достижения этой цели является улавливающее пыль укрытие (кожух, вытяжной зонт). Первый участок воздуховода после всасывающего отверстия должен быть вертикальным, а его длина должна быть не менее 1.8 м [6 футов], желательно – 2.4÷3 м [8÷10 футов]. А скорость воздуха в этом вертикальном участке должна быть очень низкой – даже по отношению к обычной низкоскоростной системе (то есть – 5.1÷6.1 м/с [1000÷1200 фут/мин]). Как и в других системах, пыль всасывается, но перемещается только самая мелкодисперсная фракция. (Вертикальный) участок 2.4÷3 м необходим для уменьшения завихрений и получения спокойного ламинарного потока, и для улучшения отделения тяжёлых крупнодисперсных частиц от лёгких в начале воздуховода.
Так как после этого вертикального участка воздуховода количество частиц в воздухе минимально, то поддерживать большую скорость в последующих горизонтальных участках воздуховода – не нужно. Также нет необходимости использовать “пилообразную” конструкцию воздуховодов и делать места для выгрузки уловленной пыли. Скорость воздуха в первом горизонтальном участке после описанного вертикального должна быть около 10 м/с [2000 fpm].
При проектировании модифицированной низкоскоростной системы с коллектором, к которому (будут) присоединяться дополнительные боковые ветви воздуховодов, скорость воздуха в коллекторе после места подсоединения первой боковой ветви нужно увеличить на ~0.51 м/с [100 fpm] (см. Рис. 1.13). Даже при большой длине и большом числе присоединённых боковых вентиляционных ветвей, скорость воздуха в коллекторе скорее всего не превысит 12.7÷15.2 м/с [2500÷3000 fpm]. Из-за маленькой потери давления в такой системе, в ней не требуется делать дорогие воздуховоды для изменения направления движения воздуха, резкие повороты или отводы. Вместо этого можно использовать “коробчатые” повороты (box elbows) и т.п.
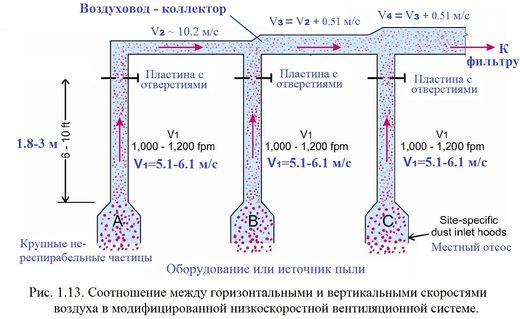
У такой модифицированной низкоскоростной системы имеются все достоинства низкоскоростной системы (слабый абразивный износ стенок, небольшие затраты на техобслуживание, низкое энергопотребление, и стабильность режима работы разных частей системы). В то же время нет необходимости использовать пилообразные воздуховоды, занимающие много места. Так как скорость воздуха в воздуховодах меньше, чем в высокоскоростной системе, и больше, чем в низкоскоростной, то диаметр (размер) воздуховодов также будет промежуточным. Другое достоинство этой системы в том, что её легко использовать при расширении или модификации имеющейся высокоскоростной системы. Нужно будет сравнить скорости в местах соединения, с учётом того, что неудобно переходить от большей скорости в воздуховоде к меньшей. Однако можно расширить систему, используя низкоскоростную модифицированную систему. Основные рекомендации по таким системам, которые были даны ранее, применимы и в этом случае, но с некоторыми исключениями.
- Рекомендация избегать горизонтальных участков воздуховодов не нужна.
- Пластины с отверстиями устанавливаются в верхней части первого низкоскоростного вертикального участка воздуховода, а не внизу. Их нужно устанавливать как можно ближе к этому участку.
- Скорость воздуха в вертикальных участках воздуховодов должна быть от 5.1 до 6.1 м/с [1000-1200 fpm].
- Скорость воздуха в горизонтальных участках должна быть не ниже 10.1 м/с [2000 fpm].
Рекомендации по проектированию разветвлённой вентиляционной системы[править]
Для предотвращения попадания пыли в воздух рабочей зоны часто приходится отсасывать загрязнённый воздух от более чем одного устройства, но при этом нередко используется один пылеуловитель и один вентилятор. Это приводит к созданию разветвлённой вентиляционной системы, Рис. 1.13 и 1.25. Так как расстояния от устройств до пылеуловителя редко бывают одинаковы, то сопротивление разных участков воздуховодов различно (см. схему).
Рекомендуется следующий порядок расчёта:
Сначала прорисовывается схема расположения воздуховодов и размещения пылеуловителя и вентилятора. Н рисунке рассмотрен простейший случай с двумя источниками пыли.
Затем выбирается наиболее удалённый источник пыли, и для известного значения расхода воздуха Q1 и допустимой скорости движения воздуха в воздуховодах участка 1 определяется площадь поперечного сечения воздуховода (участок 1). Так как маловероятно, что именно такие воздуховоды изготавливаются промышленностью, нужно определить ближайшие подходящие размеры и выбрать тот, который приемлем с точки зрения допустимой скорости воздуха. Под этот размер воздуховода проводится расчёт новой скорости воздуха. Вычисляется сопротивление всех составных частей участка 1, и определяется статическое давление в узле 1, необходимое для получения требуемого расхода воздуха Q1. Для известного расхода воздуха Q2 и допустимой скорости воздуха в воздуховоде на участке 2 определяется площадь поперечного сечения участка 2. Затем выбирается реально изготавливаемый размер воздуховода, и проводится расчёт сопротивления, скорости воздуха и статического давления в узле 1, необходимого для получения требуемого расхода воздуха Q2 на участке 2.
Маловероятно, что значения статического давления, вычисленные для двух участков, окажутся одинаковы. Простое присоединение воздуховодов приведёт к тому, что из-за меньшего сопротивления участка 2 расход воздуха в нём будет больше ожидаемого, а на участке 1 – меньше. Это может не только не обеспечить защиту от пыли около устройства 1, но и привести к засорению пылью участка 1, что полностью выведет его из строя. Для решения этой проблемы рекомендуется два способа:
- Если статические давления отличаются менее чем на 20%, то поскольку расход воздуха пропорционален квадратному корню из перепада давления, можно оставить всё без измерений. Кроме того, точность вычислений конечна, и сопротивление будет изменяться по мере загрязнения внутренней поверхности воздуховодов.
- Если статическое сопротивление участка 2 меньше, то его можно искусственно увеличить, установив на нём пластину с отверстием. Это повысит сопротивление, и статическое давление для обоих участков в узле 1 станет одинаковым.
- Можно вычислить (заниженный) размер воздуховода для участка 2, при котором расход воздуха от устройства 2 (при статическом давлении в узле 1, соответствующем нормальной работе участка 1) будет равен Q2. То есть, если использовать воздуховоды меньшего диаметра для участка 2, то скорость воздуха там будет выше (при статическом давлении в узле 1, соответствующем нормальной работе участка 1), и сопротивление участка 2 станет соответствовать участку 1.
У второго решения есть недостатки: (1) из-за большей скорости воздуха может происходить абразивный износ воздуховодов, что потребует проводить их ремонт и может ухудшить работу вентиляционной системы; (2) Из-за большей скорости воздуха может происходить всасывание крупных частиц пыли, что увеличит нагрузку на пылеуловитель и риск абразивного износа воздуховодов; (3) при необходимости модифицировать вентиляционную систему (при использовании другого оборудования, установке нового оборудования и т.п.) это будет сложно сделать; (4) реальное сопротивление воздуховодов отличается от вычисленного, и при эксплуатации оно может возрастать из-за осаждении какой-то части пыли на стенках, что увеличивает их шероховатость, а отсутствие регулятора расхода воздуха (пластины с отверстиями) затруднит наладку и коррекцию работы системы.
Рекомендуется использовать пластины с отверстиями.
Для участка 3 расход воздуха равен сумме расходов Q3 = Q1 + Q2. Для приемлемой скорости воздуха проводится расчёт поперечного сечения воздуховода, определяется реально изготавливаемый подходящий диаметр, и для этого размера проводится расчёт скорости воздуха. Определяется сопротивление всех составных частей участка 3, и статичесоке давление в месте присоединения к пылеуловителю. Если есть другие источники пыли, то в узлах присоединения их воздуховодов к уже рассчитанной части вентиляционной системы (более удалённой от пылеуловителя) повторяются действия, описанные для выравнивания статического давления в узле 1.
При выборе вентилятора, соответствующего значениям суммарного расхода воздуха и статического давления, может не оказаться подходящего. Можно выбрать ближайший более производительный, создающий большее статическое давление, и уменьшить расход воздуха и давление с помощью, например, входного направляющего аппарата, закручивающего поток воздуха в сторону вращения рабочего колеса. Это уменьшает производительность без значительного снижения КПД, а регулирование угла установки лопаток направляющего аппарата позволяет регулировать производительность и статическое давление вентилятора.
См также: Внутренние санитарно-технические устройства. Часть 3. Вентиляция и кондиционирование воздуха. Книга 1 (и книга 2 тоже). Справочник проектировщика. Москва, Стойиздат, 1992г. Под ред. Н.Н. Павлова и Ю.И. Шиллера, и др.
Пылеуловители[править]
Для очистки воздуха от загрязняющих его аэрозолей при добыче и переработке минеральных полезных ископаемых используют пылеуловители. Выбор пылеуловителя для любого конкретного случая зависит от:
- Концентрации пыли и её свойств,
- Размеров частиц,
- Требуемой степени очистки,
- Температуры и относительной влажности воздуха, и
- Способа улавливания.
К отличиям в свойствах пыли, влияющим на её улавливание, относят: абразивные свойства, взрывоопасность, липкость, “лёгкость” или “пушистость”. Форма частиц (сферическая регулярная или нерегулярная) тоже имеет значение, так как это влияет на улавливание частиц фильтровальным материалом. С точки зрения эффективного улавливания нерегулярные частицы идеальны, так как они позволяют легко образовывать пористый рыхлый воздухопроницаемый слой уловленной пыли на поверхности фильтровального материала – а этот слой увеличивает эффективность очистки и регенерации без большого роста сопротивления. Но такие частицы могут прочно застревать в самом фильтровальном материале.
Существуют различные пылеуловители – начиная от простейших гравитационных и заканчивая сложнейшими электростатическими; ниже приводится их список:
- Гравитационные пылеуловители (коробки-пылеосадители).
- Центробежные пылеуловители или циклоны.
- Промышленные тканевые рукавные фильтры.
- Промышленные фильтры с картриджами.
- Мокрые пылеуловители.
- Промышленные электрофильтры.
Ниже приводится их краткое описание с указанием достоинств и недостатков.
Гравитационные пылеуловители[править]
Гравитационные пылеуловители – это большие камеры, где скорость воздуха сильно уменьшается для того, чтобы позволить частицам пыли осесть под действием силы тяжести. Для этого поток воздуха изменяет направление движения. Воздух входит в пылеуловитель горизонтально, и сразу отклоняется прямо вниз пластиной (Рис. 1.14). При снижении скорости воздуха и его отклонении вниз сила тяжести осаждает крупные, тяжёлые частицы, а мелкие (лёгкие) частицы продолжают двигаться вместе с воздухом и не улавливаются.
Достоинствам гравитационных пылеуловителей является то, что они требуют незначительного техобслуживания, и уменьшают нагрузку на главный пылеуловитель. Но они занимают много места, и у них низкая эффективность очистки.
Центробежные пылеуловители или циклоны[править]
Для улавливания пыли в циклонах используется центробежная сила. Для этого в них входящий поток воздуха закручивается по спирали. При этом принудительном изменении направления движения частицы пыли из-за инерции стремятся сохранить первоначальное направление движения, что приводит к их отделению от потока воздуха (Рис. 1.15). Хотя по конструкции и работе это простые устройства, в них происходят сложные процессы. Для их упрощённого объяснения можно сказать, что внутри циклона образуется два вихря. Главный спускается вниз, и он несёт тяжёлые частицы (к бункеру-пылесмборнику). А в нижней части циклона возникает внутренний вихрь, который поднимается вверх и уносит из циклона лёгкие частицы.
Циклоны требуют мало обслуживания, и по соотношению стоимость/эффективность являются хорошими пылеуловителями. Они тоже могут использоваться для снижения запылённости воздуха, поступающего на главный пылеуловитель, и позволяют повторно использовать сухой уловленный продукт. Однако предсказать их параметры трудно, при их проектировании возникает ряд проблем, и они занимают много места.
Циклоны плохо улавливают лёгкую мелкодисперсную пыль. Обычно их используют для предварительной очистки для удаления крупных частиц, которые могут повредить фильтровальный материал или засорить мокрые пылеуловители. Нужно отметить, что установка циклона перед рукавным фильтром может не снизить общее сопротивление системы (из-за снижения засорения фильтра пылью), так как снижение сопротивления тканевого фильтра может полностью компенсироваться увеличением сопротивления из-за самого циклона. Падение давления у циклона может изменяться от 750 Па у низкоэффективных циклонов до 2 кПа у высокоэффективных [3-8 inches wg].
Рукавные фильтры[править]
Для улавливания пыли в рукавных промышленных фильтрах воздух пропускается через фильтровальный материал. Для очистки воздуха его скорость первоначально снижается, что приводит к осаждению крупных частиц; а затем оставшиеся частицы улавливаются при прохождении воздуха через фильтровальный материал (Рис. 1.16). Отделение частиц от воздуха происходит при их столкновении с волокнами фильтровального материала и ранее осевшими частицами, и образованию на поверхности фильтра рыхлого воздухопроницаемого слоя из уловленных частиц. Так как большая часть пыли улавливается вне ткани (на её поверхности), то когда происходит очистка фильтра, уловленная пыль падает в пылеулавливающий бункер (находящийся под рукавами из фильтровальной ткани) под действием силы тяжести. Затем уловленная пыль удаляется из бункера через устройство для выгрузки пыли.
Промышленные рукавные фильтры обычно проектируются и подбираются так, чтобы при их нормальной работе потеря давления составляла 750 Па ÷ 1.2 кПа [4÷6 inches wg]. Такие пылеуловители могут обеспечить эффективность очистки до 99.97% (у высокоэффективных противоаэрозольных фильтров НЕРА) для мелкодисперсных частиц. Фильтровальная ткань может изготавливаться из шерсти, синтетических материалов, стекловолокна и др. В большинстве случаев при работе при температуре окружающей среды, самым экономичным является использование фильтров из шерсти. Но при повышенной температуре и при химически активных (агрессивных) загрязнениях нужно использовать фильтр из другого материала. Так как рукава из фильтровального материала должны периодически заменяться, то нужно приобретать такой фильтр, который допускает их (удобную) замену. Предпочтительно использование таких пылеуловителей, которые позволяют заменять фильтры извне.
При проектировании рукавного фильтра также можно учесть экономические факторы. Для данного конкретного случая воздушных загрязнений такие факторы, как общее падение давления, цикл очистки и площадь фильтровального материала. В статье "Baghouse System Design Based on Economic Optimization"[1- 8] приводится полезная модель, которая может быть наиболее подходящей на этапе предварительного проектирования.
Плотность улавливаемого материала требует особого внимания проектировщиков. Если при низкой плотности материала он будет двигаться с воздухом вверх, и если эта скорость движения материала вверх будет достаточно большой, то это может помешать нормальной регенерации фильтровальной ткани и соответственно – эксплуатации пылеуловителя. Улавливание материала с низкой плотностью (менее 480 кг/м3) [<30 pounds per cubic feet] может потребовать изменения конструкции пылеуловителя. В таких случаях нужно изменить конструкцию фильтра для того, чтобы учесть меньшую скорость гравитационного оседания материала (путём уменьшения скорости движения воздуха вверх внутри фильтра). Обычно такое изменение может выражаться в виде увеличения расстояния между фильтровальными рукавами, уменьшения длины рукавов, или расположения входного отверстия для запылённого воздуха выше.
Наконец, размеры частиц имеют большое значение для определения отношения скорости фильтрации воздуха (расход воздуха через единицу площади фильтра) и для выбора фильтровального материала. Обычно понимают, что чем мельче пыл, и чем больше концентрация пыли, тем меньше должна быть скорость движения воздуха через фильтровальный материал. Правильный выбор рукава из фильтровального материала или картриджа, учитывающий свойства улавливаемого материала, важен для обеспечения успешной работы пылеулавливающей системы. Статья "Fine Filtration Fabric Options Designed for Better Dust Control and to Meet PM2.5 Standards"[1- 9] даёт полезную информацию и о фильтровальных материалах, и о их способностях улавливать пыль при разных условиях эксплуатации. Также рекомендуется статья "Pick the Right Baghouse Material"[1- 10], в которой приводится схема, детально описывающая свойства текстильных материалов с точки зрения фильтрации.
Поступление пыли с входящим воздухом относится к количеству пыли, поступающему во входное отверстие пылеуловителя за единицу времени. Обычно оно выражается в кг/час [pounds per minute, lbs/min, или pounds per hour, lbs/hour], и пересчитывается в граны. Запылённость выражается в граммах на м3 [grains/cubic foot, gr/cf]. Запылённость воздуха зависит от множества факторов, включая количество источников пыли, подключенных к пылеулавливающей системе, типу источников пыли (дробилки, вибросита и т.п.), поступлению пыли от этих источников, и эффективности захвата этой пыли в каждом источнике. Количество пыли, поступающее от каждого из источников, зависит от ряда параметров, включая распределение частиц пыли обрабатываемого материала по размерам, содержанию влаги и производительности оборудования.
Агентство по охране окружающей среды (США) Environmental Protection Agency EPA собрало информацию о факторах, влияющих на пылеобразование для разных технологических процессов, включая переработку минеральных полезных ископаемых[1- 11]. В таблице 1.2 приводятся некоторые из этих факторов, которые получены путём усреднения известных результатов, и которые можно считать начальной точкой при попытке определить поступление пыли в пылеуловитель. Эти значения нужно умножить на производительность конкретного используемого оборудования для получения количества поступающей пыли кг/час [lbs/min]. Чтобы эффективно количественно определить поступление пыли в пылеуловитель также следует использовать основанные на практическом опыте рекомендации изготовителей газоочистного оборудования и фильтровальных материалов. Информация о поступлении пыли поможет определить (подходящую) скорость фильтрации воздуха, выбрать подходящий фильтровальный материал, тип пылеуловителя, вид входного отверстия и метод регенерации фильтровального материала.
Источник | Общая масса пыли, частицы которой меньше 10 мкм (РМ-10)†† |
---|---|
Третичное (tertiary) дробление | 0.0010886 [0.0024] |
Просев | 0.0039463 [0.0087] |
Место перегрузки конвейера | 0.0004989 [0.0011] |
Мокрое бурение - нефрагментированный камень | 0.0000363 [0.00008] |
Выгрузка самосвала – фрагментированный камень | 0.0000073 [0.000016] |
Загрузка самосвала – конвейером, раздробленный камень | 0.00004536 [0.0001] |
- † - неконтролируемый выброс пыли при переработке материала, кг/тонна [lb/ton].
- †† - частицы РМ-10 – это те, у которых диаметр меньше 10 мкм.
Для преобразования фунтов в граны можно использовать следующую формулу:
- 1 фунт в минуту / 1 куб фут в минуту = (0.45 кг/мин) / (0.0283 м3/мин) = 15.9 кг/м3 (Уравнение 1.7) (СИ)
- 7000 гран [lbs/min] / (cfm) = гран/куб.фут
- 1 г/фт3 = 2.288 *10-6 кг/0.0283 м3 = 7000 (0.45 кг/мин).
- где lb/min = производительность оборудования, перерабатывающего материал (кг/м3), а cfm = расход воздуха в пылеулавливающей системе (1 cfm = 0.0283 м3/мин).
Ниже приводятся сведения для качественной оценки концентрации пыли в очищаемом воздухе:
- Низкая концентрация = < 2.288 грамм/м3;
- Типичная концентрация = 2.3–11.5 грамм/м3;
- Большая концентрация = 11.5–22.9 грамм/м3;
- Очень большая концентрация = >23 г/м3.
Отношение расхода воздуха к площади ткани (air to cloth ratio) – показатель отношения расхода воздуха за минуту к единице площади фильтровального материала пылеуловителя (м3/мин воздуха / м2 фильтра) (ft3 air per minute/ft2 of bag area), и математически это выражение можно выразить так:
- air to cloth ratio = Q/A (ft3 air per minute/ft2 of bag area), или
- air to cloth ratio = Q/A(м3/мин воздуха / м2 фильтра), где 0.3 *Q/A [м] = Q/A [ft]
- где Q = расход газа (воздуха) м3/мин [cfm] и A = площадь фильтровального материала всех рукавов в м2 [ft2].
Пористость фильтровального материала (ткани) будет определять то, сколько воздуха сможет пройти через неё до того, как статическое давление станет слишком большим для корпуса пылеуловителя или для установленного вентилятора. Оценив запылённость очищаемого воздуха, можно также определить – какая масса пыли осядет на каждом квадратном метре фильтровального материала за единицу времени.
Отношение расхода воздуха к площади фильтра – это также показатель средней скорости движения воздуха через фильтр. Запылённость очищаемого воздуха прямо влияет на отношение расхода к площади. Чем выше концентрация пыли, тем медленнее должен двигаться воздух через фильтр, и отношение расход/площадь меньше. При большей концентрации пыли количество пыли, осевшей на фильтровальном материале – больше, и перепад давления больше. Отношение расход /площадь менее 1.22 м3/мин / м2 (4:1 ft3/min / ft2) считается маленьким; от 1.22 до 2.13 м3/мин – средним (4:1 ÷ 7:1), а более 2.13 м3/мин / м2 (7:1) – большим. При уменьшении отношения расход/площадь у фильтра становится больше площадь материала для осаждения пыли, что позволяет уменьшить перепад давления при той же остаточной загрязнённости фильтровального материала (после регенерации).
Для уменьшения отношения расход/площадь есть два основных способа: уменьшить расход воздуха или увеличить площадь фильтровального материала. Но с точки зрения проектирования всей вентиляционной системы изменение расхода воздуха нежелательно. Поэтому чаще увеличивают площадь фильтра.
Помимо отношения расхода воздуха к площади фильтра, на метод очистки (регенерации) рукавов из фильтровального материала может влиять запылённость очищаемого воздуха. Так как на практике фильтровальные материалы работают лучше при стабильной остаточной загрязнённости фильтра (для получения оптимальной степени очистки), то для поддержания такой степени загрязнённости можно регулировать длительность периода очистки и длительность периода меду очистками. Для получения такого режима очистки используют измерение перепада давления на пылеуловителе – это называется “очистка по потребности”. Очистка рукавов фильтровального материала начинается тогда, когда перепад давления достигает заранее заданной величины (большой), и прекращается тогда, когда перепад давления становится равным заранее заданной маленькой величины. Использование такого метода гарантирует, что на фильтровальном материале рукавов есть достаточно много неочищенной пыли. Лучший способ определить оптимальный режим очистки для всей системы – это использовать накопленный опыт и рекомендации изготовителей.
Для сброса пыли, осевшей на фильтровальном материале рукавного фильтра, есть три разных способа. Они используются в фильтрах с механическим отряхиванием; обратной продувкой и обратной импульсной продувкой.
Рукавные фильтры с механическим отряхиванием пыли
В этих фильтрах для удаления пыли используется механическое устройство, которое стучит по каркасу рукава. Для такой очистки нужно временно перестать пропускать запылённый воздух через рукав. Такие пылеуловители не требуют значительных затрат на техобслуживание, и у них низкие эксплуатационные расходы, но они занимают очень много места, конструкцию трудно изменить с учётом конкретных местных потребностей и у них маленькое отношение расхода воздуха к площади фильтра - 0.61 м3/мин / м2 (2:1 фут3/мин / фут2).
У рукавных фильтров с механическим отряхиванием рукав фильтровального материала закреплён внизу и подвешен вверху к отряхивающему устройству. Запылённый воздух входит в фильтр и оседает на внешней стороне трубообразного рукава. Для обеспечения непрерывной очистки воздуха такие пылеуловители делят на секции, и когда в одной из них происходит очистка фильтровального материала, воздух движется через пылеуловитель через другие секции (Рис. 1.17). Для изготовления рукавов нужно использовать такой материал, который может противостоять встряхиванию, например – хлопок.
Некоторые рукавные фильтры с механическим отряхиванием переоборудуют в фильтры с импульсной продувкой. Но это требует больших расходов, и при надлежащем уходе за фильтром не обязательно.
При использовании механических отряхивателей нужно выполнять ряд рекомендаций:
- В каждой из секций фильтра нужно установить манометры Magnehelic для определения перепадов давления в течение периодов очистки.
- Этот перепад давления должен быть, насколько достижимо, близок к нулю – чтобы обеспечить отделение слоя уловленной пыли от фильтровального материала и его свободное падение в бункер для пыли. Если перепад давления во время очистки будет больше ~62 Па (1/4 дюйма вод. столба), это резко ухудшит очистку фильтровального материала, что уменьшит расход воздуха, повысит перепад давления и сократит срок службы фильтровального рукава.
- Отряхивание рукавов должно проводиться при возрастании перепада давления на регенерируемой секции свыше 125 Па (1/2 дюйма вод. столба).
- Нужно экспериментально подобрать наилучший интервал между отряхиваниями рукавов так, чтобы не делать это слишком часто. Это также снизит износ и рукавов, и механического отряхивателя.
Рукавные фильтры с обратной продувкой
В фильтрах с обратной продувкой используется подвижное приспособление, которое подаёт воздух под невысоким давлением 20.7÷48.3 кПа (3÷7 psig) в фильтровальный рукав для его регенерации. К подаваемому воздуху не предъявляются те требования, которые предъявляются к сжатому воздуху из-за замерзания конденсата в воздуховодах. Недостаток – такие фильтры занимают больше места, и техобслуживание механизмов затруднено. Также они хуже работают в условиях, стимулирующих коррозию.
В таких фильтрах используются рукава, пристёгнутые к “ячеистой” пластине внизу, и подвешенные в верху пылеуловителя. Для обеспечения непрерывной работы пылеуловитель должен состоять из отдельных секций. Запылённый воздух входит в фильтр, и она оседает на наружной стороне рукавов. Перед началом регенерации процесс очистки в секции фильтра прекращается. Рукава очищаются путём продувки воздуха под низким давлением в обратном направлении (по отношению к направлению движения при очистке). Это заставляет рукава немного “съёжиться”, и сбросить накопленный на поверхности слой пыли. Для предотвращения полного сжатия на фильтровальном рукаве закрепляют кольца через разные интервалы, так что пыль может быть сброшена и падает в бункер (Рис. 1.18).
Первоначально фильтры с обратной продувкой использовали для фильтровального материала (стеклоткань), используемого для очистки газа при высокой температуре. Но с появлением новых синтетических фильтровальных материалов, более стойких при повышенной температуре и физическом воздействии, интерес к таким фильтрам снизился. У таких пылеуловителей отношение расхода воздуха к площади фильтра маленькое из-за низкой эффективности очистки фильтровального материала при (низкоскоростной) обратной продувке.
Рукавные фильтры с импульсной обратной продувкой.
Такие пылеуловители используют рукава из фильтровального материала, одеваемые на металлический каркас, предотвращающий сжатие рукава из-за разрежения (Рис. 1.19). Этот каркас закрепляется в отверстиях в пластине, разделяющей полости с загрязнённым и с очищенным воздухом. Запылённый воздух входит в пылеуловитель, и проходит через фильтровальный материал снаружи вовнутрь рукава. Слой уловленной пыли образуется на внешней стороне рукава, а для его удаления используется короткая импульсная подача сжатого воздуха в отверстие рукава, через которое обычно выходит очищенный воздух. Удар сжатого воздуха изгибает и надувает рукав, сбрасывая слой уловленной пыли. Используемый сжатый воздух должен быть чистым и сухим, иначе произойдёт увлажнение фильтровального материала, что уменьшит эффективность очистки. Такие пылеуловители могут быть не разделены на секции, а очистка части рукавов может проводиться без прекращения очистки воздуха фильтром – прямо во время работы.
Рукавные фильтры с импульсной продувкой используют импульсную подачу сжатого воздуха при давлении 4÷6 атм (60÷90 psig) для регенерации фильтровального материала. Это наиболее распространённый тип рукавного фильтра с импульсной продувкой, который используется с конца 1950-х. Очистка фильтровального материала рукавов позволяет пылеулавливающей системе работать при достаточно стабильном перепаде давления и требуемом расходе воздуха. Преимуществом таких фильтров является большая степень возврата уловленного продукта и высокая эффективность очистки воздуха. Другое достоинство – возможность делать вход загрязнённого воздуха в разных местах корпуса. Недостаток – работоспособность фильтра зависит от температуры и влажности воздуха.
Из-за более частого проведения циклов очистки, такие фильтры обеспечивают большую степень очистки фильтровального материала, чем тканевые пылеуловители, обсуждавшиеся ранее. Поэтому у фильтров с импульсной продувкой отношение расхода воздуха к площади фильтра может быть больше, например – 1.83 м3/м2 мин (6:1 ft3/ft2 мин) и выше. Но при улавливании пыли абразивных материалов следует использовать отношение 1.22 м3/м2 мин (4:1 ft3/ft2 мин). При большом отношении расхода воздуха к площади фильтра может происходить (более) сильный удар воздуха о фильтр, что может привести к переносу пыли на соседние рукава при очистке, и сократить срок службы фильтра до износа.
Рукава обычно делают из нетканого войлочного фильтровального материала. В фильтрах с импульсной продувкой не используют тканые материалы, так как последние пропускают через себя много не уловленной пыли до того, как на их поверхности образуется достаточно толстый слой уловленной пыли. Так как при импульсной продувке происходит интенсивная очистка фильтровального материала, то при использовании тканых фильтровальных материалов происходил бы проскок большого количества пыли в течение какого-то интервала времени после регенерации.
По критерию “стоимость-эффективность” фильтры с импульсной продувкой более эффективны, чем их более старые аналоги – фильтры с механическим отряхиванием. Эти фильтры могут работать при большем отношении расхода воздуха к площади фильтра, не имеют никаких подвижных частей, требующих техобслуживания, и меньших начальных расходов при закупке и установке.
Картриджные фильтры
Для улавливания пыли загрязнённый воздух в картриджных фильтрах пропускается через специальные картриджи, в которых находится компактно размещённый фильтровальный материал со складками большой общей площади. Существуют два основных типа картриджных фильтров – с горизонтальным и с вертикальным размещением картриджей (Рис. 1.20).
Этот тип фильтров, использующий для улавливания пыли пропускание загрязнённого воздуха через фильтровальный материал, появился позднее других. В отличие от других таких фильтров, в которых фильтровальный материал (тканый или войлочный) используется в виде рукавов цилиндрической формы, в этом фильтре используются картриджи, в которых размещено много фильтровального материала за счёт складок. Для установки в картриджи фильтровального материала со складками могут использоваться разные фильтровальные материалы, включая полиэстер или синтетические материалы. Из-за складок площадь фильтровального материала у такого фильтра больше, чем у фильтров со складками. Но у таких фильтров больше скорость воздуха, подходящего к фильтровальному материалу, и из-за этого может произойти повторный внос уловленной ранее пыли в картридж (например – сброшенной при регенерации). Поэтому скорость фильтрации ограничивается отношением расхода воздуха к площади фильтровального материала 0.61 м3/м2 мин (2:1 ft3/ft2 мин).
Картриджные фильтры работают так же, как и рукавные фильтры с импульсной продувкой – пыль оседает на наружной стороне фильтровального материала. Очищающий (сжатый) воздух подаётся в центр элемента, сбрасывая излишек накопившейся пыли. Так как в картриджах больше фильтровального материала (за счёт складок) при одинаковом расходе воздуха картриджный фильтр получается меньше, и соответственно капитальные расходы на его покупку и установку меньше. Так как картриджи вставляются в корпус фильтра сбоку, то требования к высоте потолка помещения у таких фильтров менее жёсткие, чем у рукавных фильтров с импульсной продувкой. Фильтровальный материал может быстро заменяться, что ускоряет техобслуживание. Недостатком этих фильтров является ограничение по выбору подходящих фильтровальных материалов (по сравнению с рукавными фильтрами), что не позволяет использовать картриджные фильтры при экстремальных температуре и влажности. Из-за большой площади фильтровального материала, размещённого в картридже со складками, расходы на замену фильтра (на один картридж) выше, чем за замену одного фильтровального рукава.
Главным достоинством картриджных фильтров является их компактность и удобность замены картриджей, что уменьшает воздействие пыли на рабочих (при техобслуживании). Новые картриджи поступают упакованными в картонные коробки. При замене новый картридж вынимается из коробки, вынимает из фильтра использованный картридж, устанавливает в фильтр новый картридж, а использованный помещает в коробку. Для очистки картриджей в фильтре используется импульсная продувка сжатым воздухом. При улавливании абразивной пыли срок службы картриджа может составлять два года. Но при использовании такого фильтра покупатель становится вынужден закупать только те картриджи, которые производятся изготовителем (другие не подойдут), а такое отсутствие конкуренции приводит к повышению цен на картриджи, и увеличивает расходы.
Нужно сказать, что при наличии липкой и влажной пыли картриджные фильтры плохо работают, и их применение обычно ограничивается температурой 83° (180°F). Запылённость очищаемого воздуха обычно ниже, чем у рукавных фильтров, так как фильтровальный материал, размещённый со складками, обычно очищается хуже, чем рукава. Кроме того, горизонтальное размещение картриджей приводит к тому, что при регенерации верхних картриджей сброшенная с них пыль падает на нижние картриджи.
Мокрые пылеуловители[править]
Для улавливания пыли в мокрых пылеуловителях как улавливающая среда используется вода или другая жидкость. Существуют мокрые пылеуловители (скрубберы) разных конструкций, и в большинстве из них для улавливания пылинок используется создание мокрых мишеней, с которыми они сталкиваются. Этой влажной мишенью может быть слой воды или область, где пылинки сталкиваются с капельками воды (Рис. 1.21). Достоинствами мокрых пылеуловителей является способность работать при разной влажности, стойкость к коррозии при воздействии химических веществ, и небольшие затраты на техобслуживание. Но для мокрых пылеуловителей нужно много воды, которая удаляется вместе с уловленной пылью, что уменьшает эффективность и увеличивает затраты энергии. Для отделения уловленных частиц в промышленности часто используют пруды-отстойники, а воду из таких прудов можно использовать повторно.
Эффективность улавливания пыли мокрыми пылеуловителями определяется главным образом их перепадом давления. Чем больше перепад давления (гидравлическое сопротивление), тем больше эффективность очистки воздуха. Перепад давления у мокрых пылеуловителей обычно находится в диапазоне от 250 Па до более чем 3.7 кПа (1÷15 inches wg). При выборе конструкции мокрого пылеуловителя для конкретных условий использования учитывается требуемая степень очистки, запылённость очищаемого воздуха, и размер частиц.
При очистке влажного горячего воздуха мокрые пылеуловители являются самыми подходящими. При очистке такого воздуха с помощью тканевых (рукавных) фильтров возникают проблемы предотвращения конденсации воды и загрязнения фильтровального материала рукавов. А использование мокрых пылеуловителей устраняет эти проблемы. Но при использовании мокрых пылеуловителей возникает другая проблема – обработка воды, загрязнённой уловленной пылью. Она требует специальной обработки или использования прудов-отстойников.
Скрубберы Вентури
Разновидностью мокрых пылеуловителей являются скрубберы Вентури. Они состоят из воздуховода, форма которого схожа с формой трубки Вентури, и брызгоуловителя (Рис. 1.22). Запылённый воздух разгоняется до скорости 60-180 м/с (12,000÷36,000 feet per minute) во входной сужающейся части воздуховода. Из-за возникающих сильных завихрений происходит разрушение крупных капель воды, и возникает перепад давления от 1245 до более чем 3735 Па (5÷15 inches wg). Для защиты от абразивного износа воздуховод скруббера Вентури может быть сделан с керамической облицовкой. Сильные завихрения заставляют частицы воды и пыли сталкиваться друг с другом в горловине воздуховода. Затем полученные капли, загрязнённые пылинками, улавливаются инерционным брызгоуловителем.
Скруббер с отбойниками (Impingement Plate Scrubber)
В другом типе мокрых пылеуловителей – скруббере с отбойниками (Рис. 1.23) — загрязнённый воздух пропускается через отверстия в перфорированной пластине снизу вверх, и сталкивается со слоем воды, находящимся на пластине. Над каждым из отверстий есть пластинка, в которую ударяется прошедший отверстие воздух, что приводит к образованию маленьких капелек. Близкий контакт газа и жидкости приводит к эффективному улавливанию пылинок. Типичный перепад давления – 1 кПа (4 inches wg).
Скруббер с орошением потока каплями воды (Spray Tower Scrubber)
В таких скрубберах используют распыление воды, капли которой падают против направления движения запылённого воздуха, и при этом улавливают частицы пыли. Эффективность улавливания пыли такими скрубберами обычно низкая, а типичный перепад давления – 250-500 Па (1÷2 inches wg). При очистке воздуха, загрязнённого частицами размером ≥ 10 мкм их эффективность порядка 70%, а при улавливании меньших частиц она ещё хуже. Но такие пылеуловители могут очищать воздух при очень большой концентрации пыли без опасности засорения
Циклоны с водяной плёнкой
Как и обычные – “сухие” – циклоны, в циклонах с водяной плёнкой для улавливания частиц используется центробежная сила, смежающая пылинки до касания покрытых плёнкой воды стенок пылеуловителя. Вода для смачивания стенок подаётся в верхней части устройства, и стекая вниз, она смывает уловленные частицы. Перепад давления у такого циклона обычно 500÷2000 Па (2÷8 inches wg), и он хорошо улавливает частицы размером от 5 мкм и больше.
Промышленные электрофильтры[править]
Электрофильтры – это пылеуловители, которые используют для улавливания частиц электрические силы, перемещающие последние из потока загрязнённого воздуха к (улавливающим) пластинам - электродам. При прохождении загрязнённого воздуха через пылеуловитель частицам сообщается отрицательных заряд в первой секции устройства, где для этого специальные коронирующие электроды создают коронный разряд. При этом с таких электродов стекает поток ионов, движущихся сквозь загрязнённый воздух, и прикрепляющихся к частицам. После придания частицам отрицательного заряда на них начинает действовать электрическое поле, и они начинают притягиваться к осадительным пластинам (электродам). Слой уловленных частиц удаляется с осадительных электродов отряхиванием.
Обычно начальные затраты на закупку и монтаж электрофильтров выше, (чем у других пылеуловителей), но у них есть ряд достоинств, которые стоит упомянуть. После установки электрофильтры требуют минимального техобслуживания, так как в них (практически) нет подвижных частей. Затраты времени на установку и эксплуатационные расходы у них также ниже. Наконец, электрофильтры позволяют повторно использовать уловленный продукта в технологическом процессе.
Существует четыре основных типа электрофильтров: сухие – с плоскими осадительными электродами и проволочными коронирующими электродами, и (сухие) с плоскими электродами flat plate (dry); мокрые; и двухзонные. Электрофильтры могут очищать большие объёмы воздуха, неплохо работают при различных температурах, и требуют минимального техобслуживания. К их недостаткам относят большие размеры, эксплуатационные расходы, нестабильная эффективность. Более подробно достоинства и недостатки электрофильтров обсуждаются в руководстве ACGIH: ACGIH handbook, Industrial Ventilation: A Manual of Recommended Practice for Design[1- 1].
Устройства для выгрузки пыли[править]
Collector discharge devices
Пыль, уловленная рукавным фильтром, сбрасывается и падает вниз - в бункер пылеуловителя. В этом бункере должно быть устройство для выгрузки уловленной пыли, которое должно обеспечивать сохранение герметичности пылеуловителя в процессе выгрузки пыли, чтобы не произошло уменьшение разрежения в присоединённой к фильтру вентиляционной системе. Обычно для выгрузки уловленной пыли из бункеров пылеуловителей используют шлюзовые роторные питатели (rotary airlock valve), двойные мигалки (double dump valves), затвор типа плоская мигалка (tilt valve), и вакуумные клапаны (dribble valve). Все эти устройств есть в продаже в разных вариантах конструктивного исполнения, и производятся разными изготовителями.
Шлюзовый роторный питатель[править]
Rotary Airlock Valves
Это устройство обычно используют тогда, требуется обеспечить и герметичность, и измерение количества выгружаемого материала. Хотя такие устройства обычно используют для выгрузки пыли из рукавных фильтров, но это не наилучшее применение подобных устройств. Недостатки – большая стоимость и, возможно, большие расходы на ремонт из-за абразивного износа.
Двойные мигалки[править]
Double Dump Valves
Двойные мигалки – это два клапана, устанавливаемые последовательно в месте выгрузки пыли из бункера (рукавного фильтра). Они могут срабатывать под действием веса уловленной пыли, или автоматически. При автоматическом срабатывании, вращающийся кулачок кратковременно открывает нормально-закрытый клапан (подпружиненный) – верхний и нижний. Каждый из клапанов открывается отдельно, по-очереди – так, что когда один открыт, другой всегда закрыт. Благодаря этому пыль высыпается через один из клапанов, а другой закрытый клапан сохраняет герметичность пылеуловителя. Если клапан открывается под действием веса уловленной пыли, то его конструкция проще, а выгрузка пыли не автоматизирована (Рис. 1.24). Для установки обоих видов пылевыгрузных устройств требуется, чтобы под бункером пылеуловителя было достаточно места (по вертикали). При автоматическом открывании может происходить износ устройства на уровне расположения кулачка каждого из клапанов.
Рис. 1.24. Пылевыгрузное устройство типа двойная мигалка с противовесами
Затвор типа плоская мигалка[править]
Tilt Valves
Плоская мигалка схожа с двойной мигалкой, и их обычно устанавливают по две. Поворачивающаяся (закрывающая) часть этих затворов (язык) обычно находится или в горизонтальном, или в близком к горизонтальном положении, и присоединена к противовесу. Затворы регулируют так, чтобы они были плотно закрыты (при отсутствии уловленной пыли). По мере накопления уловленной пыли её вес начинает преодолевать разрежение в бункере и усилие от противовеса, и затвор открывается. Уловленная пыль сбрасывается вниз, на следующий затвор. Обычно расстояние между затворами – 63÷76 см (24÷30 inches) для того, чтобы верхний затвор успел закрыться до того, как откроется нижний.
Такое пылевыгрузное устройство дешевле, чем двойная мигалка или шлюзовой роторный питатель, но его трудно отрегулировать. После эксплуатации в течение некоторого периода может произойти залипание и фиксация в открытом положении. Для размещения нужно пространство ~ 1.2 м (4 feet) под бункером пылеуловителя (по вертикали).
Вакуумный клапан[править]
Vacuum or Dribble Valves
Вакуумный клапан обычно состоит из эластичной резиновой трубы, установленной в стальном кожухе, который присоединяется к нижней части бункера пылеуловителя в месте выгрузки пыли. Изготовители предлагают клапаны разной конструкции. В некоторых используется клапан, похожий по форме на рыбий хвост (в трубообразном корпусе с фланцем для крепления). При работе вентиляционной системы в бункере пылеуловителя возникает разрежение, которое заставляет резиновую трубку деформироваться и сплющиться, закрывая отверстие. Это сплющенное закрытое состояние сохраняется до тех пор, пока над клапаном не скопится достаточно много уловленного материала так, что его вес раздвинет стенки резиновой трубки, и он высыплется. Обычно такие клапаны стоят недорого, очень надёжны, не требуют техобслуживания, и не требуют много места для размещения.
Фильтровальные материалы[править]
За последние 10 лет в промышленности была проделана большая работа не столько в области самих пылеуловителей, сколько в области совершенствования фильтровальных материалов. Некоторые из разработанных материалов предназначены для использования в тяжёлых эксплуатационных условиях. Разработанные ткани могут быть предназначены или для использования в каких-то конкретных условиях, или они могут обеспечить более эффективную работу пылеуловителя . Сейчас разработано много разных фильтровальных материалов, и это увеличивает выбор при проектировании фильтров.
Одно из самых важных свойств любого пылеуловителя – его способность улавливать частицы пыли из проходящего через фильтровальный материал потока воздуха. Термин “фильтровальная ткань” и ”фильтровальный материал” – равнозначны. Для установки в пылеуловители изготовители предлагают разные фильтровальные материалы с разнообразными свойствами. Вне зависимости от различия фильтровальных материалов, их эффективность зависит от способности улавливать частицы из потока воздуха. Способность фильтровальной ткани пропускать через себя воздух (то есть – её проницаемость) обычно описывают как объём воздуха, который может пройти через квадратный фут фильтровального материала при перепаде давления 125 Па (1/2 дюйма водяного столба). Другой показатель свойств фильтровального материала – его способность улавливать частицы пыли (эффективность). Например, высокоэффективный противоаэрозольный фильтр (НЕРА) способен улавливать не менее 99.97% частиц размером 0.3 мкм. А в промышленности предпочитают для описания эффективности использовать оценку минимальной эффективности MERV (minimum efficiency reporting value rating) (Таблица 1.3). Как видно из таблицы MERV, чем эффективнее фильтр, тем разнообразнее диапазоны частиц, которые он может улавливать.
Группа | Оценка MERV | Средняя эффективность улавливания частиц (PSE) размером 0.3-1 мкм | Средняя эффективность улавливания частиц (PSE) размером 1-3 мкм | Средняя эффективность улавливания частиц (PSE) размером 3-10 мкм |
---|---|---|---|---|
1 | 1
2 3 4 |
<20%
<20% <20% <20% | ||
2 | 5
6 7 8 |
20-34.9%
35-49.9% 50-69.9% 70-84.9% | ||
3 | 9
10 11 12 |
<50%
50-64.9% 65-79.9% 80-89.9% |
≥85%
≥85% ≥85% ≥90% | |
4 | 13
14 15 16 |
<75%
75-84.9% 85-94.9% ≥95% |
≥90%
≥90% ≥90% ≥95% |
≥90%
≥90% ≥90% ≥95% |
Если способность фильтра улавливать частицы пыли за счёт касания/зацепления, инерционного осаждения, диффузии и электрических сил выше, то и его оценка MERV тоже будет выше. Ниже приводится краткое описание упомянутых механизмов улавливания аэрозолей:
- Касание/зацепление происходит, когда частицы маленького размера движутся по линиям течения воздуха, и проходят при этом рядом с волокном фильтровального материала на расстоянии своего радиуса от его поверхности, и прилипают к волокну.
- При инерционном осаждении более крупные частицы, которые не способны следовать линиям течения воздуха при их искривлении около волокон сталкиваются с последними. Инерционное осаждение возрастает с ростом скорости воздуха и уменьшением расстояния между волокнами.
- Улавливание за счёт диффузии происходит, когда самые маленькие частицы (особенно те, которые меньше 0.1 мкм) под действием ударов молекул воздуха изменяют направление движения так, что улавливаются волокнами за счёт инерционного осаждения или касания.
- Электростатическое осаждение происходит тогда, когда фильтровальный материал может сохранять электростатические заряды. Так как у частиц пыли тоже есть электрические заряды, при их прохождении через фильтр они притягиваются и улавливаются волокнами.
Фильтровальный материал изготавливается из натуральных или искусственных волокон, и может быть или тканым, или нетканым. Для описания свойств тканых фильтровальных материалов обычно используют массу единицы площади или число нитей (на 100 мм) (thread count). Для описания нетканых материалов также используют массу единицы площади, но обычно дополняют классификацией толщины фильтра. Эффективность улавливания аэрозолей неткаными материалами обычно выше, чем у тканых (при одинаковой толщине), так как у нетканых материалов меньше размер пор. Важно отметить, что с точки зрения эффективности улавливания пыли, эффективность любого фильтровального материала (или его оценка MERV) может быть повышена за счёт использования более тонких волокон, увеличением числа волокон на единицу площади, или увеличением плотности упаковки волокон.
У любого фильтровального материала при его загрязнении уловленной пылью возрастает эффективность или оценка MERV. После начального периода улавливания частиц пыли с помощью какого-то из механизмов, описанных выше, на поверхности фильтровального материала образуется слой уловленных частиц, и при продолжении фильтрации запылённого воздуха этот слой становится главным фильтром, улавливающей средой. По мере продолжения очистки воздуха всё больше и больше частиц сталкивается и улавливается слоем ранее уловленных частиц, и этот слой растёт. Через какое-то время толщина этого слоя становится такой большой, что он уже сильно мешает прохождению воздуха через фильтр, и это приводит к большому возрастанию гидравлического сопротивления. После того, как возрастающий перепад давления достиг определённого значения, нужно удалить с фильтра образовавшийся на нём слой уловленной пыли каким-то механическим способом (отряхиванием, обратной продувкой, импульсной продувкой сжатым воздухом – описано выше).
Улавливание частиц фильтровальной тканью[править]
Улавливание частиц фильтровальной тканью происходит с помощью двух механизмов. Первый – улавливание частиц волокнами ткани и осевшими на них ранее уловленными частицами - по всей толщине фильтровального материала (depth loading). Это означает, что (улавливание пыли тканью) не зависит от образования слоя уловленных частиц, что позволяет получить оптимальную эффективность. Второй механизм – улавливание частиц преимущественно слоем ранее уловленных частиц, образовавшимся на поверхности фильтровального материала (surface loading). Это значит, что для получения максимальной эффективности необходимо, чтобы произошло образование слоя уловленных частиц на поверхности.
У войлочных фильтровальных материалов используется первый механизм. А фильтровальные ткани из полиэстера, полипропилена, арамидных волокон и схожих фильтровальных волокон используют второй механизм – они должны создавать и сохранять слой уловленных частиц в течение всего времени эксплуатации пылеуловителя. Таким образом, при этом механизме очистки фильтровальный рукав становится опорой, поддержкой для слоя пыли, улавливающего частицы. Пыль может проходить внутрь фильтровальной ткани для образования слоёв уловленных частиц на волокнах. В результате уловленная пыль создаёт пористую улавливающую среду, в которой размер пор гораздо меньше, чем в самой фильтровальной ткани, и это повышает эффективность улавливания пыли ранее уловленными частицами. Без этих уловленных частиц запылённый воздух будет проходить через крупные поры фильтровальной ткани, и эффективность очистки воздуха будет слишком низкой. Поэтому при проектировании и эксплуатации рукавных фильтров с рукавами из фильтровальной ткани важно использовать подходящие: отношение расхода воздуха к площади фильтра, периоды между очисткой рукавов и давление, при котором происходит очистка. При оптимальном режиме работы перепад давления на фильтре составляет 750÷1500 Па (3÷6 inches wg), а частота проведения очистки и расход сжатого воздуха сведены к минимуму. Это не означает, что если система работает при перепаде давления больше 1500 Па, то её режим работы не оптимальный. Некоторые системы могут эффективно работать при большем перепаде давления. Система работает удовлетворительно, если перепад давления постоянен, и обеспечивается очистка воздуха в необходимой степени при заданном его расходе.
Если применяется (специальный) фильтровальный материал, у которого улавливание частиц просиходит на поверхности самого материала, то для получения оптимального режима очистки образования слоя уловленной пыли на волокнах в толще фильтровального материала, или на его поверхности - не требуется. У таких фильтровальных материалов (эффективное) улавливание пыли происходит на поверхности самого материала. В некоторых из таких фильтровальных материалов используются мембраны, состоящие из очень тонкого слоя (1 mil) фторопласта PTFE (polytetrafluoroethylene), приклеенного к подложке. В качестве подложки может использоваться обыкновенный войлок. При изготовлении размер пор контролируется, что позволяет предсказать эффективность улавливания. Размер пор настолько мал, что через них способны пройти только очень маленькие субмикронные частицы, и поэтому эффективность очистки воздуха у такого материала очень высока.
У пылеуловителей, которые используют фильтровальные материалы, схожие с войлоком, перепад давления обычно больше, чем при использовании фильтровальных материалов с улавливанием пыли на поверхности, так как у них к сопротивлению фильтровального материала добавляется сопротивление слоя уловленной пыли. Как упоминалось ранее, перепад давления у таких пылеуловителей (с образованием слоя уловленной пыли) обычно находится в пределах 750÷1500 Па, а у пылеуловителей с осаждением пыли на поверхность фильтровального материала – в пределах 500÷1000 Па (3÷6 inches wg / 2÷4 inches wg).
В рукавных фильтрах, в которых регенерация фильтровального материала проводится с помощью отряхивания, как фильтровальный материал обычно используется тканый х/б, сатин из полиэстера и войлок с небольшой массой на единицу площади. У современных пылеуловителей с регенерацией импульсной продувкой сжатым воздухом и обратной продувкой используют фильтровальные материалы с плотностью 300-600 г/м2. В двух последних типах рукавных фильтров не используют тканые фильтровальные материалы, так как процесс очистки (в таких тканях) создаёт более сильную нагрузку на ткань, чем отряхивание. При импульсной продувке произойдёт открывание (крупных) пор фильтровальной ткани, что приведёт к просачиванию большого количества неуловленной пыли (в течение некоторого периода времени сразу после продувки). В картриджных фильтрах обычно используют фильтровальные материалы из смеси целлюлозных и синтетических волокон, и скрученных (spun-bonded) волокон полиэстера.
При выборе фильтровального материала для конкретных условий использования учитывается: температура очищаемого воздуха, концентрация пыли, распределение частиц по размерам, химический состав газа, абразивные свойства (пыли), статический заряд, свойства при регенерации, требуемая степень очистки воздуха.
Ниже приводится более подробное описание этих критериев.
- Температура. Максимальная эксплуатационная температура выбираемого фильтровального материала (для длительного режима использования) должна соответствовать (быть выше) максимальной возможной температуре очищаемой газовой смеси.
- Концентрация пыли в очищаемом газе. Запылённость очищаемого газа имеет очень большое значение, особенно тогда, когда она низкая. При маленькой концентрации пыли трудно добиться образования слоя пыли у тех фильтровальных материалов, в которых этот слой обеспечивает достаточную эффективность очистки.
- Распределение частиц по размерам. При большой доле мелкодисперсных частиц требуется использование более эффективной ткани.
- Химический состав очищаемого газа. Если в очищаемом газе есть агрессивные компоненты, или органические растворители, то проектировщик должен гарантировать, что выбранный фильтровальный материал будет способен работать в таких условиях.
- Абразивные свойства. Если пыль имеет абразивные свойства, то при проектировании нужно учесть это, используя боле толстый войлок, или устанавливая “манжеты” (cuffs) на нижнюю часть тех рукавов, которые находятся рядом со отверстием для входа запылённого воздуха.
- Статический заряд. При очистке взрывоопасных пылегазовых смесей и улавливании такой пыли, которая может создать значительный статический заряд в воздуховодах, требуется заземление. Для этого, например, может использоваться проволока, вшитая в материал фильтровального рукава, и прикреплённая к перфорированной пластине для монтажа рукавов. также для заземления можно использовать антистатические волокна (epitropic fibers) – углеволокно, графитовые волокна, или добавляя к фильтровальному материалу 3-4% волокон из нержавеющей проволоки. В этих случаях важно обеспечить, чтобы конец фильтровального рукава (который используется для его крепления) был сделан из электропроводного материала, и обеспечил стекание заряда на заземление.
- Свойства при регенерации. Хорошо спроектированный рукавный фильтр решает две задачи: улавливает пыль, и сбрасывает её с фильтровального материала после улавливания. Если пыль влажная, масляная или липкая, может потребоваться обработка фильтровального материала для улучшения его очистки от уловленной пыли. Для этого может использоваться модификация поверхности фильтровального материала – подпаливание поверхности или её оглазуровывание (singeing or glazing). Также для улучшения отделения уловленной пыли поверхность материала может покрываться фторопластом или мембраной из него. Также изготавливаются специальные фильтровальные материалы, в которых волокна обрабатываются до начала изготовления войлока (это увеличивает срок службы покрытия по сравнению с обычным).
- Эффективность. Для оценки требуемой степени очистки используется допустимая концентрация пыли в очищаемом воздухе, которая определяется специалистом по охране окружающей среды на основе требований Агентства по охране окружающей среды, и требований законодательства штата или региона (которые определяют допустимое значение выбросов аэрозоля в атмосферу).
(Более подробно о тканевых фильтрах можно узнать в книге: Charles E. Billings et. al. Handbook of fabric filter technology 1970 644с 49 Мб)
Проектирование пылеулавливающей системы[править]
Применение для простых систем принципов, описанных в этой главе выше, позволяет проектировать более сложные вентиляционные системы. В сущности, сложная вентиляционная система – это просто сочетание нескольких простых систем, соединённых вместе (Рис. 1.25). При проектировании сложной системы нужно использовать следующий базовый метод:
- Рассматривается план предприятия, расположение оборудования, его высота над уровнем земли.
- Проектирование начинается с того кожуха / укрытия / местного отсоса и т.п., который наиболее удалён от вентилятора.
- Прорисовывается эскиз воздуховодов вентиляционной системы (включая вид сверху и высоту), положение вентилятора, пылеуловителя и оборудования, и каждая ветвь и секция вентиляционной системы (основной) обозначается цифрами или буквами для удобства.
- Или выбирается из имеющихся, или проектируется укрытие / местный отсос, соответствующие условиям в месте образования пыли, и определяется требуемый для него расход воздуха.
- Создаётся эскиз вентиляционной системы с укрытиями / отсосами от всех источников пыли, включая ориентацию и высоту места выпуска очищенного воздуха.
Ниже приводятся некоторые основные положения, используемые при проектировании пылеулавливающей вентиляционной системы:
- Одно из самых важных обстоятельств – количество пыли, которое (должна) улавливать вентиляционная система. У разных улавливающих систем разные способности улавливать пыль.
- (Знание) общего перепада давления в системе помогает определить тип используемого пылеуловителя. При улавливании наиболее летучей пыли разрежение во входном (в пылеуловитель) отверстии будет ниже 5 кПа (20 inches wg), т.к. для транспортировки летучей пыли от места образования до пылеуловителя не требуется использование воздуховодов с большой скоростью движения воздуха – ведь пыль не оседает. При таком разрежении можно использовать обычные рукавные фильтры и картриджные фильтры.
- В некоторых случаях требуется большее разрежение (более 10 кПа), и требуется усиленное газоочистное оборудование (способно работать при сильном разрежении).
- В большинстве вентиляционных систем могут использоваться пылеуловители круглой или прямоугольной формы. Но при большом разрежении (более 10 кПа) требуется использование более прочных цилиндрических корпусов.
После того, как будет сделана схема всей вентиляционной системы, включая все местные отсосы/укрытия, воздуховоды и пылеуловители, эта информация используется для определения требуемой производительности вентилятора. При этом (может потребоваться) многократно обращаться за помощью к изготовителям вентиляторов для подбора подходящего изделия и его параметров работы / регулировки.
Примечание к переводу: Помимо рекомендуемого авторами руководства (на английском языке), есть литература с описанием расчётов при проектировании вентиляционных сетей (высокоскоростных) на русском языке, доступна в интернет бесплатно. Например: Внутренние санитарно-технические устройства. Часть 3. Вентиляция и кондиционирование воздуха. Книга 1 (и книга 2 тоже). Справочник проектировщика. Москва, Стойиздат, 1992г. Под ред. Н.Н. Павлова и Ю.И. Шиллера.
Улавливание пыли, содержащей глину[править]
При проектировании системы, которая будет улавливать пыль, содержащую глину, требуется особая осторожность. Обычно глина высушивается до состояния, при котором содержание влаги составляет 10% - по сравнению с продукцией из кварца, которая высушивается до содержания влаги 0.5% и менее. Большее содержание влаги в глине становится важным, если температура перемещаемого воздуха достигает точки росы. Обычно это случается у стенок воздуховодов, или у стенок корпуса рукавного фильтра. Поверхность частиц глины становится липкой и они прилипают к любой поверхности, которой касаются. Через некоторое время происходит засорение или закупоривание (воздуховодов). Для предотвращения этого нужно принять дополнительные меры – теплоизоляция, подогрев воздуховодов, установка оборудования в (отапливаемом) помещении и т.п.
Вентиляторы[править]
(Выбор) вентилятора является важной частью проектирования пылеулавливающей вентиляционной системы. Они используются для перемещения воздуха в вентиляционной системе, для чего создают или избыточное давление на входе, или разрежение на выходе из неё (blowing or exhausting ventilation system). В первом случае вентилятор устанавливается около всасывающего конца вентиляционной системы, и используется для “проталкивания” воздуха через систему. Во втором случае вентилятор устанавливается около выпускного отверстия и используется для всасывания воздуха так, что тот проходит (просасывается) через всю систему[1- 3].
В вентиляционных системах используют различные вентиляторы, и их выбор зависит от их эксплуатационных характеристик. Чтобы правильно выбрать вентилятор для вентиляционной системы, нужно иметь представление об эксплуатационных характеристиках вентиляторов.
Эксплуатационные характеристики вентиляторов[править]
Эксплуатационные характеристики вентиляторов предоставляются изготовителем. Эта информация может предоставляться или в виде таблиц, и/или в виде графиков. Таблицы с характеристиками вентиляторов дают лишь минимальную необходимую информацию – статическое давление, расход воздуха, и мощность, потребляемая вентилятором (с учётом его КПД) (brake horsepower BHP)[1- 12]. Статическое давление определяется тем перепадом давления, который необходим для преодоления трения во всей вентиляционной системе. Расход воздуха – количество воздуха, которое должно перемещаться через всю вентиляционную систему. Потребляемая мощность BHP – это мощность, которую должен сообщать вентилятору двигатель при определённых значениях статического давления и расхода воздуха (и при том значении КПД, который соответствует этим расходу и давлению).
Также для описания характеристик вентиляторов используют графики параметров их работы, которые описывают взаимосвязи между параметрами вентилятора для определённых условий. Обычно такие графики строят для конкретной модели вентилятора и для определённой частоты вращения (об/мин RPM). Если нужно описать свойства определённой модели вентилятора при разной частоте вращения, то приходится использовать серии графиков, каждый из которых соответствует определённой частоте вращения. На Рис. 1.26 показаны типичные графики параметров работы: статическое давление по оси OY, а расход воздуха – по оси OX. Также на графике показана кривая потребляемой мощности BHP (со шкалой на отдельной оси OY). Иногда дополнительно приводят информацию об уровне шума и КПД[1- 3].
Вентилятор выбирают под известные значения расхода воздуха в вентиляционной системе и статическое давление. Нужно выбрать такой вентилятор, чтобы требуемые значения статического давления и расхода воздуха попадали на “рабочие участки” (operating range) его характеристик, а не в том диапазоне, где графики “сваливаются” (stalling ranges).
Если вентилятор работает в своём рабочем диапазоне, воздух проходит через лопатки его рабочего колеса плавно, без завихрений - и тихо. Если расход воздуха и статическое давление попадают на рабочий участок, то по графику можно определить, какую мощность нужно подвести к вентилятору для обеспечения его работы в этом режиме. А если расход воздуха и статическое давление попадают на не рабочий участок, то вентилятор не будет работать нормально, и произойдёт аэродинамический срыв. Это происходит, когда расход воздуха и скорость воздуха становятся настолько маленькими, что воздух уже не может двигаться, следуя контурам лопаток рабочего колеса. Воздух, входящий во входное отверстие вентилятора, отбрасывается лопатками дальше – для получения большого статического давления при маленьком расходе воздуха, что приводит к появлению сильных завихрений и завихрений. Поэтому на таком режиме работы вентилятор будет создавать сильный шум и у него будет низкий КПД из-за турбулентности и появления вихрей[1- 13].
Уравнения пересчёта параметров вентилятора[править]
Для определения того, как изменение частоты вращения влияет на статическое давление, расход воздуха и потребляемую мощность, можно использовать несколько уравнений. Эти упрощённые уравнения применимы до тех пор, пока плотность воздуха и диаметр вентилятора неизменны[1- 13].
- CFM2 / CFM1 = RPM2 / RPM1 (Уравнение 1.8) (СИ, IP)
- SP2 / SP1 = (RPM2 / RPM1)2 (Уравнение 1.9) (СИ, IP)
- BHP2 / BHP1 = (RPM2 / RPM1)3 (Уравнение 1.10) (СИ, IP)
- N2 – N1 = 50 × Log10 × (BHP2 / BHP1) (Уравнение 1.11)
- где RPM = частота вращения, об/мин;
- CFM = расход воздуха, м3/с, м3/час [cfm];
- SP = статическое давление (уравнение может использоваться и для полного, и для статического, и для динамического давлений – но одних и тех же);
- BHP = потребляемая мощность вентилятора (может использоваться для полезной и потребляемой мощностей, или для полной мощности – но для одной и той же, и
- N = уровень шума, дБ.
Индексы обозначают разные режимы работы вентилятора, то есть – 1 для одного режима, а 2 – для другого (например – разная частота вращения). Также есть уравнения, позволяющие учесть изменение диаметра рабочего колеса и плотность воздуха, но это выходит за пределы настоящей главы[1- 3]. Для определения влияния изменения плотности воздуха и диаметра рабочего колеса можно обратиться к[1- 13] и[1- 3].
Типы вентиляторов[править]
Наиболее широко используются два типа вентиляторов – осевые и радиальные (centrifugal fans). Также имеются конструкции вентиляторов, в которых сочетаются элементы обоих типов: канальные и крышные вентиляторы. Для выбора подходящего вентилятора используется информация о требуемых расходе воздуха и статическом давлении для данной вентиляционной системы.
Осевые вентиляторы
К осевым вентиляторам относят вентиляторы пропеллерного типа (propeller fans), канальные (tubeaxial fans), канальные с (сильным) поджатием потока (vaneaxial fans), и двухступенчатые осевые вентиляторы. Осевые вентиляторы перемещают воздух в направлении оси своего вращения. Чаще всего встречаются вентиляторы пропеллерного типа. Они обычно устанавливаются в стене здания около источника тепла для удаления горячего воздуха наружу (Рис. 1.28). У таких вентиляторов двигатель может располагаться по-разному: может использоваться ременная передача, или рабочее колесо устанавливается прямо на ось мотора. В настенных вентиляторах могут быть жалюзи, которые автоматически закрываются при выключении вентилятора. Вентиляторы пропеллерного типа используют тогда, когда нужно перемещать много воздуха при небольшом перепаде давления[1- 13].
Канальные вентиляторы (tubeaxial fans) используют для выброса воздуха из всасывающего воздуховода (Рис. 1.29 слева). Они состоят из рабочего колеса с большим числом лопаток, которое находится в цилиндрическом канале. Для улучшения перемещения воздуха в поперечном сечении лопатки обычно имеют аэродинамический профиль. Диаметр втулки может составлять от 30 до 50% от наружного диаметра рабочего колеса[1- 13]. (Трубообразный) корпус присоединяют к воздуховоду, и на корпусе располагается место крепления двигателя. Вентиляторы такой конструкции обычно используются тогда, когда требуется получить умеренное статическое давления (большее, чем то, которое могут обеспечить пропеллерные вентиляторы).
Канальные вентиляторы (tubeaxial fans) схожи с канальными вентиляторами с поджатием потока (vaneaxial fans). В корпусе последних есть направляющие лопатки, направленные параллельно потоку воздуха (Рис. 1.29 справа). Эти лопатки используют для изменения направления движения воздуха, закрученного рабочим колесом, в чисто осевое, не закрученное направление, что повышает статическое давление. Ни в пропеллерных, ни в канальных вентиляторах без поджатия потока (tubeaxial fans) нет таких лопаток, и из-за этого часть потребляемой энергии теряется впустую на ненужное закручивание потока. Диаметр втулки канального вентилятора с поджатием потока (vaneaxial fans) составляет от 50 до 80% от наружного диаметра рабочего колеса[1- 13]. Такие вентиляторы используют для получения большего статического давления.
Двухступенчатые осевые вентиляторы обычно состоят из двух осевых вентиляторов, соединённых последовательно. Это позволяет получить большее статическое давление, чем у одного такого вентилятора, так как статические давления складываются. В таком вентиляторе оба рабочих колеса могут вращаться в одну сторону, и тогда между ними ставят направляющие лопатки, или же они вращаются в противоположные стороны.
Радиальный вентилятор
В радиальном вентиляторе воздух движется не так, как в осевом. В радиальном вентиляторе воздух проходит через вращающееся рабочее колесо и выбрасывается в радиальном направлении лопатками – в корпус вентилятора. В результате воздух движется перпендикулярно оси вращения, или параллельно движению лопаток[1- 3], а корпус используется для направления потока воздуха в требуемую сторону (Рис. 1.30).
Существуют различные типы радиальных вентиляторов. У всех типов радиальных вентиляторов схожий характер движения воздуха, а отличие заключается в форме и расположении лопаток рабочего колеса. У лопаток разных типов есть свои достоинства при использовании вентилятора в разных случаях. В зависимости от назначения вентилятора оптимальная конструкция рабочего колеса может быть разной:
- Если поперечное сечение лопаток соответствует аэродинамическому профилю (airfoil type blades), то у такого вентилятора будет максимальный КПД и минимальный уровень шума.
- У вентилятора с искривлёнными лопатками, загнутыми назад (backward curved blades), КПД будет несколько меньше. Такая конструкция лопаток больше подходит для вентиляторов, перемещающих загрязнённый воздух, так как у них постоянная толщина, и они могут быть сделаны из более прочного материала, стойкого к воздействию загрязнённого воздуха.
- Прямые лопатки, загнутые назад (backward inclined blades) – менее прочные, и у вентилятора с такими лопатками ниже КПД. Но их легче изготавливать из-за простой формы.
- Изготавливаются рабочие колёса с радиальными лопатками, искривлёнными на конце (radial tip blades). Такие конструкции в основном используют при большом диаметре рабочего колеса (75-150 см / 30- 60 inches), которое должно работать при высокой температуре при минимальной загрязнённости воздуха[1- 13].
- Если лопатки загнуты вперёд (forward curved blades), то скорость потока воздуха будет больше, чем у любого другого радиального вентилятора того же размера при тех же оборотах. Это позволяет сделать более компактный вентилятор (по сравнению с другими типами радиальных вентиляторов). Такие вентиляторы часто используют в печах, кондиционерах, и для охлаждения электронного оборудования.
- Прямые лопатки (radial blades) – прочные и самоочищающиеся, но у вентилятора с прямыми лопатками низкий КПД. Такие вентиляторы можно использовать для перемещения газа, содержащего агрессивный дым или абразивную пыль (например – при абразивной обработке материала).
Другие типы вентиляторов[править]
Канальные радиальные вентиляторы, или радиальные прямоточные вентиляторы (axial-centrifugal fans, or tubular centrifugal, or in-line centrifugal fans) используют центробежный вентилятор для перемещения воздуха в канале воздуховода (без изменения направления движения). Для этого воздух проходит через входное отверстие, и поворачивает на 90° для прохождения через лопатки радиального вентилятора. Затем воздух движется радиально и снова поворачивает на 90° так, что движется в первоначальном направлении к выходному отверстию (Рис. 1.31). Эти вентиляторы удобно устанавливать на воздуховоды, и они создают большее статическое давление, чем осевые вентиляторы при одинаковых диаметре и оборотах. Но из-за двух поворотов воздуха на 90° их КПД ниже, чем у осевых вентиляторов.
Крышные вентиляторы[править]
Изготавливаются крышные вентиляторы как осевой, так и радиальной конструкции (Рис. 1.32). Обычно они устанавливаются на крышу завода, и они являются составной частью общей вентиляционной системы предприятия, описанной в главе 8 “Уменьшение пылеобразования во второстепенных источниках”. Большинство крышных вентиляторов используют для удаления воздуха из здания, и создания восходящего потока воздуха в здании. Но при необходимости они могут использоваться для подачи чистого воздуха в здание сверху вниз, что приведёт к появлению нисходящего потока воздуха. Выпуск удаляемого воздуха может быть радиальным или вертикальным. Вертикальный выпуск обычно используют для воздуха, загрязнённого маслом, жиром или пылью. При использовании крышных осевых вентиляторов воздуховоды (трубы для выпуска воздуха) обычно не требуются. А при использовании крышных радиальных вентиляторов воздуховоды могут потребоваться.
.
ССЫЛКИ
- ↑ 1,0 1,1 1,2 1,3 1,4 1,5 ACGIH [2010]. Industrial ventilation: a manual of recommended practice for design. 27th ed. Cincinnati, OH: American Conference of Governmental Industrial Hygienists.
- ↑ Hinds WC [1999]. Aerosol technology, properties, behavior, and measurement of airborne particles. 2nd ed. New York: John Wiley & Sons, Inc.
- ↑ 3,0 3,1 3,2 3,3 3,4 3,5 3,6 Hartman HL, Mutmansky JM, Ramani RV, Wang YJ [1997]. Mine ventilation and air conditioning. 3rd ed. New York: John Wiley & Sons, Inc.
- ↑ Swinderman RT, Marti AD, Goldbeck LJ, Strebel MG [2009]. Foundations: the practical resource for cleaner, safer, more productive dust & material control. Neponset, Illinois: Martin Engineering Company.
- ↑ Johnson GQ [2005]. Dust control system design: knowing your exhaust airflow limitations and keeping dust out of the system. Powder and Bulk Eng 19(4):51–59 http://www.powderbulk.com/.
- ↑ DallaValle JM [1932]. Velocity characteristics of hoods under suction. ASHVE Transactions 38:387.
- ↑ Fletcher B [1977]. Centreline velocity characteristics of rectangular unflanged hoods and slots under suction. Ann Occup Hyg 20:141–146.
- ↑ Caputo AC, Pacifico MP [2000]. Baghouse system design based on economic optimization. Env Prog 19(4):238–245. http://www.abcm.org.br/pt/wp-content/anais/cobem/1999/pdf/AAADAE.pdf
- ↑ Martin CT [1999]. Fine filtration fabric options designed for better dust control and to meet PM2.5 standards. Cement Industry Technical Conference IEEE IAS/PCA. pp. 385–393.
- ↑ Mycock JC [1999]. Pick the right baghouse material. Power Eng 103(7):43–46. http://www.powderbulk.com/
- ↑ EPA [1995]. AP 42, Fifth Edition, Compilation of air pollutant emission factors, volume 1: stationary point and area sources. Environmental Protection Agency. http://www.epa.gov/ttn/chief/ap42
- ↑ Greenheck Fan Corporation [1999]. The basics of fan performance tables, fan curves, system resistance curves, and fan laws. Schofield, WI: Greenheck Fan Corp.
- ↑ 13,0 13,1 13,2 13,3 13,4 13,5 13,6 Bleier FP [1998]. Fan handbook: selection, application, and design. New York: McGraw-Hill.
ГЛАВА 2. Обеспыливание с помощью воды[править]
Возможно, самым древним способом борьбы с пылью при переработке минеральных полезных ископаемых является использование воды (use of wet spray systems). При увлажнении масса каждой из частиц пыли возрастает, и это уменьшает её способность находиться в воздухе. Чем тяжелее группа частиц, тем труднее окружающему воздуху переносить их. Для эффективного пылеподавления с помощью увлажнения нужно правильно выбирать место расположения сопел, размер получаемых капель, характер распыления воды, и обеспечить необходимый уход и техобслуживание оборудования.
В большинстве случаев при переработке минеральных полезных ископаемых для увлажнения используется вода. Хотя использование распыления воды является очень простым методом, для разработки эффективной системы для конкретных условий нужно учесть ряд обстоятельств. При переработке полезных ископаемых распыление воды позволяет решать две задачи:
- Предотвращение попадания пыли в воздух путём увлажнения руды - за счёт смачивания пыли.
- Улавливание пыли, (уже) попавшей в воздух, орошением облака пыли каплями воды, которые сталкиваются с пылинками, прилипают к ним и (быстро) осаждаются вместе с ними.
В большинстве случаев для снижения запылённости используется сочетание этих методов.
Принципы борьбы с пылью с помощью воды[править]
Для эффективного использования распыления воды нужно помнить, что каждый тип руды и условия его обработки создают уникальную ситуацию, которая требует отдельного рассмотрения для разработки оптимальной (для неё) улавливающей системы. Например, распыление воды для некоторых видов руды недопустимо, особенно при большой концентрации глины или сланцев. Даже при маленькой концентрации эти вещества начнут засорять сита и произойдёт “зарастание” лотков. Кроме того, воду нельзя использовать круглый год.
Применение воды[править]
При использовании воды для снижения концентрации пыли, эффект от её применения ограничен по времени из-за испарения. Поэтому необходимо использовать распыление воды в разных местах технологической цепочки для эффективного снижения запылённости. При чрезмерном увлажнении могут возникнуть проблемы при выполнении любой операции, и переувлажнение может повлиять и на оборудование, и на технологический процесс, и на способность конечного продукта пересыпаться при транспортировке. В большинстве случаев хорошо спроектированная система, распыляющая воду мелкими капельками, увеличивает влажность (руды) не более чем на 0.1%[2- 1]; а распыление воды крупными каплями (для увлажнения для предотвращения пылеобразования) может повысить влажность на 1.5%.
При дроблении материала большинство образовавшихся частиц пыли не попадает в воздух, а остаётся на поверхности разрушенных кусков. Поэтому увлажнение для увеличения адгезии имеет большое значение, так как оно предотвращает отрыв и унос в воздух образовавшейся пыли. Для эффективной работы системы также важно обеспечить равномерность увлажнения. Пылеобразование будет наименьшим, если оросить руду водой, а затем механически перемешать руду и воду для равномерного увлажнения.
В идеале, работа оросительной системы должна быть автоматизирована так, чтобы вода распылялась только тогда, когда происходит обработка руды. При распылении воды для улавливания витающей пыли в автоматику можно добавить таймер, чтобы распыление продолжалось некоторое время после прекращения обработки руды.
Расположение сопел[править]
Из-за того, что образование пыли может происходить в разнообразных условиях, твёрдых и жёстких правил, определяющих расположение сопел для распыления воды (для снижения запылённости) - нет. Но есть указания, позволяющие повысить эффективность системы.
- В тех системах, которые используются для увлажнения руды для предотвращения образования пыли и её попадания в воздух, форсунки должны располагаться перед местом перегрузки, которое (в большинстве случаев) становится источником пыли[2- 2].
- Для хорошего перемешивания материала и воды нужно тщательно выбирать место расположения сопел[2- 2].
- Для предотвращения попадания пыли в воздух нужно раcполагать форсунки на оптимальном расстоянии от материала – достаточно далеко для того, чтобы распыляемая вода охватывала требуемую площадь, и достаточно близко для того, чтобы потоки воздуха не уносили капли воды в сторону от места, которое нужно увлажнить[2- 2]. При определении оптимального расстояния от форсунки до “цели” также нужно учитывать размер капель.
- При распылении воды для улавливания пыли, попавшей в воздух, форсунки нужно располагать так, чтобы капли воды могли взаимодействовать с пылью как можно дольше.
На Рис. 2.1 показано, как обычно используют распыление воды для снижения запылённости в месте сброса материала с конвейера в бункер. В этом случае форсунки устанавливают так, чтобы вода, распыляемая каждой из них, могла взаимодействовать с находящейся в воздухе пылью – так, чтобы не мешать работе других форсунок, и чтобы капли не уносились потоками воздуха.
Размер капель[править]
Controlling Droplet Size
При распылении воды для борьбы с пылью одним из важнейших параметров является размер капель. Если капли будет значительно больше размера пылинок, то в большинстве случаев при встрече пылинка будет увлекаться в сторону потоком воздуха, огибающим каплю, и не будет уловлена. А если размеры сопоставимы, то произойдёт столкновение, и пылинка будет уловлена каплей (Рис. 2.2). Для наилучшего улавливания пылинок их размер должен быть примерно равен размеру капель воды. Также вероятность улавливания возрастает, если (при распылении одинакового количества воды) размер капель уменьшится – из-за увеличения числа капель[2- 3].
При орошении материала для предотвращения попадания пыли в воздух нужно использовать капли размером больше 100 мкм (оптимально – от 200 до 500 мкм). А для улавливания пыли, попавшей в воздух, размер капель должен быть схожим с размером пылинок. Здесь требуется добиться столкновения капель и пылинок, и их падения вниз. Было показано, что это лучше всего обеспечивается при размере капелек от 10 до 150 мкм[2- 4]. В таблице 2.1 приводятся сведения о скорости осаждения частиц и капель разного размера.
Размер частицы пыли, мкм | Название | Скорость падения в спокойном воздухе, см/с† | Время, за которое она упадёт на 3.1 метра (10 ft), сек |
---|---|---|---|
5000-2000 | Ливень | 359 - 339 | 0.85 - 0.90 |
2000-1000 | Сильный дождь | 339 – 277 | 0.9 – 1.1 |
1000-500 | Умеренный дождь | 277 - 191 | 1.1 – 1.6 |
500-100 | Слабый дождь | 191 - 28 | 1.6 – 11 |
100-50 | Туман | 28 – 7.6 | 11 – 40 |
50-10 | Тяжёлый фоㆆ | 7.6 – 0.3 | 40 – 1020 |
10-2 | Тонкий фоㆆ | 0.3 – 0.012 | 1020 - 25400 |
† - добавлено при переводе †† - (fog) - разновидность тумана, ухудшает видимость сильнее, чем туман (mist).
Способы распыления воды[править]
Распыление – это образование капель воды при принудительной подаче её в сопло. Для распыления используются два способа.
- При гидравлическом или безвоздушном распылении (hydraulic or airless atomization) размер капель регулируется размером сопла и давлением жидкости. При этом используется высокое давление, и образуются капли маленького и среднего размера. Факел имеет форму веера с однородным распределением, полого конуса или сплошного конуса. Использование гидравлического распыления в большинстве случаев предпочтительно, так как оно дешевле из-за не использования сжатого воздуха.
- При воздушном распылении воды (air atomizing) капли образуются при разбивании жидкости сжатым воздухом. При этом давление жидкости меньше, и получаются капли маленького размера, равномерно распределённые в факеле. Но это более сложный и дорогой способ, так как для него требуется сжатый воздух. В большинстве случаев лучше располагать форсунки с воздушным распылением в тех местах, где частицы пыли очень маленькие, и форсунки должны быть как можно ближе к источнику пыли (хотя в некоторых случаях требуется использовать форсунки большой производительности так, чтобы они выпускали поток капель на большое расстояние – чтобы капли достигли облака пыли).
Добавки химических веществ, влияющие на размер капель[править]
При распылении воды иногда в неё добавляют поверхностно-активные вещества, так как они уменьшают поверхностное натяжение, что приводит к:
- уменьшению размеров капель;
- увеличению числа капель (при одинаковом расходе воды); и
- уменьшению угла смачивания[2- 2] – угла Θ между поверхностью жидкости и твёрдой поверхностью в месте их контакта (Рис. 2.3).
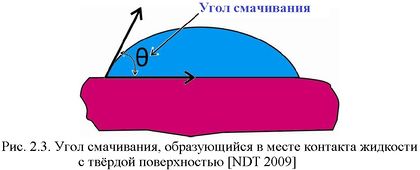
При использовании поверхностно-активных веществ улучшается смачивание частиц пыли жидкостью и их обволакивание жидкостью, что приводит к уменьшению расхода жидкости, необходимого для того же самого результата, по сравнению с распылением воды без поверхностно-активных веществ. Для улучшения увлажнения и предотвращения попадания пыли в воздух в воду добавляют небольшое количество поверхностно-активных веществ, обычно в соотношении 1:700÷1:1500[2- 7]. Хотя добавки помогают снизить запылённость, но нужно сказать, что из-за нескольких ограничений при добыче и переработке металлических и неметаллических ископаемых их используют нечасто.
- Добавки значительно дороже воды, они могут влиять на свойства перерабатываемого вещества, и на свойства конечного продукта.
- Добавки могут повреждать оборудование – например конвейерные ленты.
- Использование поверхностно-активных веществ требует больших трудозатрат, чем использование воды без добавок.
- Из-за гидрофобности (притяжения молекул) минералов при добыче и переработке металлических и не металлических полезных ископаемых добавки малополезны – по сравнению с добычей угля (уголь гидрофильный, плохо смачивается[2- 8].
Эффективность добавок зависит от:
- Свойств химической добавки;
- Гидрофобных свойств частиц минеральной пыли;
- Размера частиц пыли;
- Концентрации пыли;
- Водородного показателя воды рН, и
- От минералов, которые присутствуют в используемой воде[2- 9].
Типы форсунок и форма факела[править]
В зависимости от способа, используемого для распыления воды, и свойств получаемого факела капель, форсунки могут быть разных видов. Наиболее часто используемые форсунки дают полный конус, или полый конус; круг или полосу (веерный факел flat fan nozzle). Форсунки, использующие для распыления воды сжатый воздух, обычно дают круглый или веерный факел, а при гидравлическом распылении обычно получают полный или полый конус. Но некоторые форсунки с гидравлическим распылением тоже могут образовывать веерный факел.
Форсунки использующие сжатый воздух (пневматические)[править]
Форсунки, в которых для распыления жидкости используют сжатый воздух, иногда называют двухфазными (two-fluid nozzles), так как в них для распыления в поток жидкости вводится сжатый воздух. На Рис. 2.4. показаны две конструкции таких форсунок – с внешним и с внутренним смешиванием. В форсунках с внутренним смешиванием используется приспособление (an air cap), который смешивает потоки жидкости и газа внутри форсунки, так чтобы выбрасывалась распылённая вода, а в форсунках с внешним смешиванием приспособление (an air cap) смешивает потоки вне сопла форсунки. При внутреннем смешивании давление сжатого воздуха, распыляющее воду, направлено против давления жидкости, и дополнительно регулирует расход жидкости. При внешнем распылении давление сжатого воздуха не влияет на давление жидкости.
Форсунки с внутренним смешиванием могут создавать и круглый, и веерообразный факел, а форсунки с внешним смешиванием могут создавать веерообразный факел, как показано на Рис. 2.5.
При гидравлическом распылении вода проталкивается через отверстие (сопло) постоянного размера за счёт собственного высокого давления, что приводит к образованию капель. В зависимости от формы сопла форсунки могут быть получены капли разного размера и разная форма факела.
Гидравлические форсунки с полным конусом[править]
Hydraulic Full Cone Nozzles
Гидравлические форсунки с полным конусом создают сплошной конусообразный факел, который имеет круглое поперечное сечение, что обеспечивает большую скорость на удалении от форсунки (Рис. 2.6). Такие форсунки создают капли большого и среднего размера в широком диапазоне расходов воды и её давления. Обычно их используют тогда, когда нужно снизить запылённость, а источник пыли находится на большом расстоянии от форсунки[2- 5].
Гидравлические форсунки с полым конусом[править]
Hydraulic Hollow Cone Nozzles
Такие форсунки создают факел, который в поперечном сечении имеет кольцеобразную форму. Обычно форсунки с полым конусом обеспечивают меньший размер капель, чем другие гидравлические форсунки (при одинаковом расходе воды Рис. 2.7). Также у них больше диаметр сопла, что уменьшает риск его засорения. Гидравлические форсунки с полым конусом лучше использовать для улавливания пыли, попавшей в воздух, и они бывают двух типов по конструкции: с камерой, в которой жидкости придаётся вращательное движение, и с спиральным распылением (spiral sprays). У форсунок с вихревой камерой в большинстве случаев распыление жидкости происходит под прямым углом по отношению к направлению входящего потока. Но существуют форсунки и без изменения направления потока. Форсунки обеих конструкций создают более однородные потоки капель меньшего размера (Рис. 2.7). Если нужен больший расход воды, используют форсунки со спиральным распылением. Из-за большего размера отверстий уменьшается риск засорения. У таких форсунок распределение капель менее однородное, и размер капель больше (Рис. 2.8)[2- 5].
Гидравлические форсунки с веерообразным факелом[править]
Hydraulic Flat Fan Nozzles
Гидравлические форсунки с веерообразным факелом создают относительно большие капли в широком диапазоне расходов жидкости и углов раскрытия факела, и обычно они используются в ограниченном пространстве (Рис. 2.9). Такие форсунки также используются для смачивания материала для предотвращения попадания пыли в воздух. Эти форсунки бывают трёх конструкций – сужающиеся на краях (tapered), постоянной ширины (even) и с отклонением факела (deflected)[2- 5].
В таблице 2.2 приводятся некоторые из часто встречающихся областей применения и типичные эксплуатационные параметры используемых форсунок.
Тип форсунки | Пневматическая форсунка | Гидравлическая с дроблением на мелкие капли | Гидравлическая с полным конусом | Гидравлическая с полым конусом | Гидравлическая с веерным факелом |
---|---|---|---|---|---|
Типичное давление воды | 69-413 кПа | 207-6895 кПа | 69-2069 кПа | 34-690 кПа | 69-3448 кПа |
Типичное давление воздуха | 69-483 кПа | - | - | - | - |
Улавливание пыли, попавшей в воздух | |||||
Щековые дробилки | + | + | + | ||
Места погрузки | + | + | |||
Первичные места хранения | + | + | |||
Места перегрузки | + | + | |||
Предотвращение попадания пыли в воздух | |||||
Перегружатели | + | + | |||
Места хранения | + | + | |||
Места перегрузки материала | + | + | + | ||
Дороги | + |
На Рис. 2.10 показано типичное использование распыления воды с целью предотвращения попадания пыли в воздух и улавливания витающей пыли в месте выгрузки материала. В процессе выгрузки пыль попадает в воздух и в верхней части укрытия, и при ударе падающего материала об уже лежащий. Форсунки для улавливания пыли, попавшей в воздух, устанавливаемые в верхней части укрытия, могут быть или пневматическими, или такими гидравлическими, которые дают мелкие капли воды (с полым конусом). А форсунки для предотвращения попадания пыли в воздух, устанавливаемые в нижней части укрытия, могут быть гидравлическими (так как они дают капли большего размера), например – с полным конусом, что позволить орошать большую площадь.
На Рис. 2.11 показано применение распыления воды для снижения запылённости при перемещении и сбросе материала с конвейера – как за счёт увлажнения, так и за счёт улавливания витающей пыли. В этом случае форсунки для увлажнения материала (для предотвращения попадания пыли в воздух) устанавливают над несущей стороной конвейера. А форсунки для улавливания пыли, попавшей в воздух, устанавливают в местах сброса и перегрузки.
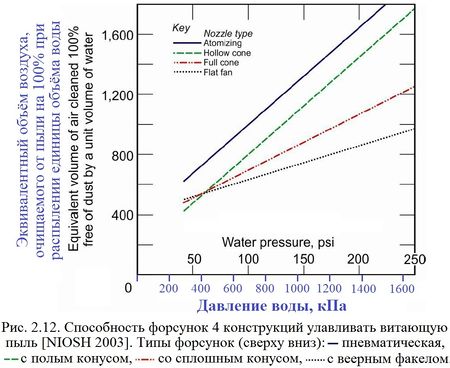
На Рис. 2.12 показано, насколько хорошо форсунки разных конструкций позволяют улавливать пыль при разных давлениях. Видно, что пневматические форсунки – самые эффективные, а следующие – гидравлические с полым конусом. При добыче и переработке полезных ископаемых форсунки с полым конусом будут самыми подходящими из-за того, что они охватывают большую площадь (при увлажнении), но не сильно увлажняют материал. Эти форсунки наиболее применимы на первых стадиях переработки материала, когда увеличение его влажности не так важно. Форсунки с веерным факелом лучше всего применять в ограниченном прямоугольном пространстве, так как это приводит к меньшей потере воды (которая при использовании форсунок с круглым факелом частично попадала бы на породу или на металлические поверхности, находящиеся рядом.
Техобслуживание оборудования, используемого для распыления воды[править]
Качество воды[править]
При борьбе с пылью с помощью распыления воды одним из важнейших обстоятельств является её качество. В первую очередь имеет значение наличие твёрдых загрязнений и её жёсткость. Если в имеющейся воде содержится много минеральных веществ, сопла будут ускоренно изнашиваться. В этом случае нудно рассмотреть возможность использования сопел из нержавеющей стали. Использование такой воды также может привести к засорению карбонатами, и увеличить расходы на техобслуживание. Хотя может оказаться невозможно изменить жёсткость используемой воды, но хорошо спланированная и проводимая программа обслуживания позволит свести к минимуму отрицательные последствия большого содержания минеральных веществ в воде.
Если сопла форсунок засоряются грязью или осадком, обеспыливающая система становится неэффективной. Так как при переработке полезных ископаемых в большинстве случаев воду для распыления берут из прудов-отстойников, то чистота воды имеет большое значение. Для предотвращения засорения форсунок осадком и грязью рекомендуется использовать системы фильтрации воды. Большинство компаний, продающих системы мокрого обеспыливания, также предлагают для них системы фильтрации воды.
Для эффективного снабжения системы мокрого обеспыливания водой рекомендуется использовать для этого отдельную специальную систему подачи воды. В такой системе питания есть насос, который подаёт требуемое количество воды при соответствующем давлении, фильтр на входе, выключатель (для предотвращения работы насоса без воды), манометр, ручной регулятор расхода воды, перекрывающий кран с ручным управлением, и панель управления (для включения вручную или по сигналам таймера). На Рис. 2.13 показана типичная система снабжения водой.
Системы подачи воды могут быть разной степени сложности – от простых, подающих постоянное количество воды, до более сложных, реагирующих на изменение условий работы изменением расхода подаваемой воды. Современные технологии позволяют определять параметры работы (концентрацию пыли и др.) и автоматически изменять расход и давление воды, подаваемой в форсунки для снижения запылённости.
В тех случаях, когда качество воды плохое, и когда в воде содержится много загрязнений (например – при использовании воды из прудов-отстойников), требуется дополнительная фильтрация. Для этих случаев рекомендуют использовать двойной сетчатый фильтр (duplex basket strainer). В таком фильтре есть две фильтрующие сетки (похожие по форме на корзинки), и переключаемый вручную клапан, позволяющий использовать для очистки воды какой-то один из фильтров – в то время, как другой проходит очистку. Сетка фильтра выбирается с учётом размеров частиц, загрязняющих воду. Сетка задерживает такие частицы, которые могут засорить сопло форсунки. Поэтому размер ячеек сетки должен быть меньше размеров таких частиц, которые больше отверстий в форсунке. На Рис. 2.14 показана типичная система с двойным фильтром.
![]() На Рис. 2.13 показана типичная система подачи воды для орошения[2- 10]. |
Техобслуживание форсунок[править]
Форсунки требуют техобслуживания, регулярных проверок, очистки, и даже замены для обеспечения качества конечного продукта, и обеспечения его производства с приемлемыми затратами. Периодичность и характер техобслуживания зависят от конкретных условий. В каких-то случаях форсунки могут продолжать нормально работать после сотен часов эксплуатации, в других требуют ежедневного обслуживания; а в большинстве случаев наблюдается что-то среднее. Как минимум, форсунки должны регулярно визуально осматриваться для обнаружения повреждения. Проведение дополнительного техобслуживания зависит от условий использования, качества воды и материала, из которого они изготовлены.
Разрушение и износ[править]
При постепенном истирании и уносе материала с поверхностей каналов форсунки диаметры последних с течением времени становятся больше и их форма нарушается (Рис. 2.15), что влияет на расход воды, давление и свойства факела.
![]() На Рис. 2.15 показан износ форсунок – старая (справа) и новая (слева)[2- 11] |
![]() На Рис. 2.16 показан результат коррозии форсунок – старая (справа) и новая (слева)[2- 11]. |
![]() На Рис. 2.17 показана новая форсунка (слева) и последствия отложения солей (справа)[2- 11]. |
Коррозия[править]
Химическое взаимодействие распыляемой жидкости или окружающей атмосферы и форсунки приводит к коррозии материала форсунки (Рис. 2.16).
Засорение[править]
Нежелательные загрязнения воды и другие взвешенные вещества могут отлагаться на стенках водяных каналов, сужая их, и нарушая равномерность распределения распыляемой воды.
![]() На Рис. 2.18 показан результат повреждения форсунки, вызванный перегревом[2- 12]. |
![]() На Рис. 2.19 показано повреждение сопел форсунок – новая (слева) и использованная, повреждённая из-за использования неподходящего инструмента при установке (справа)[2- 13]. |
Отложение растворённых веществ[править]
Отложение веществ, растворённых в воде (при её испарении) на внутренних стенках каналов форсунки создаёт слой твёрдых отложений и уменьшает отверстие для прохода жидкости (Рис. 2.17).
Повреждение при нагреве[править]
Нагрев может повредить детали форсунок, сделанные из материала, не предназначенного для применения при высокой температуре (Рис. 2.18).
Некачественная сборка[править]
Использование неровных прокладок, чрезмерная затяжка и другие недостатки сборки могут привести к утечкам, и нарушить нормальную работу системы распыления жидкости.
Случайное повреждение[править]
При установке и очистке может произойти непреднамеренное, случайное повреждение форсунки из-за использования неподходящего инструмента (Рис. 2.19).
Проверка работы форсунок[править]
Одного только визуального осмотра недостаточно для определения того, насколько хорошо работает форсунка. Наконечники сопел (на Рис. 2.18 и 2.19) показывают, что износ (который не всегда заметен) может влиять на работу форсунок.
Проверка работы оборудования[править]
Из-за ряда возможных проблем, необходимо регулярно проводить проверку работы систем распыления воды, и учитывать при этом ряд обстоятельств.
- Для оценки эффективности или при проведении измерений для конкретного случая использования газоочистного оборудования требуется или визуально оценивать концентрацию пыли в воздухе для определения эффективности распыления воды в отношении снижения запылённости, или проводить измерения концентрации пыли в воздухе. Под визуальным наблюдением имеется в виду просто осмотр места образования пыли для определения того, позволяет ли распыление воды обеспечить низкую запылённость. Так как это метод не позволяет количественно определить концентрацию пыли, субъективен и зависит от интерпретации наблюдателя, то он не позволяет точно определить эффективность работы оборудования. Разработаны и доступны приборы для измерения концентрации пыли, которые позволят более точно определить эффективность системы.
![]() На Рис. 2.20 показано распределение воды при её распылении форсункой (слева)[2- 11]. Высота столбцов гистограммы соответствует количеству воды (показано распределение воды по ширине факела - справа). Видно, что вода распределяется по ширине факела относительно равномерно. |
![]() На Рис. 2.21 показано распределение капель факела, образуемого изношенным соплом (слева)[2- 11]. Высота столбцов гистограммы соответствует количеству воды (показано распределение воды по ширине факела - справа). Видно, что износ сопла увеличивает долю воды, попадающей в центр. |
- Расход жидкости. Так как визуально определить увеличение расхода невозможно, то расход жидкости через каждую форсунку нужно определить или с помощью расходомера, или путём сбора распыляемой жидкости в ёмкость. Затем нужно сравнить результаты с паспортными техническими характеристиками форсунок, или с результатами измерений у новых форсунок.
- Давление жидкости. для определения давления жидкости в сопле форсунки нужно использовать подходящий и откалиброванный манометр.
- Равномерность распределения воды в факеле. Во многих случаях визуальное наблюдение позволяет (достаточно хорошо) оценить равномерность распределения воды в факеле. Изменения, вызванные износом или засорением, или отложением растворённых веществ, обычно заметные. Но для обнаружения постепенного износа сопла нужно использовать специальное оборудование. Для сравнения расходов воды у новой и старой форсунок при определённом одинаковом давлении может использоваться расходомер. Износ сопла приводит к увеличению расхода так, что показания расходомера позволяют количественно оценить износ.
- Направление факела форсунки. Для равномерного орошения вода должна распыляться в правильном направлении – по отношению друг к другу (так, чтобы оси факелов были параллельны).
.
ССЫЛКИ
- ↑ USBM [1987]. Dust control handbook for mineral processing.. Date accessed: December 13, 2008. U.S. Department of the Interior, Bureau of Mines. Contract No. J0235005. NTIS No. PB88–159108.
- ↑ 2,0 2,1 2,2 2,3 Blazek CF [2003]. The role of chemicals in controlling coal dust emissions. Presented at the American Coal Council PRB Coal Use: Risk Management Strategies and Tactics Course. Dearborn, Michigan, June 2003.
- ↑ Rocha E [2005a]. PowerPoint presentation slide # 30 presented by E. Rocha, General Manager, Spraying Systems do Brasil Ltda. Spray Technology Workshop for Pollution Control at Spraying Systems do Brasil Ltda, Sao Bernardo do Campo, Brazil.
- ↑ Rocha E [2005b]. PowerPoint presentation slide # 43 presented by E. Rocha, General Manager,Spraying Systems do Brasil Ltda. Spray Technology Workshop for Pollution Control at Spraying Systems do Brasil Ltda, Sao Bernardo do Campo, Brazil.
- ↑ 5,0 5,1 5,2 5,3 Bartell W, Jett B [2005]. The technology of spraying for dust suppression. Cement Americas, May/June pp. 32–37.
- ↑ NDT Educational Resource Center, Iowa State University. Ссылка. Date accessed: February 13, 2009.
- ↑ Swinderman RT, Goldbeck LJ, Marti AD [2002]. Foundations 3: the practical resource for total dust & material control. Neponset, Illinois: Martin Engineering Library.
- ↑ 8,0 8,1 NIOSH [2003]. Handbook for dust control in mining. By Kissell FN. Pittsburgh, PA: U.S. Department of Health and Human Services, Centers for Disease Control and Prevention, National Institute for Occupational Safety and Health, NIOSH Information Circular 9465, DHHS, (NIOSH) Publication No. 2003–147.
- ↑ Rocha E [2005c]. PowerPoint presentation slide # 75 presented by E. Rocha, General Manager, Spraying Systems do Brasil Ltda. Spray Technology Workshop for Pollution Control at Spraying Systems do Brasil Ltda, Sao Bernardo do Campo, Brazil.
- ↑ SSCO (Spraying Systems Co.) 2006. A guide to safe and effective tank cleaning. Ссылка.
- ↑ 11,0 11,1 11,2 11,3 11,4 Schick R [2006]. Spray technology reference guide—understanding drop size. Ссылка.
- ↑ SSCO (Spraying Systems Co. Catalog 70). Industrial spray products. Ссылка.
- ↑ SSCO (Spraying Systems Co.) 2003. Spray optimization handbook TM–410. Ссылка.
ГЛАВА 3. Бурение и взрывные работы[править]
Для проведения взрывных работ при добыче полезных ископаемых используют бурение – и на поверхности, и в шахтах. Отличия в условиях проведения буровых работ приводят к некоторым отличиям технологии их выполнения. Давно и хорошо известно, что бурение является причиной загрязнения воздуха респирабельной пылью, которая может оказывать сильное негативное воздействие и на операторов буровой установки, подсобных рабочих, и других людей, находящихся поблизости. Поэтому при бурении требуется принимать меры для уменьшения концентрации пыли, и для этого могут использоваться сухие и мокрые способы.
Для защиты операторов буровых установок от респирабельной пыли, образующейся при бурении, всё чаще используют герметичные кабины с подачей отфильтрованного воздуха. Это более подробно обсуждается в главе 9 “Кабины операторов, пульты управления и кабины мобильного оборудования”. Использование “искусственной” атмосферы в кабине для защиты оператора от загрязнённой атмосферы очень эффективно. Но защита обеспечивается лишь до тех пор, пока люди находятся в кабине, и только для этих сотрудников. Это не позволяет защитить других людей, работающих вблизи буровой установки (подсобных рабочих, взрывников (shotfirer), слесарей и др. Они могут попробовать защититься от респирабельной пыли за счёт перемещения на ту сторону, с которой ветер дует на источник пыли, но это не всегда выполнимо на практике. Поэтому сохраняется потребность в уменьшении концентрации пыли около буровой установки.
Для этого используют два основных способа: или мокрое пылеподавление, или использование циклона и тканевого фильтра (сухой способ). При использовании мокрого способа вода подаётся (распыляется) в воздух, поступающий в полый стержень бура, и при обратном движении между стенками пробуренной скважины и буровой колонной она улавливает пыль. При использовании сухого способа в месте входа бура в землю/ размещается укрытие, и запылённый воздух отсасывается из-под укрытия в пылеуловитель. После очистки воздух выбрасывается в атмосферу. При эффективном использовании и мокрого, и сухого способа снижения запылённости, можно добиться низкой концентрации пыли на рабочих местах.
В этой главе сделан обзор эффективных методов снижения запылённости при бурении и на поверхности, и под землей. За последнее столетие было проведено много исследований методов снижения запылённости. Исследования проводилось в 1920-1950г - тогда Горное Бюро (U.S. Bureau of Mines) проводило программу по предотвращению силикоза среди шахтёров. Хотя те исследования могут казаться сейчас устаревшими, принципы (снижения запылённости) сохранились, применяются сейчас и эффективны. Кроме того, многие из результатов, полученных для подземного бурения, стали использоваться при бурении на поверхности. Исследования снижения запылённости при бурении на поверхности началось в ~ 1980г, когда было признано, что у операторов поверхностных буровых установок чаще развивается силикоз. Для разработки новых методов снижения запылённости при бурении и на поверхности, и под землёй продолжают проводиться новые исследования.
Снижение запылённости при бурении на поверхности[править]
Для бурения скважин на поверхности используется как вращающийся, так и ударный метод. При использовании вращающегося способа разрушение породы происходит под действием сильного давления вращающегося сверла, прикреплённого к концу колонны буровых труб. При ударном бурении разрушение породы происходит за счёт давления и вращения, но с использованием сжатого воздуха, который действует на поршень отбойного молотка, который ударяет по наконечнику или по колонне буровых труб. Эти удары делают ненужным большое давление, используемое при вращательном бурении.
Типичный диаметр скважины достигает 38 см (15 дюймов). Скважины большого диаметра обычно получают вращательным бурением. Обычно такие скважины вертикальные, хотя иногда используют и наклонные, а для проведения взрывных работ скважины могут бурить так, чтобы они располагались в ряд, ровно. Для бурения может использоваться различное оборудование – от маленьких буровых установок на шасси трактора, до больших на гусеничном ходу (Рис. 3.1).
Для снижения запылённости на поверхности используют или мокрый, или сухой способ. В зависимости от условий работы и применяемого оборудования эти методы могут использоваться в разных вариантах. Но общие принципы снижения запылённости, описанные в этой главе, применимы для всех случаев бурения на поверхности, включая использование маленьких буровых установок на гусеничном ходу; буровых установок (“среднего” размера), размещённых на тракторах; и больших установок на гусеничном ходу.
Мокрое бурение[править]
При бурении на поверхности лучший способ уменьшить запылённость – мокрое бурение. При таком способе вода подаётся в воздух, движущийся внутри полого сверла, и затем выходит наружу между сверлом и стенками скважины, улавливая пыль (Рис. 3.2). Измерения показали, что это позволяет снизить концентрацию пыли на 96%[3- 1].
Для эффективного снижения запылённости нужно, чтобы оператор следил за подачей воды. Расход воды при этом способе небольшой – обычно 0.4÷7.6 л/мин (0.1÷2.0 gpm), но он зависит от типа сверла, геологических условий и уровня влажности разрушаемого материала. Например, измерения (проводившиеся при бурении на поверхности) показали, что при увеличении расхода воды с 0.8 до 2.4 л/мин происходит значительное снижение запылённости. Но после того, как в том конкретном случае проведения измерений, расход достиг 3.8 л/мин, возникли новые проблемы: наконечник сверла стал засоряться, и сверло стало трудно вращать из-за того, что мокрый разрушенный материал стал слишком тяжёлым для выдувания из скважины, и стал засорять пространство между сверлом и стенками скважины[3- 1]. Таким образом, подача слишком большого количества воды создаёт дополнительные проблемы. Расход воды, которую нужно подавать, зависит от типа сверла и от свойств разрушаемого материала.
Для снижения запылённости мокрым способом на шасси устанавливают бак с водой, откуда она подаётся в воздух, идущий в полом стержне бура для удаления частиц разрушенной породы из скважины. Капли воды улавливают частицы пыли, и они вместе выходят из скважины в пространстве между её стенками и буровой колонной. Это приводит к снижению запылённости рядом с местом проведения буровых работ. Подача воды контролируется оператором буровой установки из кабины, и в некоторых кабинах ставят расходомер для определения расхода воды.
Преимущества бурения мокрым способом
Потенциальным преимуществом использования воды для уменьшения запылённости может быть (помимо лучшего улавливания пыли) увеличение скорости бурения (при бурении на поверхности). (Но) информации о том, как влияет подача воды на скорость бурения – очень мало, и известно, что использование воды при подземном бурении в шахтах может повысить скорость бурения[3- 2][3- 3]. Так как это происходит при подземном бурении, это может проявляться и при бурении на поверхности. Требуется дополнительная проверка, чтобы можно было окончательно определить, может ли мокрое бурение увеличить скорость бурения на поверхности.
Рекомендации при использовании мокрого бурения
На основе результатов измерений и наблюдений за лучшим применением мокрого бурения, разработаны следующие рекомендации по его применению:
- Чтобы расход воды был близок к максимальному, оператор должен плавно увеличивать подачу воды до тех пор, пока не перестанет наблюдаться визуально заметный выброс пыли. Увеличение подачи воды выше этого количества не приведёт к сколько-нибудь значительному уменьшению запылённости, но скорее всего создаст эксплуатационные проблемы – ускоренное разрушение наконечника сверла (при использовании трёхшарошечного долота), возможное “заедание” сверла. А подача меньшего количества воды уменьшит эффективность пылеподавления.
- Важно увеличивать подачу воды постепенно, и с задержкой по времени (на тот период, который требуется для подъёма смеси воды и воздуха из скважины до поверхности).
- При бурении нужно непрерывно следить за расходом воды, чтобы её подача была оптимальной для снижения запылённости и чтобы не произошло засорения пространства между сверлом и скважиной.
- Используемая вода должно фильтроваться, чтобы грязь, содержащаяся в воде, не засорила систему мокрого пылеподавления при.
- При работе при температуре воздуха, меньшей 0°С, во время бурения система должна подогреваться, а при (длительных) перерывах вода должна сливаться. В большинстве буровых установок расположение ёмкости с водой вблизи двигателя и гидравлической системы оказывается достаточно для того, чтобы предотвратить замерзание во время работы – за исключением очень низкой температуры воздуха. Когда бурение не проводится, вода должна сливаться и из бака, и из водопроводных труб установки.
Недостатки мокрого бурения
Если при ударном бурении у этого способа есть преимущества, то при использовании вращательного бурения проявляются его недостатки. Подача воды ускорят износ трёхшарошечного долота, и уменьшает его срок службы в 2 раза и более[3- 4]. Это происходит из-за быстрого разрушения материала (подшипника / bearing), из-за водородного охрупчивания, и из-за ускоренного истирания наконечника. Истирание наконечника вызвано работой в условиях абразивной среды – смеси разрушенной породы и воды.
Для решения проблемы сокращения срока службы при мокром бурении можно подавать воду так, что она не дойдёт до наконечника. Для этого оптимизируют подачу воды, и используют сепарацию. По данным Горного Бюро (Bureau of Mines, BOM) при бурении в монцоните, песчанике, известняке и железной руде (данные собирали 14 лет) замена наконечников буров проводилась в среднем через 591 метр (без сепарации воды), а при сепарации срок службы возрастал примерно в 4.5 раз и замена в среднем проводилась через ~ 2 743 м[3- 5].
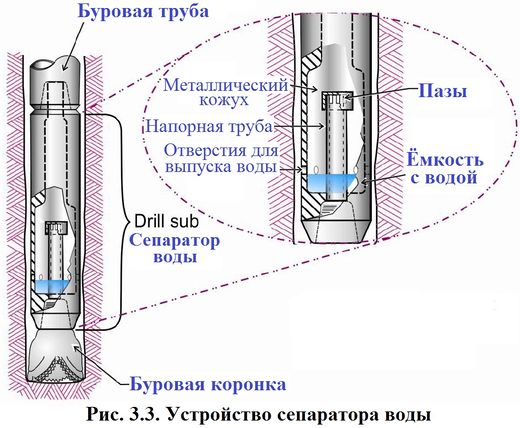
Сепаратор воды
Для отделения воды используется специальное приспособление (water separation sub). Для удаления подаваемой воды из воздуха, закачиваемого для извлечения из скважины разрушенного при бурении материала, в нём используется инерция. Для отделения воды между наконечником и колонной буровых труб устанавливают “воротник” (collar assembly), у которого с обоих сторон есть резьба, позволяющая присоединить его и к трубам, и к наконечнику. Обычно у этого приспособления есть “стабилизатор” – кольца на наружной стороне, которые используются для обеспечения положения бура по оси скважины.
Для отделения воды подаваемый воздух принуждают совершить резкий поворот немного выше буровой коронки (см. Рис. 3.3). Смесь воды и воздуха проходит через центр буровых труб, опускается ниже напорной трубы (standpipe), и разворачивается на 180º около ёмкости с водой. Затем воздух двигается вверх вне напорной трубы, проходит в напорную трубу через пазы, и разворачивается вниз, двигаясь внутри напорной трубы. Затем воздух выходит через сопла на буровой коронке. Из-за того, что масса и инерция у воды больше, чем у воздуха, она не может развернуться – как воздух – и отделяется от него. Так как внутри буровых труб избыточное давление воздуха, то вода выходит наружу через отверстия для выпуска воды. Эти отверстия находятся по периметру сепаратора выше буровой коронки. Вода попадает в кольцевое пространство между стенками скважины и буровыми трубами. Все сдуваемые воздухом кусочки разрушенной породы поднимаются вверх и проходят через это же кольцевое пространство, где увлажняются. Это не позволяет воде попасть на буровую коронку, и предотвращает образование смеси жидкости и разрушенной породы в месте разрушения последней.
Испытания показали, что при использовании сепаратора улавливается до 98% пыли, а без него – до 96%[3- 4]. Более важно то, что увеличивается срок службы буровых коронок.
Сухое бурение[править]
При сухом бурении снижение запылённости происходит без использования воды. Для улавливания пыли используют оборудование, находящееся на буровой установке снаружи скважины. Такое оборудование может работать в разных климатических условиях, и оно не замерзает при низкой температуре. Снижение концентрации пыли может достигать 99% при исправном состоянии и правильном использовании[3- 1]. Конструкция пылеулавливающего оборудования может быть разной, и она зависит от размера буровой установки.
Пылеулавливающие установки для бурового оборудования среднего и большого размера.
На Рис. 3.4 показана типичная сухая пылеулавливающая система, используемая при бурении скважин большого и среднего диаметра. Пыль попадает в воздух при продувке скважины сжатым воздухом (для удаления разрушенной породы), который подаётся через полые буровые трубы к буровой коронке (на Рис. 3.2 показано схожее изображение, но там добавляется вода). При нормальной работе разрушенная порода и пыль попадают в укрытие, которое закрывает место входа буровых труб в породу. А запылённый воздух удаляется из укрытия отсасывается и направляется в пылеуловитель. Вентиляционная система включает в себя вентилятор и тканевый фильтр, регенерация ткани в котором обычно осуществляется импульсной продувкой сжатым воздухом через определённые интервалы времени. При этом уловленная пыль сбрасывается в бункер пылеуловителя.
Источники пыли в пылеулавливающей системе
Если в пылеуловителе повреждены, или отсутствуют некоторые из тканевых фильтров (рукавов и т.п.), то это приводит к (значительному) выбросу пыли из пылеуловителя. Другие источники пыли – повреждённое или изношенное укрытие места входа буровых труб в породу, или условия работы, мешающие укрытию удерживать выходящий из скважины запылённый воздух.
У больших и средних буровых установок большое значение имеет целостность “юбки” (гибкого ограждения платформы буровой установки) и её плотное прижатие к земле. Более половины пыли, попадающей в воздух при работе буровой установки, выходит из-под ограждения укрытия и через отверстие в платформе, через которое движутся буровые трубы[3- 6]. Если между ограждением и землёй есть зазоры или щели размером более 15 см (6 дюймов), эффективность улавливания пыли значительно снизится[3- 7][3- 8]. При сухом бурении выявлено три (основных) источника пыли:
- Утечки через ограждение,
- Образование пыли при её выгрузке из пылеуловителя, и
- Утечки через отверстие в буровой платформе, через которое движутся буровые трубы.
Предотвращение утечек из укрытия
За исключением тяжёлых карьерных буровых установок на гусеничном ходу (air track drills), у большинства буровых установок схожая конструкция, и схожий расход отсасываемого воздуха. Единственным отличием является площадь зазоров, через которые может происходить утечка пыли, и это заметно влияет на эффективность пылеулавливающей системы. Чаще всего зазоры образуются между нижней частью ограждения и землёй – из-за неровного или наклонного положения буровой платформы, и по углам буровой платформы.
Прямоугольное ограждение.
У некоторых ограждений есть зазоры по углам на передней стороне ограждения, которое может подниматься гидравлическими цилиндрами для предотвращения вытаскивания разрушенной породы в отверстие в буровой платформе при подъёме буровой колонны. Так как большинство ограждений буровых платформ – прямоугольной формы, и сделаны из четырёх отдельных резиновых частей, прикреплённых к буровой платформе, просачивание запылённого воздуха наружу может произойти при образовании зазоров между частями ограждения. Для предотвращения этого добавляют угловые щитки, прикреплённые к кронштейнам, которые помогают сохранить герметичность укрытия (см. Рис. 3.5), или ограждение делают из одного куска материала (прорезиненной ленты) так, чтобы оно охватывало платформу по периметру.
Круглое ограждение
При сухом бурении иногда используют круглое ограждение буровой платформы – для улучшения изоляции источника пыли от окружающей атмосферы. Круглое ограждение не цилиндрическое, а немного коническое по форме, и у него нет открытых зазоров (как у прямоугольного – между отдельными листами). Для его крепления к нижней части буровой платформы используется стальная лента. Такое ограждение может подниматься и опускаться с помощью гидравлического привода. Для придания нижней части ограждения круглой формы и для прижатия его к земле внизу также крепится стальная круглая лента. К этой тяжёлой ленте крепятся тросики, ведущие к гидроцилиндрам для подъёма ограждения (см. Рис. 3.6). Чтобы ограждение было гибким, его делают из тонкого листа резины, и в ограждении делают маленькое отверстие для доступа, позволяющее выгружать лопатой разрушенную породу – без ухудшения изоляции источника пыли.
При бурении скважины может образовываться много разрушенной породы, и из-за этого может потребоваться поднимать круглое ограждение для предотвращения ссыпания разрушенной породы обратно в скважину. Поэтому иногда нельзя избежать образования зазоров между ограждением и землёй, или разрушенной породой. Нужно, чтобы оператор буровой установки понимал, и старался уменьшить зазоры до минимума. Для этого может потребоваться часто визуально проверять – в каком состоянии находится пространство под платформой, для чего (приходится) поднимается ограждение.
Отношение расходов воздуха – подаваемого для продувки скважины, и отсасываемого для улавливания пыли
Для эффективного снижения запылённости сухим способом нужно определённое соотношение между расходами воздуха: сжатого, подаваемого для уноса разрушенного материала из скважины, и отсасываемого пылеуловителем. Это отношение расходов обозначают QC/QB, и практика показала, что оно является важным индикатором эффективности системы обеспыливания. Расход воздуха пылеуловителя (QC) м3/час (standard cubic feet per minute, scfm) – расход воздуха у вентилятора пылеулавливающей системы, которая всасывает запылённый воздух из-под ограждения буровой платформы. А расход продувочного воздуха (bailing airflow, QB), м3/час (scfm) – расход сжатого воздуха, подаваемого в скважину к буровой коронке для удаления разрушенной породы из скважины.
Расход продувочного воздуха QB можно узнать у изготовителей бурового оборудования (это расход воздуха у компрессора буровой установки), а для измерения расхода воздуха пылеулавливающей системы лучше использовать анемометр с нагретой проволокой, или с крыльчаткой, или трубку Пито (в месте выхода воздуха из вентилятора пылеулавливающей системы). Для более точных измерений к месту выхода воздуха из пылеулавливающей системы можно прикрепить короткую (~1.2 м 4-foot) трубу, и поместить в неё анемометр – в середине трубы. Такую трубу нетрудно сделать из картона и присоединить её к выходному отверстию вентиляционной системы. Результат измерений можно привести к стандартным атмосферным условиям, но это не обязательно, так как коррекция на внешние условия обычно даёт небольшое изменение. Кроме того, расход воздуха через тканевый фильтр зависит от количества накопившейся пыли, и потому непостоянен – так, что это непостоянство заметно больше, чем поправка на отличие от стандартных атмосферных условий.
Обычно отношение расходов отсасываемого воздуха к подаваемому сжатому составляет до 3:1. Но при работе фильтров при обычной запылённости чаще всего встречается отношение 2:1[3- 9]. Оказалось, что у плохо работающих систем обеспыливания отношение расходов составляет 1:1 и меньше. Измерения показали, что при увеличении отношения расходов вынос пыли через зазоры между ограждением и землёй значительно уменьшается[3- 10][3- 11]. На Рис. 3.7 показано влияние изменения отношения расходов при разном размере зазоров на концентрацию пыли, мг/м3. Как видно, наибольшее снижение концентрации пыли получается при увеличении отношения расходов с 2:1 до 3:1, а при увеличении до 4:1 концентрация пыли становится ещё ниже.
Обеспечение оптимального отношения расходов воздуха для снижения запылённости
Для предотвращения выбросов пыли необходимо обеспечить оптимальное отношение расходов воздуха – отсасываемого вентиляционной системой и сжатого, подаваемого для удаления разрушенной породы. Расход воздуха компрессора – это максимальный расход, и обычно он слабо изменяется с течением времени при эксплуатации буровой установки. Поэтому влияние (его изменения) на отношение расходов незначительно (по сравнению с влиянием непостоянства расхода отсасываемого воздуха). Проведение обычного техобслуживания компрессора, как того требует руководство по его эксплуатации, позволяет поддерживать расход сжатого воздуха в рабочем диапазоне.
А расход воздуха пылеуловителя влияет на отношение расходов сильнее, так как на изменение этого расхода влияет много факторов. Расход воздуха у пылеуловителя с течением времени может снизиться из-за повреждения составных частей системы и недостаточно хорошего техобслуживания. При техобслуживании оператор должен:
- Проверить, что обратная продувка фильтров работает нормально, и что её параметры соответствуют паспортным.
- Проверить, что воздуховоды герметично присоединены, и что в них нет отверстий.
- Заменять фильтры – или при повреждении, или через рекомендуемые периоды.
- Проверить, что воздуховоды и входное отверстие пылеуловителя – свободны, не загорожены.
- Проверить, что вентилятор пылеуловителя нормально работает, и частота вращения соответствует паспортной.
Использование отношения расходов воздуха для снижения запылённости
Знание отношения расходов воздуха позволяет предсказать степень загрязнённости воздуха при работе буровой установки, и оценить возможное снижение концентрации пыли путём измерения нескольких основных параметров бурения скважины. Требуемыми параметрами являются: расход воздуха пылеуловителя QC, расход сжатого продувочного воздуха QB, площадь поперечного сечения ограждения буровой платформы AS, и площадь зазоров AL, или приближённая оценка этой площади[3- 12][3- 13].
Показанная на Рис. 3.8 модель (вверху) иллюстрирует относительное снижение, которое можно получить при уменьшении площади зазоров[3- 12][3- 13]. Чтобы показать, как использовать график, ниже приводится пример.
Оператор работает на буровой установке, размер платформы которой 1.2 на 1.5 м (4×5 feet). Паспортный расход воздуха компрессора QB 122.7 л/сек (260 scfm), а измеренный расход воздуха у пылеуловителя QC 250 л/сек (530 scfm). Это соответствует отношению расходов QC/QB ≈ 2. Площадь поперечного сечения укрытия вычисляется как произведение длины платформы на её ширину – 1.86 м2 (20 ft2). Площадь зазоров AL вычисляется умножением высоты зазора (LH) на длину периметра ограждения, что даёт AL = LH x 5.5 м (LH x 18 ft). Таким образом, отношение AS / AL = 1.86/(5.5×LH) {20 ft /(LH x 5.518 ft)}, и можно оценить отношение площадей с помощью LH.
Так как отношение расходов QC/QB = 2, то можно использовать верхние графики с Рис. 3.8 для определения влияния уменьшения зазоров на запылённость. При зазоре 36 см (14 inches) отношение площадей AS/AL = 0.95, что соответствует концентрации респирабельной пыли около 16 мг/м3, а при зазоре 5 см (2 inches) отношение площадей AS/AL = 6.7, и концентрация респирабельной пыли около 5 мг/м3. Этот пример показывает, что уменьшение зазоров уменьшает концентрацию респирабельной пыли.
Нужно отметить, что при оценке площади зазоров в неё нужно включать и вертикальные зазоры между листами ограждения, но во многих случаях такие зазоры могут быть незначительными. Графики для отношения расходов QC/QB > 2 схожи с показанными. Но концентрация респирабельной пыли при любом значении отношения AS/AL будет меньше, так как отношение расходов воздуха QC/QB возросло[3- 12]. Это видно из сравнения двух графиков на Рис. 3.8.
Важно не забывать, что вычисленное значение концентрации респирабельной пыли – это всего лишь относительное значение, и (эта величина) не так важна, как отношение площадей AS/AL. Важно определить, к какому участку графика относится режим работы буровой установки (это зависит от отношения площадей AS/AL), и какой из графиков нужно использовать (то есть – значение QC). Эти сведения позволят определить, какое (среднее) долговременное улучшение можно получить, если увеличить расход воздуха у пылеуловителя (например – за счёт установки чистых фильтров, или установки пылеуловителя большего размера), или если уменьшить зазоры.
Например, у буровой установки, режим работы которой попадает на левую сторону графиков на Рис. 3.8 можно значительно снизить запылённость. Если режим работы буровой установки попадает на правую сторону графиков, то достижимое уменьшение запылённости будет небольшим. Но то, что режим работы соответствует этой части графиков показывает, что работа буровая установка ведётся при эффективном снижении запылённости[3- 13]. Как уже упоминалось, при загрязнённых фильтрах и обычных производственных условиях отношение расходов QB примерно равно 2. Поэтому при бурении скважин на поверхности нужно стараться обеспечивать отношение расходов не ниже 2, и желательно увеличить его до 3 и более.
Полки для изменения движения воздуха Air-Blocking Shelf
При бурении поверхностных скважин большого и среднего размера с помощью буровых установок на гусеничном ходу оказалось, что можно эффективно уменьшить запылённость воздуха с помощью горизонтальных полок, влияющих на движение воздуха в укрытии. Использование таких полок может позволить снизить запылённости у любой большой буровой установки, у которой минимальный размер укрытия не меньше 1.2 на 1.2 м (4×4 feet). Полки шириной 15 см (6 inch) устанавливают в укрытии по периметру ограждения. Они предназначены для уменьшения выноса пыли из укрытия во время работы буровой установки. Разработка этого средства снижения запылённости проводилась на основе наблюдений за характером движения воздуха в укрытии испытательной буровой установки[3- 14][3- 15].
При бурении и использовании обычного укрытия воздух движется в нём так, как показано на Рис. 3.9 слева, и он определяется движением продувочного воздуха и влиянием вытяжки. Продувочный воздух движется (вверх) от отверстия скважины через среднюю часть укрытия (на уровне полок), сохраняя направление движения вдоль буровой трубы к нижней поверхности буровой платформы. У нижней поверхности буровой платформы за счёт эффекта Коанда (струя текущей жидкости или газа склонны “прилипать” к поверхности, с которой они встретились). Струя загрязнённого воздуха выходит из скважины, движется вверх до площадки буровой платформы, расходится в стороны веером по нижней стороне площадки буровой платформы, и по достижении её краёв движется вниз вдоль стенок ограждения. Всё это движение происходит при большой скорости. Вынос пыли из укрытия в месте его контакта с землёй происходит при столкновении потока воздуха с ней и последующего вытекания из укрытия через зазор между ограждением и землёй.
Полка шириной 15 см (6 inch), установленная по периметру ограждения, нарушает (описанный выше) характер движения воздуха. Она перенаправляет поток воздуха к центру укрытия так, что поток загрязнённого воздухе не сталкивается с землёй (Рис. 3.9, справа). Такое изменение направления движения загрязнённого воздуха уменьшает его вытекание из-под укрытия наружу[3- 14][3- 15].
На Рис. 3.10 показаны полки, установленные на буровой установке при проведении испытаний. Полки сделали из 15-см конвейерной ленты, и закрепили болтами на металлических уголках размером 5 см. Эти уголки были прикреплены болтами к ограждению укрытия по его периметру. Для полной герметизации внутреннего пространства была добавлена дверца (кусок резины), закрывавшая отверстие для доступа к внутреннему пространству извне (дверца не показана). Полки установили примерно посередине (по вертикали) между верхом укрытия и землёй. Лабораторные эксперименты показали, что установка отдельных полок на каждой из сторон укрытия на разной высоте – не эффективна. Поэтому нужно устанавливать полки так, чтобы между ними не было зазоров по углям. Трудозатраты на установку полок: два человека делают эту работу менее чем за час[3- 14].
Такие отклоняющие поток полки не требуют техобслуживания после установки – если они не повредятся при перемещении буровой от одного места работы к другому. Измерения в производственных условиях во время работы буровой установки (бурившей скважины для закладки взрывчатых веществ) показали, что при их использовании концентрация пыли уменьшается на 66–81%[3- 16] – в зависимости от направления ветра и свойств грунта. Но нужно отметить, что при очень низкой концентрации пыли (<0.5 мг/м3), (относительный) эффект от использования полок уменьшается. Это объясняется влиянием большого числа других источников пыли (пылеуловителя, утечки через отверстие в платформе, через которое проходят буровые трубы, из-за пыли, создаваемой при выполнении других работ), которые начинают влиять на концентрацию в большей степени[3- 16].
При использовании таких полок оказалось, что пыль может скапливаться на их верхней поверхности (Рис. 3.11, слева). Из-за падения с них накапливающейся пыли её концентрация может быть значительно выше (Рис. 3.11, справа). Вынос пыли из укрытия при высыпании из него разрушенной породы происходит и при отсутствии полки. Поэтому использование полок не создаёт новую проблему, но может усугубить уже имеющуюся. Для преодоления этого недостатка полки можно устанавливать под углом 45° и их изготавливают из другого материала (Рис. 3.12).
При установки полки под углом 45° нужно увеличить ширину полки с 15 до 20 см (6 to 8 inches) для сохранения эквивалентной ширины по горизонтали 15 см (6 inch). Полки должны быть сделаны из полиэтилена высокой плотности HDPE толщиной 6 мм (1/4 inch). Этот материал имеет скользкую поверхность, что уменьшает прилипание пыли к поверхности полок. Он продаётся в виде пластин размером 1.2×2.4 м (4×8 foot), из которых можно вырезать куски необходимого размера. Описанная модификация устраняет риск накопления пыли на полках. Также можно уменьшить размер секций полок для предотвращения их возможного повреждения при перемещениях буровой установки с места на место; и использовать дополнительные цепи (подвески) для предотвращения искривления. При использовании коротких секций важно, чтобы они перекрывали друга для предотвращения просачивания, снижающего эффективность полок.
Выгрузка уловленной пыли
Выгрузка уловленной пыли (из пылеуловителя) даёт до 40% от всей запылённости (по респирабельной пыли)[3- 6]. Выгрузка уловленной пыли может проводиться двумя способами: периодически через заданные интервалы времени; и при остановках в работе (trickle or batch mode). В первом случае механизм выгрузки может включаться через определённые интервалы времени (например – 1 раз в минуту), что позволит выгружать уловленную пыль на землю. Во втором случае выгрузка происходит в те моменты времени, когда сжатый воздух для продувки скважины не подаётся, например – при вынимании буровой колонны из скважины, или при наращивании буровых труб. Во втором случае запылённость выше, так как интервалы времени, в течение которых накапливается мелкодисперсный материал перед выгрузкой - больше. При сбросе мелкодисперсного материала пыль обычно попадает в воздух. При столкновении этого материала с землёй также наблюдается сильное пылеобразование. Наконец, сама буровая установка и другие машины нередко ездят по кучам выгруженной пыли, поднимая её в воздух. Для предотвращения вторичного попадания пыли в воздух нужно избегать воздействий на кучи выгруженной пыли.
Предотвращение уноса пыли при её выгрузке
Место выгрузки пыли из пылеуловителя обычно находится на 60÷90 см (24÷36 inches) платформы буровой установки. Сброс пыли с такой высоты приводит к попаданию респирабельной пыли в воздух. Для уменьшения вторичного попадания пыли в воздух, и для снижения концентрации респирабельной пыли в месте её выгрузки из пылеуловителя, к месту выгрузки можно присоединить завесу из ткани, используя большой хомут для рукавов. На Рис. 3.13 A, B и C показана установка такого ограждения. Такое ограждение можно установить поверх имеющегося резинового.
Установка такого простого ограждения на практике оказалась очень эффективным методом уменьшения концентрации респирабельной пыли. Измеренная концентрация респирабельной пыли после установки ограждения была в диапазоне 0.16-0.24 мг/м3. На Рис. 3.14 показано уменьшение концентрации респирабельной пыли около места её выгрузки при наличии ограждения и без него. Видно, что установка ограждения снижает концентрацию респирабельной пыли в месте её выгрузки на 63÷88 %[3- 17]. Нужно отметить, что снижение концентрации сильно зависит от направления и скорости ветра. Достоинство этого метода в том, что материал недорогой, и техобслуживание практически не требуется. Если ограждение будет повреждено, его легко можно заменить, прервав работу буровой установки на 1÷15 минут, или вообще без перерыва.
При установке ограждения его длину нужно выбирать так, чтобы её хватало от места выгрузки пыли до земли. Оно должно быть обрезано так, чтобы оно лишь касалось земли при опускании буровой установки. При оборачивании того материала, который используется для создания укрытия, в месте выгрузки пыли, нужно чтобы он размещался с перекрытием (см. Рис. 3.13 C). Перекрытие позволяет ткани (укрытию) расширяться при сбросе мелкодисперсной пыли на землю, что улучшает удержание респирабельной пыли в укрытии. Наличие такого ограждения также предотвращает попадание уловленной пыли на гусеницы буровой установки, что могло бы привести к попаданию респирабельной пыли в воздух при движении установки.
Борьба с просачиванием пыли через отверстие в буровой платформе
Оператор буровой установки и другие люди, находящиеся поблизости, могут подвергаться сильному воздействию пыли, просочившейся через отверстие в буровой платформе, используемое для подачи буровых труб в скважину. Когда отверстие новое, не изношенное, оно обычно предотвращает попадание разрушенной породы на верхнюю поверхность буровой платформы. Но по мере износа между платформой и буровыми трубами образуется зазор, и это позволяет пыли и разрушенной породе проходить через отверстие.
Предотвращение просачивания между буровой колонной и отверстием в буровой платформе
Чтобы свести к минимуму этот источник пыли, многие изготовители бурового оборудования устанавливают резиновые листы (обычно используют куски конвейерного транспортёра) ниже буровой платформы, закрывая место выноса пыли через отверстие в платформе. В листах делают отверстие, чтобы пропустить буровые трубы. Листы изнашиваются и повреждаются, и через некоторое время выбросы пыли через отверстие возобновляются. На Рис. 3.10 показаны эти резиновые листы, размещённые в месте, где буровые трубы проходят через буровую платформу.
Изобретение Air Ring Seal (AIRRS) предназначено для решения этой проблемы. AIRRS – не механическое уплотнение, оно не требует практически никакого техобслуживания. Оно состоит из полого тела торообразной формы, которое охватывает буровые трубы в месте их прохождения через отверстие в платформе, и в котором есть много близко расположенных отверстий (см. Рис. 3.15) с внутренней стороны[3- 4]. При подаче в AIRRS сжатого воздуха он начинает вытекать через отверстия с внутренней струйкам - с большой скоростью. Эти струйки направлены поперёк отверстия для предотвращения перемещения частиц пыли через отверстие.
Устройство AIRRS устанавливается ниже платформы буровой установки в том месте, где буровые трубы проходят через платформу – так, что трубы попадают в отверстие в торообразном корпусе AIRRS. Диаметр устройства должен быть настолько мал, насколько это возможно, но чтобы при этом сохранялся зазор между буровыми трубами и корпусом, чтобы свести к минимуму риск повреждения при поднимании буровых труб. Также очень важно, чтобы отношение расходов воздуха (сжатого и пылеуловителя) было не меньше 2, иначе при использовании устройства AIRRS будет большая утечка пыли из укрытия.
При бурении скважин на поверхности это устройство успешно и значительно снижает концентрацию респирабельной пыли, и также помогает поддерживать в чистоте платформу буровой установки[3- 4]. Установка устройства AIRRS позволяет устранить визуально заметный выброс пыли через отверстие и вынос частиц разрушенной породы. Количество воздуха, подаваемого в устройство, ограничивается производительностью компрессора буровой установки. При давлении воздуха 207 кПа (30 psi) и диаметре отверстий ~1.59 мм (1/16-inch) устройство AIRRS успешно снижает вынос пыли из укрытия[3- 4]. Но количество (подаваемого) воздуха сильно зависит от конструкции буровой установки.
Для уменьшения выноса пыли через отверстие помимо устройства AIRRS также устанавливают втулки (у которых небольшой зазор между буровыми трубами и их корпусом). Это уменьшает размер зазоров и вынос разрушенного материала. Замена втулок по мере необходимости также улучшает работу пневматического кольцевого уплотнения.
Пылеуловители небольших буровых установок
На Рис. 3.16 показаны пылеуловители буровых установок от маленького до среднего размера. Схема иллюстрирует работу таких систем. Эти системы (маленьких буровых установок) отличаются от пылеулавливающих систем больших буровых установок тем, что они улавливают/всасывают все частицы разрушенного материала, направляют их в циклон на стреле буровой установки (который отделяет крупные частицы), и затем направляет остальные частицы в пылеуловитель, который находится сзади буровой установки, где улавливается мелкая пыль.
Для эффективного уменьшения концентрации пыли большое значение имеет техобслуживание пылеуловителей. При его проведении должно решаться два важных вопроса:
- Фильтры должны заменяться до того, как их материал засорится, и
- При плохом обслуживании ограждения и уплотнения отверстия в буровой платформе они станут источниками большого количества пыли (как было показано, утечки через отверстие и в месте крепления ограждения даже более опасны, чем утечки в месте касания укрытия и земли)[3- 18].
В таких буровых установках для уменьшения пылеобразования могут использоваться и мокрые способы. Тогда в состав пылеулавливающей системы входит ёмкость с водой или смесью, которые впрыскиваются в в главный и дополнительный пылеуловители для уменьшения выноса пыли[3- 19]. Для поддержания пылеулавливающей системы в исправном и работоспособном состоянии важно следит за (эффективностью) снижения запылённости.
Снижение запылённости при бурении под землёй[править]
При бурении подземных скважин обычно используют ударное бурение при небольшом (до 76 мм / 3 дюйма) диаметре скважин. В зависимости от используемой технологии подземной добычи полезных ископаемых получаемые отверстия могут быть направлены в любую сторону. Отверстия для закладки взрывчатых веществ обычно направлены горизонтально или вертикально, и они в целом расположены симметрично. Для бурения может использоваться разное оборудование – от ручного перфоратора с поддержкой (упорами/стойками), до механизированных перфораторов на колёсном шасси Jumbo, где на одной машине есть два-три перфоратора (см. Рис. 3.17). Для снижения запылённости при бурении под землёй чаще всего используют мокрые способы. Сухие пылеуловители стали использовать позднее, и они используются не слишком широко из-за громоздкости фильтра и (относительно) сложного техобслуживания[3- 20].
Мокрое пылеподавление при бурении[править]
Wet Drilling
При мокром пылеподавлении вода используется для удаления разрушенной породы из скважины. На Рис. 3.18 показано, как вода закачивается в скважину через полый бур, выходит в центе наконечника бура, и вытекает через канал скважины, унося разрушенную породу. Давление воды, необходимое для её прокачивания, равно давлению воздуха, используемого для работы перфоратора, или меньше давления воздуха, но не более чем на 69 кПа (10 psi)[3- 2].
Самым лучшим способом снижения запылённости (на 86-97% - в зависимости от вида бурения) является мокрое бурение[3- 21][3- 22]. Угол наклона скважины прямо влияет на эффективность снижения запылённости. Наихудшее снижение запылённости обнаружилось при бурении вертикальных отверстий в кровле. При бурении наклонных отверстий (вверх от рабочего) в воздух попадало на 50-60% пыли меньше, чем при бурении вертикальных отверстий в кровле[3- 23]. Причина сильного пылеобразования при бурении вертикальных отверстий – то, что вода находится в контакте со стенками скважины непродолжительно, и то, что шлам быстро падает вниз и стекает по буровой трубе. Для увеличения пылеобразования при бурении вертикальных скважин[3- 24] используют:
- Увеличение подачи воды;
- Установку улавливателя для сбора шлама и его отвода от буровых труб;
- Проектирование таких перфораторов, у которых уменьшенная утечка воздуха спереди вдоль буровых труб; и
- Предотвращение разбрасывания стекающего шлама выходящим из перфоратора воздухом.
Изучалось влияние расхода воды на концентрацию пыли при работе разных перфораторов. У телескопических перфораторов (stoper drills) при увеличении расхода воды до 4.9 л/мин (1.3 gpm) концентрация пыли быстро убывала. А при продолжении увеличения расхода воды свыше 5 л/мин концентрация пыли снижалась, но гораздо медленнее. Это же явление наблюдалось и при работе колонковых перфораторов (drifter drill), но границей был расход воды 3.8 л/мин (1.0 gpm). Поэтому рекомендуется использовать оптимальный расход воды 4.9 л/мин для телескопических перфораторов, и 3.8 л/мин у колонковых перфораторов[3- 24]. Кроме того, мокрое бурение имеет другие преимущества – большая скорость проникания и уменьшение поломок бура (breakage), чем при сухом бурении[3- 21].
Измерения показали, что при прохождении первых 30÷60 см скважины при мокром бурении запылённость наибольшая[3- 25]. Затем концентрация пыли быстро снижается, и становится стабильной. Эти измерения также показали, что большая запылённость не связана с разбуриванием скважины, так как отверстия разбуривали перед началом измерений[3- 25].
Использование тумана и пены
Исследования также показали, что закачивание в скважину тумана из капель воды, и закачивание пены также снижает концентрацию пыли на 91-96%[3- 26][3- 27]. Но небольшое относительное снижение концентрации пыли по сравнению с мокрым бурением не окупает увеличение затрат при использовании этих способов.
Поверхностно-активные вещества (ПАВ)
Также изучалось использование добавки ПАВ к воде – но заметного улучшения не обнаружилось. Результаты показали, что добавка ПАВ при разном расходе воды уменьшает концентрацию пыли[3- 28]. Но снижение концентрации пыли при мокром бурении без всяких добавок настолько велико, что дальнейшее снижение за счёт использования ПАВ незначительно. Заявление о том, что добавка ПАВ повышает скорость бурения, сочли необоснованным из-за непостоянства скорости бурения (отклонения от -24.9% до +57.5%), и влияния на неё условий бурения[3- 28].
Распыление воды извне
Распыление воды извне, показанное на Рис. 3.19, стали использовать позднее. Но при сухом бурении концентрация пыли снижалась лишь до 25% по сравнению с сухим бурением (без использования воды вообще)[3- 21]. Для уменьшения запылённости при сухом бурении было придумано и испытано устройство – кольцо с отверстиями для распыления воды (с внутренней стороны). Это устройство одевается на бур и распыляет на него воду, находясь вне скважины. Снижение концентрации пыли при сухом бурении при использовании этого устройства было нестабильным, от 75 до 88%[3- 22]. Проводилась проверка эффективности установки ограждения вокруг места распыления воды (внешнего) на бур. Ограждение позволило снизить запылённость до 53%[3- 26]. Из-за слишком большой концентрации пыли установка такого ограждения и наружное распыление воды не могут использоваться вместо мокрого бурения – хотя и улучшает результат. Они могут использоваться как дополнение к мокрому бурению для дальнейшего уменьшения запылённости.
Снижение концентрации респирабельной пыли при взрывных работах[править]
Взрывные работы используют при добыче полезных ископаемых для периодического для разрушения породы. Это важный этап добычи полезных ископаемых, эффективность которого может сильно влиять на дробление и на расходы на измельчение руды[3- 29]. Хотя при взрывах очевидно образование большого количества пыли, но взрывные работы проводят достаточно редко, и считается, что они вносят небольшой вклад в (среднее) загрязнение воздуха мелкодисперсной пылью размером менее 10 мкм - PM10[3- 30][3- 31]. Проводились исследования для создания способа оценки того, какое количество пыли образуется при взрывах. Теперь такое приближённое определение можно сделать по формуле:
- е = 0.000225 × А1.5 (СИ)
- (е = 0.00050 × А1.5) (IP)
- где е – общее количество пыли, попавшее в воздух при взрыве, кг/взрыв (фунт/взрыв), и А – площадь взорванного участка (м2) – в случаях, когда глубина воронки не превышает 21 м (70 feet).
А для оценки доли частиц, меньших 10 мкм, используют уравнение:
- PM10 = e × 0.225 (СИ)
- (PM10 = e × 0.5) (IP)
- где PM10 = масса пыли, кг (фунты), частицы которой меньше 10 мкм, а е – общее количество пыли, попавшей в воздух (при одном взрыве).
Нужно отметить, что эти уравнения (U.S. EPA) дают лишь приблизительный результат. Чтобы определить массу пыли, попадающую в воздух при взрыве более точно, нужно учитывать факторы, зависящие от места проведения взрывов, и изученные при проведении реальных взрывов в схожих условиях[3- 32].
Снижение запылённости при проведении взрывных работ[править]
Поскольку считается, что проведение взрывов не вносит значительного вклада в (среднюю) запылённость, то документов с описанием способов снижения запылённости при проведении взрывных работ немного. Известно 5 способов, некоторые из которых способны эффективно снижать запылённость только при подземных взрывах[3- 33]:
- Увлажнение всей области, где будет проводиться взрыв,
- Установка ёмкостей с водой в скважину для закладки взрывчатки – после её закладки,
- Распыление водяного тумана перед, во время, и после взрыва,
- Использование воздухоочистителей для очистки воздуха от загрязнений, и
- Рассеивание и удаление воздушных загрязнений с помощью хорошо спроектированной вентиляционной системы.
Увлажнение области взрыва Wetting Down Blasting Area
Распространённым методом уменьшения запылённости при проведении взрывных работ является увлажнение всей взрываемой области перед взрывом. Это уменьшает попадание пыли в воздух из-за её прилипания к мокрым поверхностям[3- 33]. Этот способ оказался эффективным при проведении взрывных работ под землёй. Он также может быть эффективным при проведении взрывов на поверхности – в зависимости от (длительности) интервала времени между увлажнением и взрывом, с учётом скорости высыхания воды в имеющихся атмосферных условиях (что делает увлажнение неэффективным). Однако увлажнение места взрыва непосредственно перед ним, во время соединения проводов взрывателей, может оказаться недопустимым по соображениям безопасности.
Установка ёмкостей с водой Water Cartridges
При закладке взрывчатки в скважину после неё в отверстие может вставляться ёмкость с водой. Практика показала, что это эффективный способ при проведении подземных взрывов при добыче угля. Ёмкости закладываются после установки заряда взрывчатки, или перед ним – без какого-то негативного влияния на разрушение породы. На Рис. 3.20 показана разновидность такой ёмкости с водой. Этой ёмкостью является пластиковый мешок, который вставляют в отверстие после закладки взрывчатки, и который затем заполняют водой так, что он плотно прилегает к стенкам отверстия. Сообщали, что при подземной добыче угля использование таких ёмкостей уменьшает концентрацию пыли на 40-60%.
Генераторы тумана Fogger Sprays
На Рис. 3.21 показано использование генератора водяного тумана для снижения запылённости в забое при проведении взрывных работ. Использование такого способа началось позднее, чем других. для работы генератора тумана используют сжатый воздух и воду, пропуская их через сопло. Форсунка устанавливается на расстоянии около 30 м (100 футов) от забоя, и подача тумана начинается перед взрывом, а прекращается через 20÷30 минут после взрыва[3- 34]. Сейчас известно, что создание тумана позволяет эффективно снижать концентрацию пыли под землёй, но может ли это снизить концентрацию пыли при наземных взрывах – неизвестно.
Использование воздухоочистителей Air Filtration Systems
Другой способ уменьшения запылённости при проведении подземных взрывов, который стал использоваться позднее других – фильтрация загрязненного воздуха, удаляемого вентиляцией (Рис. 3.22). Одна из таких вентиляционных установок, используемых в Южной Африке, включает в себя противоаэрозольный фильтр (для улавливания пыли) и слой сорбента из вермикулита, обработанного карбонатом натрия и калия (для улавливания соединений азота)[3- 33]. На Рис. 3.23 показан другой метод. Фильтры располагаются вне вентиляционной системы, и форсунка распыляет воду на них (направление распыления совпадает с направлением движения воздуха). Эти фильтры используются только во время взрыва, и диаметр воздуховода, в котором они располагаются, примерно в 2 раза больше диаметра трубы вентиляционной системы[3- 34]. Сравнительно недавно для тех же целей стали использовать сухие фильтры.
Удаление пыли и газов подземной вентиляционной системой
Наиболее распространённый способ уменьшения концентрации пыли и газов при проведении взрывов – их рассеивание и удаление вентиляционной системой (под землёй), или их рассеивание в атмосфере (при наземных взрывах). При проведении взрывов под землёй их обычно планируют так, чтобы они проводились в то время, когда нет людей – чтобы для рассеивания и удаления вентиляцией пыли и газов было достаточно времени[3- 33]. Если такое расписание работ невозможно, то люди должны покинуть места проведения взрывов, и не должны заходить туда до того, как пыль и газы будут удалены или рассеются.
Необходимый для этого интервал времени зависит от конкретных условий, и зависит от местной вентиляционной системы. Поэтому важно поддерживать местную вентиляционную систему в хорошем и рабочем состоянии для улучшения удаления пыли и газов и для сокращения интервала времени, который необходим для этого.
При проведении работ на поверхности, непосредственно перед проведением взрыва люди покидают опасное место. При планировании взрывных работ учитывают метеоусловия (для уменьшения влияния на образование пыли используется низкая скорость ветра и слабая инверсия). Обычно сразу после взрыва происходит рассеивание пыли и газов – в зависимости от скорости и направления ветра, и до рассеивания пыли проведение работ в месте взрыва не разрешается. Кроме того, было отмечено (но пока точно не проверено), что использование детонаторов с задержкой взрыва на миллисекунды (при подрыве нескольких зарядов) может уменьшить пылеобразование[3- 35].
.
ССЫЛКИ
- ↑ 1,0 1,1 1,2 USBM [1987]. Optimizing dust control on surface coal mine drills. By Page SJ. U.S. Department of the Interior, Bureau of Mines Technology News 286.
- ↑ 2,0 2,1 Hustrulid WA, ed. [1982]. Underground mining methods handbook. New York: Society of Mining Engineers of the American Institute of Mining, Metallurgical, and Petroleum Engineers, Inc.
- ↑ USBM [1995]. The reduction of airborne dust generated by roof bolt drill bits through the use of water. By Sundae LS, Summers DA, Wright D, Cantrell BK. U.S. Department of the Interior, Bureau of Mines Report of Investigations 9594.
- ↑ 4,0 4,1 4,2 4,3 4,4 Page SJ [1991]. Respirable dust control on overburden drills at surface mines. Coal mining technology, economics, and policy. Session papers from the American Mining Congress Coal Convention, Pittsburgh, Pennsylvania, June 2–5, pp. 523–539.
- ↑ USBM [1988]. Impact of drill stem water separation on dust control for surface coal mines. By Page SJ. U.S. Department of the Interior, Bureau of Mines Technology News 308.
- ↑ 6,0 6,1 USBM [1985]. Quartz dust sources during overburden drilling at surface coal mines. By Maksimovic SD, Page SJ. U.S. Department of the Interior, Bureau of Mines Informational Circular 9056.
- ↑ USBM [1986]. Investigation of quartz dust sources and control mechanisms on surface mine operations, Vol. I—Results, analysis, and conclusions. By Zimmer RA, Lueck SR. U.S. Department of the Interior, Bureau of Mines Final Contract Report, NTIS: PB 86–215852, 72 pp.
- ↑ Zimmer RA, Lueck SR, Page SJ [1987]. Optimization of overburden drill dust control systems on surface coal mines. Inter J of Surface Min 1(2):155–157.
- ↑ Page SJ, Organiscak JA [2004]. Semi-empirical model for predicting surface coal mine drill respirable dust emissions. Inter J of Surface Min, Rec, and Env 18(1):42–59.
- ↑ NIOSH [2006]. Technology news 512: Improve drill dust collector capture through better shroud and inlet configurations. Pittsburgh, PA: U.S. Department of Health and Human Services, Centers for Disease Control and Prevention, National Institute for Occupational Safety and Health Publication No. 2006–108.
- ↑ Organiscak JA, Page SJ [2005]. Development of a dust collector inlet hood for enhanced surface mine drill dust capture. Inter J of Surface Min, Rec, and Env. 19(1):12–28.
- ↑ 12,0 12,1 12,2 Page SJ, Listak JM, Reed WR [2008a]. Drill dust capture-improve dust capture on your surface drill. Coal Age.
- ↑ 13,0 13,1 13,2 Page SJ, Reed WR, Listak JM [2008b]. An expanded model for predicting surface coal mine drill respirable dust emissions. Inter J of Surface Min, Rec, and Env 22(3):210–221.
- ↑ 14,0 14,1 14,2 Potts JD, Reed WR [2008]. Horizontal air blocking shelf reduces dust leakage from surface drill shroud. Transactions of the Society of Mining, Metallurgy, and Exploration. Littleton, Colorado: Society for Mining, Metallurgy, and Exploration, Inc. 324:55–60.
- ↑ 15,0 15,1 Reed WR, Potts JD [2009]. Improved drill shroud capture of respirable dust utilizing air nozzles underneath the drill deck. Transactions of the Society of Mining, Metallurgy, and Exploration. Littleton, Colorado: Society for Mining, Metallurgy, and Exploration. 326:1–9. Статья.
- ↑ 16,0 16,1 Potts JD, Reed WR [2010]. Field evaluation of air-blocking shelf for dust control on blasthole drills. Submitted to Mining Engineering, 2010.
- ↑ Reed WR, Organiscak JA, Page SJ [2004]. New approach controls dust at the collector dump point. Coal Age, June, pp. 20–22.
- ↑ USBM [1956]. Dust control in mining, tunneling, and quarrying in the United States. By Owings CW. U.S. Department of the Interior, Bureau of Mines Information Circular 7760.
- ↑ Sandvik [2005]. Tamrock ranger drills feature rock pilot, dust minimizor systems for enhanced and cleaner operation. Atlanta, Georgia: Sandvik Mining and Construction. - документ не найден.
- ↑ USBM [1951]. Roof bolting and dust control. By Westfield J, Anderson FG, Owings CW, Harmon JP, Johnson L. U.S. Department of the Interior, Bureau of Mines Information Circular 7615.
- ↑ 21,0 21,1 21,2 USBM [1921]. Dust reduction by wet stopers. By Harrington D. U.S. Department of the Interior, Bureau of Mines Report of Investigations 2291.
- ↑ 22,0 22,1 USBM [1939]. Dust produced by drilling when water is sprayed on the outside of the drill steel. By Johnson JA, Agnew WG. U.S. Department of the Interior, Bureau of Mines Report of Investigations 3478.
- ↑ USBM [1938a]. Effect of angle of drilling on dust dissemination. By Brown CE, Schrenk HH. U.S. Department of the Interior, Bureau of Mines Report of Investigations 3381.
- ↑ 24,0 24,1 USBM [1938c]. Relation of dust dissemination to water flow through rock drills. By Brown CE, Schrenk HH. U.S. Department of the Interior, Bureau of Mines Report of Investigations 3393.
- ↑ 25,0 25,1 USBM [1938b]. Relation of dust concentration to depth of hole during wet drilling. By Littlefield JB, Schrenk HH. U.S. Department of the Interior, Bureau of Mines Report of Investigations 3369.
- ↑ 26,0 26,1 USBM [1982a]. An evaluation of three wet dust control techniques for face drills. Page SJ. U.S. Department of the Interior, Bureau of Mines Report of Investigations 8596.
- ↑ USBM [1982b]. Evaluation of the use of foam for dust control on face drills and crushers. By Page SJ. U.S. Department of the Interior, Bureau of Mines Report of Investigations 8595.
- ↑ 28,0 28,1 USBM [1943]. Use of wetting agents in reducing dust produced by wet drilling in basalt. By Johnson JA. U.S. Department of the Interior, Bureau of Mines Report of Investigations 3678.
- ↑ Hustrulid WA [1999]. Blasting principles for open pit mining, Vol. 1—General design concepts. Rotterdam, Netherlands: A.A. Balkema.
- ↑ EPA [1991]. Review of Surface Coal Mining Emissions Factors. U.S. Environmental Protection Agency, Office of Air Quality Planning and Standards, Research Triangle Park, North Carolina, July.
- ↑ Richards J, Brozell T [2001]. Compilation of National Stone, Sand and Gravel Association Sponsored Emission Factor and Air Quality Studies 1991–2001. Arlington, Virginia: National Stone, Sand and Gravel Association www.nssga.org .
- ↑ EPA [1998]. Review of Emission Factors for AP—42 Section 11.9 Western Surface Coal Mining. U.S. Environmental Protection Agency, Office of Air Quality Planning and Standards, Research Triangle Park, North Carolina, September.
- ↑ 33,0 33,1 33,2 33,3 Cummins AB, Given IA, eds. [1973]. SME Mining engineering handbook, Vol. 1. New York: Society of Mining Engineers of the American Institute of Mining, Metallurgical, and Petroleum Engineers, Inc.
- ↑ 34,0 34,1 ILO [1965]. Guide to the prevention and suppression of dust in mining, tunnelling, and quarrying. International Labour Office, Geneva, Switzerland; Atar, South Africa.
- ↑ Miller S, Emerick JC, Vogely WA [1985]. The secondary effects of mineral development. Economics of the mineral industries, chapter 5.15B. Littleton, Colorado: Society of Mining, Metallurgy, and Exploration.
ГЛАВА 4. Дробление, размол и просеивание[править]
Crushing, milling and screening
По самой своей природе процессы дробления, размола и просева минеральных полезных ископаемых могут стать источниками значительного количества пыли. Для снижении концентрации пыли при выполнении этих технологических процессов требуется правильно определить источники пыли, найти подходящие методы снижения концентрации пыли, применить их и обеспечить необходимое и своевременное техобслуживание используемого оборудования.
Для уменьшения воздействия пыли на рабочих можно использовать технические средства для снижения пылеобразования или изоляции источников пыли, описанные ниже; или же изолировать рабочего от источника пыли, как описано в главе 9 “Кабины операторов, пульты управления и кабины мобильного оборудования”. Как дополнение к применению технических средств, широко используют организационные мероприятия – инструкции/ выполнения работы, организация выполнения работы, обучение рабочих. В те периоды времени, когда происходит установка, ремонт, техобслуживание (и другие не-ежесменные работы) достаточно эффективных технических средств защиты, и когда полученное с их помощью снижение запылённости оказывается недостаточным, может потребоваться использование средств индивидуальной защиты.
Как и у всякого оборудования, установка выбранных технических средств снижения запылённости (когда выбрано подходящее оборудование), не гарантирует, что они сохранят работоспособность и эффективность при дальнейшей эксплуатации. Параметры работы газоочистного оборудования, которое часто является дорогостоящим, нужно периодически проверять; у самого оборудования проводить техобслуживание, и – при необходимости – модернизацию. Например, эффективность пылеулавливающей системы, установленной для защиты рабочих от пыли, можно проверить только если сделать замеры концентрации пыли в зоне дыхания рабочего с помощью индивидуальных пробоотборников и сравнить концентрации химических веществ с ПДКрз.
Разное оборудование для переработки минерального сырья загрязняет воздух пылью в разной степени. Если принять интенсивность пылеобразования первичной дробилки как основу для сравнения, то в таблице 4.1 можно найти информацию об интенсивности пылеобразования при проведении других широко используемых видов обработки минеральных ископаемых. Приведённое ранжирование основано на оценках EPA для дробления камней/щебёнки, и представлено здесь лишь для иллюстрации интенсивности пылеобразования у разных процессов[4- 1]. Видно, что чем мельче конечный продукт, тем больше интенсивность пылеобразования, что и следовало ожидать.
Оборудование | Относительная интенсивность пылеобразования |
---|---|
Первичная дробилка | 1 |
Вторичная дробилка | Нет данных, информация для третичной дробилки является верхней границей возможных значений. |
Третичная дробилка (сухая) | 51 |
Третичная дробилка (мокрая) | 2 |
Просеивание (сухое) | 214 |
Просеивание (мокрое) | 12 |
Предотвращение попадания пыли в воздух и очистка воздуха от пыли[править]
Мокрые способы[править]
Мокрые способы снижения концентрации пыли могут быть очень эффективными и менее дорогими по капитальным и эксплуатационным расходам, но они могут оказаться неподходящими из-за свойств минерального сырья, из-за проблем при дальнейшей переработке, или из-за невыполнения технических условий покупателя. Кроме того, при проведении переработки в местах с холодным климатом нужно предусмотреть защиту от замерзания, и нарастание льда создаёт дополнительную опасность для рабочих.
Как более подробно обсуждалось в главе 2 “Обеспыливание с помощью воды”, все методы, использующие воду для снижения концентрации пыли, можно разделить на две группы – предотвращение (попадания пыли в воздух), и улавливание (попавшей в воздух пыли). При предотвращении вода используется для того, чтобы помешать пыли попасть в воздух. При улавливании капли воды смачивают частицы пыли, уже попавшие в воздух, увеличивая их массу и заставляя их оседать под действием силы тяжести гораздо быстрее.
В целом, предотвращение гораздо эффективнее, чем улавливание[4- 2][4- 3]. Но при дальнейшем измельчении намоченного материала из-за увеличения площади его поверхности нужно его дополнительно увлажнять. А это может создать дополнительные проблемы, так как дополнительное увлажнение для предотвращения попадания пыли в воздух может сделать материал слишком сырым, так что это помешает нормальной работе и техобслуживанию оборудования, переработке материала или получению конечного продукта с требуемыми свойствами. Поэтому часто трудно избежать некоторого компромисса между снижением концентрации пыли и эффективностью технологического процесса.
Улавливание респирабельной пыли с помощью распыления воды форсунками на облако пыли обычно малоэффективно. При использовании форсунок с гидравлическим распылением сложно получить достаточно маленькие капельки воды для того, чтобы они могли столкнуться и уловить мелкие респирабельные пылинки. Мелкие капельки можно получить с помощью пневматических форсунок, но для этого нужен источник сжатого воздуха, а очень маленькие сопла чаще засоряются, что увеличивает затраты на техобслуживание. Кроме того, использование пневматических форсунок из-за большого объёма выпускаемой смеси воздуха и воды обычно требует использования укрытий для предотвращения переноса пыли в окружающее пространство. Всё это увеличивает эксплуатационные расходы.
Сухие способы снижения запылённости[править]
Для уменьшения концентрации пыли при транспортировке (см. главу 5 “Перевозка и перемещение материала”) и переработке минеральных полезных ископаемых можно использовать укрытия с разрежением, местные вентиляционные отсосы и очистку запылённого воздуха. Этот подход, который можно назвать сухим способом снижения запылённости, может потребовать больших капитальных и эксплуатационных расходов, но может оказаться очень эффективным. Кроме того, использование сухого способа может потребоваться тогда, когда увлажнение отрицательно сказывается на качестве продукта (например - тронов или глины).
При использовании сухих способов нужно создать условия для предотвращения распространения запылённого воздуха от источника пыли на рабочие места сотрудников. Для этого используют вытяжную вентиляцию, которая создаёт разрежение в ограниченном укрытием пространстве (разрежение - по отношению к окружающему пространству, см. главу 1 “Принципы пылеулавливания”). На расход отсасываемого воздуха влияет:
- Степень закрытости ограниченного пространства (при увеличении площади проёмов расход воздуха возрастает);
- Движение воздуха, вызванное перемещением и обработкой материала (включая тот воздух, который увлекается перемещающимся материалом и движущимся оборудованием), и количество воздуха, вытесняемое материалом, входящим в или выходящим из укрытия,
- Влиянием внешнего движения воздуха и его направлением движения, которое может мешать созданию разрежения в укрытии.
Дробление[править]
При измельчении материала используется как минимум одна измельчающая установка, а обычно их используют несколько, и они часто бывают разной конструкции. При выборе типа измельчителя учитывают требуемые размеры кусков исходного и получаемого продукта, а также производительность. При выборе также учитывается твёрдость, состав, и абразивные свойства измельчаемого материала. Для первичного этапа измельчения чаще всего используют щековую дробилку (jaw crusher), Рис. 4.1, которая измельчает материал, сжимая его между подвижной и неподвижной плитами. Коническая (Рис. 4.2 слева) или вращательная конусная gyratory (Рис. 4.2 справа) дробилки могут использоваться для первичного или вторичного измельчения. Они разрушают материал за счёт сжатия.
Молотковые дробилки hammermills (Рис. 4.3 слева), ударные дробилки impact breakers (Рис. 4.3 в центре) и валковая дробилка roll crushers (Рис. 4.3 справа) разрушают материал за счёт удара. Отличие между разрушением за счёт сжатия и за счёт удара в том, с какой скоростью разрушающая сила передаётся от частей устройства к разрушаемым кускам материала. При сжатии передача энергии происходит медленнее, чем при ударе, и в сжимающих измельчителях пылеобразование несколько меньше, чем ударных.
Для снижения концентрации пыли при измельчении материала можно использовать мокрые способы, сделать укрытие для изоляции источника пыли от окружающего пространства – с и без отсасывания запылённого воздуха, или использовать сочетание мокрых и сухих методов. Обычно (стараются) закрыть верхнюю часть измельчителя (место загрузки материала) в максимальной степени, насколько удаётся[4- 4]. Укрытия должны быть сделаны из стойкого материала, с учётом производственных условий на месте установки и климатических условий.
На Рис. 4.4 показано применение мокрого способа уменьшения запылённости в месте загрузки материала ковшовым погрузчиком. Передняя – открытая - часть укрытия может быть уменьшена с помощью установки подвешиваемой занавеси (вверху) и высокого бордюра или бермы (уступа) внизу. Для экономии нужно использовать автоматику, включающую распыление воды только тогда, когда происходит выгрузка материала.
Как описывалось в главе 2 "Обеспыливание с помощью воды", при использовании воды для увлажнения материала для предотвращения попадания пыли в воздух обычно применяют форсунки со сплошной струёй (с факелом - полным конусом; или с факелом - полым конусом). А при распылении воды для улавливания пыли, уже попавшей в воздух, используют форсунки с факелом – полым конусом. Чтобы обеспечить хороший охват (смачиваемого материала / запылённого воздуха) струи воды должны немного перекрываться.
На Рис. 4.5 показано использование вытяжной вентиляции для снижения концентрации пыли в месте загрузки материала.
Укрытие места образования пыли должно быть как можно более полным, то есть площадь открытых отверстий должна быть сведена к минимуму. Для начальной (приблизительной) оценки расхода отсасываемого воздуха для укрытия, схожего с показанным на Рис. 4.5, можно использовать уравнение 4.1. это уравнение учитывает то, что выгружаемый материал вытесняет воздух:
- Qe = 9 × Т / G (м3/с) = 32368 × Т / G (м3/час) (Уравнение 4.1) (СИ)
- [Qe = 33.3 × (600*Т/G)] (Уравнение 4.1) (IP)
(коэффициенты 9 и 32368 используется вместо коэффициентов 33.3 и 600 для исходных данных в метрах, кг/м3 и кг/сек; а коэффициент 33.3 и 600 – для исходных данных в футах, фунтах/фут3 и тоннах/мин)
- где Qe = расход отсасываемого воздуха, м3/с, м3/час (cubic feet per minute);
- T = масса выгружаемого материала, кг/сек (тонн в минуту); и
- G = насыпная плотность материала, кг/м3 (pounds per cubic foot).
Если выгрузка материала происходит с перерывами, то нужно подумать об установке автоматики, включающей вытяжку и/или распыление воды только в то время, когда происходит выгрузка.
При использовании вытяжной вентиляции для уменьшения концентрации пыли нужно предусмотреть устройство проёмов для доступа и для техобслуживания, и эти проёмы должны плотно, герметично закрываться. Проёмы, расположенные в подходящих местах, и подходящего размера, позволят рабочим выполнять необходимые действия без необходимости в переделке укрытия. Это снизит риск утечки пыли из укрытия через отверстия, (придётся сделать по необходимости – при отсутствии подходящих люков) в не предусмотренных изначально местах, и не имеющие плотно закрывающихся дверей.
Для предотвращения уноса пыли через открытые отверстия рекомендуется поддерживать скорость воздуха не ниже 1 м/с (200 feet per minute) во всех отверстиях[4- 4]. В тех случаях, когда в укрытие входит или выходит ленточный транспортёр, рекомендуется добавлять его скорость движения к скорости 1 м/с, чтобы учесть движение воздуха, вызванное перемещением ремня конвейера, и перемещение материала, который вытесняет воздух[4- 5].
Например, в укрытии с начальной скоростью улавливания (скорость воздуха в проёмах) Vinit 1 м/с (200 feet per minute fpm) при прохождении транспортёра со скоростью ленты Vbelt 1.25 м/с (250 fpm), получаем рекомендуемую скорость воздуха в проёмах (Vcap):
- Скорость улавливания (Vcap) = Vinit 1 м/с + Vbelt 1.25 м/с = 2.25 м/с (200 fpm + 250 fpm = 450 fpm).
А расход воздуха, отсасываемого из укрытия, вычисляется умножением площади всех проёмов в укрытии на скорость улавливания:
- Qe (м3/сек) = Vcap (м/с) x площадь (м2) (СИ)
- Qe (cfm) = Vcap (fpm) x open area (sq ft) (IP)
И снова, эти начальные оценки скорости воздуха и расхода воздуха требуют проверки – они должны (1) обеспечить требуемое снижение концентрации пыли, и (2) не требовать чрезмерного расхода энергии. Более подробно работа вытяжной вентиляции рассмотрена в главе 1 “Принципы пылеулавливания”.
Если это возможно, нужно делать укрытия большого размера так, чтобы крупнодисперсная пыль могла оседать в них (внутри). Осаждение крупных частиц пыли таким способом снижает нагрузку на системы транспортировки и очистки воздуха.
При падении материала в местах его выгрузки возникает движение воздуха – из-за вовлечения воздуха в движение материала, и из-за вытеснения воздуха выгружаемым материалом[4- 6][4- 7]. При среднем размере кусков материала больше 3 мм (1/8 дюйма, или 0.01 фута), для оценки этой скорости воздуха можно использовать уравнение 4.2:
- Qe = 0.1157 × Au × (R × S2 / D)1/3 (м3/с) = 416.5 × Au × (R × S2 / D)1/3 (м3/час)
- Qe = 10 × Au [R × S2/D]1/3 (Уравнение 4.2) (IP)
(коэффициенты 0.1157 и 416.5 используется вместо коэффициента 10 для исходных данных в метрах и кг/сек; а коэффициент 10 – для исходных данных в футах и тоннах/час, см. Уравнение 1.2 – они одинаковы)
- где Qе = расход отсасываемого воздуха, м3/с, м3/час (cubic feet per minute);
- Au = Площадь открытых проёмов укрытия, м2 (square feet);
- R = Подача материала, тонн в час;
- S = Высота падения материала, м (feet); и
- D = Средний размер частиц материала, м (feet).
На рисунках 4.2÷4.6 показано определение расхода отсасываемого воздуха с помощью уравнения 4.2. В каждом из случаев отмечена высота падения материала (переменная S в уравнении 4.2). Площадь открытого проёма вверху (Au) у места перегрузки равна площади поперечного сечения жёлоба/лотка, и не закрытого пространства между жёлобом и окружающими элементами конструкции укрытия. Если лоток не используется, то для определения площади проёма можно использовать оценку площади открытого пространства в месте, где есть проём (например – для размещение ленточного транспортёра).
На Рис. 4.8 и 4.9 показано, как происходит перегрузка материала из места выгрузки на конвейер. У щековой дробилки, у которой площадь поперечного сечения проёма не постоянна, величина площади открытого проёма вверху (обеспыливаемой системы) Au равна площади отверстия в нижней части дробилки (Рис. 4.8).
Для измельчителей с постоянным поперечным сечением, например – для конических дробилок, площадью проёма вверху (обеспыливаемой системы) является площадь загрузочного отверстия (самой) дробилки (Рис. 4.9).
О снижении запылённости в местах перегрузки материала более подробно написано в главе 5 “Перевозка и перемещение материала”.
При использовании мокрого обеспыливания при измельчении материала, показанного на Рис. 4.10 и 4.11, материал увлажняется перед измельчением; после измельчения, или в обоих случаях. Увлажнение чаще всего используется в местах загрузки материала в дробилку и при выгрузке из неё. При измельчении размер кусков уменьшается, что приводит к соответствующему увеличению площади поверхности, которая не увлажнена. Поэтому если материал увлажнялся перед измельчением, то скорее всего, его придётся увлажнять снова после измельчения, чтобы смочить вновь образовавшуюся сухую поверхность.
При использовании мокрых способов обеспыливания нужно помнить, что форсунки с полным конусом создают капли большего размера, чем форсунки с полым конусом. Для улавливания пыли, уже попавшей в воздух, нужно использовать форсунки с полым конусом, и распыление воды должно охватывать всё пространство, в котором находится пыль. А при использовании увлажнения для предотвращения попадания пыли в воздух (например – в бункере для материала), нужно использовать форсунки с полным конусом – так, чтобы они охватывали всю площадь увлажняемого материала. При увлажнении подвижного материала, например – на ленте конвейера, следует использовать форсунки с веерообразным факелом (чтобы наибольший размер поперечного сечения факела был перпендикулярен направлению движения материала), и перекрытие должно составлять около 30% от ширины факела. Мокрые методы обеспыливания более подробно описаны в главе 2 “Обеспыливание с помощью воды”.
Механическое перемещение частей дробилок может вызывать движение воздуха. Работу щековой дробилки можно сравнить с движением мехов, а конусная дробилка действует как вентилятор, хотя части дробилок обоих типов движутся на маленькой скорости. Части молотковой дробилки движутся с большой скоростью, и их можно сравнить с радиальными вентиляторами. Описан метод, позволяющий вычислить максимальный расход воздуха, создаваемый такими дробилками[4- 8]. Для определения максимального объёма воздуха (м3 / cubic feet), перемещаемого за один оборот (Agen rev), можно рассматривать подвижную часть молотковой дробилки как вентилятор, и использовать уравнение 4.3:
- Agen rev = π / ( 4 × D2 × W) (Уравнение 4.3) (СИ, IP)
- где D = диаметр молотковой дробилки (наибольший размер), м (feet); и
- W = ширина молотков, м (feet).
Затем можно получить минутный расход воздуха (м3/мин / cfm), умножив полученную величину (Agen rev) на частоту вращения (об/мин). Для более точного определения расхода воздуха следует измерять скорость воздуха в проёмах укрытия при работающем и при не работающем оборудовании. Если скорость движения воздуха извне внутрь укрытия во время работы оборудовании окажется недостаточной, то нужно увеличить расход воздуха, отсасываемого из укрытия, или разместить в нём экраны / перегородки.
Рекомендации по снижению запылённости при дроблении[править]
Для уменьшения воздействия пыли на операторов при дроблении материала можно рекомендовать:
- Поддерживайте в исправном состоянии запирающие приспособления, и используйте их. Они помогают (снизить запылённость) только при их применении.
- Если это допустимо и возможно, периодически мойте территорию. Периодическое промывание полов предотвращает накопление материала, который в противном случае может накопиться в таком количестве, что потребуется его убирать сухим способом, что приведёт к попаданию пыли в воздух.
- Поддерживайте в исправном состоянии системы фильтрации приточного и рециркуляционного воздуха в кабинах операторов оборудования, кабинах ковшовых погрузчиков и другой используемой подвижной техники. Обеспечьте использование лишь тех фильтров, которые должны применяться, и проводите техобслуживание в соответствии с указаниями изготовителя.
- При выполнении работы (внутри) пылеуловителей, мельниц, воздушных сепараторов, вибросит и дробилок используйте сертифицированные респираторы с тем уровнем защиты, который соответствует условиям работы.
- Если возможно, автоматизируйте процесс дробления, используя датчики и/или видеокамеры. Это позволит оператору управлять работой оборудования издали, и снизит риск вдыхания пыли.
- Если за работой дробильного оборудования нужно наблюдать непрерывно, используйте закрытые кабины для операторов с подачей в них отфильтрованного воздуха под избыточным давлением. См. главу 9 “Кабины операторов, пульты управления и кабины мобильного оборудования”.
Размол[править]
Размалывание (которое иногда называют растиранием) – это процесс, при котором зёрна минеральных полезных ископаемых уменьшаются в размерах за счёт сжатия, истирания и ударов. На основе принципа действия, мельницы можно разделить на два вида: барабанные мельницы (tumbling mills), Рис. 4.12, и башенные мельницы (stirring mills), Рис. 4.13. Барабанные мельницы обычно вращаются вокруг горизонтальной оси, и их вращающаяся оболочка передаёт движение загруженному содержимому. А башенные мельницы могут быть горизонтальными или вертикальными, и для передачи движения содержимому используется подвижный внутренний элемент конструкции.
В барабанных мельницах используют какие-то инертные тела для измельчения материала. Часто это стержни или шары, которые обычно делают из металлических сплавов или из керамики с высокой плотностью (если большое значение имеет предотвращение попадания металла в готовый продукт). В бесшаровых мельницах (autogenous mills) используется самоистирание материала, а в мельницах полу-самоизмельчения (semi-autogenous mills) используется сочетание перерабатываемого сырья и шаров. В башенных мельницах материал измельчается между неподвижными и вращающимися частями мельницы. Материал, выгружаемый из мельницы, может иметь размер частиц от 40 до 300 мкм у башенных мельниц и от 40 до менее чем 15 мкм у барабанных мельниц[4- 9].
Хотя измельчение минеральных полезных ископаемых можно проводить с помощью мокрого размола, в промышленности чаще используют сухое размалывание. В некоторых технологических процессах в мельницу для размола подаётся отсев, полученный при сухом просеивании. В этом случае в мельницу поступает сухой материал с размером зёрен менее 1.7 мм (12 mesh), а размер полученных частиц порядка 50 мкм. Но при мелком помоле некоторых материалов размер полученных частиц может быть меньше 10 мкм. Это означает, что все частицы готового продукта – респирабельного размера.
В некоторых случаях производят размалывание материала, который закупается во влажном кусковом состоянии, и сушится перед помолом. Несмотря на влажность исходного материала, всё технологическое оборудование, используемое для подготовки и подачи материала в мельницу, может стать источником пыли, и это должно учитываться при разработке системы обеспыливания.
При размоле и сепарации/классификации главным является предотвращение распространения пыли за пределы оборудования, которое размалывает, сепарирует/просеивает и хранит готовый продукт, а улавливание пыли – второстепенно. Всё оборудование, которое перемещает материал к и от мельницы, должно быть загерметизировано. Все места перегрузки должны быть полностью закрыты.
Рекомендации по снижению запылённости при размалывании материала[править]
Для уменьшения воздействия пыли на операторов при размоле можно рекомендовать:
- Мельницы и связанное с ними оборудование должны быть закрыты герметичными кожухами, в которых должно поддерживаться небольшое разрежение в течение всего времени их использования, а отсасываемый воздух должен направляться в пылеуловитель. Это приведёт к тому, что во всех зазорах и неплотностях воздух будет двигаться снаружи вовнутрь, что предотвратит вынос пыли наружу.
- Для осмотра и доступа к оборудованию в кожухе должны быть сделаны люки и двери – так, чтобы когда они открыты размолотый материал оставался внутри.
- Все люки и двери должны находиться в местах, где наклон поверхности кожуха составляет 45° по отношению к горизонтали, или меньше. Лучше всего размещать люки на горизонтальных поверхностях, так как это обеспечивает удобный доступ и риск высыпания материала минимален (см. Рис. 4.14).
- Размалывающее оборудование и помещения, где оно находится, должны быть приспособлены для мытья (например – из шланга).
- Для уборки должна быть установлена и должна применяться вакуумная (пылесосная) система. Нельзя проводить уборку с помощью сухого подметания, так как при этом пыль поднимается с пола в воздух. По той же причине нельзя сдувать пыль с оборудования или пола сжатым воздухом.
- Верхние этажи/ярусы (здания) (upper levels) около технологического оборудования должны быть сделаны со сплошным полом – так, чтобы при просыпании материала он оставался на них, а не просыпался ниже, что приводит к попаданию пыли в воздух.
- Разные части технологического процесса должны проводиться в отдельных помещениях/укрытиях для улучшения изоляции (потенциального источника пыли) от окружающего пространства. Примеры: не укрытые места хранения, места фасовки, места выгрузки материала.
- Если температура выше нуля, то нужно поддерживать полы во влажном состоянии так, чтобы любая упавшая пыль сразу намокала и не могла попасть в воздух.
- Рекомендуется обеспечить воздухообмен во всех помещениях не менее 10 раз в час.
- При сепарации частиц по размерам нужно использовать указания поставщика в отношении места отсоса воздуха и расхода отсасываемого воздуха для получения наилучшего результата. При выполнении других видов переработки материала (измельчении, погрузке/выгрузке) расположение и расход воздуха у местных отсосов должны быть такими, чтобы в местах перегрузки материала не было сильного движения воздуха, так чтобы движение воздуха не могло поднимать пыль.
- При запуске новых или недавно установленных шаровых мельниц (tumbling mills), отсасываемый из них воздух первое время будет очень влажным– до тех пор, пока нагрев при измельчении материала не приведёт к удалению влаги (из влажного материала curing grout). Это может привести к увлажнению труб и их засорению попадающей затем в воздуховоды сухой пылью; и это может привести к засорению фильтровального материала в рукавных и картриджных фильтрах. Обычно эта проблема исчезает, когда мельница разогревается до рабочей температуры, и материал высыхает.
Просев[править]
При просеве образуется много пыли из-за того, что происходит обработка частиц наименьшего размера. Пыль попадает в воздух с вибрирующего сита, которое разделяет частицы по размерам. Кроме того, при просеве материал может падать с какой-то высоты, что также приводит к попаданию пыли в воздух. Для снижения концентрации пыли при просеве используются такие же методы, что и при измельчении, но мокрые способы обычно не используют из-за риска засорения отверстий сита мокрым материалом. При просеивании на сито обычно не сбрасывают много материала одновременно – как в дробилки и другие измельчители – из-за того, что вибросита эффективно работают только при том количестве подаваемого материала, на которое они рассчитаны. При перегрузке сита (из-за большой подачи материала, или при подаче материала с большими скачками) может произойти ускоренный износ частей сита, снижение эффективности работы и потенциальное увеличение количества пыли, попадающей в воздух.
Вибросита должны размещаться в полностью закрытом укрытии, которое должно быть подключено к обеспыливающей вентиляционной системе, или должно использоваться мокрое обеспыливание – если это допустимо. Количество люков и проёмов в укрытии сита, используемых для осмотров и обслуживания, должно быть сведено к минимуму, и они должны закрываться герметичными крышками.
Для закрывания проёмов между подвижными частями вибросита и неподвижными частями оборудования нужно использовать гибкие материалы – резину и синтетические материалы. Так как уплотнение между подвижными и неподвижными частями оборудования подвергается значительным динамическим нагрузкам, то его нужно регулярно проверять для обнаружения повреждений – по расписанию, составляемому с учётом режима эксплуатации. Некоторые изготовители вибросит производят также и дополнительные компоненты для обеспыливания именно их оборудования – укрытия, гибкие уплотнения и др., использование которых позволяет эффективно снизить концентрацию пыли. Поэтому нужно обратиться к продавцам с запросом – нет ли к продаваемым ситам дополнительных приспособлений для снижения запылённости.
Для оценки расхода воздуха, который должен отсасываться из укрытия вибросита, в первом приближении можно использовать метод вовлечения воздух в движение (с помощью уравнения 4.2), На Рис. 4.15 и 4.16 показана схема вентиляции при обеспыливании сит. На рисунках показана высота падения материала (уравнение 4.2, переменная S). Размер верхнего проёма в укрытии (уравнение 4.2, переменная Au) – это площадь поперечного сечения лотка подачи материала плюс площадь любого другого не закрытого проёма в месте входя лотка в укрытие.
Другой способ оценки расхода отсасываемого воздуха (в первом приближении) – брать по 0.272 м3/сек / 914 м3/час (50 cfm per square foot) на каждый квадратный метр площади сита (если оно плоское)[4- 10]. Если на вибросите установлено несколько сит (с разными ячейками - одно над другим), то это значение не нужно увеличивать, так как площадь источника пыли при расположении нескольких сит одно над другим не возрастает по сравнению с одиночным ситом. Если сито вращающееся, то рекомендуется брать по 0.544 м3/сек / 1828 м3/час на 1 м2 поперечного сечения вращающегося сита (100 cfm per square foot of screen cylindrical cross section) при скорости движения воздуха в проёмах внутрь укрытия не менее 2 м/с (400 fpm)[4- 10].
Место отсоса воздуха из укрытия нужно выбирать так, чтобы не происходило засасывания получаемого мелкодисперсного продукта. Отсос воздуха из укрытия поблизости от места выгрузки (вдали от места загрузки материала) может уменьшить унос мелкодисперсных частиц. Также можно присоединять вентиляционную трубу к укрытию с помощью переходника, увеличивающего площадь поперечного сечения воздуховода в месте его присоединения. Это уменьшит скорость движения всасываемого воздуха, и уменьшит унос мелкодисперсных частиц.
Рекомендации по уменьшению попадания пыли в воздух при просеивании[править]
Приведённые ниже рекомендации взяты из практики применения сит на разных предприятиях, и когда это возможно нужно их применять:
- При необходимости проведите уборку оборудования или помещения – до начала и во время работы – преимущественно с помощью пылесосного оборудования, или проводя мокрую уборку.
- Перед очисткой сита прекратите подачу материала – если это возможно. Чем меньше материала на сите, тем меньше пыли попадёт в воздух.
- При очистке открывайте только верхнюю или только нижнюю часть сита (не открывайте их одновременно). Чем больше размер проёма (открытого люка), тем меньше эффективность вентиляционной системы.
- При проведении очистки открывайте не более одного сита одновременно – не открывайте несколько сит сразу. Чем больше размер открытых проёмов, тем меньше эффективность вентиляционной системы, предотвращающей унос пыли наружу.
- При очистке сит используйте только такие щётки, у которых длинные ручки, которые позволяют рабочему находиться на удалении от источника пыли.
- Изучите возможность использования вибраторов с переменной частотой колебаний, так как это значительно увеличивает периоды времени между проведением очисток сит. А чем реже проводится такая работа, тем меньше длительность периодов времени, в течение которых возможно воздействие пыли на рабочих.
- Открывайте деки сита (в многоуровневых ситах с разными ячейками дека – это один уровень) медленно, чтобы вытяжная вентиляция продолжала работать по периметру сита. При быстром открывании могут возникнуть такие завихрения, которые могут вынести пыль из укрытия в окружающее пространство, так что она может попасть в органы дыхания.
- Не хлопайте декой сита при её закрывании. Хлопанье приведёт к тому, что материал – неважно, как много или мало – сможет попасть в воздух из-за сотрясения укрытия.
- Деки сит не должны быть покрыты пылью. Это уменьшает вероятность попадания пыли в воздух при открывании и закрывании дек, и риск попадания пыли в воздух при воздействия ветра и т.п.
- Если деках сит требуется воздухонепроницаемое уплотнение, то проводите техобслуживание уплотнений. Хорошо загерметизированные деки сит должны обеспечить воздухонепроницаемость, когда все герметизирующие прокладки и т.п. на месте, и когда все запирающие приспособления закрыты.
- Затворы (люки) и запирающие приспособления (зажимы и т.п.) должны поддерживаться в исправном и работоспособном состоянии. Задвижки и т.п. эффективны только тогда, когда они используются.
- Если это позволяет технологический процесс и свойства материала, периодически мойте помещение около сит. Это удаляет материал до того, как его накопится так много, что потребуется сухая уборка. А при сухой уборке вероятность попадания пыли в воздух и её вдыхания гораздо выше.
Техобслуживание[править]
Для надёжной защиты рабочих от пыли важно проводит качественное и своевременное обслуживание обеспыливающего оборудования[4- 4]. Дробилки и сита вибрируют во время работы, и их вибрация ускоряет износ и разрушение остального оборудования. А появление даже небольших отверстий в местах износа, разрушения/выпадения прокладок, разрывах гибких эластичных соединений, может привести к просачиванию воздуха, уменьшающему скорость улавливания пыли (скорость движения воздуха внутрь оборудования и укрытия) в используемых технологических проёмах[4- 7]. Это может привести к чрезмерному воздействию пыли на рабочих – особенно тогда, когда численные значения ПДКрз маленькие.
Операторы должны записывать “базовые” параметры работы обеспыливающего оборудования при его эффективной работе, в том числе:
- Скорость воздуха в проёмах укрытия;
- Статическое давление воздуха в воздуховодах;
- Скоростной напор в воздуховодах и в местах всасывания воздуха в воздуховоды; а также
- Давление и расход воды в мокрых обеспыливающих системах.
При проведении последующих периодических проверок их результаты нужно сравнивать с “базовыми” (полученными при эффективной работе оборудования). При наличии значительных отклонений от базовых значений нужно установить причину отличия и выполнить корректирующие мероприятия – если это необходимо.
На основе рекомендаций изготовителя нужно составить график проведения периодического (профилактического) техобслуживания. При планировании такой работы нужно учитывать обнаруженный износ частей оборудования, показатели работы системы и результаты измерения запылённости.
.
ССЫЛКИ
- ↑ EPA [2003]. AP 42, Fifth Edition, Compilation of air pollutant emission factors, volume 1: stationary point and area sources. United States Environmental Protection Agency. Chapter 11: Mineral Products Industry; Background Information for Revised AP-42 Section 11.19.2, Crushed Stone Processing and Pulverized Mineral Processing [online] available at URL: Date accessed 09/04/2008.
- ↑ NIOSH [2003]. Handbook for dust control in mining. By Kissell FN. Pittsburgh, PA: U.S. Department of Health and Human Services, Centers for Disease Control and Prevention, National Institute for Occupational Safety and Health, NIOSH Information Circular 9465, DHHS, (NIOSH) Publication No. 2003–147.
- ↑ USBM [1978]. Improved dust control at chutes, dumps, transfer points and crushers in noncoal mining operations. U.S. Department of the Interior, Bureau of Mines Contract No. H0230027. NTIS No. PB 297–422.
- ↑ 4,0 4,1 4,2 USBM [1974]. Survey of past and present methods used to control respirable dust in noncoal mines and ore processing mills—final report. U.S. Department of the Interior, Bureau of Mines Contract No. H0220030. NTIS No. PB 240 662.
- ↑ Yourt GR [1969]. Design for dust control at mine crushing and screening operations. Canadian Mining Journal 90(10):65–70. www.canadianminingjournal.com
- ↑ Anderson DM [1964]. Dust control design by the air induction method. Industrial Medicine and Surgery. 33:68–72.
- ↑ 7,0 7,1 Goldbeck LJ, Marti AD [1996]. Dust control at conveyor transfer points: containment, suppression and collection. Bulk Solids Handling 16(3):367–372.
- ↑ Burton DJ, ed. [1999]. Hemeon's plant & process ventilation. 3 rd ed. Boca Raton, Florida: Lewis Publishers.
- ↑ Wills BA [2008]. Wills' Mineral Processing Technology, 7 th ed. Oxford, UK: Elsevier Ltd.
- ↑ 10,0 10,1 ACGIH [2010]. Industrial ventilation: a manual of recommended practice. 27th ed. Cincinnati, Ohio: American Conference of Governmental Industrial Hygienists.
ГЛАВА 5. Перевозка и перемещение материала[править]
Для перемещения минерального сырья с одного места на другое существует множество разнообразных типов оборудования. Сам перемещаемый материал может быть очень разнообразен – от необработанной руды до полностью переработанного готового конечного продукта. У разных методов перемещения материала есть свои сильные и слабые стороны. Для правильного выбора подходящего оборудования нужно учесть свойства перемещаемого материала, дальность перемещения, вид перемещения (то есть – по горизонтали, по вертикали, наклонно вверх или наклонно вниз). В этой главе рассматриваются наиболее часто используемые системы (перемещающие материал), и способы уменьшения попадания пыли в воздух и просыпания материала при их работе.
Ленточные конвейеры[править]
При переработке минеральных полезных ископаемых одним из наиболее часто используемых видов оборудования являются ленточные конвейеры. Конвейеры и соответствующие места перегрузки материала могут стать источниками значительного количества респирабельной пыли, и главным источником неорганизованного попадания пыли в атмосферу. Для предотвращения этого работодатель должен бороться с загрязнением воздуха путём герметизации оборудования, предотвращения попадания пыли в воздух, или её улавливания. При этом особого внимания требуют места перегрузки материала. Ленточный конвейер состоит из различных составных частей (Рис. 5.1).
При перемещении материала ленточными конвейерами пыль попадает в воздух в трёх случаях: при просыпании материала, при его падении вниз с нижней стороны холостой ветви ленты (к которой он прилип или прицепился) и попадание пыли в воздух в местах перегрузки материала (Рис. 5.2). Для предотвращения неконтролируемого загрязнения атмосферы пылью нужно бороться с её попаданием в воздух всеми тремя путями.
Предотвращение просыпания материала[править]
Просыпание материала может происходить или в местах его перегрузки, или при перемещении – из-за недостаточных усилий для его предотвращения. Просыпание при перемещении обычно связано с падением материала (прилипшего к ленте) с её холостой ветви, и это будет рассмотрено позже.
Чаще всего просыпание происходит в местах перегрузки. В принципе, материал может скапливаться везде (по длине конвейера), но обычно он сваливается около ведущего ролика. Для эффективного предотвращения просыпания материала в местах перегрузки используют 4 способа:
- Подача материала на движущийся конвейер должна проводиться так, чтобы направление движения и скорость подаваемого материала совпадали с этими параметрами принимающего конвейера.
- Материал должен подаваться на середину ленты конвейера.
- Уменьшение высоты падения материала на конвейер уменьшает удар, и уменьшает вовлечение воздуха в движение материала.
- Использование боковых оградительных планок (skirtboard, "skirting") позволяет регулировать загрузку материала на ленту при его подаче.
Предложенные способы рассмотрены более подробно ниже.
1. Подача материала на конвейер в том направлении, в каком движется лента, и с той же скоростью. На Рис. 5.3 показана схема перегрузки материала с верхнего конвейера (с ведущего ролика конвейера) на нижний конвейер (конец, где находится ведомый ролик) – простейший случай, когда у обоих конвейеров совпадают направления движения, и они находятся на одной линии. Материал подаётся на нижний конвейер в направлении его движения, и скорости движения конвейеров должны различаться в минимальной степени.
А если направления движения материала на двух конвейерах, например, перпендикулярны, то добиться соответствия скорости и направления движения подаваемого материала и принимающего конвейера – гораздо труднее. (При перегрузке материала) часто используют (impact beds) – приспособления для предотвращения повреждения конструкции падающим материалом. Они также позволяют управлять направлением и скоростью движения падающего материала (Рис. 5.4).
Иногда вблизи ленты принимающего конвейера размещают изогнутые пластинки (curved plates) для более точного направления движения подаваемого материала. С помощью таких пластин и (impact beds) можно заставить материал двигаться в том же направлении, что и принимающий конвейер, и регулировать его размещение на ленте.
2. Размещение материала на середине ленты принимающего конвейера. Для предотвращения просыпания крайне важно размещать его в центре ленты. Это сводит к минимуму риск просыпания материала в местах его перегрузки. Если материал будет находиться ближе к одной из сторон ленты, чем к другой (Рис. 5.6), он может сместить ленту вбок с конвейера.
3. Уменьшение высоты падения материала на ленту конвейера, что уменьшает его удар о ленту и уменьшает вовлечение воздуха в движение (см. Рис. 5.7). Высота падения – это расстояние, с которого материал падает до встречи с конвейером. Большая высота падения позволяет частицам маленького размера отделяться от перемещаемого материала, а при маленькой высоте падения у маленьких частиц меньше времени для отделения, и это уменьшает пылеобразование. Кроме того, падение с большей высоты способствует провисанию ленты конвейера. А при провисании ленты материал захватывается и удерживается “ложбинами” между роликами, что в свою очередь приводит к не контролируемому пылеобразованию, а также к разрушению ленты. Для решения этих проблем могут использоваться противоударные опоры (impact cradles), или (impact beds). В такой противоударной опоре может быть гладкая верхняя поверхность (соприкасающаяся с движущимся ремнём) под которой находятся амортизирующие слои резины, поглощающие удары (Рис. 5.8). А если удары слабые, или почти отсутствуют, то могут использоваться только лёгкие боковые опоры (Рис. 5.9). Для разработки эффективных противоударных опор используйте стандарт ассоциации изготовителей транспортировочного оборудования (Conveyor Equipment Manufacturers Association, CEMA) Standard 575–2000 (Таблица 5.1 и Рис. 5.7)[5- 1].
Обозначение
Code |
Уровень нагрузки
Rating |
Сила удара†, Н
[Lbf] |
Параметр, равный произведению массы на высоту падения W x h, кг×м
[lb-ft] |
---|---|---|---|
L | маленькая | <37810 [<8,500] | <27.7 [<200] |
M | средняя | 37810÷53378 [8,500÷12,000] | 27.7÷138.4 [200÷1,000] |
H | большая | 53378÷75620 [12,000÷17,000] | 138.4÷276.8 [1,000÷2,000] |
† перевод единиц силы: 1 Lbf = 4.45 Н ( http://physics.nist.gov/Pubs/SP811/appenB9.html#FORCE )
4. Использование боковых оградительных планок (skirtboard, skirting) для регулирования размещения материала, подаваемого на конвейер. Боковые бортики (skirting, Рис. 5.10) – это продолжение стенок загрузочного лотка, которое используется для ограничения размещения мелких частиц руды и пыли в месте перегрузки, и для ограничения пространства, в котором происходит укладка материала на ленту – чтобы он размещался в центре ленты в требуемом виде.
Эти бортики используются для того, чтобы удерживать материал (в нужном месте) после того, как он покинет загрузочный лоток и до того, как он приобретёт ту же скорость, что и лента конвейера. Обычно эти планки изготавливают из стали и размещают так, чтобы нижний край был немного выше ремня. А этот зазор в свою очередь герметизируется с помощью гибкого эластичного уплотнения – ленты, прикрепляемой (болтами или зажимом) к внешней стенке (кожуха, см. Рис. 5.10).
Теоретически, боковое ограждение по длине (вдоль ленты) должно достигать ведущего ролика конвейера – за пределы того места, где сброшенный на ленту материал примет установившуюся форму (профиль). В ассоциации изготовителей транспортировочного оборудования CEMA отметили, что длина такого ограждения зависит от отличий в скоростях между материалом (в тот момент, когда он достигает ленты) и лентой конвейера[5- 1]. Ассоциация рекомендует использовать ограждение длиной по 60 см на каждые 0.5 м/мин скорости ленты (2 feet for every 100 fpm) при минимальной длине не менее 0.9 м. Выполнение этой рекомендации, разработанной на основе опыта перемещения “легко транспортируемых материалов” (может) оказаться недостаточным для тех материалов, которые обычно требуют пылеулавливания, или материалов, которые могут катиться по ленте конвейера – тех, работа с которыми труднее. Также есть другие рекомендации. Так в Инженерных войсках США (U.S. Army Corps of Engineers) в техническом руководстве по проектированию паровых котельных установок (Design of Steam Boiler Plants) рекомендует использовать такие бортики, которые простираются на 1.5 м (5 feet) с места падения материала, и рекомендуют увеличивать эту длину на 30 см на каждые 0.5 м/с скорости конвейерной ленты (1 foot for every 100 fpm)[5- 2].
Сравним рекомендации этих двух организаций, полученные опытным путём (Таблица 5.2). При скорости ленты 3 м/с (600 fpm) CEMA рекомендует длину ограждения 3.66 м (12 feet), а Руководство Инженерных войск – 3.35 м (11 feet). Хотя отличие в 31 см выглядит незначительным, на практике оно может вылиться в различие между отсутствием просыпания материала и значительным просыпанием материала. Поэтому в каждом случае нужно рассмотреть все обстоятельства индивидуально, и главное - учесть поведение материала в условиях его перемещения.
CEMA | Army Corps of Engineers |
---|---|
61 см ограждения на каждые 0.5 м/с скорости ленты конвейера.
При скорости 3 м/с получим: 61×(3/0.5) = 366 см |
152 см плюс 30.5 см на каждые 0.5 м/с скорости ленты конвейера.
При скорости 3 м/с получим: 152 + 30.5×(3/0.5) = 335 см |
Наклонное расположение боковых частей ограждения ленты конвейера (inclined skirting design) при котором наклон ленты ограждения составляет около 30° по отношению к вертикали, предпочтительнее стандартного вертикального ограждения из-за меньшего износа.
Противопылевое ограждение (dust curtains), Рис. 5.11 – это эффективный и недорогой способ создания укрытия, предотвращающего распространение пыли, и такие ограждения должны устанавливаться и на входе, и на выходе из места подачи материала на ленту конвейера.
В некоторых руководствах по проектированию рекомендуют:
- Создавать скорость воздуха, отсасываемого из укрытия или загрузочного лотка, не более 2.5 м/с (500 fpm) чтобы свести к минимуму всасывание крупных частиц [Yourt 1990].
- При устройстве ограждения ленты конвейера с помощью занавесей из листов резины, его порой делают двойным. В этом случае расстояние между двумя занавесями (с одной стороны) должно быть не меньше ~450 мм (~18 inches) чтобы между ними было достаточно большое “мёртвое пространство”, позволяющее пыли оседать[5- 3].
- Занавеси перед местом подачи материала на конвейер должны располагаться (по направлению движения конвейерной ленты) так, чтобы увеличить объём ограниченного пространства.
- А занавеси после места выгрузки материала на конвейер должны быть как минимум на 25 мм (1 дюйм) выше верха насыпанного на конвейер материала[5- 3].
Унос материала, прилипшего к ленте, её холостой ветвью[править]
Та часть материала, которая прилипла или прицепилась к ленте конвейера, и осталась на ней после прохождения ведущего ролика (то есть – на холостой ветви), называется “унесённая обратно” (carryback). Этот материал склонен падать с нижней стороны холостой ленты при её прокатывании по поддерживающим холостым роликам. Из-за этого (под и около) конвейера накапливаются кучи (такого просыпавшегося) материала, и его нужно убирать, а это увеличивает воздействие пыли на рабочих. Мелкодисперсная респирабельная фракция этого падающего материала попадает в воздух, и это увеличивает концентрацию пыли. Для предотвращения этого необходимо заставить прилипший материал упасть сразу за ведущим роликом – до того, как он начнёт падать при прохождении холостых поддерживающих роликов, и станет загрязнять воздух и/или заставлять рабочих убирать просыпавшийся материал (что связано с воздействием пыли).
Главный способ борьбы с обратным уносом – очистка ленты сразу после её прохождении последнего или ведущего ролика (то есть – сразу после выгрузки материала с конвейера). Для очистки ленты в основном используют механические скребки, или щётки, или ленту моют.
Скребки для очистки ленты
Многообразие видов скребков для очистки ленты так велико, что его трудно описать, и такое описание не является целью настоящего руководства. Поэтому мы опишем (только) основные типы и размещение скребков. Хотя разные производители изготавливают различные системы очистки конвейеров, которые имеют разные торговые названия, они выполняют одну и ту же функцию – уменьшают количество материала, остающегося на поверхности ленты после выгрузки материала с конвейера.
(Прилипший) материал может или соскабливаться, или отшелушиваться от ленты конвейера. При соскребании, скребок устанавливается под углом к направлению движения ленты конвейера (Рис. 5.12).
Для эффективного удаления прилипшего материала с ленты могут использоваться многоступенчатые скребковые системы, в которых есть пред-очиститель (находится у ведущего ролика и удаляет большую часть материала), и затем дополнительные скребки, которые обеспечивают окончательную очистку. Дополнительные скребки могут устанавливаться или (сразу) после ведущего ролика – когда лента сходит с него, или дальше от него. Для того, чтобы скребки эффективно очищали ленту, и чтобы её износ не был чрезмерным, давление лезвия скребка на ленту должно быть небольшим[5- 3]. При большой концентрации пыли нередко используют и два, и три скребка, размещая их в разных местах (для более полной очистки холостой ветви ленты конвейера от уносимого прилипшего материала)[5- 4].
При очистке ленты желательно чтобы удаляемый прилипший материал попадал в поток используемого материала с помощью лотка для счищенного материала (Рис. 5.13). Такой лоток должен быть достаточно большим – чтобы улавливать и направлять счищенный материал, и он должен быть достаточно круто наклоненным – чтобы предотвратить скапливание счищенного материала (иногда для предотвращения скапливания используют электровибраторы).
Промывка ленты конвейера
Ряд исследований показал, что крупные частицы материала легко удаляются соскребанием, но мелкие частицы респирабельного размера стремятся остаться прилипшими к ленте конвейера. Для удаления частиц, которые плохо соскребаются, может использоваться промывка ленты. Для этого на ленту распыляется вода как раз перед тем, как начнётся соскребание прилипшего материала. В руководстве Martin Engineering, Foundations: The Practical Resource for Cleaner, Safer, More Productive Dust & Material Control[5- 5] вопросам, относящиеся к работе систем промывки ленты конвейера, отведена целая глава, где они подробно рассмотрены.
Проектирование и эксплуатация конвейеров[править]
При использовании ленточных конвейеров нужно решать ряд проблем, связанных с количеством лент и общим полным расстоянием, на которое должен перемещаться перерабатываемый материал. Некоторые конвейеры устанавливаются на открытом воздухе – там, где попадание пыли в воздух менее важно, чем попадание пыли в воздух закрытых помещений. Другая проблема, относящаяся именно к ленточным конвейерам – это их способность становиться мощными источниками пыли при их загрузке тяжёлой рудой, или когда они почти пустые. Чтобы конвейеры не становились источником пыли, от обслуживающего персонала требуется много внимания к их техническому состоянию, своевременная замена и ремонт износившихся и разрушившихся частей, в том числе и ленты конвейера. При осмотрах и техобслуживании основное внимание (должно) уделяться тому, чтобы обеспечить нормальный режим работы всех частей системы. Материал может высыпаться из лотков через отверстия, образовавшиеся в результате износа или абразивного истирания, и даже через маленькие отверстия, образовавшиеся при выпадении болтов, а также через большие отверстия (не закрытые люки). Всё это может стать источником загрязнения воздуха пылью. В каких-то случаях для обеспечения герметичности укрытия может потребоваться полная замена всего загрузочного лотка.
Сращивание концов лент конвейера[править]
Для получения замкнутой петли, у каждой ленты конвейера должно быть хотя бы одно место, где её концы соединяются. А из-за разрушения лент у них нередко бывает более одного места соединения концов. При использовании ленточных конвейеров при добыче минеральных полезных ископаемых для соединения концов часто используют механическое соединение, или вулканизацию (как показано на Рис. 5.14).
Места механического соединения ленты конвейера часто становятся местами значительного просыпания материала и сильного пылеобразования, так как материал может просыпаться через маленькие отверстия в месте соединения. Чтобы избежать такого просыпания можно использовать соединение с помощью вулканизации. При использовании соединения таким способом целостность ленты не нарушается, и обычно не изменяется ни форма, ни размеры лент. Для предотвращения просыпания материала и пылеобразования рекомендуется соединять концы ленты с помощью вулканизации – когда это допускается другими обстоятельствами.
Проектирование мест перегрузки[править]
Для уменьшения загрязнения воздуха пылью часто используют устройство укрытий на обоих концах конвейера, так как это эффективно снижает загрязнение воздуха пылью и ограждает опасные места подвижного оборудования. Если невозможно предотвратить образование пыли в местах перегрузки материала, требуется использование эффективной вентиляции. При проектировании укрытий важно правильно определить их размер, так как материал, сбрасываемый на конвейер, увлекает за собой воздух (эффект Вентури), и это может привести к созданию избыточного давления в укрытии недостаточно большого размера. Укрытия конвейера и мест перегрузки материала могут быть или полными, или неполными – в зависимости от конструкции транспортной системы.
Хотя (перемещение материала) ленточным конвейером выглядит как простой процесс, но при неудачном проектировании и размещении укрытий мест перегрузки материала они могут стать источниками сильного загрязнения воздуха пылью. Ниже рассмотрены некоторые важные обстоятельства, относящиеся к проектированию эффективных мест перегрузки или лотков при использовании местных вентиляционных отсосов (см. также Рис. 5.15):
- Оказалось, что для уменьшения уноса и всасывания крупных частиц входное отверстие воздуховода вентиляционной системы должно размещаться в кожухе укрытия на расстоянии не менее 1.8 м (6 футов) от места сбрасывания материала[5- 6]. С той же целью скорость движения воздуха у основания конусного раструба всасывающего отверстия воздуховода должна быть не более 2.5 м/с (500 fpm)[5- 7].
- При проектировании мест перегрузки и необходимости оставить часть проёмов в укрытии открытыми в них должна поддерживаться скорость воздуха (внутрь) не менее 1/м/с (200 fpm) чтобы предотвратить распространение пыли из укрытия наружу[5- 8]. А канадская ассоциация The Mining Association of Canada (MAC) рекомендует использовать скорость в проёмах, на 25% большую указанной выше величины (1.25 × 1 м/с / ×200 fpm)[5- 6].
- Важно свести число отверстий к минимуму чтобы сохранить достаточно большую скорость всасывания воздуха в отверстиях и проёмах. Для этого могут использоваться (подвесные) пластиковые ленты, и другие средства. Рекомендуется делать укрытия мест перегрузки достаточно большими, чтобы скорость движения воздуха в (таком) укрытии была менее 1 м/с (200 fpm)[5- 3]. В укрытиях большего размера больше места для затухания и рассеивания воздушных потоков. Если укрытие будет слишком маленького размера, то (движение воздуха внутри такого укрытия) будет стимулировать вытекание загрязнённого воздуха из укрытия наружу, вынося частицы пыли в воздух рабочей зоны.
- Места перегрузки материала должны быть такого размера, чтобы это позволяло материалу пересыпаться без засорения и без образования пробок и засоров. На основе накопленного опыта считается, что для предотвращения засоров ширина лотка должна быть минимум в три раза больше максимального размера кусков материала[5- 9].
- Ограждение (skirtboard) в месте перегрузки должно быть таким высоким и таким длинным, чтобы это позволяло хотя бы части пыли осесть под действием силы тяжести. При маленькой скорости ленты конвейера можно использовать опытное правило – по 60 см длины на каждые 0.5 м/с (100 feet/min) скорости ленты[5- 3]. Если скорость ленты конвейера больше, чем вычисленная скорость движения воздуха, то (длина ограждения в месте перегрузки) должна быть по 0.9 м на каждые 0.5 м/с скорости ленты конвейера (100 feet/min)[5- 3].
- Место выгрузки материала должно быть сконструировано так, чтобы он падал на наклонную поверхность, или на специальные приспособления, предотвращающие разрушение конструкции из-за ударов (impact bed). В качестве таких приспособлений могут использоваться места, позволяющие материалу скапливаться – так, что удар падающих кусков приходится по уже скопившемуся материалу, а не по элементам конструкции. Это уменьшает разрушение, износ и истирание конструкции (Рис. 5.16).
- Всеми возможными способами следует избегать падения материала с высоты. Для этого можно использовать ступенчатые места перегрузки (rock ladders), телескопические устройства подачи материала, лотки для спуска материала спиралеобразной формы, и такие лотки подачи материала в бункер, которые входят в бункер через проём (для подачи материала) и затем внутри бункера спускаются до его нижней части.
- Нужно избегать любых резких изменений направления движения продукта.
Для эффективного предотвращения выноса пыли из укрытия в окружающее пространство важно правильно определить то, сколько воздуха нужно отсасывать из укрытия. Общий расход отсасываемого воздуха Qtot можно вычислить с помощью уравнения 5.1[5- 3]:
- Qtot = Qdis + Qind + Qgen (Уравнение 5.1) (СИ, IP)
- где Qtot = общий расход отсасываемого воздуха, м3/с (cubic feet per minute);
- Qdis = вычисленный расход вытесняемого воздуха, м3/с (cubic feet per minute);
- Qind = вычисленный расход воздуха, вовлекаемого в движение, м3/с (cubic feet per minute); и
- Qgen = расход воздуха, перемещаемого движущимися частями оборудования, м3/с (cubic feet per minute).
Расход вытесняемого воздуха возрастает при возрастании объёмного расхода подаваемого материала. Его можно вычислить с помощью уравнения 5.2[5- 3]:
- Qdis = массовый расход материала, кг/сек / насыпная плотность, кг/м3 (Уравнение 5.2) (СИ)
- Qdis = массовый расход материала, (lb/min) / насыпная плотность, (lb/ft3) (Уравнение 5.2) (IP)
(Ответ зависит от использованных единиц измерения - при подстановке кг/м3 и кг/с получаются м3/с).
При движении материала на ленте конвейера он переносит с собой небольшое количество воздуха, находящегося в пустотах между частицами материала. А при сбросе материала с конвейера каждая из частиц начинает увлекать за собой больше воздуха. При достижении материалом поверхности (на которую его сбросили), этот вовлечённый в движение воздух продолжает перемещаться, создавая значительное избыточное давление при своём растекании от центра места сброса материала. Уравнение 5.3 позволяет вычислить – какой расход вовлечённого в движение воздуха[5- 3]:
- Qind = 0.1157 × Au × ( R × S2 / D )1/3 (м3/с) = 416.5 × Au × ( R × S2 / D )1/3 (м3/час) (Уравнение 5.3) (СИ)
:Qind = 10 × Au × ( R × S2 / D )1/3 (Уравнение 5.3) (IP)
((коэффициенты 0.1157 и 416.5 используется вместо коэффициента 10 для исходных данных в метрах и кг/сек; а коэффициент 10 – для исходных данных в футах и тоннах/час, см. Уравнение 1.2)
- где Qind = расход воздуха, вовлекаемого в движение, м3/с, м3/час (cubic feet per minute);
- Au = площадь открытых проёмов в укрытии, м2, (square feet) (где воздух вовлекается в укрытие из-за увлечения падающим материалом);
- R = расход подаваемого материала, кг/сек (тонн в час);
- S = высота свободного падения материала, м (feet); и
- D = средний диаметр кусков материала, м (feet).
Также движение воздуха Qgen может возникать из-за перемещения частей оборудования, которое подаёт материал в место перегрузки (например – движение частей дробилки), и такое движение оборудование может действовать на воздух как вентилятор. Дополнительную информацию о том, какое количество воздуха перемещается при движении частей оборудования, можно получить у его изготовителей.
Распыление воды для предотвращения попадания пыли в воздух[править]
Как уже более подробно обсуждалось в главе 2 “Обеспыливание с помощью воды”, распыление воды может использоваться или для предотвращения попадания пыли в воздух; или для улавливания той пыли, которая уже попала в воздух. При правильном проектировании, удачной установке и правильном применении распыление воды может стать эффективным и недорогим способом снижения концентрации пыли при работе конвейеров. Чаще всего применение распыления воды сводится к подаче воды на продукт, находящийся на ленте конвейера (с охватом всей ширины материала на ленте) для его увлажнения, и это оказывается довольно эффективно. При использовании распыления воды рекомендуется:
- Не использовать форсунки с большим расходом и при большом давлении воды. Энергия движущейся воды передаётся частицам материала, и это увеличивает пылеобразование[5- 3].
- Для того, чтобы степень увлажнения материала была оптимальной, нужно её изменять и искать оптимальное значение. Можно начать с такой подачи воды, чтобы влажность материала была 1%. При чрезмерном увлажнении может происходить слипание материала, и при низких температурах это может негативно повлиять на работоспособность конвейера.
- Результаты некоторых исследований показали, что увлажнение холостой ветви ленты конвейера уменьшает попадание пыли в воздух. Это уменьшает попадание пыли с поддерживающих ленту роликов ременных приводов и шкивов.
- Установка форсунок вверху (для увлажнения материала) и внизу (для уменьшения попадания пыли от поддерживающих роликов) в одном и том же месте конвейера может оказаться очень эффективной[5- 10][5- 11]. Это также удобно с точки зрения монтажа и экономии средств.
- Чаще всего используют форсунки, у которых веерная форма факела, так как это сводит к минимуму объём добавляемой воды при одинаковом охвате. Правильно подавать воду на материал до места, где происходит попадание пыли в воздух (места перегрузки или сброса материала), так как при “перемешивании” воды и материала увеличивается площадь смоченной поверхности кусков, что уменьшает попадание пыли в воздух.
- Использование большего числа форсунок с меньшим расходом воды, и установка их на небольшом расстоянии от материала более выгодна, чем использование меньшего числа форсунок большей производительности[5- 12].
Для улавливания пыли, уже попавшей в воздух, используется распыление или не обработанной воды, или воды с добавками химических реагентов (уменьшающих поверхностное натяжение), что приводит к образованию тумана или пены (предотвращающей попадание частиц пыли в воздух). Такое применение распыления воды встречается реже, чем (распыление для увлажнения) из-за больших расходов и возможных проблем, связанных с химическим загрязнением (материала).
Винтовые конвейеры[править]
Screw conveyors
Винтовые конвейеры – один из наиболее старых и простых механизмов для перемещения сыпучего материала (Рис. 5.17). Он состоит из шнека, вращающегося в неподвижном жёлобе (также разработаны конвейеры, в которых шнек неподвижен, и вокруг него вращается цилиндрический корпус). Подаваемый в жёлоб материал перемещается вдоль его оси за счёт вращения шнека. Винтовые конвейеры могут располагаться горизонтально, вертикально или наклонно.
Обычно полость, в которой находится шнек винтового конвейера, полностью герметизируется (кроме открытых мест загрузки и выгрузки), и при правильной конструкции мест перегрузки можно предотвратить попадание пыли в воздух. Для крепления крышки винтового конвейера обычно используют болты и гайки. Но для предотвращения попадания пыли в воздух нужно устанавливать самоклеющуюся неопреновую резиновую прокладку.
При правильном проектировании и хорошем техобслуживании корпуса, уплотнений и мест загрузки/выгрузки, винтовые конвейеры не просыпают материал и не являются источниками пыли. Просыпание материала может произойти только при образовании зазора в месте входа вала шнека в корпус. Для поддержки вала шнека нужно использовать подшипниковую опору, находящуюся вне корпуса винтового конвейера (Рис. 5.18). Если есть зазор между валом шнека и корпусом, и подшипниковый узел находится вне корпуса, можно установить сальниковое уплотнение. Это предотвратит просыпание материала и защитит подшипник.
Ковшовые элеваторы[править]
Bucket elevators
Типичный ковшовый элеватор состоит из большого числа ковшей, прикреплённых к цепи или к ремню (Рис. 5.19), который движется между верхним и нижним шкивами. При загрузке ковшей они зачерпывают материал из нижней части корпуса элеватора, или из (потока) материала, подаваемого в корпус элеватора. Материал высыпается из ковшей при прохождении ими верхнего шкива.
Стальной кожух элеватора закрывает весь механизм и тем самым эффективно предотвращает распространение пыли при его работе – при отсутствии отверстий и проёмов. Источниками пыли обычно становится или нижняя часть (“башмак”) корпуса элеватора, где в него загружается подаваемый материал, или верхняя часть, где материал выгружается.
Для предотвращения выноса пыли в нижней части элеватора нужно грамотно сконструировать ту её часть, которая находится между подающим материал оборудованием и элеватором (подобно тому, как это делается у ленточных конвейеров). Можно значительно уменьшить пылеобразование, если уменьшить высоту, с которой падает материал, и если подавать материал в нижнюю часть корпуса элеватора постепенно.
Для предотвращения выноса пыли из верхней части элеватора требуется эффективная вентиляция (см. главе 1 “Принципы пылеулавливания”), а также нужно аккуратно спроектировать участок между местом выгрузки материала и получающим его оборудованием. Рекомендуется отсасывать не менее 0.5 м3/с на каждый 1 м2 поперечного сечения корпуса элеватора (100 cfm for every square foot of casing cross-sectional area)[5- 13]. Отсос запылённого воздуха из корпуса элеватора может проводиться в его верхней части, над ведущим шкивом (Рис. 5.20). При скорости ремня более 1 м/с (200 fpm) может потребоваться увеличенный расход воздуха. Если высота элеватора больше 9 м (30 feet), то нужно сделать второй отсос воздуха из корпуса – сбоку над нижним шкивом. В месте загрузки материала в элеватор тоже нужен местный вентиляционный отсос.
Пневмотранспорт[править]
В пневмотранспортных системах для перемещения материала используют трубы, по которым его двигает перепад давления воздуха (избыточное давление или разрежение). При использовании избыточного давления пневмотранспортные системы могут быть двух видов – использующие разбавленную фазу (dilute phase), или фазу с большой плотностью (dense phase). В первом случае перемещается воздух, содержащий относительно небольшую долю материала, а во втором случае доля материала в перемещаемой смеси материала с воздухом большая. Первый способ может использоваться тогда, когда скорость воздуха в трубах достаточно большая для перемещения взвешенных в нём частиц материала. Во втором случае не требуется, чтобы воздух сдувал и уносил частицы материала. Материал лежит в нижней части горизонтальных труб системы, и иногда (медленно) перемещается. В системах, перемещающих воздух с небольшим содержанием материала обычно используется небольшое давление, которое можно получить с помощью вентилятора, а в системах, перемещающих смесь с большой долей материала, используется источник сжатого воздуха.
При подаче материала в систему с избыточным давлением он перемещается там до сепаратора (циклона, тканевого фильтра или другого сухого пылеуловителя). Сепаратор отделяет частицы материала и направляет их в бункер, а воздух выходит через выпускное отверстие в циклоне или фильтре (Рис. 5.21).
Так как пневмотранспортные системы, работающие при избыточном давлении, полностью загерметизированы, и поэтому они обычно не являются источником загрязнения воздуха пылью (исключение – места, изношенные до появления отверстий). Так как наиболее интенсивный износ труб пневмотранспортных систем происходит в местах изменения направления движения, нужно делать такие места с большим радиусом кривизны, и из прочного материала. Для предотвращения износа мест изменения направления движения материала из-за истирания используют разные технические решения (Рис. 5.22). Для предотвращения чрезмерного абразивного износа, места изменения направления движения могут облицовываться специальными износостойкими или керамическими материалами. В пневмотранспортных системах с низким давлением также могут быть утечки пыли в местах соединений. Для предотвращения этого нужно использовать самоклеящиеся неопреновые прокладки.
Системы, перемещающие смесь материала с воздухом при большой доле первого, работают при избыточном давлении, и поэтому при подаче в них материала нужно использовать какое-то механическое приспособление, предотвращающее перетекание воздуха и материала в ту ёмкость, из которой он подаётся в пневмотранспортную систему. Такими приспособлениями могут быть шлюзовый роторный питатель, или двойная мигалка (rotary valve or double dump valve) (Рис. 5.23). У этих устройств есть подвижные части и уплотнения, которые могут быстро изнашиваться и требовать частого ремонта и техобслуживания. Разбирание этих устройств также может привести к сильному запылению воздуха и воздействию пыли на слесарей-механиков, и это требует прерывания работы технологического оборудования.
Нередко хорошей альтернативой механическим питателям при подача материала в пневмотранспортную систему становятся эжекторы Вентури. Эжекторы преобразуют избыточное давление сжатого воздуха в разрежение, используемое для перемещения материала в транспортной линии (Рис. 5.24 и 5.25). В пневмотранспортном оборудовании нет подвижных частей, и обычно оно требует минимального техобслуживания и небольших затрат времени на ремонт. В пылеуловителях, мельницах/измельчителях, ленточных или вибрационных питателях и др. может использоваться эжектор вентури. Такие системы обычно проектируются изготовителем из-за необходимости учитывать особенности конкретного технологического производства.
Вакуумные системы обеспечивают чистый и эффективный сбор материала из транспортных средств (вагонов, грузовиков) и бункеров для переноса в другое оборудование. Так как трубы такой системы находятся под разрежением, то обычно проблем с утечкой пыли не возникает. Для отделения материала от воздуха в конце такой системы используют циклоны или тканевые фильтры. Тип отделителей-сепараторов определяется требованиями к степени разделения.
.
ССЫЛКИ
- ↑ 1,0 1,1 1,2 CEMA Standard 575–2000. Bulk material belt conveyor impact bed/cradle selection and dimensions. Ссылка.
- ↑ Swinderman RT, Goldbeck LJ, Marti AD [2002]. Foundations 3: the practical resource for total dust & material control. Neponset, Illinois: Martin Engineering. Martin Engineering Library
- ↑ 3,0 3,1 3,2 3,3 3,4 3,5 3,6 3,7 3,8 3,9 Goldbeck LJ, Marti AD [2010]. Dust control at conveyor transfer points: containment, suppression and collection. [1]. Date accessed August 23, 2010.
- ↑ Roberts AW, Ooms M, Bennett D [1987]. Bulk solid conveyor belt interaction in relation to belt cleaning. Bulk Solids Handling 7(3):355–362.
- ↑ Swinderman RT, Marti AD, Goldbeck LJ, Strebel MG [2009]. Foundations: the practical resource for cleaner, safer, more productive dust & material control. Neponset, Illinois: Martin Engineering Company. Martin Engineering Library
- ↑ 6,0 6,1 MAC [1980]. Design guidelines for dust control at mine shafts and surface operations. 3rd ed. Ottawa, Ontario, Canada: Mining Association of Canada.
- ↑ Yourt GR. [1990]. Design principles for dust control at mine crushing and screening operations. Canadian Mining J 10:65–70.
- ↑ USBM [1974]. Survey of past and present methods used to control respirable dust in noncoal mines and ore processing mills—final report. U.S. Department of the Interior, Bureau of Mines Contract No. H0220030. NTIS No. PB 240 662.
- ↑ USBM [1987]. Dust control handbook for minerals processing. U.S Department of the Interior, Bureau of Mines. U.S. Bureau of Mines Contract No. J0235005. Martin Marietta Corporation and Marcom Associates, Inc.
- ↑ Courtney WG [1983]. Single spray reduces dust 90%. Coal Mining & Processing. June, pp. 75–77.
- ↑ Ford VHW [1973]. Bottom belt sprays as a method of dust control on conveyors. Min Technology (United Kingdom) 55(635):387–391.
- ↑ NIOSH [2003]. Handbook for dust control in mining. By Kissell FN. Pittsburgh, PA: U.S. Department of Health and Human Services, Centers for Disease Control and Prevention, National Institute for Occupational Safety and Health, NIOSH Information Circular 9465, DHHS, (NIOSH) Publication No. 2003–147.
- ↑ ACGIH [2010]. Industrial ventilation: a manual of recommended practice for design. 27th ed. Cincinnati, OH: American Conference of Governmental Industrial Hygienists.
ГЛАВА 6. Фасовка[править]
Bagging
В этой главе рассмотрены те методы снижения воздействия пыли на рабочих, которые используются изготовителями продукции (из минеральных полезных ископаемых) при фасовке конечного продукта (для доставки потребителю) и складировании расфасованного продукта. Погрузка конечного продукта в ёмкости обычно называется “фасовка” (bagging). А складывание таких ёмкостей (мешков и т.п.) на паллеты (поддоны) для отправки потребителю называют паллетизированием (palletizing). Для фасовки используют разнообразные ёмкости, начиная от мешков 25 кг и заканчивая мягкими контейнерами, вмещающими более тонны материала. Обычно на поддоны укладывают ёмкости маленького размера (25÷50 кг и т.п.), а ёмкости большого размера в обычно грузят индивидуально, так как их перевозят по-отдельности. И заполнение ёмкостей материалом, и их укладка на поддоны может проводиться как вручную, так и механизировано – вплоть до полной автоматизации процесса. Попадание пыли в воздух при фасовке и укладке мешков 25÷50 кг на паллеты прямо влияет на количество пыли, вдыхаемое рабочими.
При переработке минеральных ископаемых воздействие пыли на рабочих, занятых фасовкой и укладкой мешков на поддоны, а также на рабочих, которые находятся рядом с местами фасовки и укладки – наиболее сильное. При снижении концентрации пыли при фасовке и укладке мешков одной из проблем является огромное многообразие используемых мешков и фасовочного оборудования. Заполнение мешков может проводиться как в простых машинах с ручным управлением наполнения одного мешка, так и в полностью автоматизированных фасовочных станциях, одновременно наполняющих несколько мешков.
Помимо воздействия респирабельной пыли при фасовке и укладке мешков, рабочие подвергаются значительному риску развития заболеваний опорно-двигательного аппарата из-за выполнения повторяющихся движений и поднимания тяжёлых мешков. Это стимулирует многих работодателей стремиться внедрять полностью автоматизированное или полу-автоматизированное оборудование для фасовки и укладки мешков.
Ёмкости (мешки) как источник пыли[править]
Чтобы решить проблемы повышенной запылённости при фасовке, нужно рассмотреть ряд вопросов, относящихся к выдуванию материала обратно из ёмкости, вытеканию материала из сопла загрузочного устройства (при уже убранном заполненном мешке), и загрязнённым мешкам. При фасовке и укладке на поддоны мешков весом 25 и 50 кг эти источники пыли прямо влияют на воздействие пыли на рабочих. В этом диапазоне массы (тары) для транспортировки материала используют ёмкости двух типов - с открытым верхом, и закрытые ёмкости с встроенным клапаном.
Мешки с открытым верхом подаются снизу вверх, и наполняются готовым продуктом. Мешки с открытым верхом обычно используют для транспортировки материала, состоящего из частиц большого размера - обычно крупнее 0.125 мм (120 mesh). При заполнении мешков с открытым верхом источниками пыли обычно является просачивание из загрузочного лотка (когда заполненный мешок убран), и унос пыли из открытого мешка перед его закрыванием. Иногда такие мешки с открытым верхом перемещают в приспособление (cage device) для установки в правильное положение перед закрыванием. Это перемещение тоже может привести к попаданию пыли в воздух. Так как такие ёмкости обычно используют для фасовки материалов с частицами большого размера, то обычно и запылённость при их наполнении не такая большая, как при наполнении мешков с клапаном (ёмкости с закрытым верхом).
При фасовке мешков с клапаном для эффективного уменьшения концентрации пыли нужно рассмотреть три основных источника пыли. Первый источник пыли - это обратный вынос запылённого воздуха из мешка (product blowback), который происходит при заполнении ёмкости, и который приводит к распространению пыли от клапана мешка в окружающее пространство. Этот обратный вынос происходит из-за появления в ёмкости избыточного давления (при её заполнении материалом, вытесняющим воздух), которое заставляет запылённый воздух вытекать из мешка наружу через его клапан рядом с выпускным отверстием, по которому материал подаётся в мешок. Вторым значительным источником пыли является вытекание из сопла для подачи материала в ёмкость - в то время, когда уже заполненный мешок убран. Обычно это называют "rooster tail" (петушиный хвост) из-за формы струи вытекающего из сопла продукта. Обе вышеописанные проблемы возникают из-за того, что при заполнении ёмкости в ней возникает избыточное давление воздуха. В обоих случаях пыль попадает в воздух и загрязняет наружную поверхность ёмкости. В результате из-за наличия пыли на наружной поверхности ёмкости она становится третьим важным источником пыли – уже при укладке мешков, и при выполнении любой другой работы с ними, в том числе и у конечного потребителя продукции. На Рис. 6.1 показано, как происходит обратный вынос запылённого воздуха из мешка, просыпание из заполненного сопла устройства загрузки и загрязнение наружной поверхности заполненного мешка. Если мешок слишком маленький, это приводит к большому выносу пыли из-за обратного выноса запылённого воздуха и из-за просыпания материала из сопла устройства загрузки, и это нужно учитывать при анализе источников загрязнения воздуха.
При заполнении мешков весом 25 и 50 кг одним из источников пыли становится клапан мешка. Клапан такой ёмкости - это встроенный ниппель, через которое сопло устройства подачи материала вставляется в мешок перед его заполнением (Рис. 6.2). От конструкции используемого клапана ёмкости зависит то, сколько пыли поступит в окружающее пространство за счёт обратного выноса материала и из-за просыпания из сопла загрузочного устройства. Как только мешок вынут из загрузочного устройства, масса материала, заполняющая объём мешка, давит на клапан мешка изнутри, стремясь закрыть его и не допустить просыпание материала наружу при транспортировке и укладке. Но нередко материал наполняет клапан мешка, и закрывается недостаточно плотно, что приводит к просыпанию продукта и утечкам пыли из клапана при перемещении ёмкости. Эта способность клапана предотвращать просыпание и просачивание у клапанов разных конструкций различна.
Наконец, источником пыли становятся разрушенные, протёртые и порванные мешки. При разрывании мешка в атмосферу цеха попадает много материала и пыли. Такое разрушение мешка может произойти, например, из-за заводских дефектов, в том числе плохого проклеивания, и неправильного хранения пустых мешков. Место разрыва сильно влияет на количество пыли, попадающее в воздух. Если мешок разрывается в процессе его наполнения, то это приводит к более сильному воздействию, чем разрыв при извлечении наполненного мешка (из приспособления для наполнения) и разрыв при транспортировке. Во всех случаях разрыв мешка приводит к поступлению в воздух большого количества пыли, и сильному воздействию на рабочих, находящихся рядом.
Влияние мешка на попадание пыли в воздух[править]
В конечном счёте на образование пыли и попадание её в окружающее пространство влияет ряд факторов, относящихся к мешку: его конструкция, наличие и характер перфорации, способа заполнения, и влияние дефектов / разрушения на образование пыли.
Конструкция мешка[править]
Для упаковки минеральных материалов чаще всего используют многослойные мешки из бумаги, и ниже мы будем рассматривать лишь их использование. Факторы, обсуждаемые при использовании мешков с клапаном, также относятся и к мешкам с открытым верхом.
Сама конструкция бумажного мешка сильно влияет на уменьшение запылённости во время фасовки. Состав бумаги, её пористость, количество использованных складок или слоёв, удельный вес или толщина использованных листов бумаги (от которых зависит прочность), конструкция клапана, наличие перфорации - всё это влияет на то, сколько пыли образуется или высвободится при фасовке.
За последние годы в области изготовления бумажных мешков произошло значительное улучшение технологии[6- 1]. Сейчас в отрасли стандартной используемой бумагой является крафт-бумага (natural kraft (NK) paper). При изготовлении 25 и 50-кг мешков обычно используют 3-4 слоя такой бумаги. Из-за слабой пористости такой бумаги воздух практически не проходит через неё, и при использовании мешков из крафт-бумаги для упаковки минеральных продуктов для предотвращения разрыва мешка под действием избыточного внутреннего давления мешок должен быть с отверстиями (перфорированный).
Другой разработкой стало использование растягивающейся крафт-бумаги (extensible kraft (EK) paper), которую иногда называют "высокоэффективной бумагой" (high performance paper). Эта бумага прочнее, так что при изготовлении мешков число слоёв можно уменьшить примерно на 30% по отношению к аналогичному мешку из обычной крафт-бумаги. Есть два способа для экономии на бумаге. Во-первых (так поступают чаще всего) можно изготавливать мешки с меньшим числом слоёв бумаги. Например, если вместо бумаги NK или FK использовать ЕК крафт-бумагу, то вместо обычных 3-4 слоёв можно ограничиться использованием двух слоёв бумаги. А с каждым уменьшением числа слоёв увеличивается пористость мешка, и он становится более воздухопроницаемым. Несмотря на свою популярность улучшенная крафт-бумага (ЕК) недостаточно хорошо пропускает воздух, и поэтому при многих видах фасовки нужно выпускать воздух из мешка наружу чтобы избежать его разрыва. Другой способ - уменьшение толщины (удельного веса) листов используемой бумаги.
В 1990-х была разработана специальная бумага (airflow extensible kraft (AEK) paper). Она такая же прочная, как и ЕК бумага, но она ещё и воздухонепроницаемая. Воздухопроницаемость новой бумаги является большим достоинством, так как это позволяет заполнить материалом весь мешок, не оставляя пустых мест, и за счёт этого можно использовать мешки меньшего размера. Эта пористая бумага значительно превосходит перфорированную по своей способности выпускать избыток воздуха, уменьшая его давление в (заполняемом) мешке. При использовании АЕК бумаги перфорация не нужна, и поэтому прочность мешка увеличивается (прирост до 20%). Чем быстрее воздух может выйти из мешка, тем быстрее можно наполнить мешок и сложить его на поддон. Это увеличивает производительность и экономит средства.
При использовании новой пористой бумаги АЕК скорость выхода воздуха из мешка в 3-4 раза больше, чем при использовании стандартной крафт-бумаги (NK или FK), а прочность та же самая. При наполнении мешка бумага работает как противоаэрозольный фильтр. Это позволяет материалу свободно заполнять мешок, воздух выходит из мешка, а пыль остаётся внутри, и не попадает в зону дыхания рабочих и в окружающее пространство. Из-за этого наружная поверхность такого мешка чище. При анализе того, как можно снизить запылённость при фасовке за счёт факторов, относящихся к мешку, лучшим выбором является использование пористой крафт-бумаги АЕК.
Перфорация мешка[править]
Чтобы заполнить мешок материалом при фасовке, нужно выпустить наружу воздух, захваченный в мешке подаваемым туда материалом, и перемешанный с ним. Для выпуска воздуха из мешка при подаче в него материала в бумаге, из которого изготовлен мешок, делают вентиляционные отверстия (перфорацию). Для этого при изготовлении многослойных мешков стенки протыкаются для получения маленьких вентиляционных отверстий, что позволяет воздуху выходить из мешка по мере его наполнения.
Широко используют два вида перфорации - прокалывание отверстий по всей площади мешка, и прокалывание около клапана. В обоих случаях прочность бумаги, из которой сделан мешок, снижается (снижение на <20%).
Перфорация всей поверхности мешка
Для оценки эффективности использования мешка важно рассмотреть использование перфорации всего мешка. Каждый слой бумаги прокалывается по-отдельности при изготовлении, что приводит к наличию отверстий по всей поверхности мешка. Но отверстия в разных слоях (2-4 слоя) не совпадают, поэтому воздух просачивается через отверстия, а продукт не высыпается. Наличие отверстий приводит к снижению давления в мешке при его наполнении, и уменьшает риск разрыва. Так как отверстия в разных слоях бумаги не совпадают, то обычно продукт не просыпается. Но бывают исключения – для очень мелкодисперсных материалов, например при размере частиц 0.045 мм (325 mesh) и менее. Как упоминалось ранее, прочность мешка из-за перфорации может снизиться - на 20%. Стандартные размеры отверстий 3.1, 2.4 и 1.6 мм (1/8, 3/32 и 1/16 inches), а расстояния между отверстиями от 19×19 мм до 51×76 мм (3/4×3/4 to 2×3 inch) (Рис. 6.3).
Перфорация около клапана
При использовании перфорации около клапана отверстия создаются после размещения всех слоёв бумаги, на последнем этапе изготовления, и этим такая перфорация отличается от перфорации всей поверхности мешка. Прокалываются все слои бумаги (2-4 слоя), и отверстия в слоях совпадают. Так как большая часть воздуха выходит из мешка в районе расположения клапана (вокруг сопла устройства подачи материала), вверху, то наличие перфорации около клапана наиболее эффективно. Кроме того, это уменьшает загрязнение (наружной поверхности мешка) при вытекании избыточного воздуха и материала. Расстояния между центрами отверстий могут изменяться от 6.4×6.4 мм до 25.4×25.4 мм (1/4×1/4 и 1×1 дюйма). Диаметры отверстий те же, что и при перфорации всей поверхности мешка: 3.1, 2.4 и 1.6 мм (1/8, 3/32 и 1/16 inches). Так как при загрузке мешка часть материала выносится наружу, то при использовании такой системы фасовки лучше всего сделать местный вентиляционный отсос (local exhaust ventilation LEV). На Рис. 6.4 показан пример заполнения мешка с перфорацией около клапана, и то, как вытекание вытесняемого воздуха снижает избыточное давление в мешке, предотвращая его разрыв.
Так как заполнение мешка сопровождается вытеканием запылённого воздуха и продукта, то в большинстве случаев требуется использование вытяжной вентиляции для улавливания пыли. Для улавливания пыли обычно используют два способа - или располагают местные вентиляционные отсосы вокруг сопла, подающего материал в мешок, и/или размещаю
т всасывающее отверстие под установкой для фасовки. В зависимости от концентрации пыли, эти способы могут использоваться вместе или порознь. Оба способа будут рассмотрены ниже более подробно.
Способ заполнения мешка[править]
В этом разделе будет рассмотрено два типа ёмкостей - с открытым верхом, и с клапаном. Рис. На Рис. 6.5. показано типичное заполнение мешка с открытым верхом. Оператор одевает мешок на горловину устройства подачи материала, и затем нажимает кнопку, включая подачу. Затем происходит относительно быстрое заполнение мешка насыпаемым продуктом. При загрузке материала верхняя часть мешка обычно плотно закрыта, и присоединена к местному вентиляционному отсосу для удаления всей пыли, попадающей в воздух при загрузке. После окончания загрузки мешок автоматически вынимается из загрузочной машины и сбрасывается на конвейер с небольшой высоты. Затем верхняя часть мешка запечатывается или за счёт использования нагрева, или зашиванием нейлоновой нитью. Оба способа закрывания обеспечивают хорошую герметичность и попадание в воздух минимального количества пыли.
Следующим по распространённости (при переработке минеральных ископаемых) являются мешки с вставленным клапаном (pasted valve bag). Выбора типа клапана (из всего множества предлагаемого изготовителями), сильно влияет на способность герметично закрывать 25 и 50-кг мешки с продуктом и снижать количество пыли, попадающее в воздух при заполнении мешка, его перемещении, и укладке на поддон. Два десятилетия назад было проведено исследование, в котором изучалось 5 разных видов клапанов. Сравнивалась их способность герметично закрывать мешки и степень загрязнения воздуха пылью. Сравнивали стандартный бумажный клапан, полиэтиленовый, удлинённый полиэтиленовый, с двойным улавливанием (double trap), и вспененный (foam)[6- 2][6- 3]. Наилучшим оказался удлинённый полиэтиленовый клапан (Рис. 6.6). Это простой пластиковый клапан, длина которого примерно на 5 см (2 inches) больше длины стандартного бумажного или полиэтиленового клапана.
Исследование показало, что эффективность клапана зависит от его длины, и от материала, из которого он изготовлен. Чем длиннее клапан, тем меньше материала высыпается из мешка, и тем меньше пыли попадает в воздух. Но предполагается, что когда длина клапана становится слишком большой по отношению к длине сопла устройства загрузки материала, то это начинает отрицательно сказываться на скорости заполнения мешка. Из всех видов материалов для изготовления клапана наилучшим оказался поролон. При проведении исследования вспененный (поролоновый) клапан был самым коротким (10 см / 4 дюйма), а удлинённый полиэтиленовый клапан был длиной 15 см (6 дюймов). Получилось, что в порядке убывания эффективности клапаны нужно расположить так: удлинённый полиэтиленовый, вспененный, стандартный бумажный, полиэтиленовый и с двойным улавливанием. На Рис. 6.7 сравнивается снижение концентрации пыли при использовании удлинённого полиэтиленового клапана и вспененного клапана по отношению к использованию стандартного бумажного клапана. При использовании удлинённого полиэтиленового клапана концентрация респирабельной пыли уменьшилась на 45-65% по сравнению со стандартным бумажным[6- 2][6- 3].
При фасовке продукта в мешки нужно помнить, что высыпание материала и загрязнение воздуха пылью прямо зависят от типа и эффективности клапана в используемых мешках. Удлинённый полиэтиленовый клапан - наиболее эффективный, а его стоимость незначительно выше стоимости стандартного бумажного клапана.
Проводившийся недавно обзор показал, что в отрасли для фасовки чаще всего используют стандартный бумажный, полиэтиленовый и удлинённый полиэтиленовый клапаны. С учётом этой информации работодателям следует рассмотреть возможность перехода к использованию мешков с удлинённым полиэтиленовым клапанам для уменьшения загрязнения воздуха пылью при наполнении мешков, их перемещении и укладке на поддоны.
Также изготавливаются мешки с клапаном, который после заполнения мешка заваривается при воздействии звука. На внутренней поверхности такого клапана есть (специальный) клей, который заклеивает клапан при воздействии звуковой энергии. Звук излучается или соплом загрузки материала, или при специальным дополнительным оборудованием (после заполнения мешка). Теоретически нагрев и расплавление клея должны обеспечить лучшую герметизацию внутренней поверхности клапана, и уменьшить просачивание через него.
Но при использовании клапанов такого типа иногда возникает проблема - при попадании материала в клапан последний не заклеивается достаточно плотно, что приводит к просыпанию продукта. Другой недостаток этого типа клапанов - расход энергии (на звуковое заклеивание) обычно гораздо больше, чем у клапанов других конструкций.
Последствия разрыва мешка[править]
Помимо рассмотренных выше источников загрязнения воздуха пылью, разрывы, повреждения и разрушения мешков (которые могут случиться во время наполнения, перемещения или укладки) приводят к сильному загрязнению пылью воздуха и окружающего пространства. Если мешок рвётся при его заполнении материалом, то это приводит к быстрому попаданию большого количества пыли и продукта в воздух рабочей зоны. Другая проблема, возникающая при разрывах мешка - то, что производительность обеспыливающего оборудования не рассчитана на такие случаи, и оно не может справиться с таким количеством пыли, попавшим в воздух. Разрыв мешка при его заполнении может произойти из-за недостаточно хорошего склеивания (на заводе-изготовителе), неправильного хранения (при длительном нахождении в условиях сильной влажности и/или высокой температуры, или повреждение мешков при хранении), и по ряду других причин.
Мешки могут рваться не только при заполнении, но и при перемещении и при укладке на поддоны, что также приводит к попаданию большого количества пыли в воздух рабочей зоны. Чаще всего мешки рвутся из-за надрезов и надрывов, возникающих при столкновении с острыми краями при перемещении, или при неаккуратном складывании на поддоны.
Так как каждый разрыв мешка может привести к сильному загрязнению воздуха респирабельной пылью, и воздействию пыли на рабочих, нужно изучить каждую операцию с точки зрения возможности повреждения мешка при её выполнении. В некоторых случаях фасованные мешки требуется взвесить, и мешки с недостаточным весом отводятся на другую конвейерную линию. Это приводит к сбору мешков с неправильным весом в устройство для утилизации - обычно такое, что повторная ручная обработка мешков не требуется. Рекомендуется размещать такое устройство вне предприятия для того, чтобы снизить риск загрязнения заводского воздуха пылью при выбрасывании мешков. После заполнения ёмкости для мешков с неправильным весом её забирают, и утилизируют мешки безопасным способом. В место сбора мешков с неправильным весом устанавливается новый накопительный бункер, и цикл повторяется.
Способы снижения запылённости при фасовке 25 и 50-кг мешков[править]
Фасовка мешков может проводиться разными способами - начиная от заполнения вручную и заканчивая полностью автоматизированными многопозиционными машинами (multi-station machine). В этом разделе описываются способы снижения концентрации респирабельной пыли при фасовке 25 и 50-кг мешков.
Местный вентиляционный отсос около сопла подачи материала в мешок[править]
Одним из самых первых методов улавливания пыли, попадающей в воздух при работе фасовочного оборудования, был очень простой местный вентиляционный отсос с кожухом, окружавшим заполняемый мешок[6- 4]. Если оборудование могло заполнять несколько мешков (сразу), то такой отсос устанавливался около каждого из сопел подачи материала в мешок. Такие отсосы обычно делают на заводах - изготовителях из листовой стали, и они могут подойти к большинству из используемого фасовочного оборудования (Рис. 6.8).
Для уменьшения затрат времени на установку и техобслуживание, кожух обычно изготавливают из 4 отдельных частей, что позволяет легко собрать его на месте установки, соединив части болтами. Нижняя часть укрытия, в котором находится мешок во время заполнения, должна быть наклонной, чтобы (просыпавшийся) материал соскальзывал в бункер, обычно размещаемый под фасовочным оборудованием. Кожух местного вентиляционного отсоса (задняя сторона) должен позволять зажимать мешок и вставлять в него сопло загрузки материала.
При модернизации старых фасовочных машин может потребоваться перестановка кнопки включения так, чтобы она оказалась снаружи устанавливаемого кожуха местного вентиляционного отсоса. Кожух используется для того, чтобы улавливать мелкодисперсную респирабельную пыль, попадающую в воздух при заполнении мешка (при обратном выносе и при утечке из сопла загрузочной машины после убирания заполненного мешка), и позволять тяжёлым частицам и просыпавшемуся продукту падать вниз в бункер (для последующего использования).
Каждый из кожухов должен присоединяться к местной обеспыливающей вентиляционной системе для улавливания пыли, попадающей в воздух при заполнении мешка и при его убирании из фасовочной машины. Расход воздуха, который отсасывается от места фасовки, зависит от площади всасывающего отверстия воздуховода (при скорости воздуха 1 м/с [200 fpm] обеспечивается адекватный захват пыли). При типичной площади 0.37 м2 (4 ft2) требуется отсасывать 0.378 м3/с (1400 м3/час / 800 cfm). Исследование показало, что использование такого отсоса снижает попадание пыли в воздух рабочей зоны на 90-100%[6- 5]. Для получения информации о присоединении таких отсосов к местной обеспыливающей вентиляционной системе см. главе 1 ”Принципы пылеулавливания”.
Улавливающие бункеры (под станцией заполнения мешков)[править]
Подобно тому, как устраивали местные вентиляционные отсосы у каждого из мест заполнения мешков, можно сделать бункер для улавливания просыпавшегося материала и пыли – но под всей станцией заполнения мешков. Это позволит улавливать и использовать весь просыпавшийся материал и пыль. Это особенно выгодно при использовании станции с 3 или 4 соплам для заполнения мешков. Для такого оборудования использование (одного большого) бункера с местным вентиляционным отсосом легче (с точки зрения изготовления), и это экономически выгоднее, чем делать воздуховоды к каждому из (нескольких) мест заполнения мешков индивидуально.
На Рис. 6.9 показана типичная конструкция подобного типа (для одного места заполнения мешков). При проектировании таких конструкций важно размещать места забора воздуха в верхней части бункера, и поближе к месту заполнения мешков. Это приведёт к тому, что наиболее тяжёлые частицы пыли и просыпавшийся продукт будут падать в бункер, не улавливаясь вентиляционной системой, и будут выгружаться из бункера винтовым конвейером.
При проектировании обоих видов обеспыливающих систем (и с местными отсосами у каждого из мест заполнения мешков, и с общим бункером с отсосом) важно обеспечить подачу замещающего воздуха так, чтобы он не был загрязнён пылью. При работе местной обеспыливающей вентиляционной системы окружающий воздух будет притекать к местам заполнения мешков взамен отсасываемого. Так как этот воздух попадает на рабочие места и в зону дыхания оператора фасовочного оборудования (перед удалением через местный вентиляционный отсос), для уменьшения вредного воздействия пыли на рабочего нужно чтобы концентрация пыли в нём была минимальна[6- 6][6- 7]. Если температура окружающего здание воздуха приемлема, и там нет источников пыли около места забора воздуха, то его можно использовать для замены отсасываемого обеспыливающей вентиляцией.
Двухсопловая система заполнения мешков (Dual-nozzle bagging system)[править]
У односопловой системы заполнения мешков основными источниками пыли являются обратный вынос продукта, просыпание из загрузочного сопла, и загрязнение наружной поверхности мешков. Для уменьшения этих недостатков и уменьшения вредного воздействия на рабочего была разработана двухсопловая система. На Рис. 6.10 показаны главные составные части такой двухсопловой фасовочной системы. У неё два сопла (для уменьшения попадания пыли в воздух из-за обратного уноса и просыпания из сопла) и зажим.
У исходной конструкции для заполнения мешка используется сопло подачи материала. А у двухсопловой сопло подачи материала находится внутри второго (большего) сопла, которое удаляет избыток воздуха из мешка после его заполнения для снижения избыточного давления. При заполнении мешка происходит вытеснение из него воздуха, и он удаляется через второе сопло. Для этого используется побудитель тяги – эжектор (подача сжатого воздуха в сопло Вентури), расход удаляемого воздуха ~0.5 литра/сек (50 cfm). Для регулирования расхода удаляемого воздуха используется клапан с зажимом. Когда зажим открыт, воздух отсасывается.
При загрузке мешок немного переполняется, и удерживается в фасовочной машине зажимами. Затем открывается пережимной клапан (pinch valve), и вытяжка удаляет избыточный воздух из мешка. Через несколько секунд зажим мешка открывается, и заполненный мешок падает из фасовочной станции вниз. Вытяжка продолжает работать при удалении мешка, очищая от пыли пространство около клапана мешка. Уловленный вытяжкой материал может использоваться повторно.
Другой важной частью двухсопловой системы является улучшенный зажим (мешка). В начальной конструкции площадь контакта зажима и сопла была невелика. У улучшенного зажима площадь контакта с соплом ~60% (в основном - вверху и по бокам). Это уменьшает обратный унос продукта при заполнении мешка. Небольшая регулируемая обратная утечка необходима для предотвращения разрыва мешка при заполнении, но это должно происходить в нижней части загрузочного сопла для снижения загрязнения пылью пространства около мешка.
Исследования показали, что двухсопловая система может быть очень эффективным средством снижения концентрации респирабельной пыли в зоне дыхания рабочих, заполняющих и укладывающих мешки на поддоны[6- 8][6- 9]. На Рис. 6.11 показано, что установка двухсопловой системы снизила воздействие респирабельной пыли на рабочего – оператора на одном из заводов на 83%. Также использование двухсопловой системы приводит к двукратному снижению концентрации пыли в бункере под фасовочной станцией. Это объясняется меньшим просыпанием материала из-за обратного уноса во время заполнения мешка, и при просачивании из сопла подачи. Использование двухсопловой системы уменьшает попадания пыли и материала в окружающее пространство, и уменьшает воздействие пыли в 10 раз при погрузке в закрытые транспортные средства.
Использовать двухсопловую системы рекомендуется в основном для фасовочных станций с 3-4 соплами подачи материала, так как это сводит к минимуму снижение производительности (из-за затрат времени на ожидание снижения давления) после заполнения мешка. Такая система может также использоваться для снижения запылённости при использовании одного-двух сопел подачи материала, но при этом снижение производительности будет больше (так как оператор будет ждать при заполнении каждого мешка, а при заполнении нескольких мешков одновременно это имеет меньшее значение). Разработаны и продаются другие аналогичные системы для снижения давления в мешке после его заполнения[6- 10].
Система OASIS (воздушный душ)[править]
Система подачи очищенного воздуха сверху (Overhead Air Supply Island System, OASIS) может подать очищенный воздух сверху вниз в зону дыхания. Одно из главных достоинств системы – то, что она размещается над рабочим, и потому совместима с самым разнообразным оборудованием. На Рис. 6.12 показана система OASIS (воздушный душ) над рабочим местом оператора фасовочной машины.
Конструкция системы OASIS относительно проста. Окружающий заводской воздух всасывается в систему, и проходит через фильтр первичной очистки, где обычно используются высокоэффективные противоаэрозольные фильтры НЕРА. После входа воздуха в основную камеру, он проходит через дополнительные зоны нагрева или охлаждения (они могут встраиваться в установку при необходимости – если нужно улучшить микроклимат на рабочем месте в отношении температуры воздуха). Затем воздух выходит из установки через фильтр-воздухораспределитель. Это обеспечивает равномерное распределение потоков чистого отфильтрованного воздуха в направлении на рабочего, и обеспечивает очистку воздуха в случаях, когда нарушается работа фильтра первичной очистки. Если при фасовке в воздух попадает много пыли, то она загрязняет наружные слои потоков чистого воздуха, выпускаемых OASIS, после того, как они пройдут мимо рабочего. В этом случае рекомендуется отсасывать запылённый воздух с помощью местного вентиляционного отсоса.
При использовании системы OASIS целью является получение средней скорости воздуха, движущегося вниз в зоне дыхания рабочего, около 2 м/с (375 fpm). Это обычно полностью предотвращает попадание запылённого воздуха в зону дыхания в центр потока подаваемого воздуха[6- 11]. Важной особенностью системы OASIS является использование самоочищающегося фильтра для предварительной очистки. Для удаления уловленной пыли с фильтра есть разные технологии. Например, для этой цели широко используется такой эффективный способ, как импульсная обратная продувка (см. главу 1 “Принципы пылеулавливания”).
Система OASIS очень эффективно снижает воздействие респирабельной пыли на рабочих. При фасовке воздействие респирабельной пыли уменьшилось на величину 82 и 98% при выполнении двух различных операций – по сравнению с воздействием при выключенной системой[6- 12]. При выполнении обоих операций концентрация пыли в воздухе, отфильтрованном OASIS, не превышала 0.04 мг/м3.
Если OASIS используется для защиты стоящих рабочих, то её работу можно улучшить, подвесив прозрачные пластиковые полосы по бокам. Это станет для рабочего индикатором границы зоны чистого воздуха, и покажет, где система не сможет защитить его.
Дополнительным достоинством системы OASIS является то, что её работа улучшает качество воздуха в помещении. Это связано с тем, что система берёт воздух из помещения, очищает его, и затем выпускает на рабочего. После этого отфильтрованный воздух снова попадает в помещение. На одном из предприятий, где использовали OASIS, концентрация респирабельной пыли уменьшилась на 12% во всём здании[6- 11]. Расход чистого воздуха, подаваемого OASIS, может изменяться в зависимости от размера установки, но обычно он находится в диапазоне 2.8÷4.7 м3/с (6,000÷10,000 cfm). Полезность возвращения в помещение очищенного воздуха была показана и в других исследованиях[6- 13]. У систем OASIS схожая конструкция, и они могут изготавливаться и устанавливаться силами самого предприятия, или с привлечением любой местной вентиляционной компании, которая изготавливает вентиляционное и пылеулавливающее оборудование.
Автоматизированное оборудование для установки и заполнения мешков[править]
Многие изготовители производят автоматизированные фасовочные системы, которые позволяют избавиться от выполнения работы вручную. Обычно в таких системах есть устройство для автоматического размещения мешков и устройство для их наполнения. В большинстве автоматизированных систем рабочий должен только класть пустые 25 или 50-кг мешки в приёмное устройство. После этого момента система работает автоматически. Обычно в таких системах используется манипулятор, который захватывает пустые мешки из приёмного устройства, и помещает их в устройство для наполнения (через сопло подачи). Когда мешок оказывается размещён, начинается его наполнение. Оно продолжается до тех пор, пока сигнал от датчиков не покажет, что вес мешка достиг требуемого значения. Затем включается приспособление, которое извлекает заполненный мешок из устройства для заполнения. На Рис. 6.13 показан пример места складывания пустых мешков и автоматического устройства для их подачи в приспособление для заполнения материалом и автоматизированное устройство, которое устанавливает (пустые) мешки в устройство для их заполнения.
При использовании мешков с открытым верхом, обычно полуавтоматическая система устанавливает, заполняет и взвешивает мешки, а рабочий вручную подаёт мешок в запаковывающее устройство. В полностью автоматизированных системах все операции выполняются автоматически, и рабочий-оператор должен только следить за нормальной работой оборудования.
Чтобы оценить уровень автоматизации (полу-автоматическая система или полностью автоматизированная) нужно учитывать много разных факторов[6- 14]. На тех предприятиях, где фасовка проводится при односменном режиме работы, чаще используют полу-автоматизированное оборудование. При фасовке многих разных материалов, очистку и переключение на фасовку другого материала проще делать на полу-автоматизированном оборудовании. Использование автоматизированных фасовочных систем требует больших затрат на обслуживание и ремонт, чем использование не автоматизированного оборудования. Также важно иметь запас расходуемых при ремонте запчастей – особенно когда изготовитель находится достаточно далеко. А не автоматизированное оборудование проще, там меньше деталей, и меньше перечень запчастей, запас которых нужно иметь.
При использовании полностью автоматизированных систем можно увеличить выпуск продукции. Кроме того, экономятся средства из-за ненужности рабочих для фасовки вручную. Отсутствие людей, выполняющих фасовку вручную, уменьшает воздействие респирабельной пыли на людей, количество заболеваний опорно-двигательной системы, и количество случаев временной утраты трудоспособности.
И при использовании полностью автоматизированных систем, и при фасовке вручную, сохраняется необходимость в применении местного вентиляционного отсоса в месте заполнения мешков (для удаления пыли, попадающей в воздух при выдувании материала обратно из мешка и при просыпании материала из сопла подачи материала). Хотя рабочие в основном находятся вне области, где происходит заполнение мешков, но если при фасовке произойдёт попадание пыли в воздух, то она будет воздействовать на рабочих, находящихся около автоматизированного фасовочного оборудования. Для предотвращения этого часть используется очень эффективный способ – места заполнения мешков отделяются от окружающего пространства с помощью прозрачных пластиковых полос. Это создаёт физическое препятствие, отделяющее потенциально запылённую зону от окружающего пространства, и улучшающее эффективность местных вентиляционных отсосов.
Расходы при закупке автоматизированного фасовочного оборудования гораздо больше, чем при закупке оборудования, где используется выполнение части работы вручную. При анализе затрат следует учесть расходы за длительный интервал времени, учесть воздействие на рабочих респирабельной пыли и необходимость выполнения тяжёлой физической работы (создающей риск заболевания органов дыхания и опорно-двигательного аппарата).
Защита от пыли при перемещении и укладке 25 и 50-кг мешков на паллеты[править]
Устройства для очистки мешков и ленты транспортёра[править]
Устройство для очистки мешков и ленты транспортёра (B&BCD Bag and Belt Cleaning Device) предназначено для уменьшения попадания в воздух пыли, находящейся на наружной поверхности мешков (при их движении из места заполнения материалом к месту укладки на поддоны). Такое устройство уменьшает воздействие пыли на всех рабочих, выполняющих фасовку и укладку, и находящихся рядом.
Оборудование может использоваться при фасовке любых минеральных полезных ископаемых в бумажные мешки 25 и 50 кг. Устройство должно устанавливаться на конвейерной линии как можно ближе к месту заполнения мешков.
На Рис. 6.14 показан один из вариантов такого устройства. Его длина 3 м (10 футов), и для удаления пыли с боковых сторон мешка используются щётки в сочетании с соплами, выпускающими струи воздуха. Сначала мешки поступают в устройство через проём, занавешенный прочными гибкими пластиковыми полосами, отделяющими устройство от окружающего пространства. Затем мешки попадают в область очистки передней и верхней поверхности, для чего используется стационарная щётка на кронштейне, который может качаться (как маятник). Затем мешки проходят через вторую занавесь из пластиковых лент, и попадают в основную камеру для очистки. Там они проходят под круглой вращающейся щёткой, очищающей верхнюю поверхность каждого мешка. Для очистки боковых поверхностей используются неподвижные щётки, расположенные по бокам, и сопла, выпускающие струи воздуха (находятся после щёток и обеспечивают дополнительную очистку). С той стороны устройства, с которой находится клапан очищаемого мешка, используются сопла с большим расходом/скоростью воздуха - для более эффективной очистки области около клапана. После сопел мешок попадает на круглую вращающуюся щётку, очищающую его нижнюю поверхность. Затем мешок выходит из устройства, пройдя через занавесь из гибких пластиковых полос.
Чтобы сметённая и сдутая пыль могла свободно падать вниз, для перемещения мешков в устройстве по всей его длине используется конвейер с несущей частью из цепей. Упавший вниз материал затем снова используется, а для его выгрузки из бункера под устройством для очистки мешков используется скребковый конвейер. После прохождения через устройство и мешки, и лента конвейера должны быть практически чистыми от пыли.
Изучение работы устройства для очистки мешков на двух предприятиях показало, что оно очень заметно снижает концентрацию респирабельной пыли. По данным[6- 15][6- 16] его использование обеспечило снижение количества пыли на поверхности мешков на 78÷90%.
Другой источник пыли – сжатие мешков. При сжатии мешков в специальном приспособлении необходимо принять меры для улавливания пыли, поступающей в воздух. Например, можно сжимать мешки в устройстве для очистки их внешней поверхности.
В этом разделе описан один из видов таких устройств, а они изготавливаются разной конструкции разными изготовителями, или их можно изготовить на месте силами самого предприятия, или на каком-то машиностроительном предприятии. У такого устройства должна быть своя опора, чтобы оно могло устанавливаться в любом месте на конвейерной линии. Логично разместить устройство поближе к месту заполнения мешков, чтобы удалять пыль как можно быстрее. Для работы устройства обычно требуется электроэнергия и сжатый воздух (для привода щёток, перемещения мешков, и сдувания пыли).
Для предотвращения попадания пыли с мешков в окружающее пространство необходимо поддерживать разрежение в укрытии, в котором находится устройство (см. главу 1 “Принципы пылеулавливания” для получения необходимой информации о вентиляционной системе).
Полу-автоматизированные системы укладки мешков на паллеты[править]
В полу-автоматизированных системах укладка мешков проводится совместно и рабочими, и автоматической системой. Существует огромное множество типов конструкций подобного оборудования. В одном из случаев рабочий укладывает мешки вручную, но используется гидравлический подъёмник для уменьшения усилий. Подъёмник обеспечивает постоянную высоту места, на которое укладываются мешки, в течение всего времени заполнения паллеты. Подъёмник регулируется так, чтобы высота места, на которое укладываются мешки, была наилучшей с точки зрения эргономики (Рис. 6.15). Для улавливания пыли, попадающей в воздух при укладке мешков, используется сдувающее-всасывающая вентиляция[6- 17]. Она состоит из воздуходувки, создающей поток воздуха с небольшим расходом (примерно 60 л/сек, 120 cfm). Поток направляется над верхней поверхностью мешков, для чего используются два сопла диаметром ~76 мм, скорость воздуха около 6 м/с (1,200 fpm). Струи направлены на всасывающий зонт, находящийся с другой стороны паллеты. Перемещаясь примерно на 3-3.6 м поток воздуха захватывает пыль, попавшую в воздух с мешков. Всасывающая вентиляционная система работает при расходе воздуха около 1.2 м3/с (2,500 cfm).
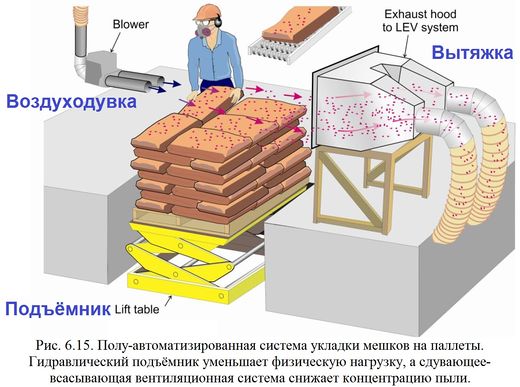
При работе полу-автоматизированного оборудования при укладке мешков на паллеты рабочий вручную укладывает мешки на поверхность, которая может двигаться в вертикальном направлении. Но он укладывает мешки в один слой, а саму укладку мешков на паллету проводит механическое оборудование автоматически. Так как заболевания спины встречаются у укладчиков чаще всего, использование такого оборудования значительно снижает риск их появления из-за уменьшения усилий и ненужности поднимания тяжёлых мешков. Но при использовании такого способа укладки пыль с мешков может попасть в зону дыхания рабочего. Тут может оказаться очень эффективным подача чистого воздуха сверху (см. описание системы OASIS выше).
Для улавливания пыли помимо системы OASIS можно использовать местный вентиляционный отсос (Рис. 6.16)[6- 18]. При использовании местного вентиляционного отсоса возникает проблема (как и во многих других подобных случаях) возможность попадания большого количества пыли в зону дыхания рабочего тогда, когда он находится между источником пыли и всасывающим отверстием. В рассматриваемом случае, если рабочий высунется из-под “воздушного душа”, в его зону дыхания может попасть пыль, сдутая с мешков в сторону всасывающего отверстия вентиляционной системы.
Автоматизированные системы укладки мешков на паллеты[править]
Разными компаниями разработано оборудование для автоматизированной укладки мешков на паллеты – как с использованием традиционной технологии “высокой укладки” (high-level pallet loading), так и для низкой укладки. В первом случае паллеты подаются в автоматическое устройство для укладки мешков на уровне пола, и потом поднимаются для начала укладки. После завершения укладки они снова опускаются на уровень пола перед перемещением в оборудование для обматывания пластиковой плёнкой, или перемещением к месту погрузки.
При использовании оборудования для “высокой укладки” мешки подаются в установку с помощью ленточного конвейера. Затем в установке они попадают на поверхность, покрытую роликами – в заранее определённое место (чтобы сформировать слой мешков), как устанавливается с помощью заранее введённой программы. После завершения формирования слоя он автоматически укладывается на предыдущий, и начинается формирование нового слоя. Каждый слой укладывается не так, как предыдущий, чтобы мешки не развалились (как при укладке вручную, так и при автоматической). После укладки требуемого количества слоёв паллета опускается на пол, и автоматическая укладка завершается. На Рис. 6.17 показана типичная система для автоматизированной “высокой” укладки мешков на паллету. Такое оборудование изготавливается многими производителями в различном конструктивном исполнении.
При использовании “низкой укладки” во время укладки мешков паллета остаётся на уровне пола. Механическое устройство берёт мешки и укладывает их на паллету. Чаще всего для этого используют робототизированный манипулятор.
Такое оборудование (с манипулятором, Рис. 6.18) становится всё более популярным из-за высокой производительности и относительно небольших затрат на техобслуживание (по сравнению с рассмотренным выше оборудованием для “высокой укладки”). Заполненные мешки перемещаются с места фасовки к месту укладки с помощью ленточного конвейера. При поступлении к месту укладки фотоэлемент обнаруживает поступление мешка, и мешок захватывается манипулятором с “пальцами”. Манипулятор аккуратно укладывает мешок на паллету в соответствии с заранее введённой программой. Манипулятор можно запрограммировать так, чтобы он укладывал мешки с небольшими зазорами, чтобы предотвратить их падение на паллету (что приводит к выбросу пыли через клапан). Такой манипулятор может использоваться для одновременной укладки мешков на две отдельные паллеты с повышенной скоростью, что увеличивает производительность.
Такие автоматизированные системы с манипулятором являются наилучшим оборудованием для укладки мешков, так как они проще, и по критерию стоимость/эффективность лучше, чем оборудование для “высокой укладки”. При использовании такого оборудования эксплуатационные расходы, поломки и затраты на техобслуживание минимальны[6- 19]. Они занимают меньше места, и у них меньше потенциальных источников пыли.
При использовании любой автоматической системы важно обеспечить адекватное ограждение для предотвращения попадания рабочих в места, где работает автоматизированное оборудование (или даже когда оно включено). Из-за достаточно большой скорости движения и большой массы манипуляторов, и большой амплитуде перемещения, их столкновение с рабочим может привести к серьёзной травме и даже к смерти.
При последовательной установке автоматизированных систем для размещения мешков, их наполнения, очистки наполненных мешков, их взвешивания и маркировки, укладки на паллеты и обматывания наполненных паллет, рабочий исключается из производственного процесса. Это, в свою очередь, снижает риск воздействия пыли на рабочего, который теперь обеспечивает надзор за нормальной работой оборудования, и обеспечивает его техобслуживание. Другое достоинство автоматизированного оборудования – снижение риска развития заболеваний опорно-двигательной системы из-за отсутствия ручного труда.
Нужно подчеркнуть, что использование автоматизированного оборудования не устраняет риск воздействия пыли. Нужно определить, сколько респирабельной пыли попадает в воздух при работе автоматизированного оборудования, и при необходимости принять меры для уменьшения её концентрации – чтобы она не попала в соседние помещения и в зону дыхания рабочих. Для этого обычно отгораживают места образования пыли с помощью пластиковых лент и используют местные вентиляционные отсосы для удаления респирабельной пыли.
Обматывание паллет плёнкой[править]
Наконец, рассмотрим обматывание паллет с бумажными мешками пластиковой плёнкой с точки зрения борьбы с пылью. Паллеты обматывают пластиковой плёнкой для того, чтобы предотвратить их рассыпание и избежать выноса пыли из мешков в воздух, а также для защиты мешков от повреждения при их перевозке на паллете. В настоящее время используют два вида оборудования для обматывания паллет: (1) обматывание термоусадочной стретч-плёнкой, и (2) закрывание паллеты готовым пластиковым мешком стретч худ. Оба вида оборудования широко используются при переработке минеральных полезных ископаемых, и они могут работать как автоматически, так и с ручным управлением. При выборе типа оборудования обычно учитывается размер паллеты, которую нужно будет обматывать.
При использовании оборудования для обматывания мешков нужно обеспечить полное отсутствие воздуха в последних. Если мешки “надуты”, то после обматывания они спустят воздух, станут меньше, натяжение плёнки уменьшится, и обмотка паллеты станет неэффективной. Если трудно избежать такой “надутости” мешков, можно использовать пресс для паллет для сжатия и выдавливания избыточного воздуха из мешков непосредственно перед обмоткой паллеты.
Одним из первых разработанных и применявшихся методов обмотки была спиральная обмотки. Она может выполняться или вручную, или автоматически. При ручной обмотке нагруженная паллета устанавливается на свободное открытое место, и рабочий ходит вокруг паллеты по кругу, наматывая на неё пластиковую плёнку по спирали. После полного заматывания паллеты рабочий обрезает конец пластиковой ленты и крепит его на паллете.
При автоматической обмотке загруженная паллета устанавливается на вращающуюся опору. При вращении опоры и паллеты плёнка непрерывно наматывается на паллету, и медленно перемещается – сначала вверх, а затем вниз, и обеспечивается заранее заданное предварительное натяжение (Рис. 6.19). После завершения обмотки механическое устройство обрезает ленту и помогает закрепить свободный конец на паллете.
В течение многих лет обмотка пластиковой плёнкой была наилучшим и наиболее дешёвым способом защиты груза при перевозке[6- 20]. Недостатком спиральной обмотки является то, что верх паллеты плохо закрыт, и пыль может попасть в воздух через это место. Кроме того, при нахождении паллет вне помещений в них может попасть дождь, влага, и продукт может намокнуть. Чтобы избежать этого, при спиральной обмотке паллету сначала накрывают листом (пластиковой плёнки), а потом обматывают. Обычно эту “крышу” рабочий кладёт вручную, что увеличивает затраты времени и удорожает процесс.
Другой способ обматывать паллеты – использование сжимающейся “обёртки” или плёнки в виде рукава стретч худ (stretch hood). При использовании этого метода вся паллета накрывается одним листом (рукавом) из пластиковой плёнки, который потом нагревается, а при этом стягивается, уменьшаясь в размерах, плотно охватывая паллету. Такой способ упаковки может использоваться и вручную, и автоматизировано. Такая упаковка позволяет хранить паллеты вне зданий без риска намокания. Паллеты, упакованные с помощью стретч худ, считаются более надёжно упакованными, чем при использовании термоусадочной плёнки. Так как такие паллеты более стабильны, и их легче обрабатывать и перемещать[6- 21].
Мягкие контейнеры[править]
Мягкие контейнеры называют по-разному: ”Flexible Intermediate Bulk Containers FIBCs”, "bulk bags", "semi-bulk bags", "mini-bulk bags" и "big bags" (биг-бэг). Они используются для перевозки продукции, и стали более популярными за последние годы. По критерию стоимость/эффективность они часто превосходят мешки на 25, 40 и 50 кг – и для изготовителя продукции (из минеральных полезных ископаемых), и для её потребителя. Наилучший способ снижения запылённости при наполнении мягкого контейнера – это использование расширяющегося мешка из неопреновой резины, который помещается в мягкий контейнер. Мешок расширяется, и полностью закрывает и продукт, и место загрузки, предотвращая вынос пыли при наполнении (Рис. 6.20). При использовании такого мешка, в горловине трубки/лотка подачи продукта в мягкий контейнер должен быть местный вентиляционный отсос, который будет удалять воздух, вытесняемый из мягкого контейнера при его заполнении (Рис. 6.21).
Если всё же пыль попадает в воздух, можно использовать другой эффективный способ защиты – изолировать место заполнения мягких контейнеров от остального пространства предприятия. Рабочий может заходить в такое пространство для того, чтобы вручную установить пустой мягкий контейнер в приспособление для его заполнения. Затем рабочий выходит, и нажимает кнопку включения наполняющего устройства. С помощью местного вентиляционного отсоса в ограниченной области наполнения поддерживается разрежение, и поэтому попавшая в воздух пыль не может достичь оператора. После завершения заполнения мягкого контейнера рабочий снова входит в место наполнения, удаляет заполненный мешок и устанавливает пустой.
Нужно отметить, что при заполнении мягких контейнеров воздействие пыли на рабочих сильно зависит от их поведения при запаковывании наполненного контейнера. У большинства мягких контейнеров есть тканевая горловина для загрузки материала, которую после заполнения нужно навязывать. Нужно, чтобы при выполнении этой работы оператор направлял открытый конец горловины от себя, чтобы выходящий из контейнера запылённый воздух не попадал в его зону дыхания.
Уборка - очистка полов в местах наполнения мешков, их укладки на паллеты, и на складах[править]
Паллеты, на которых уложены мешки 25 или 50 кг, или на которые поставлены мягкие контейнеры, обычно перемещают с помощью вилочных погрузчиков – прямо в фуры, или в железнодорожные вагоны, или же их отвозят на склад, где они хранятся до момента погрузки на транспортные средства. Если на полу или дорогах есть пыль, то она может попасть в воздух при движении вилочных погрузчиков и других транспортных средств. Для удаления пыли с полов и дорог на предприятиях, перерабатывающих полезные ископаемые, чаще всего используют два способа: моют водой и чистят машинами.
Для эффективного смывания пыли с полов помещения нужно чтобы с самого начала здание было правильно спроектировано и построено. Полы должны иметь уклон в сторону дренажной системы, чтобы смывание было эффективным, и чтобы свести к минимуму образование луж на полу. Как правило, для того, чтобы поливание полов из шланга было достаточно эффективным, оно должно проводиться каждую смену.
При использовании машин для уборки полов нужно учесть, что их изготавливают многие производители – самых разных типов. Они могут быть разного размера и производительности, могут перевозить оператора, или ехать рядом с идущим сотрудником, который управляет ими. Нужно продумать то, как и куда будет выбрасываться собранный мусор. Не имеет смысла очень эффективно убирать полы, но допускать потом воздействие собранной пыли на сотрудника при очистке уборочной машины или при выбрасывании мусора. Дополнительная информация об уборочных машинах приводится в главе 8 “Уменьшение пылеобразования во второстепенных источниках” в разделе "Уборка".
Изоляция участков с источниками пыли с помощью занавесей из пластиковых лент, и местных вентиляционных отсосов[править]
Результат использования разных методов снижения запылённости, описанных выше, можно улучшить, если изолировать места работы оборудования, загрязняющего воздух, от остального пространства предприятия. Для этого можно использовать занавеси из прозрачных пластиковых лент. При подключении местного вентиляционного отсоса воздух будет двигаться внутрь, препятствуя вытеканию пыли наружу. Такой способ – “отгораживание + вытяжка” – имеет ряд преимуществ. Занавесь препятствует распространению пыли по всему заводу. Она также визуально и физически предупреждает рабочих о том, где повышенная запылённость. Рабочие понимают, куда не следует входить, пока оборудование работает.
Другое достоинство занавеси в том, что она увеличивает эффективность местного вентиляционного отсоса. Так как местный отсос улавливает не всю пыль, то наличие занавеси создаёт дополнительное укрытие, кожух, повышающее эффективность. С экономической точки зрения занавесь из прозрачных пластиковых лент является относительно очень недорогим средством защиты от пыли.
Прозрачные ленты занавеси позволяют рабочим видеть, что происходит за занавесью, а это повышает безопасность. Занавеси из прозрачных лент используются не только при фасовке и укладке мешков, но и при выполнении других видов работ при переработке минеральных полезных ископаемых. Для правильного подключения местного вентиляционного отсоса и определения расхода воздуха см. главе 1 “Принципы пылеулавливания”.
Рекомендации по организации работ для снижения запылённости при фасовке и укладке мешков[править]
Ниже приводится перечень рекомендаций, выполнение которых уменьшит воздействие респирабельной пыли на рабочих, занятых фасовкой и укладкой мешков.
- Используйте лотки и т.п. приспособления для того, чтобы высота падения продукта вне укрытий была минимальной;
- Насколько возможно - не давайте накапливаться пыли на полах и дорогах, чтобы предотвратить попадание пыли в воздух при движении транспорта;
- Следите за тем, чтобы в местах обработки мешков, их сброса, разворота, транспортировки и др. не было острых кромок, углов и т.п., способных порвать или протереть мешок;
- Следите за исправностью клапанов в устройствах подачи материала в мешок чтобы предотвратить просыпание продукта в периоды времени, когда не проводится наполнение мешка;
- Найдите наиболее подходящие конструкции мешков, клапанов и фасовочных машин;
- Предотвращайте попадание пыли в воздух, которое происходит при вытеснении воздуха из мешка загружаемым материалом, при просыпании из сопла подачи загрузочной машины, и утечек из фасовочного оборудования. Эти источники пыли также загрязняют наружную поверхность мешков, и требуют большего расхода воздуха у местного вентиляционного отсоса;
- Рассмотрите возможность использования двухсопловой системы заполнения мешков (рассматривалась выше) для снижения концентрации пыли;
- При необходимости - уменьшите скорость подачи материала в мешок для снижения обратного выноса;
- Аккуратно укладывайте мешки на паллеты. Если кидать или сбрасывать мешки (на конвейер или на паллеты), увеличивается риск попадания пыли в воздух и риск разрыва мешка;
- При укладке мешков на паллеты используйте гидравлический подъёмник для уменьшения попадания пыли в воздух и для снижения тяжести труда (описано выше в разделе “Полу-автоматизированные системы укладки мешков на паллеты”). Постоянная высота верхнего края укладываемых мешков увеличивает эффективность сдувающе-всасывающей вентиляции;
- Используйте пустые мягкие контейнеры, изготовленные в соответствии с требованиями стандартов, и не загрязнённые пылью. При повторном использовании мягких контейнеров они часто возвращаются чистыми изнутри, но пыль остаётся в складках ткани снаружи, и она попадает в воздух во время работы с такими контейнерами;
- Храните все пустые мешки в чистых местах, и накрывайте их, чтобы на них не скапливалась пыль;
- При запечатывании загрузочной горловины мягкого контейнера оператор всегда должен направлять отверстие горловины от себя, чтобы выходящий из мягкого контейнера запылённый воздух не попадал в его зону дыхания;
- Избегайте размещения оператора между источником пыли и всасывающим отверстием местного вентиляционного отсоса. Если это произойдёт, запылённый воздух может двигаться в сторону рабочего, увеличивая воздействие пыли;
- Изучите возможность использования вспомогательного механического оборудования для предотвращения падения наполненных мешков на паллету. Использование такого оборудования также значительно снижает риск развития заболеваний опорно-двигательной системы;
- Рассмотрите возможность установки устройства для очистки мешков и ленты конвейера между фасовочным оборудованием и местом укладки мешков на паллеты (см. выше). Для очистки мешков можно успешно использовать механические щётки и сопла, выпускающие струи воздуха. Щётки нужно часто регулировать и заменять из-за износа. Для улавливания сметённой и сдутой пыли нужен местный вентиляционный отсос;
- Разработайте инструкции для сотрудников на случай разрыва мешка – такую, чтобы свести к минимуму выполнение работы вручную. Можно использовать уборочную машину с пылесосом, или устройство для сбора мусора с вентиляцией. Нужно приложить все усилия для того, чтобы свести к минимуму и предотвратить выполнение работ с порвавшимися мешками вручную;
- Изолируйте, отделите места фасовки и укладки мешков на паллеты от основного пространства предприятия с помощью занавесей из прозрачных пластиковых лент. Если нет необходимости делать перегородку так, чтобы можно было пройти – делайте её сплошной и твёрдой. В этих изолированных местах должно поддерживаться разрежение (с помощью местного вентиляционного отсоса), чтобы предотвратить вынос пыли наружу в другие, незагрязнённые места;
- Старайтесь улавливать пыль в месте её попадания в воздух с помощью местных вентиляционных отсосов – вместо того, чтобы направлять её в сторону или разбавлять чистым воздухом. Использование вентиляторов, перемешивающих воздух, не удаляет пыль из воздуха помещений предприятия;
- Используйте воздушный душ, подающий чистый воздух на рабочее место сверху (система OASIS), периодически очищая и заменяя фильтры, и следя за тем, чтобы чистый отфильтрованный воздух распределялся равномерно. При загрязнении фильтров может произойти значительное уменьшение расхода воздуха;
- Проверяйте и смазывайте подшипники у вентиляционного оборудования, включая систему OASIS, и проверяйте ременные передачи вентиляторов (если есть). Изучите возможность использования датчика измерения перепада давления, или системы индикации о неполадках, или проводите проверки во время техобслуживания;
- Нужно периодически проверять и очищать воздуховоды местных вентиляционных отсосов для обеспечения нормальной работы вентиляции. Также нужно проверять скорость воздуха в местах установки местных вентиляционных отсосов, чтобы она была достаточно большой для захвата пыли в источнике.
.
ССЫЛКИ
- ↑ Kearns P [2004]. What's new in paper and plastic bags. Powder and Bulk Eng 18(5):75–79.
- ↑ 2,0 2,1 USBM [1986b]. Dust reduction capabilities of five commercial bag valves. By Cecala AB, Covelli A, Thimons ED. U.S. Department of the Interior, Bureau of Mines Information Circular 9068.
- ↑ 3,0 3,1 Cecala AB, Muldoon T [1986]. Closing the door on dust - dust exposure of bag operator and stackers compared for commercial bag valves. Pit & Quarry 78(11):36–37.
- ↑ USBM [1983]. Technology News 54: Dust control hood for bag-filling machines. By Volkwein JC, Pittsburgh, Pennsylvania: U.S. Department of the Interior, Bureau of Mines.
- ↑ USBM [1981]. SF6 tracer gas tests of bagging-machine hood enclosures. By Vinson RP, Volkwein JC, Thimons ED. U.S. Department of the Interior, Bureau of Mines Report of Investigations 8527.
- ↑ USBM [1986a]. Impact of background sources on dust exposure of bag machine operator. By Cecala AB, Thimons ED. U.S. Department of the Interior, Bureau of Mines Information Circular 9089.
- ↑ Constance JA [2004]. Ways to control airborne contaminants in your plant. Powder and Bulk Eng 18(5):118–119.
- ↑ USBM [1984a]. Technology News 207: New nozzle system reduces dust during bagging operation. By Cecala AC. Pittsburgh, Pennsylvania: U.S. Department of the Interior, Bureau of Mines.
- ↑ USBM [1984b]. New bag nozzle to reduce dust from fluidized air bag machine. By Cecala AB, Volkwein JC, Thimons ED. U.S. Department of the Interior, Bureau of Mines Report of Investigations 8886.
- ↑ Case History [2006a]. Dustless bag filling system puts material in, takes dust out. Powder and Bulk Eng 20(5):82–87. http://www.powderbulk.com/
- ↑ 11,0 11,1 Volkwein JC, Engel MR, Raether TD [1986]. Get away from dust with clean air from overhead air supply island (OASIS). International Symposium on Respirable Dust in the Minerals Industry, University Park, Pennsylvania. Статья на стр. 360
- ↑ Robertson JL [1986]. Overhead filters reduce dust level in air supply. Rock Products 89(7):24.
- ↑ Godbey T [2005]. Recirculating your cleaned air: is it right for your plant? Powder and Bulk Eng 19(10):31–37.
- ↑ White D [2006]. Is it time to automate your bagging line? Powder and Bulk Eng 20(5):71–75.
- ↑ Cecala AB, Timko RJ, Prokop AD [1997]. Bag and belt cleaner reduces employee dust exposure. Rock Products 100(3):41–43.
- ↑ USBM [1995]. Reducing respirable dust levels during bag conveying and stacking using bag and belt cleaner device. By Cecala AB, Timko RJ, Prokop AD. U.S. Department of the Interior, Bureau of Mines Report of Investigations 9596. http://stacks.cdc.gov/view/cdc/10225/
- ↑ Cecala AB, Covelli A [1990]. Automation to control silica dust during pallet loading process. In: Proceedings of SME Annual Meeting. Preprint 90–28.
- ↑ Cecala AB, Zimmer JA, Smith B, Viles S [2000]. Improved dust control for bag handlers. Rock Products 103(4):46–49.
- ↑ Case History [2006b]. Robotic palletizer improves company's bottom line. Powder and Bulk Eng 20(5):88–93. http://www.powderbulk.com/
- ↑ Packaging system eases mineral dust problems [1978]. Pit and Quarry 70(10):104–106.
- ↑ New Installations [2006]. Stretch-hood fits like a glove. Powder and Bulk Eng 20(5):76–81.
ГЛАВА 7. Погрузка продукта[править]
При пересыпании продукта та пыль, которая находится в нём, может оторваться от частиц продукта, и попасть в воздух. Это происходит при падении материала в ёмкость, используемую для его перевозки (например – грузовой автомобиль, железнодорожный вагон, корабль). Попадание запылённого воздуха в зону дыхания рабочих создаёт риск развития заболеваний, и другие проблемы. На концентрацию пыли при погрузке материала влияет ряд факторов:
- Тип продукта, и его фракционный состав.
- Влажность продукта.
- Количество загружаемого продукта, и скорость загрузки.
- Высота падения при загрузке.
- Внешние факторы – скорость ветра, идёт ли дождь, физические свойства ёмкости (в которую загружается продукт).
Три первых фактора относятся к загружаемому продукту, и их можно определить, зная технологический процесс, или запросив поставщика. Проводившиеся недавно исследования показали, что обычно увеличение размера частиц и увеличение влажности уменьшает концентрацию респирабельной пыли в воздухе. При увлажнении для предотвращения образования пыли, содержание влаги 1% может считаться хорошей начальной точкой при измельчении материала[7- 1]. Более подробно использование увлажнения для борьбы с пылью рассмотрено в главе 2 “Обеспыливание с помощью воды”.
Три последних фактора относятся к процессу погрузки материала. Для уменьшения воздействия пыли на рабочих нужно использовать эффективные средства коллективной защиты. Например, можно уменьшить расстояние, с которого материал падает, и можно установить физические барьеры для защиты от ветра. Ниже будут рассмотрены следующие методы, используемые в отрасли:
- Использование загрузочных лотков;
- Бункер для предотвращения образования пыли;
- Использование укрытий, кожухов.
Загрузочные лотки[править]
Загрузочные лотки предназначены для переноса продукта из мест хранения на предприятии в транспортные средства, используемые для его перевозки. Обычно их делают так, чтобы они могли удлиняться, опускаясь вниз до загружаемого транспортного средства, а затем они втягиваются или поднимаются обратно. Изучение описаний такого оборудования, изготавливаемого несколькими производителями, показал что они могут перемещаться на расстояние от метра до 30 м. Как показано на Рис. 7.1, эти устройства могут состоять из нескольких телескопических труб или желобов, которые могут вытягиваться и втягиваться. На том же рисунке показано, что у такого устройства обычно есть внешний кожух, создающий оболочку вокруг приспособления для загрузки материала. Этот кожух защищает продукт от негативных внешних воздействий (дождь, ветер и т.д.), и ограничивает распространение образующейся пыли.
В зависимости от условий выгрузки материала, концевая часть устройства может быть специальной конструкции (например – с герметичным креплением к проёму для загрузки). Нередко концевую часть загрузочного устройства делают конической формы, чтобы она частично входила в проём для загрузки и плотно закрывала его. На Рис. 7.2 показаны примеры таких концевых частей, предназначенные для уменьшения выноса пыли наружу при загрузке транспортных средств. Если у транспортного средства есть несколько проёмов, то во время загрузки должен быть открыт только один – тот, через который подаётся материал – чтобы уменьшить вынос пыли наружу.
Файл:Обеспыливание 2012 Рис. 07.03..jpg На Рис. 7.3 показаны рисунок и фотография шарнирно закреплённого устройства для загрузки. Возможность перемещаться позволяет обеспечить правильное расположение приспособления относительно загрузочного проёма. |
Чтобы реализовать те плюсы, которые даёт конический конец загрузочного устройства, нужно обеспечить правильное положение погрузочного устройства относительно загрузочного проёма (чтобы снизить риск попадания пыли в воздух при погрузке). Для этого можно использовать шарнирно закреплённые загрузочные устройства. Это оборудование позволяет перемещать загрузочное устройство вправо-влево и вперёд-назад так, чтобы можно было разместить конус в оптимальном положении над транспортным средством, что сведёт к минимуму просыпание материала и вынос пыли. Оператор может контролировать положение места выгрузки из кабины управления, или с помощью подвесного пульта управления. На Рис. 7.3 показана схема устройства и фотография шарнирно закреплённого приспособления для загрузки материала в транспортное средство[7- 2].
При погрузки материала в открытые транспортные ёмкости, на концевой части устройства для подачи материала должна быть “юбка”, ограждение, которые будут отделять высыпаемый продукт от окружающего пространства для уменьшения запылённости. Обычно такое ограждение делают из многослойной прорезиненной ткани, или обычной ткани, и регулируют его положение по высоте (flare out) по мере загрузки продукта. Для эффективной борьбы с пылью и для предотвращения засорения устройства для подачи материала, нужно периодически поднимать его конец (по мере увеличения уровня насыпанного материала). Для автоматизации такого подъёма могут использоваться датчики, свешивающиеся вниз с устройства для подачи материала. По мере заполнения ёмкости транспортного средства материал отклоняет такие датчики от вертикального положения (например – на 15° и более), что включает автоматический подъём. На Рис. 7.4 показаны примеры подобных датчиков.
.
Пылеулавливающее оборудование и устройства для загрузки материала[править]
Падение материала из устройства для загрузки в ёмкость транспортного средства создаёт поток воздуха, который может унести пыль, оторвавшуюся от частиц материала. При ударе падающего материала (о дно ёмкости или о поверхность ранее сброшенного материала), продукт сжимается, и вовлечённый в движение воздух (находившийся между частицами материала) выходит наружу, увлекая с собой пыль. При увеличении высоты, с которой падает материал, скорость движения воздуха возрастает, и попадание пыли в воздух усиливается[7- 3]. При загрузке в ёмкость определённого объёма материала он вытесняет из ёмкости такое же количество воздуха, и последний может вынести с собой пыль. В главе 1 "Принципы пылеулавливания" рассмотрено и показано вовлечение воздуха в движение падающего материала, и образование пыли при его падении.
Для предотвращения попадания в атмосферу этого вытесняемого запылённого воздуха обычно используют сухую систему пылеулавливания, присоединяя её к устройству для подачи материала в ёмкость. Эта пылеулавливающая вентиляционная система создаёт поток воздуха в кольцевом пространстве между наружным ограждением и внутренней частью загрузочного устройства, по которому подаётся материал (Рис. 7.1). Для улавливания пыли обычно используется фильтровальная ткань в виде рукавов или картриджей. Для отряхивания осевшей на ткани пыли используется обратная продувка сжатым воздухом. Пылеуловитель должен находиться на расстоянии от устройства для загрузки, и соединяться с ним с помощью воздуховодов, как показано на Рис. 7.1 слева. Другое конструктивное решение – размещение пылеуловителя в верхней части загрузочного устройства (Рис. 7.1 справа – пылеуловитель и вентилятор размещены на устройстве подачи материала).
Обзор технических характеристик оборудования, изготавливаемого для загрузки материала и имеющего встроенный местный отсос, показал что расход отсасываемого запылённого воздуха превышает объёмный расход подаваемого материала в диапазоне от 1.8[7- 4] до 4.9[7- 5] раз. Для вычисления расхода воздуха, который должен отсасываться, можно использовать уравнение 1.2 из главы 1 “Принципы пылеулавливания”. Уравнение учитывает скорость подачи материала, высоту его падения, размер частиц, и размер проёма для загрузки материала. Нужно заметить, что при слишком большом расходе отсасываемого воздуха он будет уносить с собой в пылеуловитель часть подаваемого материала.
Устройства для погрузки со ступенчатым пересыпанием материала[править]
Cascading Loading Spout
На Рис. 7.5 показана схема и фотография[7- 6] устройства для загрузки материала, состоящего из серии последовательно расположенных конусов, не дающих материалу падать сразу с большой высоты, а заставляющих его много раз падать с одного конуса на другой. Как упоминалось ранее, при свободном падении продукта может произойти попадание пыли в окружающий воздух. Использование серии лотков – наклонённых конусов – не позволяет материалу падать с большой высоты. Это позволяет уменьшить скорость падения и вовлечение воздуха в движение материала, постепенно пересыпающегося с одного конуса на следующий, находящийся с небольшим перепадом по высоте. Первоначально это приспособление придумали для уменьшения повреждения продукта, но оказалось, что оно может уменьшить пылеобразование за счёт уменьшения скорости падения[7- 7]. Улучшение переноса материала позволяет частицам быть в более близком контакте друг с другом, что уменьшает отрыв и унос маленьких частиц в воздух. Как первичные средства борьбы с пылью в таких устройствах используются ограждение, защищающее от ветра, и “юбка” в месте высыпания материала. Обычно в устройствах для подачи материала, где продукт пересыпается по каскадным лоткам, нет вытяжки и сухого пылеуловителя. При разном расходе подаваемого продукта размер конусов, расстояние между ними и их наклон должны быть разными. Поскольку в таких устройствах материал находится в постоянном контакте с конусами, для защиты от протирания используют износостойкие (с внутренней стороны) вкладыши.
Бункер для предотвращения образования пыли[править]
Dust suppression hopper
Для уменьшения пылеобразования при погрузке материала может использоваться другое устройство – бункер для предотвращения образования пыли (Dust Suppression Hopper DSH)[7- 8]. Это устройство устанавливается в месте, где высыпается материал, и оно предназначено для того, чтобы высыпаемый материал перемещался в ёмкость в виде сплошного неразрывного потока[7- 9]. В бункере накапливается материал, и поэтому поток высыпаемого материала всегда непрерывный и сплошной, схожий с твёрдым телом, что уменьшает вовлечение воздуха в движение. В нижней части бункера есть пробка, перекрывающая высыпание материала до тех пор, пока в бункере не накопится достаточное количество. Для регулирования зазора между пробкой и бункером используется или пружина, или запрограммированный контроллер. Материал подаётся в бункер сверху, и не высыпается из него до тех пор, пока его не накопится достаточно много – так, что давление на пробку не станет достаточно большим, и пробка не сместиться, открывая проход для высыпания. Затем материал высыпается из бункера в виде сплошной неразрывной струи (Рис. 7.6), а не в виде потока отдельно падающих частиц. Это уменьшает пылеобразование[7- 3].
Файл:Обеспыливание 2012 Рис. 7.6. Бункер для предотвращения образования пыли.jpg На Рис. 7.6 показан бункер для предотвращения образования пыли. Он накапливает материал, а потом выпускает его сплошной струей, что уменьшает образование пыли. |
Файл:Обеспыливание 2012 Рис. 7.7. Место погрузки вагонов, изолированное пластиковыми лентами.jpg На Рис. 7.7 показано место погрузки железнодорожных вагонов, изолированное от окружающего пространства пластиковыми лентами для предотвращения распространения пыли. |
Укрытия[править]
Enclosures
Лучший способ борьбы с пылью при высыпании материала в ёмкость – это предотвращение её попадания в воздух. Но если пыль всё же попала в воздух, то нужно стараться предотвратить попадание пыли в зону дыхания находящихся рядом рабочих. Для этого можно использовать укрытие, отделяющее источник пыли от окружающего пространства, или кабину, отделяющую рабочего от загрязнённой атмосферы. Ниже рассматриваются оба метода.
Укрытие места погрузки[править]
Укрытие в месте выгрузки материала предназначено для предотвращения распространения попавшей в воздух пыли и её улавливания так, чтобы она не могла попасть в зону дыхания находящихся рядом рабочих, и загрязнить окружающее пространство. Такой способ борьбы с пылью обычно используется при погрузке материала в грузовые автомобили и в железнодорожные вагоны. В сущности, создаётся физический барьер, который изолирует источник пыли от окружающего пространства. Он сводит к минимуму влияние внешних факторов – таких, как сильный ветер. Барьер может быть сделан в виде проницаемой перегородки из гибких пластиковых полос, листов прорезиненной ткани или занавеси, герметизирующих место подачи материала в загрузочный проём ёмкости транспортного средства. На Рис. 7.7 показан другой вариант, сделанный в виде гибких пластиковых лент или занавеси, закрывающих место погрузки железнодорожных вагонов. В любом случае каждая из таких лент должна размещаться так, чтобы она частично перекрывала соседние - чтобы более эффективно препятствовать распространению пыли. Кроме того, воздух из получившегося укрытия должен отсасываться вентиляционной пылеулавливающей системой. Для определения первоначального приближённого значения расхода отсасываемого воздуха и производительности сухого пылеуловителя можно использовать уравнение 4.1 из главы 4 "Дробление, размол и просеивание". Если утечка пыли из укрытия будет происходить, это может объясняться или недостаточной изолированностью источника пыли (зазоры в укрытии), или недостаточным расходом воздуха, или обоими причинами.
Ниже приводится список вопросов, которые нужно решить для того, чтобы рабочим не нужно было входить в место загрузки в укрытии.
- Люки транспортных средств должны открываться до того, как они окажутся в укрытии.
- Для повышения точности установки устройства подачи материала и снижения риска просыпания можно использовать видеокамеры.
- Для подачи сигнала оператору о полном заполнении ёмкости и/или автоматического выключения подачи материала можно использовать датчики. Для этого изготавливаются датчики разных конструкций – поворотные, датчики давления, ёмкостные, инфракрасные. Использование датчиков позволит оператору находиться дальше от источника пыли.
- После полного наполнения ёмкости транспортного средства загрузочное приспособление должно подниматься на заданную и достаточно большую высоту так, чтобы транспортное средство могло проехать не задевая его. Это гарантирует, что будет достаточно большой зазор, и уменьшит потери времени между загрузкой двух ёмкостей. Для этого можно использовать датчики уровня и переключатели диапазонов (измерений уровней).
- Во время загрузки материала и в процессе выполнения всех работ по очистке нужно запрещать сотрудникам входить в укрытие. Процесс загрузки должен быть разработан так, чтобы сотрудники не должны были входить в укрытие. А если сотрудники должны войти в укрытие, то нужно определить возможную степень загрязнённости воздуха, чтобы выбрать и использовать адекватные СИЗ органов дыхания.
Изолированные кабины для операторов, управляющих оборудованием[править]
Один из самых эффективных способов защиты рабочих от пыли – использование изолированных кабин для операторов, управляющих работой оборудования, в которых обеспечен микроклимат и в которые подаётся отфильтрованный воздух. Проведённые исследования показали, что подходящая исправная система подачи очищенного воздуха в достаточно герметичную кабину может снизить воздействие респирабельной пыли на оператора на 90%[7- 10]. Другое достоинство этих кабин в том, что можно установить оборудование для кондиционирования воздуха (подогрева, охлаждения и т.п.), чтобы сделать рабочее место оператора более комфортабельным. На Рис. 7.8 показана кабина оператора, наблюдающего за местом погрузки материала.
С точки зрения предотвращения воздействия пыли на человека необходимо сделать закрытую кабину, в которую будет подаваться отфильтрованный воздух, и в которой будет поддерживаться избыточное давление. Избыточное давление предотвратит возможное просачивание запылённого воздуха в кабину и её попадание в органы дыхания. Более подробная информация о конструкции и работе таких кабин приводится в главе 9 “Кабины операторов, пульты управления и кабины мобильного оборудования”.
.
ССЫЛКИ
- ↑ NIOSH [2003]. Handbook for dust control in mining. By Kissell FN. Pittsburgh, PA: U.S. Department of Health and Human Services, Centers for Disease Control and Prevention, National Institute for Occupational Safety and Health, NIOSH Information Circular 9465, DHHS, (NIOSH) Publication No. 2003–147.
- ↑ Midwest International Standard Products [2010]. Date accessed: October 6, 2010.
- ↑ 3,0 3,1 Biere G, Swinderman RT, Marti AD [2010]. Conveyor upgrades increase plant availability, reduce airborne dust. Coal Power Magazine [online] Feb 16. Reduce-Airborne-Dust_242.html Date accessed: October 18, 2010.
- ↑ SLY, Inc. [2010]. Date accessed: October 8, 2010.
- ↑ PEBCO [2010]. Date accessed: October 8, 2010.
- ↑ Cleveland Cascade [2010]. Date accessed: November 18, 2010.
- ↑ Maxwell AS [1999]. Degradation, segregation and dust control of bulk materials. Solids Handling 19(3):399 403.
- ↑ DSH Systems [2010]. Dust Suppression Hopper Systems. Date accessed: October 7, 2010.
- ↑ Wypych P [2009]. Award winners can solve grain's dust problems. Australian Bulk Handling Review. Date accessed: October 13, 2010.
- ↑ NIOSH [2008]. Key design factors of enclosed cab dust filtration systems. By Organiscak JA, Cecala AB. U.S. Department of Health and Human Services, Centers for Disease Control and Prevention, National Institute for Occupational Safety and Health, Report of Investigations 9677, DHHS (NIOSH) Publication No. 2009–103.
ГЛАВА 8. Уменьшение пылеобразования во второстепенных источниках[править]
В этой главе рассматриваются различные второстепенные источники пыли, которые часто встречаются на предприятиях, перерабатывающих минеральные полезные ископаемые, и которые могут сильно увеличить воздействие респирабельной пыли на рабочих. В некоторых случаях воздействие респирабельной пыли на рабочих из-за таких второстепенных источников может быть больше, чем от основных источников (во время выполнения основной работы). Поэтому нужно выявлять такие второстепенные источники, и защищать от них рабочих. В этой главе указаны (некоторые из) таких источников, и приводятся рекомендуемые способы уменьшения воздействия пыли на рабочих.
Удаление пыли с загрязнённой рабочей одежды[править]
При переработке полезных ископаемых значительный вклад в воздействие респирабельной пыли на рабочих может внести загрязнённая одежда. Зафиксированы отдельные случаи, когда воздействие респирабельной пыли, попавшей в зону дыхания с загрязнённой рабочей одежды, могло на порядок превышать вклад окружающего загрязнённого воздуха[8- 1]. Нужно сказать, что как только одежда испачкалась, она становится непрерывным источником пыли – до тех пор, пока не будет очищена, или пока рабочий не переоденется.
Один из методов решения этой проблемы – использование пыленепроницаемой одежды, которая снимается после выполнения работы в “грязных” условиях и затем в конце смены выбрасывается. Это уменьшает попадание пыли на собственную одежду рабочего. Такая одежда также очень популярна при выполнении работы в условиях воздействия токсичной пыли. Недостатками этой одежды является то, что она неудобна, так как препятствует теплоотдаче, а также её повышенная цена.
Сейчас в США официально одобрено (MSHA) использование лишь одного способа очистки загрязнённой одежды – с использованием пылесосной системы с высокоэффективным фильтром (НЕРА). Но это требует больших затрат времени и вряд ли позволит эффективно очистить одежду. Рабочему трудно эффективно почистить свою собственную одежду с помощью пылесосной насадки, особенно на спине и на ногах.
Использование сжатого воздуха для сдувания пыли с загрязнённой одежды запрещено MSHA, но поскольку пылесосное оборудование неэффективно и требует больших затрат времени, рабочие могут попробовать использовать такой запрещённый метод (сдувая пыль с одежды помощью шланга). Хотя этот метод очистки вряд ли заметно эффективней рекомендуемого (с помощью пылесосной установки), он требует меньше времени, и не хуже рекомендуемого (в отношении очистки труднодоступных мест). При использовании этого способа происходит загрязнение воздуха пылью, что увеличивает воздействие респирабельной пыли на рабочего и его коллег, находящихся поблизости - а это серьёзный недостаток[8- 2].
После загрязнения одежды попавший на неё материал становится источником пыли при выполнении каких-то движений во время работы. С учётом этого и того, что пыль может воздействовать на рабочих из разных источников в течение смены, самый эффективный способ защиты – частая смена загрязнившейся одежды. Хотя для таких целей уже много лет используют одноразовую одежду, и разработаны материалы, к которым плохо “прилипает” грязь и пыль, большинство шахтёров продолжает использовать стандартную рабочую одежду (обычно из demin – грубая х/б ткань для рабочей одежды, джинсов и т.п.), и носят её годами[8- 3][8- 4][8- 5]. Для решения проблемы был разработан быстрый, безопасный и эффективный метод, позволяющий рабочим чистить свою одежду в течение дня.
Новая технология для очистки рабочей одежды от пыли[править]
Новый метод очистки загрязнённой одежды от пыли разрабатывался совместно NIOSH и Unimin Corporation. Хотя этот метод не избавляет от необходимости стирать рабочую одежду в прачечной, но он позволяет рабочим периодически безопасно очищать свою одежду от пыли в течение дня (многократно) – до того, как она будет постирана. Система очистки состоит из 4 компонент: (1) кабина для очистки, (2) ёмкость с (сжатым) воздухом, (3) система подачи струи сжатого воздуха, и (4) вытяжка. На Рис. 8.1 приводится схема системы.
Для очистки одежды рабочий входит в кабину, одевает СИЗ (органов дыхания, зрения и слуха), включает подачу сжатого воздуха, и поворачивается так, чтобы струи воздуха сдували пыль с одежды со всех сторон. Через небольшой период времени (18 секунд) подача воздуха автоматически выключается, и рабочий может выйти из кабины в гораздо более чистой рабочей одежде.
Кабина для очистки[править]
Размер кабины - 122×107 см (48×42 inches), так что у рабочего достаточно места для вращения перед соплами, выпускающими струи воздуха (чтобы очистить одежду со всех сторон). Окружающий воздух поступает в кабину через отверстие 60 см в её крыше, движется вниз и отсасывается через проём в нижней боковой части кабины. Этот воздух при движении уносит сдутую с одежды пыль из зоны дыхания рабочего. Затем запылённый воздух направляется в вентиляционную систему.
Ёмкость со сжатым воздухом[править]
Как источник воздуха для системы его распыления в кабине используется ёмкость со сжатым воздухом. Размер ёмкости определяется с учётом конструкции системы распыления. Можно использовать баллон объёмом 470 или 940 л (120- или 240-gallon, при переводе брался сухой галлон США) - в зависимости от числа рабочих, которым нужно чистить одежду. Производственные испытания показали, что на очистку в среднем уходит 18 секунд, а баллона 470 л (120-gallon) хватает на 22 секунды. Если кабина будет использоваться несколькими рабочими последовательно, нужно использовать баллон 940 л (240-gallon). Давление воздуха в баллоне должно быть не меньше 1 МПа (150 psi), баллон должен находиться как можно ближе к кабине и должен соединяться с насадкой для распыления воздуха жёсткими трубами. Нужно установить регулятор давления, подающий в сопла воздух под давлением не более 207 кПа (2 атм, 30 psi).
Насадка для распыления воздуха[править]
На Рис. 8.2 показана конструкция насадки для распыления воздуха. Она состоит из 26 сопел, размещённых на расстоянии ~5 см друг от друга (2 inches). Нижнее сопло находится на высоте 15 см от пола, оно круглого сечения, и предназначено для очистки обуви (у него несколько выше расход воздуха). Оно закреплено шарнирно, и может отклоняться вниз. Остальные 25 сопел щелеобразной формы, и лабораторные испытания показали, что при меньшем расстоянии до одежды их эффективность очистки выше. Расход воздуха через систему распыления немного меньше чем 850 м3/ч, 236 л/сек (500 cfm).
Первоначально систему распыления проектировали под рабочего ростом 178 см (5 feet 10 inches) – это средний рост американского рабочего-мужчины. Рабочие меньшего роста могут закрыть верхние сопла для предотвращения попадания струй воздуха прямо в лицо.
Между источником сжатого воздуха и соплами для его распыления нужно установить воздушный фильтр. Это снизит риск того, что частицы металла или ржавчины попадут в поток выдуваемого воздуха.
Вытяжка[править]
Для эффективного удаления пыли важно, чтобы в течение всего времени использования кабина для очистки одежды находилась под разрежением так, чтобы сдутая с одежды пыль не могла попасть наружу – в воздух рабочей зоны. На этапе проектирования испытания показали, что при отсасывании 0.94 м3/с (2,000 cfm) удаётся сохранять разрежение в кабине в течение всего времени очистки одежды. В системе распыления воздуха установлен клапан, не пропускающий сжатый воздух в сопла при отсутствии достаточного разрежения в кабине.
Для удаления запылённого воздуха из кабины рекомендуется использовать два метода:
- Отсасывание запылённого воздуха с его последующей очисткой в пылеуловителе, например – тканевом фильтре[8- 6]), или
- Отсасывание запылённого воздуха с его отводом (без очистки) в малолюдное место[8- 7]. На предприятиях, перерабатывающих минеральные полезные ископаемые, есть множество источников пыли, и добавка к ним небольшого количества сдутой с одежды пыли не приведёт к сколько-нибудь значительному увеличению загрязнённости вдыхаемого воздуха.
Безопасность[править]
Все рабочие, входящие в кабину, должны одевать соответствующие СИЗ, включая сертифицированные респираторы, подобранные под размер их лица и проверенные приборами (на отсутствие просачивания между маской и лицом, fit-test). На респираторах должны устанавливаться фильтры, соответствующие перерабатываемым материалам, и должны использоваться СИЗ глаз и слуха.
Кроме того, согласно требованиям Управления по охране труда (OSHA), перед тем, как струя воздуха будет направлена на человека для очистки одежды, давление в соплах не должно превышать 2 атм.
Эффективность метода очистки одежды[править]
При разработке описанного нового метода сравнивалась его эффективность с методом, рекомендованным MSHA, и с использованием одиночной струи, выпускаемой из шланга. При проведении проверок одежда рабочих из х/б или смеси х/б и полиэстера загрязнялась известковой пылью перед входом рабочего в кабину. В таблице 8.1 показана эффективность трёх методов очистки двух видов одежды и затраты времени на очистку.
Очевидно, что новый метод очистки гораздо эффективнее, и требует несравненно меньше времени. В таблице также показано, что одежда из смеси х/б и полиэстера очищается лучше, чем из 100% х/б. На Рис. 8.3 показаны фотографии рабочего до и после очистки одежды в кабине.
Одежда из → | 100% х/б | Смесь х/б и полиэстера | ||
---|---|---|---|---|
Метод очистки ↓ | Масса оставшейся после очистки пыли, грамм | Длительность очистки | Масса оставшейся после очистки пыли, грамм | Длительность очистки |
Пылесосная установкой | 63.1 | 398 | 45.5 | 346 |
Струя из шланга | 68.8 | 183 | 48.4 | 173 |
Кабина для очистки | 42.3 | 17 | 21.9 | 18 |
Требования законодательства (США) к очистке одежды[править]
В США вопросы очистки одежды затрагиваются в двух нормативных документах. Во-первых, в стандарте MSHA [30 CFR Part 56.13020], сказано: "Категорически запрещается направлять струю сжатого воздуха на рабочего. При использовании сжатого воздуха, нужно принять все необходимые меры для того, чтобы защитить людей от (риска) травмы". В насадке для распыления воздуха есть приспособление, которое позволяет закрывать верхние сопла при использовании кабины рабочими маленького роста. Это не позволяет струям сжатого воздуха попадать на лицо -они направлены только на одежду.
В другом документе – стандарт по охране труда, разработанном OSHA [29 CFR 1910.242(b)] сказано: “Нельзя использовать сжатый воздух для очистки, кроме тех случаев, когда его давление уменьшено до 2 атм, и требуется обязательное применении ограждения для защиты от частиц (стружки, ржавчины и т.п.) и носка СИЗ”. Этот документ ограничивает давление в соплах насадки 2 атм. В связи с требованиями этих документов работодатель может подать заявление в окружное отделение MSHA для получения разрешения на использование этой системы очистки одежды на своём предприятии.
Поскольку использование такой системы уже разрешено в других отраслях промышленности, то получить разрешение будет несложно. Те, кто заинтересован в использовании этой новой технологии, могут связаться с изготовителями подобного оборудования. (например: устройства, которые мы разработали, продаёт компания Cleaning Systems (http://www.cleanclothbooth.com/).
Уборка[править]
Хотя кажется, что вопросы уборки рабочих мест не имеют большого значения, однако они могут сильно повлиять на воздействие респирабельной пыли на рабочих, занятых переработкой минеральных полезных ископаемых. При правильной и своевременной уборке воздействие респирабельной пыли на рабочих может значительно снизиться. С другой стороны, при недостаточно частой или неправильно проводимой уборке результат может быть противоположный. При проведении одного исследования было зафиксировано увеличение воздействия пыли на рабочих при сухом подметании пола метлой. Средняя концентрация респирабельной пыли в зоне дыхания рабочих, находившихся на том же этаже, возросла с 0.03 мг/м3 (до подметания) до 0.17 мг/м3 во время и сразу после подметания (Рис. 8.4). Рекомендуется не использовать этот способ уборки из-за интенсивного загрязнения воздуха пылью[8- 1].
Часто случается, что материал просыпается. В этом случае первоначальную уборку материала часто проводят с помощью мини-погрузчика с ковшом (bobcat - “рыжая рысь”), или вручную лопатами. При уборке материала вручную рабочие должны использовать достаточно эффективные респираторы. После уборки основного объёма материала, или при общей уборке, желательно регулярно мыть помещение. В идеале, это нужно предусмотреть при проектировании здания – так, чтобы полы были с уклоном, и имелся дренаж для отвода воды. Хотя смывание очень эффективно, но нужно сказать, что это может привести к увеличению концентрации респирабельной пыли в воздухе во время уборки. При ударе воды о кучки мелкодисперсного материала может произойти попадание пыли в воздух. При использовании смывания для уборки, смыв грязи должен проводиться ежесменно или (как минимум) ежедневно, чтобы грязь не накапливалась.
Кроме смывания грязи для уборки широко используются уборочные машины и/или пылесосные вакуумные системы. Хотя такое оборудование стоит гораздо дороже, чем приспособления для смывания грязи, его использование не приводит к попаданию пыли в воздух в том количестве, в каком она попадает при смывании.
При решении вопроса о методе уборки полов Вы столкнётесь с тем, что множество изготовителей производит огромное количество разных типов уборочного оборудования. Некоторые машины перевозят оператора, а у других оператор идёт рядом с машиной (Рис. 8.5). Нужно проработать вопросы, относящиеся к выбрасыванию собранной пыли. Бессмысленно эффективно убирать полы для того, чтобы затем подвергать рабочего воздействию собранной пыли при её выбрасывании.
Кроме того, существуют разные виды пылесосного оборудования. Они различаются по своей производительности, могут быть стационарными (с разводкой труб по предприятию с узлами для подключения шлангов), и мобильными. Некоторые работодатели заключают договора с клиринговыми компаниями, которые применяют мощные мобильные установки, размещаемые на грузовиках, и приезжают для проведения уборки. Почти во всех случаях рабочий использует устройство для всасывания воздуха чтобы вручную собрать продукт и пыль в установку (Рис. 8.6). Такая уборка занимает много времени и её трудно выполнить в труднодоступных местах на заводе. В большинстве случаев такую уборку нельзя проводить ежесменно или ежедневно, так как это трудоёмкая работа. При использовании промышленных пылесосных установок нужно учесть риск электрических разрядов из-за накопления статического электричества во время уборки. Для уменьшения риска можно использовать не-электропроводные трубы или заземление.
Помимо смыва грязи водой, подметания, и использования промышленных пылесосов, для очистки полов на предприятиях, перерабатывающих полезные ископаемые, могут использоваться смеси для подметания полов. Обычно их не используют для уборки всего предприятия – а лишь в оживлённых местах и в очень запылённых местах, для уменьшения попадания пыли в воздух. Так как изготавливается много разных видов таких смесей, можно попробовать использовать разные виды на разных участках предприятия для определения эффективности в конкретных производственных условиях.
Уборка должна проводиться в конце каждой смены так, чтобы рабочие следующей смены приходили на убранные, чистые рабочие места. При проведении уборки в начале смены увеличивается риск загрязнения одежды, что увеличивает дозу вдыхаемой пыли в течение смены.
Наконец, на загрязнённость производственных и других помещений прямо влияет исправность и отрегулированность заводского оборудования, и совершенство технологии. Если Вы наблюдаете скопления материала на полу, это означает, что какие-то процессы или установки допускают утечки. В некоторых случаях можно визуально наблюдать вытекание пыли из отверстий в повреждённом оборудовании, и тогда для уменьшения утечки нужно сразу его ремонтировать. А если утечки пыли повторяются, нужно не просто устранить их, а выявить причину их появления и определить, какие нужны корректирующие действия для её устранения – для предотвращения утечек в будущем.
Для каждого технологического процесса или операции на предприятии должна быть разработана инструкция по его выполнению (Standard Operating Procedure, SOP) включающая регулярные проверки, техобслуживание, график проведения уборки. Регулярная уборка, техобслуживание и ремонт оборудования значительно уменьшают воздействие пыли из-за уменьшения её образования и её попадания в воздух и на пол.
Общий подход к проектированию заводской вентиляции[править]
Для уменьшения воздействия пыли на людей в любом здании эффективный план борьбы с пылью должен включать в себя улавливание пыли в главных местах её образования – до того, как она попадёт в воздух рабочей зоны и доберётся до рабочих. На большинстве предприятий, перерабатывающих минеральные полезные ископаемые, для борьбы с пылью используют стандартные технические средства коллективной защиты (местные вентиляционные отсосы, распыление воды, мокрые пылеуловители и промышленные электрофильтры), см. главу 1 “Принципы пылеулавливания”. Эти средства коллективной защиты достаточно эффективны для борьбы с пылью, попавшей в воздух, но они не позволяют устранить непрерывное накопление пыли, (которая затем) попадает в воздух из вторичных источников, таких как:
- Оседание материала на стенах, балках и другом оборудовании, так что пыль попадает в воздух при вибрации и при сильном ветре;
- Накопление продукта на дорожках для прохода, лестницах и других площадках, так что пыль может попасть в воздух при перемещении рабочих и из-за вибрации конструкций и оборудования;
- Просачивание или падение материала из лотков, конвейерных дорог и пылеуловителей;
- Источниками пыли могут стать повреждённые крышки ёмкостей и экраны, или пыль может попасть в воздух при их открывании для проверки и уборки, и
- Пыль может попадать в воздух и накапливаться из-за недостаточно хорошей организации проведения уборки.
Так как в большинстве случаев здания, в которых находится оборудование и происходит переработка минеральных полезных ископаемых, могут считаться закрытыми системами, то вышеуказанные вторичные источники пыли, а также множество других неназванных источников, могут привести к тому, что концентрация пыли в здании с каждым днём/сменой будет возрастать. Чтобы предотвратить возрастание концентрации пыли до опасной величины нужно бороться с вторичными источниками пыли. Один из наиболее эффективных методов борьбы – использование общеобменной вентиляции (total structure ventilation system).
Принцип работы общеобменной вентиляции[править]
Принцип работы общеобменной вентиляции – подавать в здание чистый окружающий воздух так, чтобы он проходил через здание и удалял запылённый воздух. Для этого используют перемещение воздуха снизу вверх, для чего устанавливают вытяжные вентиляторы в верхней части здания – вдали от рабочих мест как внутри, так и снаружи здания. Для определения количества и производительности этих вентиляторов используют информацию о начальной концентрации респирабельной пыли и общем объёме здания. Нужно сказать, что всё работающее заводское оборудование выделяет тепло, и на результат работы вентиляторов накладывается влияние подъёма вверх нагретого воздуха[8- 8][8- 9][8- 10]. На Рис. 8.7 показано, как работает такая общеобменная вентиляция. Чтобы использование общеобменной вентиляции давало желаемый эффект, должны выполняться три условия: в здание должен подаваться не загрязнённый воздух, воздух в здании должен перемещаться вверх, и у здания должна быть оболочка (стены) без разрывов.
Подача в здание чистого воздуха[править]
Подача чистого воздуха в здание происходит в нижней части здания – через проёмы в стенах, закрытые жалюзи; и через открытые двери. Очень важно, чтобы в подаваемом воздухе не было пыли из внешних источников – таких, как места загрузки материала, места с интенсивным движением транспорта. В противном случае подаваемый воздух может содержать респирабельную пыль, и его подача может увеличить запылённость на рабочих местах. В зависимости от внешних условий можно изменять положение мест, из которых воздух поступает в здание, закрывая двери и проёмы в стенах.
Эффективное восходящее движение воздуха[править]
Вентиляционная система должна создавать поток воздуха, движущийся вверх во всех частях здания, и удаляющий пыль от основных источников и с рабочих мест. При расположении вытяжных вентиляторов в верхней части здания (например – крышных вентиляторов), а проёмов для входа окружающего воздуха в нижней получается наиболее эффективный (для очистки всего здания) характер движения воздуха. Нужно заметить, что такая схема вентиляции не подходит для многоэтажных зданий со сплошными полами, не пропускающими воздух, так как это не позволяет “продувать” всё здание.
Наличие целостной оболочки (стен) в здании[править]
Competent Shell of Structure
Так как (всасывающая) вентиляционная система перемещает воздух из мест с наименьшим сопротивлением, оболочка здания – его стены – не должны иметь открытых проёмов. Стены должны быть сплошными, без открытых или разбитых окон, отверстий, щелей (особенно рядом с вытяжными вентиляторами). Вытяжные вентиляторы создают разрежение в здании, и если в его стенах будут проёмы, воздух начнёт двигаться через них – внося пыль от внешних источников, и не удаляя пыль от внутренних из-за соответственного уменьшения движения воздуха в здании.
При использовании этой общеобменной вентиляции воздухообмен в здании может быть на уровне 10-35 раз в час (acph). Было проведено два исследования общеобменной вентиляции всего здания для определения её эффективности. В первом исследовании при десятикратном воздухообмене во всём здании наблюдалось снижение концентрации респирабельной пыли на 40%. Во втором исследовании используемое оборудование позволяло обеспечить воздухообмен 17 и 34 раза в час. При этом снижение концентрации респирабельной пыли во всём здании было 47 и 74% соответственно[8- 10].
Параметры, влияющие на общеобменную вентиляцию[править]
На работу общеобменной вентиляции может влиять преобладающее направление ветра. При использовании крышных вентиляторов это влияние минимально, а при использовании вентиляторов, устанавливаемых на стенах, их нужно размещать в таких местах, чтобы при преобладающем направлении ветра он противодействовал их работе. В идеале вытяжные вентиляторы должны выбрасывать воздух в направлении преобладающего направления ветра. Это также уменьшает вероятность попадания выбрасываемого запылённого воздуха в здание вместе с подаваемым чистым.
Использование общеобменной вентиляции с большим воздухообменом зимой, при очень низкой температуре воздуха, может увеличить уязвимость оборудования из-за замерзания. Для решения этой проблемы нужно подогревать подаваемый воздух, но это требует очень больших расходов. Легче и проще снизить воздухообмен при низкой температуре окружающего воздуха. Для этого можно использовать вентиляторы с регулируемой частотой вращения, или отключать часть вентиляторов (если их много). Если уменьшение воздухообмена недопустимо, можно попробовать использовать установки для подогрева воздуха, подаваемого непосредственно на конкретные рабочие места.
Расходы[править]
Доказано, что использование общеобменной вентиляции для снижения концентрации респирабельной пыли во всём закрытом здании предприятия, перерабатывающего минеральные полезные ископаемые, является самым лучшим методом по критерию расходы/эффективность. Этот метод отличается не только небольшими капитальными затратами, но и низкими эксплуатационными расходами, включая техобслуживание (по сравнению с другими техническими средствами). Всё оборудование, необходимое для работы такой вентиляционной системы, может быть установлено своими силами, что уменьшит затраты.
Использование зданий с открытой конструкцией[править]
Open structure design
Для защиты от пыли, образующейся и попадающей в воздух при переработке минеральных полезных ископаемых, для уноса запылённого воздуха и его разбавления можно использовать окружающий чистый воздух. Поэтому в некоторых случаях для улучшения условий труда можно использовать здания с открытой конструкцией (open structure design). Проветривание зданий с такой конструкцией схоже с проветриванием зданий с помощью общеобменной вентиляции, так как позволяет уменьшить концентрацию пыли во всём здании. При использовании зданий такой конструкции окружающая среда используется как эффективное средство для разбавления и уноса пыли, образовавшейся и попавшей в воздух при работе оборудования. Во время выполнения работы не должно быть никаких визуально заметных выбросов пыли. Как и при использовании общеобменной вентиляционной системы, главной задачей остаётся улавливание пыли в главных местах её образования и попадания в воздух – до того, как она попадёт в воздух рабочей зоны и загрязнит помещение. Использование зданий с открытой конструкцией является дополнительным и вспомогательным методом защиты от той пыли, которую не удалось уловить в источнике.
Исследование производственных зданий трёх разных конструкций (со стенами из кирпича, открытой конструкции и стенами из листов стали (masonry, open-structure design, steel-sided design) показало, что в здании с открытой конструкцией концентрация пыли значительно ниже, чем в других [8- 11][8- 12]. На Рис. 8.8 показана схема здания с открытой конструкцией и с крышей, и для сравнения - аналогичное здание со стенами. Крыша незначительно увеличивает защиту от (атмосферного воздействия) по сравнению с полностью открытым зданием. Если рассматривается возможность использования здания с открытой конструкцией для размещения производственного оборудования, нужно учесть ряд обстоятельств:
- Материал, попавший в воздух из-за вибрации или сильного ветра, может скапливаться на стенах, балках и оборудовании.
- Использование здания с открытой конструкцией должно быть вторичным и вспомогательным методом снижения концентрации пыли. Нужно использовать технические средства коллективной защиты для улавливания пыли в месте её образования - до того, как она попадёт в воздух рабочей зоны, и загрязнит помещения.
- Нужно гарантировать надёжную защиту от падения для рабочих. Используйте защитные ограждения и перила.
- Нужно, чтобы рабочие и оборудование были защищены от неблагоприятного воздействия факторов окружающей среды (дождя, снега, мокрого снега и града). Для этого можно использовать такую конструкцию здания, чтобы его крыша была значительно шире основной части. Кроме того, при низких температурах воздуха может замёрзнуть оборудование.
С точки зрения требований имеющегося федерального законодательства единственное, что нужно учесть – это требования Агентства по охране окружающей среды EPA к отсутствию визуально заметных выбросов пыли. Имеется в виду качественный замер, проводимый федеральным инспектором – отсутствие визуально заметного факела пыли. Если хоть какие-то выбросы пыли из здания с открытой конструкцией будут видимы, нужно использовать главные методы защиты от пыли для устранения выбросов.
При использовании зданий с открытой конструкцией не только уменьшается концентрации респирабельной пыли, но и снижается воздействие шума на рабочих (так как у таких зданий нет отражения звука от стен). Очевидно, что строительство производственных зданий с открытой конструкцией (при строительстве новых предприятий) экономически выгодно, так как снижаются затраты на закупку стройматериалов и объём выполняемой работы. Некоторые компании могут захотеть переделать уже построенные здания, чтобы они стали более открытыми – чтобы дополнительно уменьшить концентрацию респирабельной пыли и уровень шума.
Фоновые источники пыли[править]
Если воздействие респирабельной пыли на рабочего превышает допустимое, то чаще всего предполагают, что это происходит при выполнении его основной работы. Проводилось исследование, которое показало, что во многих случаях это не так. Если измерения показывают, что воздействие респирабельной пыли на рабочего чрезмерно большое, то требуется определить – какую работу он выполняет, выявить источники пыли (вносящие вклад в воздействие на рабочего), и величину вклада каждого из источников. Иногда вторичные или фоновые источники пыли могут вносить основной вклад в общее воздействие.
Примеры вторичных источников пыли[править]
Ниже приводится несколько примеров, выявленных в процессе проведения исследований в производственных условиях, которые показывают, что вторичные источники пыли могут вносить значительный вклад в общее воздействие респирабельной пыли на рабочего[8- 13][8- 14][8- 15].
Попадание в здание пыли от источников, находящихся вне здания[править]
При попадании в здание той пыли, которая находилась снаружи здания, её воздействию может подвергаться любой рабочий. В большинстве случаев при заполнении бункеров материалом используется обеспыливающая вентиляционная система, отсасывающая воздух из бункера (для создания в нём разрежения) и отводящая загрязнённый воздух из зоны дыхания оператора (см. главу 6 “Фасовка”). Важно, чтобы воздух, поступающий на рабочие места и в зону дыхания вместо отсасываемого, был достаточно чистый. В одном из исследований во время проведения измерений обнаружилось что воздух, поступающий на рабочее место, приходил непосредственно с места загрузки материала в бункер вне здания. Пыль, попадавшая в воздух при загрузке материала в бункер, проходила в здание через открытую дверь, попадая на рабочие места. В те периоды времени, когда загрузка материала не проводилась, на рабочих местах в здании концентрация пыли была в среднем 0.17 мг/м3. А когда грузовик выгружал материал (вне здания) из-за притока загрязнённого воздуха средняя концентрация возрастала до 0.42 мг/м3 (Рис. 8.9). Исследование показало, что при использовании притока наружного воздуха взамен отсасываемого запылённого, приточный воздух должен браться там, где он не загрязнён.
Влияние индивидуальных особенностей выполнения работы на воздействие пыли на разных рабочих[править]
При измерениях эффективности четырёх разных методов уменьшения воздействия респирабельной пыли на рабочих оказалось, что у двух рабочих (выполнявших одинаковую работу) очень разное воздействие пыли. Рабочие вручную вставляли и вынимали мешки из устройства для их заполнения и укладывали их на ленточный конвейер. На Рис. 8.10 показаны результаты сравнения воздействия респирабельной пыли на двух рабочих, выполнявших одинаковую работу при использовании разных средств коллективной защиты (пронумерованы от 1 до 4). Обратите внимание на то, что во всех случаях воздействие респирабельной пыли на второго рабочего было значительно меньше, чем на первого. Главной причиной отличия было то, что первый рабочий выполнял свою работу менее аккуратно. В целом это привело к тому, что воздействие респирабельной пыли на второго рабочего было в среднем на 70% меньше, чем на первого.
Заметим, что второй рабочий всегда закрывал рукой клапан мешка после его извлечения из устройства для наполнения при переносе на конвейер (Рис. 8.11). Предположительно, именно это сыграло важную роль в уменьшении воздействия респирабельной пыли на второго рабочего. Сравнение отличий у этих двух рабочих показывает то, как характер выполнения работы влияет на воздействие пыли.
Разрыв мешков с материалом[править]
В большинстве случаев мешки рвутся из-за дефектов, возникших при их изготовлении. В одном конкретном случае было измерено увеличение концентрации пыли в зоне дыхания оператора до и после разрыва мешка. Она возросла с 0.07 мг/м3 до 0.48 мг/м3 – в среднем. Так как при движении мешка по конвейеру его разрыв происходит не непосредственно перед рабочим, пыль сильно загрязняет окружающий воздух, а затем он перемещается к оператору (Рис. 8.12). Это происходит из-за того, что на рабочем месте оператора работает местный вентиляционный отсос, создающий разрежение, которое заставляет (загрязнённый) окружающий воздух двигаться в сторону оператора.
Тканевая обивка сидений и звукопоглощающие покрытия[править]
При переработке минеральных полезных ископаемых рабочим часто приходится сидеть во время выполнения работы. Это справедливо и для операторов мобильного оборудования; тех, кто работает в пультах управления; операторов дробильного и размалывающего оборудования; для некоторых операторов оборудования, наполняющего мешки; операторов, следящих за загрузкой ёмкостей; водителей вилочных погрузчиков; сотрудников лабораторий и др. Помимо “сидячих” рабочих мест люди могут сидеть и в других местах – в столовой, помещениях для отдыха и др. (чтобы ноги отдохнули). Если эти сиденья покрыты тканью, то в ней может накопиться много грязи, и при посадке рабочего на сиденье и последующих движениях (уже сидя) в воздух попадёт много пыли. Поэтому нельзя использовать стулья с тканевой обивкой, а нужно использовать пластиковые виниловые сиденья. Но если покрытие такого сиденья протрётся так сильно, что станет виден поролон, его нужно менять – так как поролон тоже может накапливать много грязи, и он может стать источником пыли.
При использовании шумопоглощающих покрытий для уменьшения воздействия шума (от оборудования, в закрытых кабинах и т.п.) нужно выбирать подходящие материалы. При старении материала, и при использовании поролона, такое покрытие тоже может накапливать пыль и становиться источником загрязнения воздуха – как и ткань на сиденьях.
Загрязнённая рабочая обувь[править]
Как и загрязнённая одежда, грязная обувь становится дополнительным источником пыли, воздействующей на рабочих. Это происходит, когда рабочий проходит по влажному продукту, когда перегружает его, при образовании слякоти, и/или когда материал прилипает к обуви. При переработке минеральных полезных ископаемых сырые условия (из-за дождя или при использовании мокрых методов борьбы с пылью) – не редкость. Как только обувь испачкалась, рабочий разносит грязь повсюду, куда ходит – пока грязь не оторвётся или пока обувь не будет почищена. На Рис. 8.13 показано, как в кабине мобильного оборудования накопилась грязь, принесённая на грязной обуви. Очевидно, что такое количество грязи может создать большую запылённость при попадании материала в воздух.
Если условия работы такие, что в рабочую зону приносится много материала, пыли, то нужно проводить уборку – ежедневно или ежесменно. В других случаях, когда загрязнение слабее, уборку можно проводить реже, но в любом случае важно свести к минимуму воздействие пыли на рабочих, возникающее из-за этой грязи.
Для уменьшения количества пыли, попадающей в воздух из-за выноса грязи, было проверено и показало себя эффективным использование связывающих добавок (sweeping compounds). Было проведено исследование того, как применение без-зернистых добавок, не содержащих нефтепродукты, снижает запылённость в закрытых кабинах[8- 16]. На Рис. 8.14 показаны средние концентрации респирабельной пыли в двух закрытых кабинах для трёх-пяти смен, при использовании и при не использовании добавок. Полученные концентрации респирабельной пыли показали снижение концентрации с 0.18 и 0.68 мг/м3 до 0.07 и 0.12 мг/м3 для двух буровых установок соответственно. Эти результаты показывают, что использование добавок снижает концентрацию респирабельной пыли в тех случаях, когда происходит прямой контакт и есть возможность образовать связь между добавкой и грязью на полу или резиновом коврике, лежащем на полу.
Нужно заметить, что перед тем, как использовать какую-нибудь из добавок, работодатель должен проверить её паспорт безопасности (Material Safety Data Sheet MSDS) чтобы гарантировать, что в ней нет компонент, способных оказать вредное воздействие на рабочих в закрытых кабинах. Кроме того, эти добавки нужно своевременно заменять – как только они насытились грязью до такой степени, что не способны больше связывать новую грязь.
В каких-то случаях для уменьшения распространения грязи может оказаться практичнее установить приспособление для мытья и очистки обуви. Такие приспособления относительно недороги, и могут устанавливаться в разных местах вокруг места работы в грязных условиях.
Техобслуживание[править]
Для эффективной защиты рабочих от пыли большое значение имеет проведение техобслуживание средств коллективной защиты[8- 17]. Нужно разработать расписание проведения работ по техобслуживанию и профилактическому ремонту на основе результатов измерений концентраций пыли, показателей работы оборудования, и его наблюдаемого износа.
Рекомендации по защите от пыли при проведении техобслуживания[править]
При проведении техобслуживания рабочие могут подвергаться более сильному воздействию пыли из-за того, что для выполнения работы они могут находиться там, где средства коллективной защиты не работают или плохо работают; или потому, что ремонт может выполняться в условиях, отличающихся от обычных, ежесменных. Рекомендуется:
- При необходимости очищайте оборудование и места проведения работ с помощью мокрой уборки или с помощью пылесосного оборудования – до начала работы и во время работы. Работа в загрязнённом месте увеличивает воздействие пыли на рабочих.
- Как можно чаще используйте приспособления, позволяющие выполнять работу на удалении от источника пыли и грязи. Это уменьшает вероятность воздействия пыли и грязи на рабочих, проводящих техобслуживание, из-за меньшего контакта с загрязнёнными частями оборудования (ограждениями, кожухами и др.).
- При замене и очистке загрязнённых воздушных фильтров (мобильного оборудования, кабин, пультов управления и рабочих мест операторов) делайте это вдали от мест забора чистого наружного воздуха и воздуха для систем рециркуляции. Нужно уделять внимание эффективности фильтров, когда требуется их замена. Более подробная информация приводится в главе 9 “Кабины операторов, пульты управления и кабины мобильного оборудования”.
- Обеспечьте проходы к тому оборудованию, у которого проводится регулярное техобслуживание. Это уменьшит воздействие пыли при перелезании через (загрязнённое) оборудование и т.п.
- Для уменьшения воздействия пыли на рабочих используйте подъёмное оборудование и другую механизацию.
- Сразу после завершения проведения техобслуживания очищайте загрязнённую спецодежду с помощью кабины для очистки, или другого оборудования. См. раздел “Удаление пыли с загрязнённой рабочей одежды” в этой главе выше. Кроме того, носка пылезащитной одежды (типа Tyvek™ или Kleenguard™), может значительно уменьшить загрязнение рабочей одежды и перенос пыли на чистые рабочие места и домой (рабочим).
- При носке перчаток используйте такие, у которых нет пор, где может накапливаться пыль, так как это может увеличить воздействие на рабочих.
- Когда возможно, мойте мобильное оборудование перед его закатыванием в места проведения техобслуживания (для ремонта).
- Не используйте сжатый воздух для очистки.
- Периодически очищайте внутреннюю поверхность кабин (мобильного оборудования, пультов управления, рабочих мест операторов) для удаления накапливающихся пыли, материала и грязи.
.
ССЫЛКИ
- ↑ 1,0 1,1 USBM [1986]. Impact of background sources on dust exposure of bag machine operator. By Cecala AB, Thimons ED. U.S. Department of the Interior, Bureau of Mines Information Circular 9089.
- ↑ Pollock DE, Cecala AB, O'Brien AD, Zimmer JA, Howell JL [2005]. Dusting off. Rock Products. March. pp. 30–34.
- ↑ Langenhove LV, Hertleer C [2004]. Smart clothing: a new life. Inter J of Clothing Science and Tech. 16(1&2):63–72.
- ↑ Hartsky MA, Reed KL, Warheit DB [2000]. Assessments of the barrier effectiveness of protective clothing fabrics to aerosols of chrysotile asbestos fibers. Performance of Protective Clothing: Issues and Priorities for the 21st Century: Seventh Volume, ASTM STP 1386, pp. 141–154.
- ↑ Salusbury I [2004]. Tailor-made-self-cleaning clothing, chemical warfare suits that trap toxins. Materials World. August. pp. 18–20.
- ↑ Cecala AB, O'Brien AD, Pollock DE, Zimmer JA, Howell JL, McWilliams LJ [2007]. Reducing respirable dust exposure of workers using an improved clothes cleaning process. Inter J of Min Res Eng 12(2):73–94.
- ↑ Cecala AB, Pollock DE, Zimmer JA, O'Brien AD, Fox WF [2008]. Reducing dust exposure from contaminated work clothing with a stand-alone cleaning system. In: Wallace, ed. Proceedings of 12th U.S./North American Mine Ventilation Symposium. Omnipress. ISMN 978–0–615–20009–5, pp. 637–643.
- ↑ Cecala AB, Mucha R [1991]. General ventilation reduces mill dust concentrations. Pit & Quarry 84(1):48–53.
- ↑ Cecala AB [1998]. Supplementing your dust control equipment with whole-plant ventilation. Powder & Bulk Engineering 12(1):19–32. http://www.powderbulk.com/browse-articles/
- ↑ 10,0 10,1 Cecala AB, Klinowski GW, Thimons ED [1995]. Reducing respirable dust concentrations at mineral processing facilities using total mill ventilation system. Min Eng 47(6):575–576.
- ↑ Cecala AB, Rider JP, Zimmer JA, Timko RJ [2007]. Dial down dust and noise exposure. Aggregates Manager 12(7):50–53. www.google.ru/url?sa=t&rct=j&q=&esrc=s&source=web&cd=1&ved=0CBwQFjAA&url=http%3A%2F%2Fstacks.cdc.gov%2Fview%2Fcdc%2F8651%2Fcdc_8651_DS1.pdf&ei=BaMBVZLrJYn_ygOw9IHYAw&usg=AFQjCNG3_hT7RCuUnq1a38qN0pqPJ_5fhw&bvm=bv.87920726,d.bGQ&cad=rjt
- ↑ USBM [2006]. Lower respirable dust and noise exposure with an open structure design. By Cecala AB, Rider JP, Zimmer JA, Timko RJ. U.S. Department of Health and Human Services, Centers for Disease Control and Prevention, National Institute for Occupational Safety and Health, NIOSH Report of Investigations 9670.
- ↑ Cecala AB, Thimons ED [1987]. Significant dust exposures from background sources. Pit & Quarry 79(12):46–51.
- ↑ USBM [1988]. Technology news 299: Reduce bagging machine operator's dust exposure by controlling background dust sources. U.S. Department of the Interior, Bureau of Mines.
- ↑ Cecala AB, Thimons ED [1992]. Some factors impacting bag operator's dust exposure. Pit & Quarry 85(5):38–40.
- ↑ NIOSH [2001]. Technology news 487: Sweeping compound application reduces dust from soiled floor within enclosed operator cabs. By Organiscak JA, Page SJ, Cecala AB. Pittsburgh, PA: U.S. Department of Health and Human Services, Centers for Disease Control and Prevention, National Institute for Occupational Safety and Health.
- ↑ USBM [1974]. Survey of past and present methods used to control respirable dust in noncoal mines and ore processing mills–final report. U.S. Department of the Interior, Bureau of Mines Contract No. H0220030. NTIS No. PB 240 662.
ГЛАВА 9. Кабины операторов, пульты управления и кабины мобильного оборудования[править]
Для защиты рабочих от пыли при добыче и переработке минеральных полезных ископаемых уже много лет используют изоляцию рабочих от запылённой атмосферы в кабинах. При хорошей конструкции, правильной установке и исправном состоянии такие кабины могут обеспечить создание здоровых и безопасных условий труда, обеспечивая рабочего достаточным количеством чистого и пригодногом для дыхания воздуха. За последнее десятилетие в этой области было проведено множество исследований, что позволило выявить потенциальные проблемы, пути их решения и главные факторы, определяющие эффективность кабин.
Рабочий, находящийся в кабине, окружён различными динамично изменяющимися источниками пыли. А кабины создают микроклимат, в котором рабочих будет подвергаться воздействию респирабельной пыли или в меньшей степени, или в большей степени. Воздействие пыли на рабочих в кабине может быть повышенным из-за внутрикабинных источников пыли (подогреватели пола, грязь на полу и стенах, грязь на одежде и др.). Кабины мобильного оборудования труднее обслуживать и поддерживать в исправном и чистом состоянии, чем стационарные кабины, поскольку перемещение оборудования создаёт дополнительный риск нарушения целостности и герметичности кабины.
На Рис. 9.1 показана общая схема вентиляции кабины. При добыче и переработке минеральных полезных ископаемых для защиты от пыли операторов, находящихся в закрытых кабинах, в первую очередь нужно использовать вентиляционные системы очистки и подачи воздуха в кабину. В таких кабинах должна быть эффективная система фильтрации воздуха, очищающая как наружный, так и внутренний воздух, а сама кабина должна быть достаточно герметичной, чтобы в ней можно было поддерживать избыточное давление. Эффективные системы очистки воздуха и создания избыточного давления в кабине объединяют в блоки отопления, вентиляции и кондиционирования (heating, ventilating and air-conditioning [HVAC] units). Для того, чтобы улучшить качество воздуха в закрытых кабинах при наземной добыче полезных ископаемых, было проведено много исследований, и результаты этих исследований можно применять к пылезащитным кабинам операторов и помещениям пультов управления.
Терминология, используемая для оценки эффективности[править]
При изучении оборудования, обеспечивающего очистку воздуха и создание избыточного давления, для описания эффективности таких систем могут использоваться разные критерии. Ниже приводятся те показатели эффективности, которые нашли широкое применение:
- Коэффициент защиты КЗ (Protection Factor PF) = отношение наружной концентрации (Со) к внутрикабинной (Ci) = Со/Сi;
- Эффективность (Efficiency, η) = (Со-Сi)/Co – как десятичная дробь, или как проценты (после умножения на 100).
- Проникание (Penetration, Pen) = 1 – η; - как десятичная дробь.
где Co = наружная концентрация респирабельной пыли, а Ci = внутрикабинная концентрация респирабельной пыли. Ниже приводятся формулы, описывающие взаимосвязи между указанными показателями эффективности.
- PF = Сo/Ci = 1/(1- η) = 1/Pen (Уравнение 9.1) (СИ, IP)
Очевидно, что чем больше будет значение коэффициента защиты и эффективности, и чем меньше будет значение проникания, и тем выше будет качество воздуха в кабине оператора. Для примера в таблице 9.1 приводится сравнение значений трёх показателей при разном качестве воздуха в кабине.
Коэффициент защиты | Эффективность, % | Проникание |
---|---|---|
2 | 50 | 0.50 |
5 | 80 | 0.20 |
10 | 90 | 0.10 |
100 | 99 | 0.01 |
1 000 | 99.9 | 0.001 |
В этой главе для оценки эффективности защиты от пыли будет использоваться коэффициент защиты КЗ (PF).
Система очистки воздуха и поддержания избыточного давления в кабине[править]
Результаты исследований в производственных условиях[править]
Проведение медосмотров в центральной Пенсильвании в середине 1990-х выявило значительное число случаев развития силикоза у операторов мобильного оборудования при использовании закрытых кабин, не обеспечивающих требуемый уровень защиты[9- 1]. Поэтому разные организации начали изучать кабины чтобы лучше разобраться в их недостатках и найти пути их устранения для улучшения качества воздуха и защиты рабочих. При проведении некоторых из этих исследований новые блоки очистки и подачи воздуха устанавливали на старые кабины для улучшения качества воздуха в них. В таблице 9.2 приводятся результаты некоторых из проведённых исследований – в порядке повышения эффективности защиты[9- 2][9- 3][9- 4][9- 5].
Оборудование | Избыточное давление в кабине, Па (дюймы вод. ст.) | Средняя концентрация пыли, мг/м3 | Коэффициент защиты КЗ | |
---|---|---|---|---|
в кабине | снаружи | |||
1. Буровая установка | Наличие не обнаружено | 0.08 | 0.22 | 2.8 |
2. Самосвал | 2.5 (0.01) | 0.32 | 1.01 | 3.2 |
3. Ковшовый погрузчик | 3.7 (0.015) | 0.03 | 0.30 | 10.0 |
4. Буровая установка | 50÷100 (0.20÷0.40) | 0.05 | 2.80 | 56.0 |
5. Буровая установка | 17÷30 (0.07÷0.12) | 0.07 | 6.25 | 89.3 |
Эти исследования позволили выявить некоторые очень важные факторы, от которых зависит качество воздуха в кабинах и в конечном счёте – сохранение здоровья рабочих. Очень важна герметичность кабин, и соответственно – их способность сохранять избыточное давление. Два исследования, результаты которых приведены в двух верхних строках таблицы 9.2, показали что отсутствие избыточного давления или его небольшая величина приводят к незначительному повышению качества воздуха в кабине. При установке идентичных блоков очистки и подачи воздуха на буровую установку (строка 1) и на ковшовый погрузчик (строка 3) значения КЗ составили 2.8 и 10. При работе блока очистки и подачи в первом случае не удалось создать избыточное давление, а во втором – удалось, хотя и небольшое. Также нужно заметить, что низкая запылённость наружного воздуха может отрицательно сказаться на КЗ.
Другим важным фактором было качество и эффективность системы очистки и подачи воздуха. При проведении разных исследований, показанных в таблице 9.2, обнаружилось значительное улучшение качества воздуха в кабине при эффективном улавливании частиц из подаваемого в кабину окружающего воздуха. Если удавалось создать достаточно большое, то удавалось получить хорошее качество воздуха в кабине – как это показывают большие значения КЗ.
Лабораторные исследования[править]
В результате проведения исследований в различных производственных условиях был выявлен ряд разных факторов, которые определяли эффективности системы очистки и подачи воздуха. Для изучения этих факторов были проведены исследования в контролируемых лабораторных условиях, что позволило систематично изучить кабины разной конструкции. На Рис. 9.2 показана схема лабораторной установки, использовавшейся для проведения лабораторного исследования, и параметры, которые изучались[9- 6][9- 7].
На Рис. 9.2, приводятся следующие параметры: PF = protection factor, коэффициент защиты КЗ = Co/Ci; Co = концентрация пыли снаружи кабины; Ci = концентрация пыли в кабине; ηi = эффективность очистки наружного воздуха, как десятичная дробь; Qi = количество подаваемого воздуха; QL = количество просачивающегося воздуха; l = доля просачивающегося неочищенного воздуха, QL/Qi; ηr = эффективность фильтра, используемого для очистки рециркулирующего воздуха; QR = количество воздуха, который очищается при рециркуляции; Qw = количество воздуха, просочившегося из-за ветра; и Vc = объём кабины.
Результаты этого исследования показали, что на качество воздуха в кабине в наибольшей степени влияет степень очистки подаваемого воздуха, и использование фильтров, очищающих рециркулирующий воздух. При анализе работы фильтра для очистки приточного воздуха оказалось, что наличие очистки рециркулирующего воздуха значительно улучшает итоговое качество воздуха из-за многократно повторяющейся очистки внутреннего воздуха в кабине. А добавка вентилятора подачи наружного воздуха заметно увеличивает и давление в кабине, и расход приточного воздуха. На качество воздуха в кабине также влияют загрязнение фильтра очистки приточного воздуха и просачивание неотфильтрованного воздуха.
Математическая модель для определения коэффициента защиты закрытой кабины
При проведении исследования кабины в лабораторных условиях изучалось влияние параметров системы очистки и подачи воздуха, и была разработана математическая модель. В безразмерном уравнении 9.2 (где эффективность выражена как десятичная дробь, а не в процентах) должны использоваться расходы воздуха, измеренные в одинаковых единицах, а эффективность фильтров должна описываться как десятичная дробь. Для определения КЗ в уравнении используются эффективность фильтра очистки приточного воздуха, расхода приточного воздуха, просачивания неотфильтрованного воздуха, эффективности фильтра очистки рециркулирующего воздуха, расхода рециркулирующего воздуха, и просачивания неотфильтрованного воздуха в кабину из-за ветра. При выводе уравнения использовали модель зависимости массы (вредных) веществ в воздухе помещения в зависимости от времени (time-dependent mass balance model of airborne substances).
- КЗ = PF = Co/Ci = ( Qi + Qr × ηr ) / ( Qi × [ 1 – ηi + l × ηi ] + Qw ) (Уравнение 9.2) (СИ, IP)
Уравнение 9.2 позволяет оценить, как изменения разных параметров системы и её составных частей влияют на коэффициент защиты КЗ. Если давление в кабине выше скоростного напора, создаваемого ветром, то можно считать, что просачивание неотфильтрованного воздуха из-за ветра равно нулю (Рис. 9.3). С помощью уравнения 9.2 можно определить то, какими должны быть параметры вентиляционной системы для получения желаемого значения КЗ – так, чтобы улучшить качество воздуха и защитить рабочих в требуемой степени.
Рекомендации для блока очистки и подачи воздуха[править]
На основе информации, полученной при проведении лабораторного и производственных исследований, разработаны рекомендации, которые нужно использовать для того, чтобы система подачи и очистки воздуха обеспечивала эффективную защиту.
Обеспечение герметичности кабины для создания избыточного давления, способного противодействовать поддуву из-за ветра[править]
Для того, чтобы система эффективно защищала оператора, необходимо создать в помещении кабины избыточное давление, что при негерметичности кабины невозможно. Измерения показали, что на величину избыточного давления сильно влияют изолирующие уплотнения на новых дверях, и герметизация трещин и отверстий в стенах кабины. Для предотвращения просачивания неотфильтрованного воздуха в кабину избыточное давление должно быть больше, чем скоростной напор ветра[9- 8]. Для определения той скорости ветра, при которой кабина может защитить (при данном избыточном давлении) можно использовать уравнение 9.3:
- Эквивалентная скорость ветра (м/с) = 20.32 × ([Δр/249]1/2) = 1.288 × [Δр]1/2 (Уравнение 9.3) (СИ)
- при стандартных давлении и температуре, и избыточном давлении Δр в Паскалях
- Эквивалентная скорость ветра (миль/час) = (4000*[Δр]1/2) * 0.011364 (миль/час / футов/мин) (Уравнение 9.3) (IP)
- при стандартных давлении и температуре, и избыточном давлении Δр в дюймах водяного столба.
На Рис. 9.3 приводится зависимость эквивалентной скорости ветра от избыточного давления в кабине. Видно, что при давлении 12, 25, 62, 125 и 249 Па (0.05, 0.1, 0.25, 0.5 и 1.0 inches wg) кабина будет защищена от просачивания из-за давления ветра при скорости воздуха до 4.5, 6.4, 10.1, 14.4 и 20.3 м/с (10.2, 14.4, 22.7, 32.1 и 45.5 mph). Хотя проведение исследований в производственных условиях показало, что даже небольшое избыточное давление в кабине оказывает положительное влияние на уменьшение вредного воздействия, на основании накопленного опыта можно рекомендовать поддерживать давление не ниже 12 Па, а оптимально – не ниже 12÷62 Па (0.05, 0.05 и 0.25 inches wg).
Для изоляции кабины её двери и окна должны быть всегда закрыты[править]
Чтобы в кабине было избыточное давление необходимо, чтобы двери и окна были закрыты всё время – кроме тех случаев, когда нужно войти или выйти из кабины. Эта проблема проявилась при проведении исследования в производственных условиях, когда оператор буровой установки многократно открывал дверь кабины чтобы вручную наращивать длину бура[9- 9][9- 10]. При этом дверь открывалась на период от 20 до 45 секунд. Так как дверь открывалась тогда, когда бурение не проводилось, и не было видно облака дыма, то казалось, что это не оказывает значительного влияния на воздействие респирабельной пыли на оператора. Но анализ результатов измерений, проводившихся в кабине, показал что в те периоды, когда дверь была открыта, произошло значительное увеличение концентрации респирабельной пыли. Это оказалось неожиданным, так как бурение прекращалось примерно за 2 минуты до того, как открывалась дверь. На Рис. 9.4 показаны средние концентрации для трёх дней, когда проводились измерения, в те периоды времени, когда дверь была открыта, и когда закрыта. В среднем при закрытой двери концентрация была 0.09 мг/м3, а при открытой – 0.81 мг/м3. Хотя никакого облака визуально заметной пыли не было, во время бурения при закрытой двери концентрация респирабельной пыли была в 9 раз ниже.
Полученные результаты наглядно показали, что важно держать все двери и окна закрытыми всё время, чтобы сохранять избыточное давление в кабине. Единственное исключение – случаи, когда оператор входит или выходит из кабины. Нужно подчеркнуть, что даже при отсутствии визуально заметного облака пыли (снаружи), концентрация респирабельной пыли вне кабины может быть значительно выше, чем в кабине.
Эффективная фильтрация воздуха[править]
Чтобы эффективно очищать воздух и чтобы обеспечить оператора в кабине чистым воздухом, нужно обеспечить очистку и приточного воздуха, и очистку рециркулирующего воздуха.
Эффективная очистка наружного воздуха и создание избыточного давления в кабине
Для того, чтобы не допустить повышения концентрации углекислого газа в кабине, нужно подавать в неё не менее 12 л/сек (25 cfm) (очищенного) отфильтрованного воздуха на каждого человека, находящегося в кабине[9- 11]. Обычно у большинства кабин этот показатель находится в пределах от 19 до 33 л/сек на 1 человека (40÷70 cfm). Единственный способ создать и сохранять избыточное давление в кабине – подавать в неё воздух извне, а наличие избыточного давления необходимо для обеспечения эффективной защиты. Расход подаваемого в кабину воздуха должен тщательно контролироваться и оптимизироваться. После выявления оптимального режима и соответствующего расхода воздуха, превышение этого расхода ухудшает эффективность защиты из-за увеличения проникания частиц и ухудшения эффективности фильтра (через который начинает проникать больше частиц).
При подаче наружного отфильтрованного воздуха в кабину оптимальный расход воздуха должен обеспечивать требуемое избыточное давление - и не более того (так как больший расход воздуха снизит качество воздуха в кабине). Чтобы показать это, мы использовали коэффициент защиты, который вычисляли с помощью математической модели, разработанной во время проведения лабораторного исследования. Рассмотрим пример, в котором будем считать, что расход воздуха в системе рециркуляции составляет (QR) = 141.5 л/сек (300 cfm), степень очистки рециркуляционного фильтра 70%, расход приточного воздуха (QI) = 23.6 л/сек (50 cfm), степень очистки приточного воздуха 95%, а просачивание неотфильтрованного воздуха отсутствует (l=0). Предположим, что расход подаваемого воздуха (QI) возрос с 23.6 до 33 л/сек (50 → 70 cfm). Это приведёт к уменьшению коэффициента защиты с 104 до 80 (при увеличении подачи воздуха в кабину на 9.4 л/сек).
Необходимо, чтобы наружный воздух, подаваемый в кабину, пропускался через высокоэффективные фильтры. Результаты лабораторного исследования показали, что при увеличении степени очистки подаваемого в кабину наружного воздуха с 38 до 99% количество респирабельной пыли в ней уменьшилось в 10 раз. Оптимальная подача воздуха должна создавать такое избыточное давление, при котором не будет просачивания неотфильтрованного воздуха через зазоры из-за ветра, но который не будет создавать излишнюю нагрузку на фильтры вентиляционной системы. Кроме того, нужно поддерживать оптимальную температуру подаваемого воздуха – или подогревать его зимой, или охлаждать летом. А увеличение расхода воздуха приведёт к увеличению затрат на поддержание необходимой температуры.
Расположение места забора наружного воздуха.
Имеет значение то, в каком месте всасывается окружающий воздух для подачи в кабину. Если воздух будет всасываться около источников большого количества пыли, это создаст повышенную нагрузку на систему фильтрации. Это приведёт к загрязнению фильтров и уменьшит эффективность защиты из-за уменьшения избыточного давления в кабине (из-за уменьшения подачи воздуха в кабину). А увеличение перепада давления на (загрязнённом) фильтре увеличит риск просачивания пыли через картридж фильтра. Увеличение концентрации пыли во всасываемом воздухе потребует более частой замены фильтров или проведения более частой очистки фильтров, что увеличит расходы. Наконец, фильтр очищает воздух с какой-то конечной эффективностью, и увеличение концентрации пыли в очищаемом воздухе соответственно увеличит концентрацию пыли в очищенном воздухе, подаваемом в кабину, и в воздухе кабины.
Для предотвращения этих негативных последствий требуется размещать место всасывания наружного воздуха вдали от источников пыли для уменьшения загрязнения фильтра[9- 12]. Для этого всасывающее отверстие обычно располагают повыше (дальше от земли); и на той стороне кабины, которая находится с противоположной стороны от источника пыли. Это также приводит к тому, что кабина отчасти заслоняет собой всасывающее отверстие от некоторой части пыли.
Использование предфильтра
При фильтрации окружающего воздуха рекомендуется использовать не один, а два фильтра – предфильтр для грубой очистки от крупных частиц, и за ним фильтр более высокой эффективности. Использование предфильтра продлит срок службы основного фильтра и увеличит его эффективность. Для предварительной очистки воздуха от наиболее крупных частиц может использоваться или центробежный пылеуловитель, или фильтр (с регенерацией с помощью обратной продувки сжатым воздухом). Обратная продувка картриджа для удаления накопившейся уловленной пыли может проводиться через заранее заданные интервалы времени, или при увеличении перепада давления сверх заданной величины.
Использование эффективной рециркуляционной системы очистки
Для надёжной защиты рабочего в кабине важно использовать вентиляционную систему, которая берёт воздух в кабине, очищает его и снова подаёт в кабину (режим рециркуляции). Лабораторные исследования показали, что эффективность защиты от респирабельной пыли (КЗ) возрастает в 10 раз при использовании системы очистки рециркулирующего воздуха с фильтром эффективностью 85÷94.9% (по сравнению с отсутствием рециркуляционной системы очистки). Результаты лабораторного исследования также показали, что при использовании системы очистки рециркулирующего воздуха концентрация пыли в кабине снижается до стабильного уровня (после открывания дверей) в 2 раза быстрее. Без очистки рециркулирующего воздуха на стабилизацию концентрации уходило в среднем от 16 до 29 минут, а при очистке – от 6 до 11 минут (в среднем). Таким образом, использование очистки воздуха в системе рециркуляции значительно улучшает качество воздуха и уменьшает длительность воздействия пыли после закрывания двери кабины[9- 13]. Ещё одно достоинство использования такой системы – то, что можно пропустить очищенный рециркулирующий воздух через систему отопления и кондиционирования, что позволить поддерживать стабильную температуру в кабине.
Подогреватели воздуха, выпускающие нагретый воздух у пола[править]
Нужно исключить использование любых устройств для подогрева воздуха или вентиляторов, расположенных около пола, так как они могут увеличить запылённость воздуха в кабине. Результаты исследования, проводившегося в производственных условиях, показали что вентилятор отопительного устройства, расположенный около пола, и использовавшийся зимой для обогрева кабины буровой установки, сильно увеличивал концентрацию пыли в кабине (Рис. 9.5)[9- 14][9- 15].
Поскольку пол является самым грязным местом в кабине, работа отопительной системы (выпускающей тёплый воздух на пол) может создать серьёзные проблемы. Оператор заносит грязь в кабину на обуви, и при её перемещении образуется пыль, которая разносится вентилятором отопительной системы по всей кабине. Этот вентилятор также стремиться поднять, сдуть в воздух пыль, которая может находиться на одежде оператора буровой установки. Из-за того, что такие отопительные установки сильно увеличивают запылённость воздуха, их не следует использовать вообще, а когда это невозможно – их нужно переместить выше так, чтобы они в меньшей степени поднимали пыль с пола и сдували её с одежды оператора. Кроме того, в кабине не должно быть никаких вентиляторов около пола, так как их работа может привести к попаданию пыли в воздух. В идеале, подогреватель воздуха должен входить в состав блока очистки и подачи – чтобы подогретый воздух подавался с верхней части кабины вниз.
Поддержание чистоты (в кабине и в вентиляционной системе)[править]
Чтобы обеспечить нормальное функционирование системы подачи и очистки воздуха в кабину, необходимо проводить очистку и своевременное техобслуживание (замена фильтров при необходимости и т.п.). Кроме того, при проведении техобслуживания нужно проверять целостность вентиляционной системы, состояние прокладок и т.п. – то, от чего зависит её герметичность (а также наличие трещин, засоров и т.п.). Без необходимого техобслуживания и ремонта с течением времени вентиляционная система изнашивается и повреждается – так, что со временем перестаёт обеспечивать требуемый уровень защиты, что приводит к чрезмерному воздействию на рабочих респирабельной пыли.
При проведении исследований в производственных условиях мы много раз сталкивались с загрязнённым, изношенным и повреждённым вентиляционным оборудованием – таким, что оно (уже) не могло обеспечивать требуемый уровень защиты рабочих (Рис. 9.6 слева). В некоторых случаях становилось видно, что на первом месте была не защита от пыли, а комфорт (например – температура воздуха). Хотя во многих закрытых кабинах есть оборудование для подогрева и охлаждения воздуха, иногда рабочие просто открывали окна (для удобства и комфорта), что снижало эффективность защиты от пыли. При небольших финансовых затратах и небольших усилиях можно обеспечить эффективное техобслуживание систем подачи и очистки воздуха – так, что через небольшой промежуток времени они снова станут обеспечивать рабочих чистым воздухом высокого качества (Рис. 9.6 справа).
Когда рабочие входят в кабину из места работы, они приносят с собой грязь и материал, которые скапливаются на полу. Если поступление грязи в кабину большое, нужно проводить уборку кабины ежедневно или ежесменно. Если поступление грязи в кабину меньше, уборку можно проводить реже. Уборка должна проводиться так, чтобы внутренние поверхности кабины были в таком состоянии, которое сводит воздействие респирабельной пыли на рабочих к минимуму.
Использование фильтров без электростатического осаждения частиц и визуальная индикация необходимости замены фильтра[править]
Для очистки наружного и рециркулирующего воздуха рекомендуется использовать механические фильтры без электростатического осаждения частиц. По мере загрязнения не-электростатических фильтров их эффективность возрастает. Это происходит из-за того, что при улавливании частиц они образуют слой на поверхности фильтра (или его волокон), который затем сам начинает улавливать пыль. Но при увеличении толщины слоя уловленных частиц возрастает сопротивление движению воздуха, и уменьшается его расход. При дальнейшем увеличении сопротивления наступает момент, когда фильтр нужно заменить или очистить. В идеале система очистки и подачи воздуха должна включать в себя индикатор, сигнализирующий о необходимости замены (или очистки).
Удобность замены фильтров[править]
При проектировании системы очистки и подачи воздуха, очень важно обеспечить удобность замены фильтров (когда это необходимо). Систему нельзя считать хорошей, если замена фильтров настолько затруднена, что рабочие или ремонтники избегают тратить времени на выполнения этой работы. Другой важный вопрос – загрязнение пылью при замене фильтров. Фильтры должны быть легко заменяемы, и при их замене не должно происходить значительного загрязнения (уловленной) пылью ни рабочего, ни окружающего пространства. При замене фильтра, выполненного в виде картриджа, рекомендуется вынимать новый фильтр из его картонной упаковки, и затем помещать в неё старый загрязнённый фильтр. Затем можно заклеить коробку липкой лентой, и выбросить его.
Оптимальное движение воздуха в кабине[править]
Если обстоятельства позволяют, то для максимального улучшения качества воздуха в зоне дыхания оператора в кабине можно использовать систему вентиляции кабины, при которой воздух движется в одном направлении (uni-directional airflow pattern), см. Рис. 9.7 справа. В большинстве систем очистки и подачи воздуха, место всасывания воздуха из кабины в рециркуляционную систему, и место подачи воздуха в кабину находится на крыше кабины. К сожалению, это приводит к тому, что запылённый воздух “подталкивается” в зону дыхания рабочего (при всасывании воздуха из кабины в рециркуляционную систему – он движется снизу вверх). В некоторых (неудачных) конструкциях расстояние между отверстиями для выпуска и для всасывания воздуха на крыше кабины составляет ~20 см (within inches), что приводит к тому, что выпущенный в кабину чистый воздух сразу всасывается в рециркуляционную систему – проходя над зоной дыхания рабочего. Поэтому во многих улучшенных вентиляционных системах организовано вертикальное движение воздуха сверху вниз во всём пространстве кабины (за счёт установки воздуховода так, что всасывание загрязнённого воздуха в рециркуляционную систему происходит около пола).
Оптимальные параметры эффективной системы[править]
При модернизации устаревшей системы вентиляции кабины нужно найти оптимальное соотношение между разными параметрами и факторами. Если необходимо обеспечить защиту рабочих от токсичной пыли, нужно приложить усилия для получения максимальной эффективности. А если требуется защита от нетоксичной пыли, степень защиты может быть меньше.
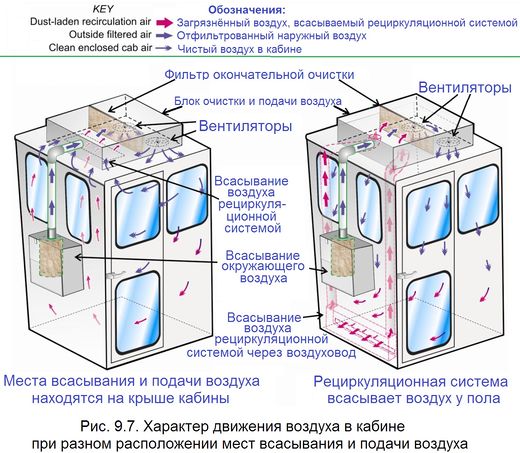
В таблице 9.3 показано, как разные параметры влияют на общую эффективность системы очистки и подачи воздуха. В таблице показаны вычисленные значения коэффициентов защиты, полученные с помощью математической модели (уравнение 9.2), которая была разработана на основе результатов лабораторного исследования. В таблице используются те же значения параметров, которые использовались в рассмотренных ранее примерах: расход приточного воздуха (Qi) 23.6 л/сек (50 cfm), расход воздуха в рециркуляционной системе (QR) 141.5 л/сек (300 cfm), эффективность очистки фильтра в рециркуляционной системе (ηR) = 0.7 (70%), эффективность очистки у фильтра для приточного воздуха (ηI) = 0.95 (95%), и просачивание (l) = 0,5%, 10% и 15%.
Таблица показала, какие важные факторы влияют на общую эффективность системы. Во-первых, она показала, как увеличение просачивания снижает эффективность всей системы. Просачивание может происходить или при наличии в корпусе кабины зазоров или проёмов, или при недостаточной подаче очищенного наружного воздуха. Просачивание неотфильтрованного воздуха происходит или из-за недостаточной герметичности корпуса кабины (зазоры, отверстия, неплотности), или при недостаточном расходе приточного воздуха. Если рассматривать такую кабину, в которую не просачивается неотфильтрованный воздух, то при добавке рециркуляционной системы (расход 141.5 л/сек [300 cfm] эффективность фильтра 70%) коэффициент защиты возрастает с 20 до 104. Это показывает, что рециркуляционная система сильно улучшает защиту оператора. Причём установка в рециркуляционную систему высокоэффективного противоаэрозольного фильтра НЕРА не приводит к какому-то заметно лучшему результату (по сравнению с использованием фильтров умеренной эффективности - (70÷95%). Первый столбец таблицы 9.3 показывает, что при нулевом просачивании (l=0) увеличение эффективности фильтра рециркуляционной системы с 70 до 95% коэффициент защиты увеличивается лишь на 24 пункта. Так как внутрикабинный воздух продолжает непрерывно прокачиваться через фильтр рециркуляционной вентиляционной системы, то это приведёт к улавливанию всей респирабельной пыли, которая многократно направляется в фильтры рециркуляционной системы.
l = 0.00 | l = 0.05 | l = 0.10 | l = 0.15 | |
---|---|---|---|---|
(QI) = 23.6 л/сек (50 cfm)
(QR) = 141.5 л/сек (300 cfm) (ηI) = 0.95 (ηR) = 0 |
20.0 | 10.3 | 6.9 | 5.2 |
(QI) = 23.6 л/сек (50 cfm)
(QR) = 141.5 л/сек (300 cfm) (ηI) = 0.95 (ηR) = 0.70 |
104.0 | 53.3 | 35.9 | 27.0 |
(QI) = 23.6 л/сек (50 cfm)
(QR) = 141.5 л/сек (300 cfm) (ηI) = 0.95 (ηR) = 0.90 |
128.0 | 65.6 | 44.1 | 33.2 |
Другие способы уменьшения концентрации пыли в кабине[править]
Отдельные блоки высокоэффективной очистки воздуха маленькой производительности[править]
В некоторых из кабин операторов и помещений с пультами управления устанавливают отдельные воздухоочистители с противоаэрозольными фильтрами высокой эффективности НЕРА. Для этого используют маленькие и портативные установки, которые стояг значительно дешевле, чем рассмотренные выше встроенные системы очистки. Но такие (маленькие) системы могут быть достаточно эффективны лишь тогда, когда их производительность достаточна для размера помещения, и при своевременной замене фильтров[9- 16]. Очевидным и значительным недостатком таких устройств является отсутствие избыточного давления в помещении, что не позволяет предотвратить просачивание запылённого воздуха снаружи внутрь. Ряд исследований показал, что во многих случаях они не обеспечивают требуемую степень защиты, и что работодателю лучше приложить внимание, силы и средства для улучшения работы уже имеющихся блоков очистки и подачи воздуха, встроенных в крышу кабины[9- 17][9- 18]. Поэтому в большинстве случаев не рекомендуется использовать устанавливаемые отдельно воздухоочистители с противоаэрозольными фильтрами высокой эффективности НЕРА, и их нужно заменять на более эффективные рециркуляционные системы адекватной производительности.
.
ССЫЛКИ
- ↑ CDC [2000]. Notice to readers: NIOSH Alert; silicosis screening in surface coal miners — Pennsylvania, 1996–1997. Cincinnati, OH: U.S. Department of Health and Human Services, Centers for Disease Control and Prevention, National Institute for Occupational Safety and Health.MMWR Weekly 49(27):612–615.
- ↑ Organiscak JA, Cecala AB, Thimons ED, Heitbrink WA, Schmitz M, Ahrenholtz E [2004]. NIOSH/Industry collaborative efforts show improved mining equipment cab dust protection. SME Transactions 2003 Littleton, Colorado: Society for Mining, Metallurgy and Exploration, Inc., 314:145–152.
- ↑ Chekan GJ, Colinet JF [2003]. Retrofit options for better dust control—cab filtration, pressurization systems prove effective in reducing silica dust exposures in older trucks. Aggregates Manager, December, 8(9):9–12.
- ↑ Cecala AB, Organiscak JA, Zimmer JA, Heitbrink WA, Moyer ES, Schmitz M, Ahrenholtz E, Coppock CC, Andrews EH [2005]. Reducing enclosed cab drill operator's respirable dust exposure with effective filtration and pressurization techniques. [Reducing enclosed cab drill operator's respirable dust exposure with effective filtration and pressurization techniques J of Occ and Env Hyg 2(1):]54–63.
- ↑ Cecala AB, Organiscak JA, Heitbrink WA, Zimmer JA, Fisher T, Gresh RE, Ashley JD II [2004]. Reducing enclosed cab drill operator's respirable dust exposure at surface coal operations with a retrofitted filtration and pressurization system. SME Transactions 2003, Littleton, Colorado: Society for Mining, Metallurgy and Exploration, Inc, 314:31–36.
- ↑ NIOSH [2008b]. Key design factors of enclosed cab dust filtration systems. By Organiscak JA, Cecala AB. U.S. Department of Health and Human Services, Centers for Disease Control and Prevention, National Institute for Occupational Safety and Health: NIOSH Report of Investigations 9677.
- ↑ Organiscak JA, Cecala AB [2008]. Laboratory investigation of enclosed cab filtration system performance factors. Min Eng 60(12):74–80.
- ↑ Heitbrink WA, Thimons ED, Organiscak JA, Cecala AB, Schmitz M, Ahrenhottz E [2000]. Static pressure requirements for ventilated enclosures. Proceedings of the Sixth International Symposium on Ventilation for Contaminant Control, Helsinki, Finland, June 4–7.
- ↑ Cecala AB, Organiscak JA, Zimmer JA, Moredock D, Hillis M [2007]. Closing the door to dust when adding drill steels. Rock Products www.rockproducts.com, October, pp. 29–32.
- ↑ NIOSH [2008a]. Technology news 533: Minimizing respirable dust exposure in enclosed cabs by maintaining cab integrity. By Cecala AB, Organiscak JA. Pittsburgh, PA: U.S. Department of Health and Human Services, Centers for Disease Control and Prevention, National Institute for Occupational Safety and Health, DHHS (NIOSH) Publication No. 2008–147.
- ↑ ASABE [2003]. Agricultural Cabs—Engineering Control of Environmental Air Quality, Part 1: Definitions, Test Methods, and Safety Practices [Standard 5525–1.1]. St. Joseph, Michigan: American Society of Agricultural and Biological Engineers.
- ↑ NIOSH [2001a]. Technology news 485: Improved cab air inlet location reduces dust levels and air filter loading rates. By Organiscak JA, Page SJ. Pittsburgh, PA: U.S. Department of Health and Human Services, Centers for Disease Control and Prevention, National Institute for Occupational Safety and Health.
- ↑ NIOSH [2007]. Technology news 528: Recirculation filter is key to improving dust control in enclosed cabs. By Organiscak JA, Cecala AB. Pittsburgh, PA: U.S. Department of Health and Human Services, Centers for Disease Control and Prevention, National Institute for Occupational Safety and Health, DHHS (NIOSH) Publication No. 2008–100.
- ↑ Cecala AB, Organiscak JA, Heitbrink WA [2001]. Dust underfoot—enclosed cab floor heaters can significantly increase operator's respirable dust exposure. Rock Products 104(4):39–44.
- ↑ NIOSH [2001b]. Technology news 486: Floor heaters can increase operator's dust exposure in enclosed cabs. By Cecala AB, Organiscak JA. Pittsburgh, PA: U.S. Department of Health and Human Services, Centers for Disease Control and Prevention, National Institute for Occupational Safety and Health.
- ↑ Logson R [1998/1999]. Controlling respirable dust in plant control rooms. Stone Review, The Bimonthly Publication of the National Stone Association. December 1998/January 1999, 14(6):43–44.
- ↑ Cecala AB, Zimmer JA [2004a]. Clearing the air. Aggregates Manager J 9(4):12–14.
- ↑ Cecala AB, Zimmer JA [2004b]. Filtered recirculation—a critical component to maintaining acceptable air quality in enclosed cabs for surface mining equipment. Proceedings of 10th U.S./N.A. Mine Ventilation Symposium. Anchorage, Alaska. May 16–19, pp. 377–387.
ГЛАВА 10. Уменьшение запылённости при попадании пыли в воздух с дорог, мест хранения и открытых мест[править]
Словарь[править]
Пересчёт формул из системы IP в СИ[править]
- Уравнение 1.2 в системе IP, если все переменные равны 1:
- Q = 10 × Au × (R × S2 / D)1/3 = 10 куб футов/мин = 0.00471947 м3/с = 16.99 м3/час
- 1 фут = 0.3048 м, 1 тонна в час = 1000/3600 = 0.277 кг/сек, 1 куб фут/мин = (0.3048)3 /60 = 0,000472 м3/с
- Уравнение 1.2 в системе СИ (без коэффициента 10 вначале), подставив те же физические значения получим:
- Q = (0.3048)2 × (0,277 кг/сек × [0.3048 × 0.3048 / 0.3048] )1/3 = 0,04079 м3/с
- Поэтому для м3/с коэффициент равен не 10, а (0.00472/0.0408=) 0.1157, а для м3/час – 416.5
- Результат:
- Q = 0.1157 × Au × (R × S2 / D)1/3 (м3/с) = 416.5 × Au × (R × S2 / D)1/3 (м3/час) (Уравнение 1.2) (СИ)
- Уравнение 1.3 в системе IP, если все переменные равны 1:
- Q = 1 × Vx × (10 × X2 + Ah) = 11 куб футов/мин = 0,00519 м3/с = 18,69 м3/час
- 1 фут = 0.3048 м, 1 фут/мин = 0.3048/60 = 0,00508 м/сек, 1 куб фут/мин = (0.3048)3/60 = 0,000472 м3/с
- Уравнение 1.3 в системе СИ (без коэффициента 1 вначале), подставив те же физические значения получим:
- Q = 0.00508 × (10 × 0.3048 × 0.3048 + 0.3048 × 0.3048) = 0,00519 м3/с
- Поэтому для м3/с коэффициент равен (0.0052/0.0052=) 1, а для м3/час – 3600.
- Результат:
- Q = 1 × Vx × (10 × X2 + Ah) (м3/с) = 3600 × Vx × (10 × X2 + Ah) (м3/час) (Уравнение 1.3) (СИ)
- Уравнение 1.4 отличается от уравнения 1.3 коэффициентом 5 вместо 10 в скобках, а общий коэффициент перед уравнением тот же:
- Q = 1 × Vx (5 × X2 + Ah) (м3/с) = 3600 × Vx (5 × X2 + Ah) (м3/час) (Уравнение 1.4) (СИ)
- Уравнение 1.5 отличается от уравнения 1.3 коэффициентом 0.75 вместо 1 перед уравнением:
- Q = 0.75 × Vx (10 × X2 + Ah) (м3/с) = 2700 × Vx (10 × X2 + Ah) (м3/час) (Уравнение 1.5) (СИ)
- Уравнение 4.1 в системе IP, если все переменные равны 1:
- Qe = 33.3 × ( 600 × Т / G ) = 19980 куб футов/мин = 9.43 м3/ч = 33946 м3/час
- 1 тонна в минуту = 1000/60 = 16.67 кг/сек, 1 фунт = 0.45 кг, 1 фунт/куб фут = 0.45/0.30483 = 15.9 кг/м3
- Уравнение 4.1 в системе СИ (без коэффициентов 33.3 и 600), подставив те же физические значения получим:
- Q = 16.57/15.69 = 1.049 м3/с
- Поэтому для м3/с коэффициент равен (9.43/1.049=) 8.99, а для м3/час – 32368.
- Результат:
- Qe = 9 × Т / G (м3/с) = 32368 × Т / G (м3/час) (Уравнение 4.1) (СИ)
- Уравнение 4.2 и 1.2 одинаковы.
- Уравнение 5.3 и 1.2 одинаковы.